Agricultural Machinery Design – How Bulk Material Simulation Can Accelerate the Design Process and Improve Machine Performance
Challenges of Designing Agricultural Machinery
The agricultural machinery market is a highly competitive one. Manufacturers of agricultural equipment need to continuously increase the quality and reliability of their machines but also innovate and deliver solutions that are tailored to the demands of the agricultural sector.
One challenging aspect relates to the range of operations and conditions that machines have to perform in. Tractors, combines, and forage harvesters are all designed to work with a range of bulk materials such as crops (in various stages of being processed), seeds and soils, all of which may vary in properties depending on the location and seasonal conditions. The variability of these materials can have a strong effect on the performance of the machines.
Combine harvesters for instance have to deal with soil, grains and also fibrous materials. The cohesive nature of the fibers could lead to blockage within the harvesting equipment and non-optimized cutting could result in poor quality crops and final product.
Grain augers which are used in combines and other agriculture areas to transport grain is another example where the material handled can pose a challenge. When transporting the seeds, it’s important not to leave any material behind in the auger that may then contaminate the product. Some grain types or mixes can be abrasive and cause problems with equipment wear especially in continuous processes for bulk material transport. Optimizing the unloading of the auger is therefore crucial.
In the case of tillage equipment, the blades might be interacting with a range of soils with different levels of compressibility and stickiness, or perhaps harder materials like rocks, all of which will have an impact on the machine. Being able to predict how the equipment will be affected by a specific material and identifying potential wear on tools represents a key aspect to ensure the machine will perform as expected.
In all these examples, predicting the bulk behavior of materials and their impact on the machine is critical to achieve efficiency and performance; however, it is challenging due to the complexity and variability of bulk materials. Using physical testing of new equipment designs is expensive and limiting, especially when considering testing against crops in the field where missing a seasonal testing window due to adverse weather conditions can significantly delay the time to market for new designs.
Using simulation in the design process
