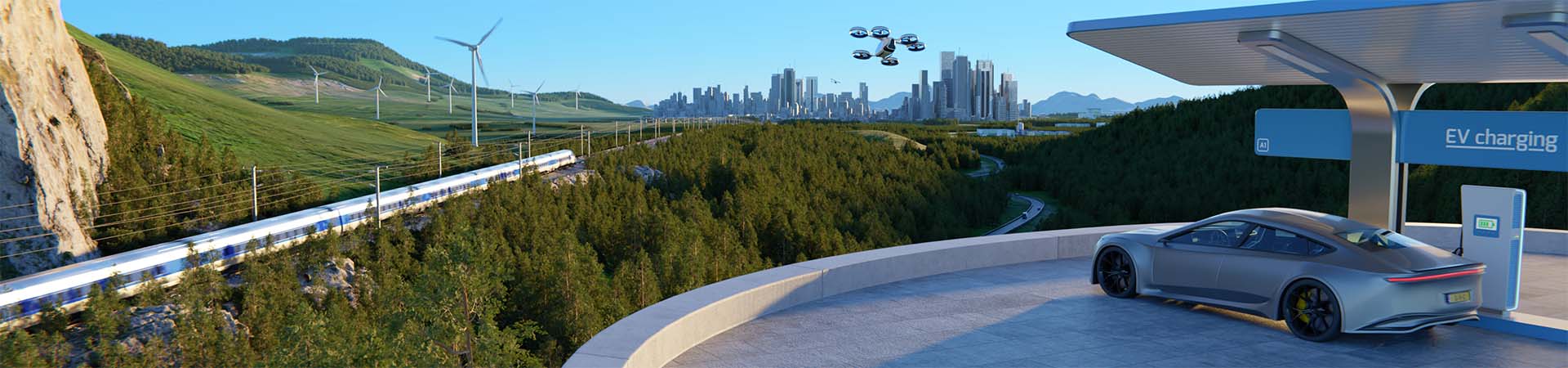
Electrification
Meeting the world's growing transportation needs and green mobility demands is a difficult undertaking. Altair’s impactful electrification solutions are addressing this challenge by helping companies develop energy-efficient systems, like electric powertrains that release fewer carbon emissions into the atmosphere, and sustainable electric road-vehicles, watercraft, heavy-machinery, and rail systems.
Companies are leveraging Altair's connected capabilities to lightweight designs, optimize integrated system performance, reach sustainability and efficiency goals, and drive e-mobility advancements faster.
Designing a Sustainable Future
Businesses that successfully and rapidly meet consumer demand for sustainable electrification innovations are poised to gain significant market share, but innovation requires the right technology partners with the right design, simulation, data analytics, artificial intelligence (AI), and high-performance computing (HPC) offerings.
Altair’s electrification solutions accelerate lightweighting, enhance energy efficiency, and optimize systems to lessen environmental impacts, thereby enabling companies to meet their sustainability goals and consumer demands for heavy-equipment, aircraft, auto, rail, and other e-transportation solutions.
In addition, e-Mobility solutions must connect and interact with their surroundings without interfering with in-vehicle electrical systems (EMC/EMI). Altair® Feko® high-frequency electromagnetics software and wave propagation tools help vehicle designers perform virtual drive testing and consider a full array of environmental obstacles using either dedicated short-range communications (DSRC) or 5G wireless signals.
Accelerate Electrification
Faster Processes
Altair electrification solutions and streamlined product validation processes give users holistic insight for better decision-making between technical, safety, and efficiency tradeoffs, enabling teams to rapidly optimize and develop complex, connected architectures in e-powered systems.
Faster Turnaround
Global access to connected multiphysics capabilities and data through Altair One™ enables frictionless collaboration and turnaround. Access to repeatable, simulation-driven design processes shortens development cycles, improves efficiency, and supports production at a mass-market scale. On-demand HPC offers secure, scalable simulation capabilities during peak demand. Flexible cloud-based HPC also supports multi-disciplinary optimization studies on multiple programs at once, which reduces development costs and risk.
