
Transform Your Operations with Smart Manufacturing Solutions
Altair’s advanced software and cloud-based solutions seamlessly integrate the essential technologies behind Industry 4.0 – including the Industrial Internet of Things (IIoT) – to support smart manufacturing. By integrating these cutting-edge technologies, Altair helps organizations transition to fully connected, automated, and efficient smart manufacturing processes.
We tackle the most critical challenges in modern manufacturing, from handling massive real-time data streams to boosting production flexibility and minimizing downtime. With our simulation and data science tools, manufacturers can create digital twins of their processes and machinery, enabling them to optimize operations and boost efficiency across the board.
With high-performance computing (HPC) and artificial intelligence (AI), we provide the computational power and intelligent insights needed to drive innovation across every stage of production. From advanced data analytics for predictive maintenance to AI-driven decision-making that reduces waste and increases throughput, our solutions power digital transformation and smart manufacturing—not just in your production facilities, but throughout your entire supply chain.
See how Nokia IIoT Networks are Powered by 5G
Learn More
The Smart, Connected Factory Floor
Altair can help you deploy edge compute clusters, train and execute machine learning models, implement complex application business logic, perform data transforms, visualize real-time data, and much more.
The 5G standard is the foundation for many IIoT applications. Simulating the devices, 5G antennas, and the 5G networks they are operating within, helps to create the desired communication performance.
We give you the building blocks for your digital transformation to get moving fast, scale quickly, and continue to improve over time.
Master complex concepts with ease with our Blueprint series, a comprehensive learning initiative that simplifies technical concepts into easy-to-follow modules.

Process Optimization
Manufacturing simulation has traditionally been applied during the latter stages of product development, but Altair has pioneered simulation-driven design for manufacturing (SDfM), bringing manufacturing simulation into the earliest stages of concept design with fast, accurate solvers and intuitive interfaces. This innovation allows concept designs to consider more manufacturing options and constraints, enabling engineers to better understand designs instead of depending purely on institutional know-how.
Learn more about:

Smarter Equipment
The increasing complexity of industrial machinery requires active management of technical risks in product line development and customer implementation projects. Altair’s integrated product and process simulation tools allow a holistic view of the system from different roles to ensure perfectly running production earlier.
Machine learning enables equipment to become self-aware, optimize itself, allow machine makers to automate path error corrections, and vary manufacturing tolerances or mechanical aging of the system.
Manufacturing Analytics
Industrial Internet of Things (IIoT) is increasing connectivity, generating data, and unlocking potential. Altair knows how to take full advantage of data to fuel innovation, drive new opportunities, and accelerate your smart manufacturing transformation.
Digital Twins
Digital twins help organizations optimize performance, gain visibility of in-service life, know when and where to perform maintenance, and how to extend a product’s remaining useful life. We take a complete, open, and flexible approach that enables your digital transformation vision on your terms.
Additive Manufacturing
Today, many organizations are taking new approaches to the design and optimization of components for additive manufacturing. Altair provides a powerful, comprehensive solution that enables designers to unleash the potential of additive manufacturing to create intricate, organic shapes to meet functional requirements without needing to deal with the constraints of traditional manufacturing methods.
New to AI for engineering and manufacturing?
Get Started HereFeatured Resources

Implement Effective Manufacturing Process Analytics
By extracting real value from their data, manufacturers can make accurate predictions about component life, replacement requirements, energy efficiency, utilization, and other factors that have direct impacts on production capacity, throughput, quality, sales, customer acceptance, and overall efficiency.
Low cost sensors and new wireless connectivity tools enable manufacturers to employ digital analytics more effectively than ever before. With the right tools, they can gather, cleanse, process, and visualize massive amounts of data from disparate sources that cover all phases of the product life cycle, from product design to warranty claims.
This guide explains some of the major challenges involved in applying data analytics to manufacturing processes and the benefits of developing optimized approaches to addressing those challenges.

Generative Design Competitive Ranking by ABI Research
This study assesses and compares nine suppliers of generative design software to offer an unbiased assessment and ranking Only platforms with a dedicated market focus on industrial and manufacturing were considered.
This report sets out the market positioning of each profiled company leader, mainstream, and followers ABI Research developed this Competitive Assessment (to offer a comparative assessment and ranking of the following suppliers of generative design software Altair, Ansys, Autodesk, Dassault Systèmes Hexagon, nTopology ParaMatters PTC, and Siemens.
Altair was ranked Overall Leader, Top Innovator, and Top Implementer.

Guide to Process Manufacturing
Any industry that produces bulk quantities of goods such as pharmaceuticals, food, chemicals, or cosmetics, is seeking to produce these products consistently while reducing cost factors like waste and down time. Due to the nature of process manufacturing, multiple ingredients are combined to be mixed, coated, or sorted, so understanding the behavior of these processes is of paramount importance for manufacturers. Through the use of simulation modeling and Smart Manufacturing principals, manufacturers are now able to optimize these processes, leading to greater productivity and profitability.

Research Report: Simulation-Driven Design for Manufacturing (SDfM) Experiences
Product engineers are under consistent pressure to reduce the costs, improve the quality and increase the throughput of manufacturing processes. This fast-paced environment is not well suited for trial-and-error manufacturing engineering.
How are engineers responding to these challenges? Is simulation and simulation-driven design for manufacturing (SDfM) well established across the industry? When simulation is deployed, does it deliver on the promises of reducing costs while improving throughput and quality? And what are the barriers to the adoption of simulation during the early stages of product development?
In this 2021 survey report conducted by Engineering.com, we discuss those questions and discover:
- Top design priorities
- Top benefits of SDfM
- Top barriers to expanding and adopting SDfM
- Risks to staying competitive in the market
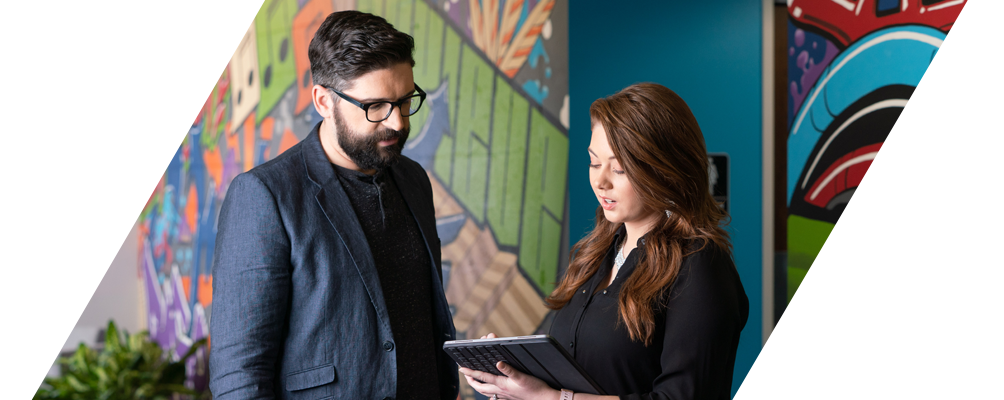