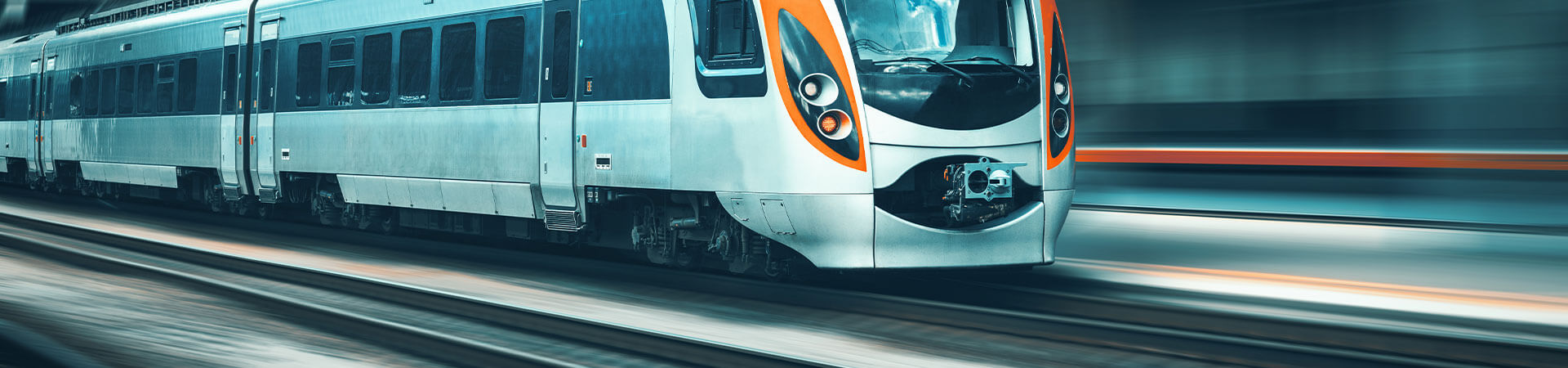
Rail
As with many other sectors, the rail industry has an increasing emphasis on reliability, availability, and connectivity to ensure maintenance and operational costs are optimized. It needs to develop robust and aerodynamic rail car designs that provide comfort and safety to the passengers. To succeed companies must exploit CAE as early as possible in the process to drive decision making and deliver designs on time, on target, and on cost.
Digitalization has also emerged as a key driver for innovation in railways. It provides significant opportunities to streamline operations, improve reliability of assets, and enhance passenger (or freight customer) experience while reducing costs. It is being used to derive real-time information on rail movements and is an enabler of predictive maintenance for fixed assets and rolling stock.
Maximize Reliability, Availability, and Desirability
Drivers and Passenger Environment: Competition in the rail industry requires constant innovation to make the passenger experience more pleasant and convenient. The advanced noise, vibration, and harshness (NVH) analysis of Altair® OptiStruct® is used broadly to ensure the passenger experience is enhanced, and quality is further addressed by Altair® Squeak and Rattle Director™. Altair CFD™ provides solutions engineers need to design better passenger compartment airflow and thermal comfort.
Optimize Connectivity and Operational Costs
Network Connectivity: Equipment connectivity and electromagnetic compatibility (EMC) is essential to today’s rolling stock, and can be optimized with Altair® Feko® and Altair® Flux®. Feko is widely for the design and placement of antennas and modeling wave propagation for network simulation. Feko can also simulate both the radiation and irradiation of cables, antennas, and devices to inform the design of effective shielding. In addition, Altair® WRAP™, a Feko component, can ensure precise and efficient planning for seamless railway communication systems to address coverage, interference, and redundancy needs. Flux can evaluate the magnetic field radiated by power cables and busbars, and the effect of external fields on the operation of sensors or actuators.