Efficient Powertrains
OEMs producing e-Mobility products must address battery range, drivetrain efficiency, and charging times. Getting the design right for these aspects is vital to successful product development and requires rapid exploration of higher system voltages, innovative cooling implementations, efficient power conversion, optimized vehicle aerodynamics and vehicle-weight reduction to ensure transmission and distribution systems can handle the increased load from electrification.
Altair’s electrification and multiphysics workflows provide a digitally connected end-to-end simulation process for designing efficient powertrains that balance performance, cost, and weight requirements.
Affordable Electric Solutions
Electrified mobility lifecycles and maintenance differ from their internal combustion engine (ICE) counterparts. Companies need technology partners that understand the difference and offer future-focused solutions that include digital twin capabilities that can adapt to new requirements without increasing costs.
Whether adapting existing workflows or deploying new processes for today’s demands, Altair's electrification solutions meet you where you are and evolve with your company to bring product innovations to market faster and more cost effectively. Our flexible Altair Units licensing system saves companies 30-50% over traditional licensing methods and enables seamless computing and collaboration across engineering teams.
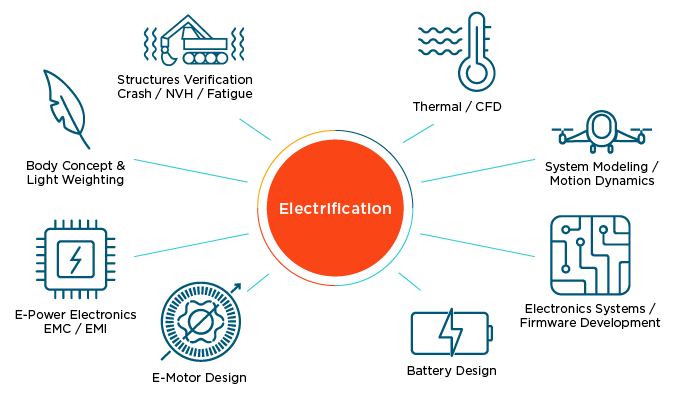
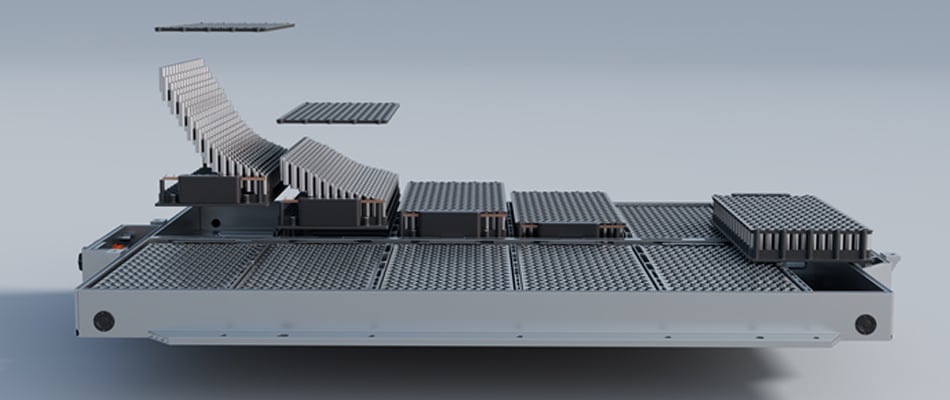
Battery Design for Vehicle Electrification
Developing efficient, high-capacity, safe and affordable batteries is crucial for the successful adoption of electric vehicles (EVs) and renewable energy systems.
Lighter vehicles require less battery power to accelerate and maintain speed, allowing a single charge to go further. Generative design empowers engineers to remove material while maintaining strength and stiffness properties required for safety and comfort. Thermal management is also a key aspect of the design. Implementing the right cooling strategy ensures optimized charging times and longer battery life.
Sound battery pack design is critical for safety, and insights from simulated vehicle-crash, road-debris-impact, and shock events need to align with vehicle program timelines. Altair’s investment in vehicle safety, in collaboration with leaders
in vehicle battery research, enables the efficient and accurate mechanical failure analysis to prevent battery fires.