Using simulation and computer-aided-engineering (CAE) tools presents a lot of benefits to machinery design as it enables to perform virtual testing of equipment. As mentioned above, for simulating agricultural processes, an important aspect is to take into consideration the material that the machine is supposed to handle or interact with. This is possible using a modeling technique called the discrete element method (DEM). DEM is a particle-scale numerical method for modeling the bulk behavior of granular materials including grains, seeds, crops, soils and stems. With DEM it is possible to recreate the behavior of these materials and analyze how they will interact with a piece of equipment during a range of operation and process conditions.
DEM tools such as Altair EDEMTM software can be used for the design, performance testing, and optimization of agricultural machinery such as combine harvesters, hay and forage equipment, tillage tools, seeder/fertilizer equipment and grain handling and transport systems.
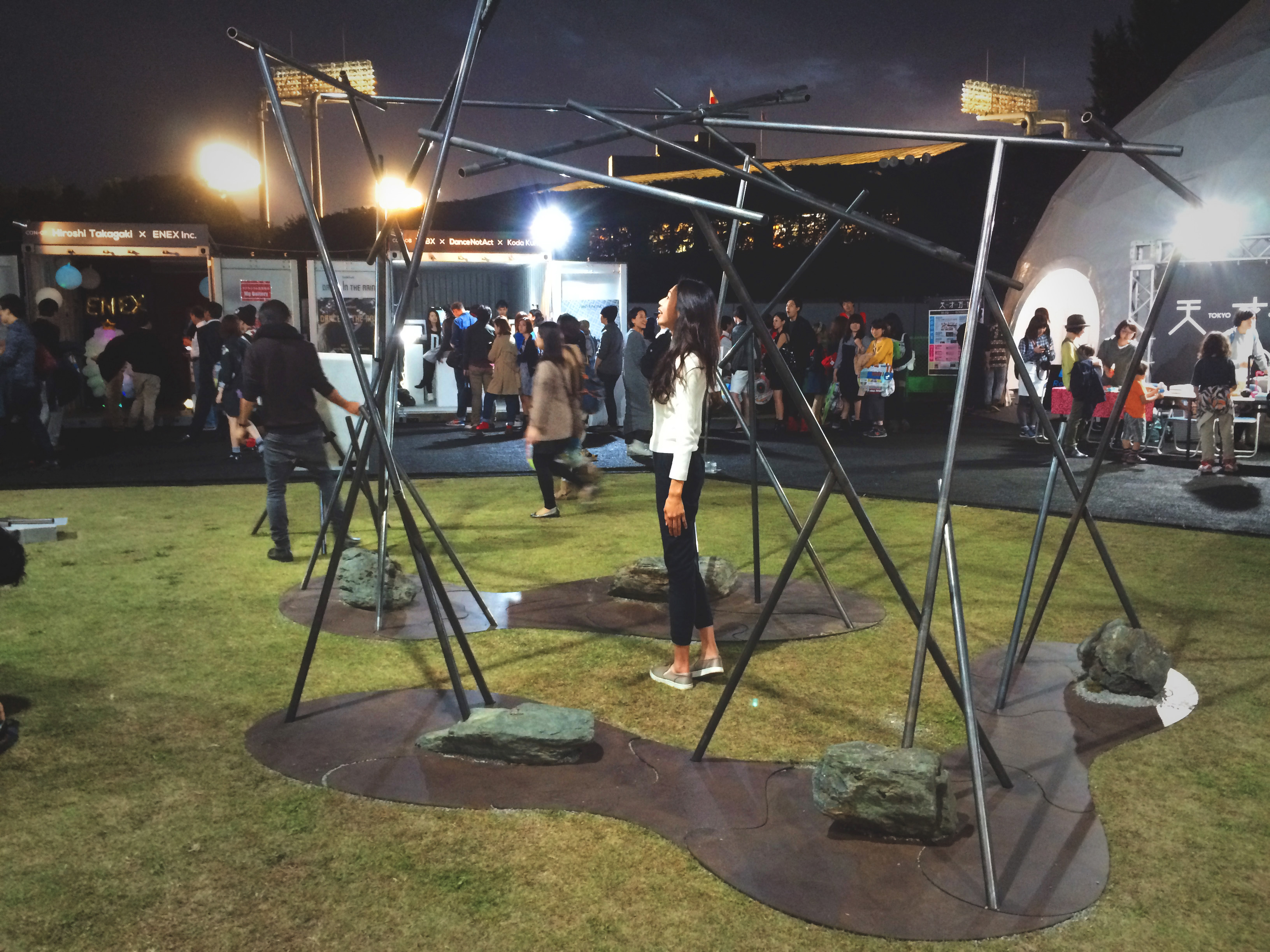
Using EDEM bulk material simulation as part of the design process can bring a lot of benefits to agricultural equipment manufacturers. These include the ability to:
- Predict complicated bulk material behavior such as fibrous material cutting, transportation and bailing
- Predict the flow of products such as grains to deliver optimal material flow properties
- Identify risk of blockages in the equipment due to high flow rates, pulsing flows, cohesive/wet materials or long fibrous materials
- Investigate tool wear interaction responses with soils or abrasive grain mixes
- Predict equipment kinematic response due to impacts with large rocks, compressed or sticky materials
- Perform testing out of season without having to ship prototypes to areas where crop is growing, thus reducing the need for physical prototypes
Using EDEM bulk material simulation therefore can help address some of the challenges of designing agricultural machinery. This type of simulation enables manufacturers to get key insight into crop-machine and soil-machine interactions and to virtually test designs for a wide range of materials with different properties.
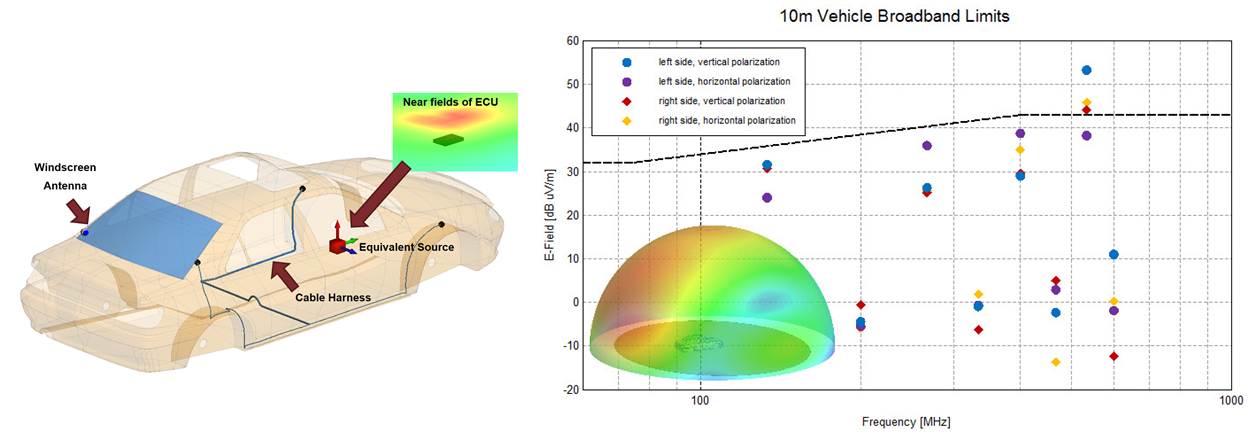
EDEM can also be used alongside other CAE tools including multi-body dynamics, finite element analysis and computational fluid dynamics – providing greater insight into equipment performance and confidence that simulations represent real-life scenarios.
Adding EDEM to the engineering toolkit can help manufacturers shorten design cycles, reduce product development time and costs, reduce the need and thus the cost of physical prototyping as well as driving product innovation.
Find out more about the various applications of EDEM simulation in the design of agricultural machinery with this on-demand webinar.