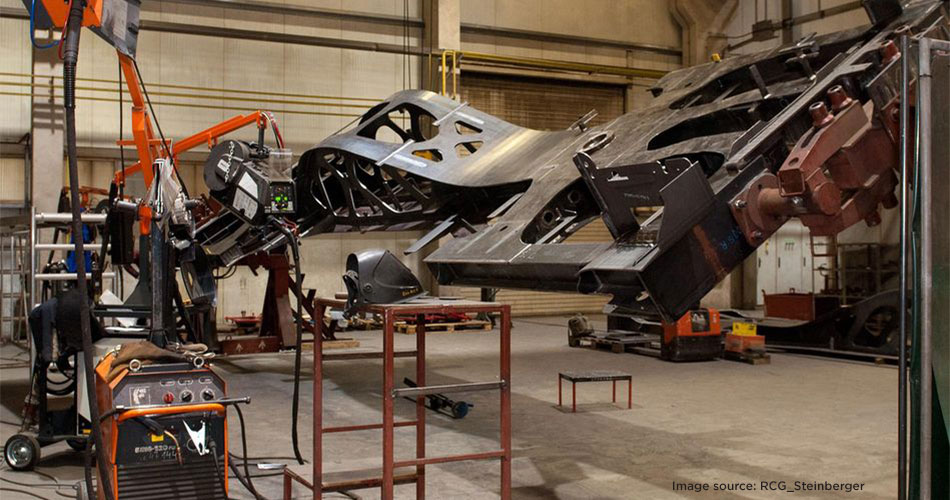
Tools for Structural Integrity
Optimized and Robust Designs: Altair® OptiStruct® and Altair® HyperStudy® are powerful tools in design development to meet performance requirements, all while handling the trade-offs. Railcar body optimization achieves the structural requirements for safety, acoustics, weight and cost. Bogie designs achieve the optimal balance of durability, acoustics, assembly and performance. Seat optimization helps meet all safety, weight and comfort requirements. Pantograph design benefit from an optimal robustness, impact, and transmission efficiency.
Mechanical Analysis: Detailed occupant simulation using certified occupant models and seat models for crash and impact simulations are performed with Altair® Radioss®. It is the leading solution for performing dynamic simulations on the impact of metallic and composite structures.
To rail industry durability requirements Altair® HyperLife® provides a comprehensive and easy-to-use durability analysis workflow. It is automating the weld certification and complies with industry norms like DVS, Eurocode, and FKM. For the generation of load cycles, Altair® MotionSolve® is a powerful product for full dynamic simulation, including those with flexible bodies.
Interested in accelerating your weld certification?
Learn More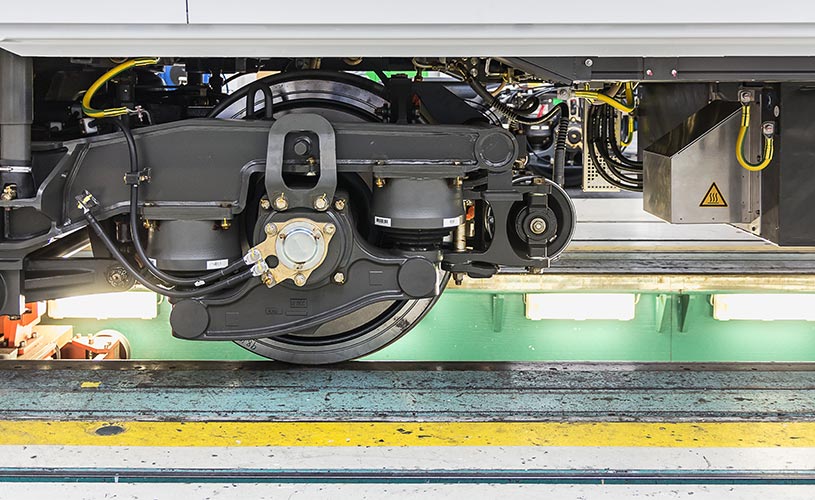
Tools to Optimize Efficiencies and Reduce Downtime
Electric Drivetrains: Altair® FluxMotor® is dedicated to the simulation-driven design of electric rotating machines. It enables users to build from standard or customized parts, add windings and change materials to quickly develop a concept design. Flux models even the most complex electromechanical systems with proven accuracy. It provides multiphysic capabilities – magneto static, steady-state, and transient conditions, along with electrical and thermal properties – to optimize machine performance, efficiency, dimensions, cost, and weight.
Reduce Downtime and Extend Useful Life: Asset management with the Internet of Things (IoT) has given birth to "digital twins" of critical assets. Digital twins help organizations optimize product performance, gain visibility into the in-service life of a product, know when and where to perform predictive maintenance, and how to extend a product’s remaining useful life (RUL).
Featured Resources

Driving a Sustainable Rail - Cargo Solution Simulation Helps TransANT Meet Weight and Weld Certification Requirements
While rail is the most environmentally friendly means of transport, freight trains today do not look much different than those from the past. To reach the climate and energy targets of the European Union while achieving higher payloads and a better ROI, the railway sector needs an innovation boost to build more efficient and sustainable rail freight wagons. TransAnt GmbH, a joint venture with ÖBB Rail Cargo Group and voestalpine Steel Division, was established to bring more efficient and sustainable rail freight solutions to the market. With its innovative concept based on modularity and lightweight design, once operational the company seeks to revolutionize the market as a full supplier of freight wagons. The company used Altair® HyperWorks® for topology optimization – in particular Altair® HyperMesh® – to realize the transition to a weldable structure, Altair® HyperView® for pre- and post-processing, and Altair® OptiStruct® for FEA (including local buckling) and optimization.