Electric Motor Simulation
Developing innovative e-motor designs requires proven multiphysics and optimization solutions. To meet these modern design challenges, Altair® e-Motor Director™ seamlessly combines electromagnetics, noise, harshness, and vibration (NVH), and computational fluid dynamics (CFD) simulation capabilities in a single working environment. Here specialists can store best-practices for reuse by non-specialists for faster product development.
Leveraging rapid design exploration and feasibility ranking during the concept phase informs optimal downstream e-propulsion decisions. Engineering teams can use Altair® FluxMotor® to make performance comparisons and determine the best e-motor topologies while considering constraints like efficiency, temperature, weight, compactness, and cost. Detailed e-motor electromagnetics coupled with thermal simulation with Altair CFD™ helps teams design high-power-density electric drives. Altair® OptiStruct® offers insight into sound quality and vibration influenced by e-propulsion systems.
Power Electronics and E-Motor Drive Simulation
Efficient and reliable power management is crucial to a vehicle’s performance. This includes power conversion and distribution to ensure that electrified systems inside drivetrains designed for automotive electrification, aircraft electrification, and other e-mobility systems operate safely.
Simulating multi-physics e-mobility systems within a single, connected solution environment helps electrification innovators better understand the impacts of drivetrains, e-motors, and battery functionality on system performance. With over 25 years of expertise packed inside its power electronics system technology, Altair® PSIM™ provides a complete workflow from concept design to hardware implementation for power converters and motor drives. With valuable insights into power losses, cooling requirements, conducted electromagnetic interference (EMI), and converter characteristics, companies can observe and optimize complex interactions to ensure their next-generation products exceed customer demands for reliable, efficient, and cost-effective e-mobility.
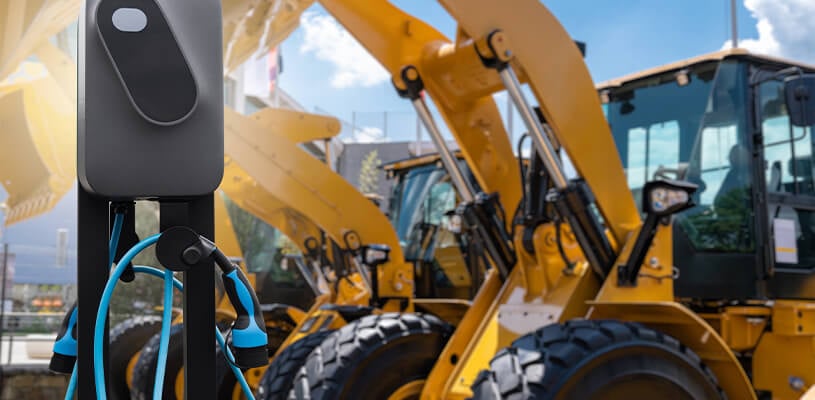
Vehicle Electrification: Systems and Dynamics
Incorporating electrified systems into existing product designs can be complex, especially when maintaining or improving dynamics that include multiple and interconnected systems. Altair's model-based development solutions support multiple simulation models of varying fidelity to accelerate design delivery while handling different levels of mechatronic system complexity. Using models that range from 0D to 3D at various stages along the electric machine, power converter, and control-strategy design development enables companies to adapt and improve control algorithms in a continuous, connected development process. And leveraging integrated 1D and 3D models in sequential or concurrent simulations helps companies assess product operation to boost design efficiency. Altair's multidisciplinary system simulation solutions can predict the combined impact of various parameters on electromagnetic, thermal, and structural performance to produce optimized designs.
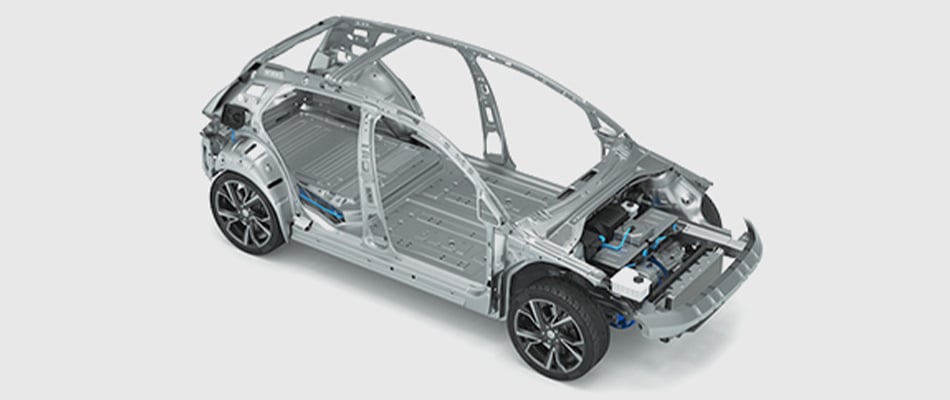
Lightweighting and Electrification
Lighter products require less energy and power for all possible running conditions, leading to longer battery life and extended range compared to heavier products. A lighter battery pack increases range and makes secondary-effect weight-savings possible. For example, less battery power results in a scaled-down battery pack, which puts a lighter load on the product's structure and contributes to further weight savings. These lightweighting tendencies affect vehicle structural safety, NVH, and driving dynamics. Companies can leverage Altair’s generative design and multi-body dynamics solutions to discover their product design’s weight-saving potential and its influence on the driver’s experience.
Featured Resources
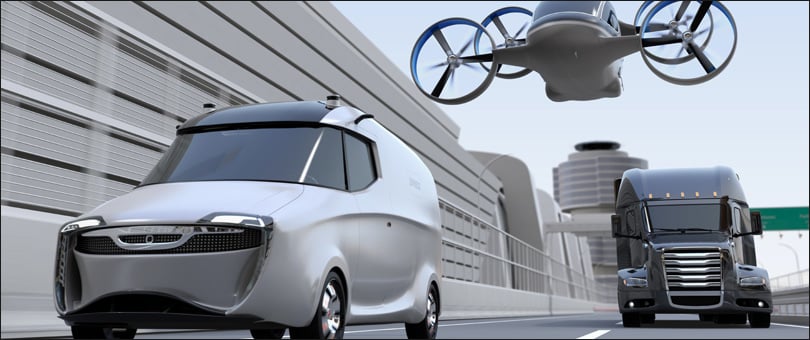
Your Global Partner to Boost Electrification Projects
The path towards electrification requires significant investment, changes to technologies, development processes and even organizational structures. This introductory webinar will reveal Altair's simulation- and data-driven design tools to accelerate all electrification projects by helping to make good decisions early. The session will cover solutions for the design of the various parts of electric drive systems, from the battery to the wheels; while considering system integration and the architecture changes that must be made at vehicle level to build innovative energy efficient electric mobility solutions.
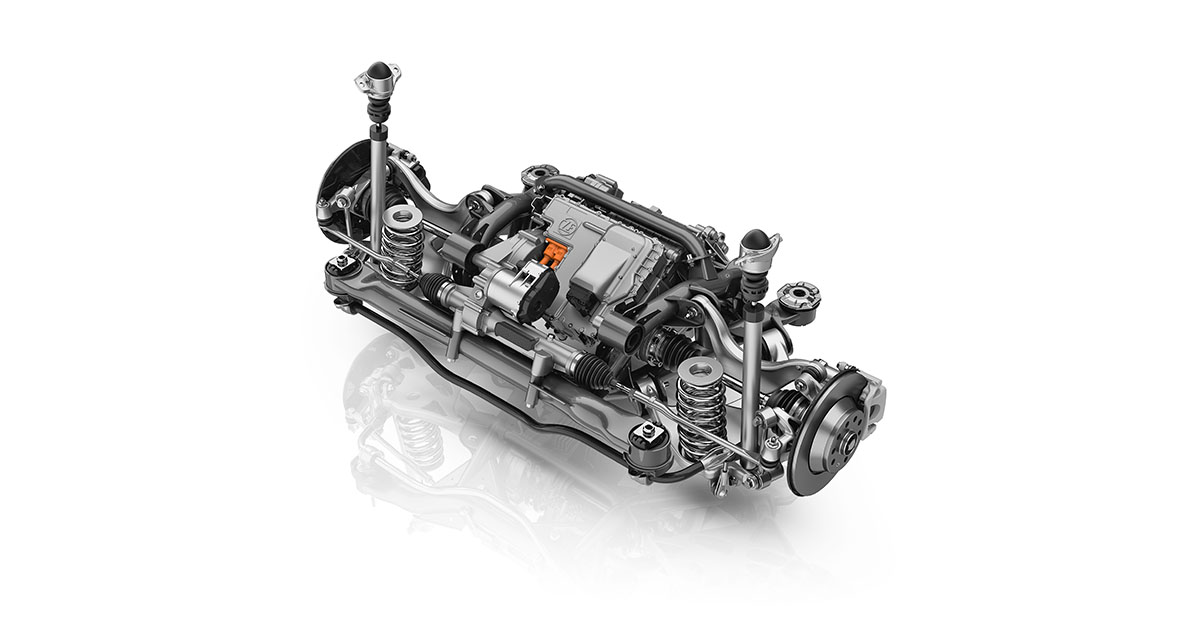
Fully Automated Optimization Engine
ZF develops a wide variety of e-motors and e-drives for a broad spectrum of automotive customers. To optimally incorporate development and production costs from the outset, their designers must find solutions to maximize shared parts within the given requirements for the motors. ZF, in collaboration with Altair, employed a simulation and data-driven solution that empowered them to consider shared parts, costs, and further constraints to automatically find best configurations for a modular motor platform.