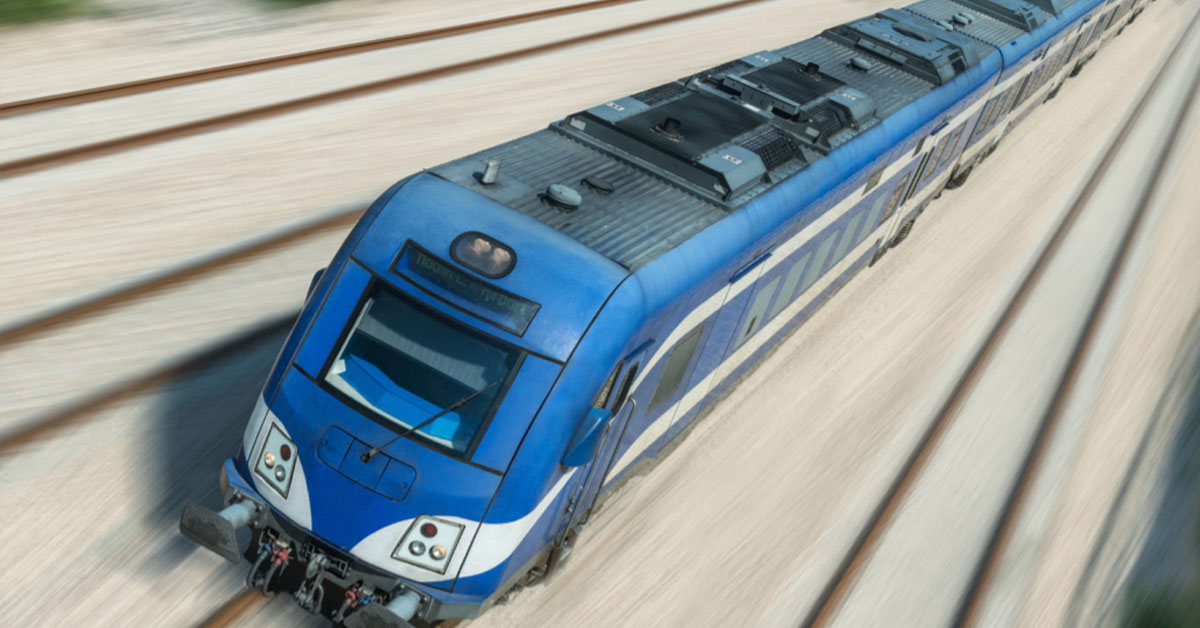
Sharma & Associates
Sharma & Associates (SA), a Chicago-based consulting firm that is focused on providing engineering solutions to the railroad industry, led the effort. Since 1995, SA have delivered safe, effective and efficient solutions to its customers, which include the Federal Railroad Administration (FRA), the Association of American Railroads (AAR), railroads and transit agencies, rail car builders and rail car component manufacturers. The objective of the Altair ProductDesign team effort was to develop an ‘Engineer Protection System (EPS)’ that can protect train crew in frontal collisions (a common mode of train collision) from secondary impact injuries.
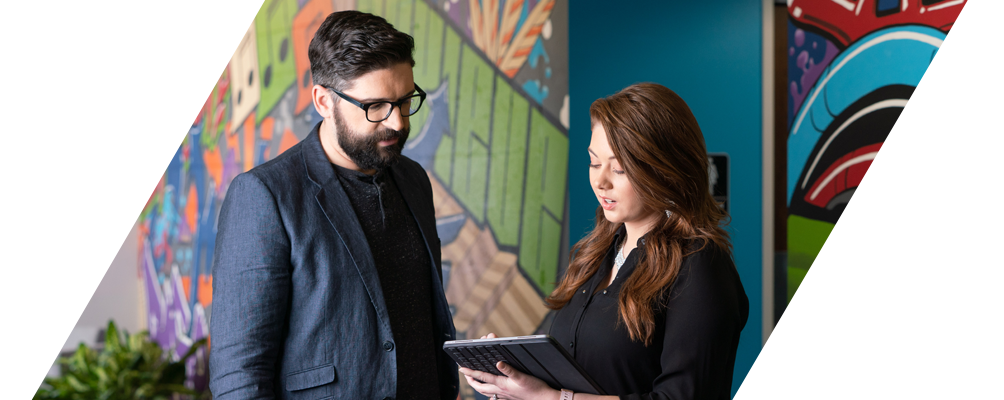