Disrupting the Battery Development Process with an Intelligent Digital Twin
Danson Joseph, Managing Director of Danecca, presents at the UK Altair Technology Conference 2022.
Simulation is now the dominant technology driving the design process. Optimization and machine learning, together with the availability of inexpensive computing place simulation at the heart of the design process, and at the evolution of the Digital Twin. EV battery packs present a unique opportunity to showcase the power of simulation and the benefits of the Digital Twin.
Battery Thermal Management Systems (BTMS) use logic to control the thermal balance needed for reliable and long-lasting battery pack designs. A key driver is ensuring cells operate under load within a specified temperature window. The system design challenge is to balance the heat generated by current demand and supply against an efficient cooling strategy.
A Digital Twin has been created which presents a virtual representation of a physical battery pack subject to a transient duty cycle. The Digital Twin mimics the embedded control logic of the hardware to manage system heating and cooling during the event.
Capturing the complex physics and system response with the Digital Twin in timescales commensurate with the physical hardware enhances the role of simulation within the UK battery development community. The battery Digital Twin presents new opportunities for rapid, holistic, design exploration and innovation.

Accurately Predicting Electric Vehicle Range with an Intelligent Digital Twin
A conversation with Selcuk Sever, Principal Engineer at Switch Mobility, discussing its collaboration with Altair to accurately predict the range of its electric buses. With accurate range prediction, Switch Mobility can give its public transport authority customer confidence that electric buses can meet the requirements of their bus routes.
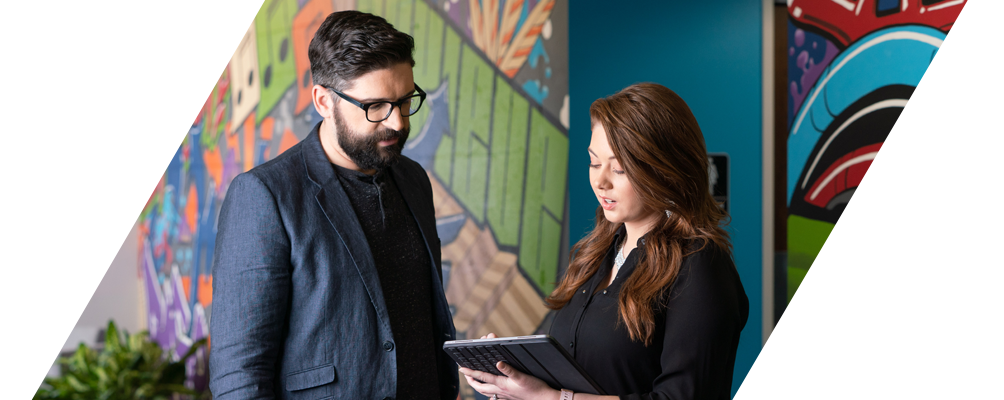