Are Barbells Designed Strong Enough to Withstand the Next World Record Lift?
Competitive weightlifting brings together some of the world’s strongest athletes, lifting massive amounts of weight. It’s physical competition in one of its purest forms. When watching these lifters compete, you may notice the barbell flexing due to the mass amounts of weight on each side of the bar.
For a point of reference, in 2004 two-time Olympic weightlifting champion Hossein Rezazadeh broke the record for the clean and jerk by lifting an impressive 264.4 kilograms (580.9 pounds). When watching the video, you can see how much the bar flexes when Hossein squats down for a full squat clean, hops back up, catches the barbell, and then proceeds to dip and move into a split jerk. Throughout the entire dynamic movement, the bar seems to flex at different rates depending on the motion of his body and which move he’s performing.
After seeing how much movement occurred within the barbell, it made us wonder if the bar would be at risk of breaking if it met a certain maximum weight capacity. Barbells are designed with non-linear motion in mind, meaning whether the bar is being pulled down or up with weight on either end, the design has a degree of flexibility to it to prevent breaking, cracking, etc.
To simulate the world-record clean and jerk, Altair® SimSolid™ was used to study the movement and weight displacement of the barbell to see if the barbell can safely withstand the dynamic loads during these high-intensity movements. SimSolid solver technology supports the analysis of linear static, modal, and thermal properties, along with more complex coupled, nonlinear, transient dynamic effects such as movement created with free weight exercise equipment. Coupled with SimSolid, Altair® OptiStruct® simulated the structural analysis of the barbell, demonstrating the velocity of both the lift and drop of the bar.
Using the Motion analysis module within Inspire, the profile of the bar was initially designed to simulate the motion that occurred during the full clean and jerk movement. Integrated within the Inspire tool, users can study dynamic motion of moving systems, making it easy to view boundary loads during structural analysis or topology optimization.
The displacement and acceleration results found in Inspire were transferred to SimSolid to study the stresses on the barbell resulting from the lift. On the barbell, bonded contact conditions are replaced with sliding between the weight plates and the bar as well as between the plates themselves because bonded contacts would likely add to the stiffness of the model. Changing them to sliding removes some of this artificial stiffening.
Immovable constraint applied at the center of the bar
A modal analysis with immovable support, followed by a transient dynamic analysis in Inspire was conducted to study the base excitation. A time span was set for this model based on how long the full movement motion would take to complete, with damping set to 0.2.
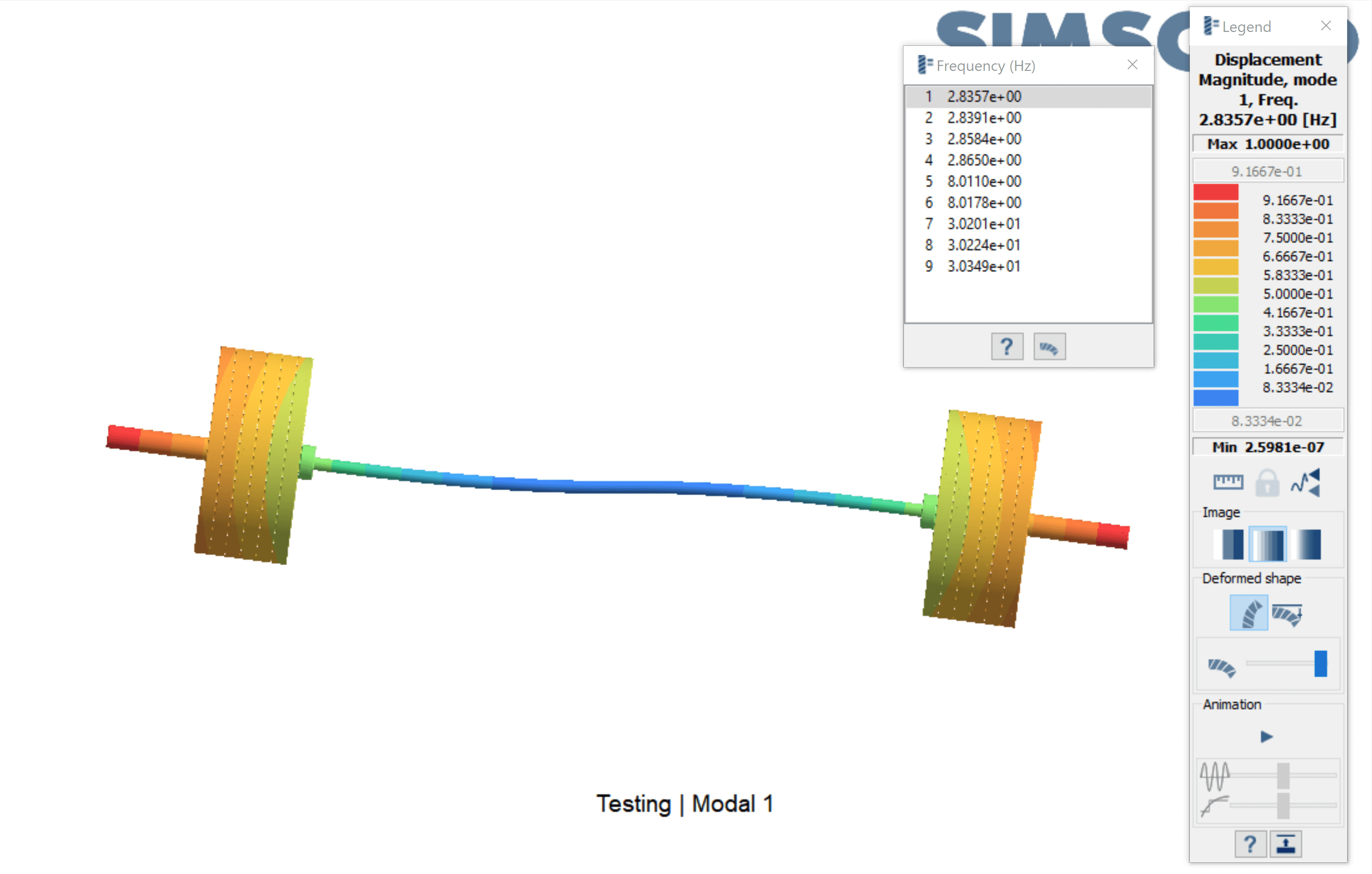

By adding a base excitation to the immovable support and assigning a CSV time function, the simulation was able to show the assembly moving up and down just as it did in Inspire Motion, but now it could flex and bend like it would in real life. However, after adding translational inertia to simulate gravity throughout the simulation, the displacement result wasn’t exactly realistic – It was clearly underdamped and vibrated too much.
A different approach was used after reviewing the first simulation results. The immovable support located in the middle of the bar wasn’t realistic because of the stress concentration it caused (with stress levels of 1186 MPa). The underdamped vibration led to unrealistically large deflections, so the next step was to apply more realistic constraints and more damping.
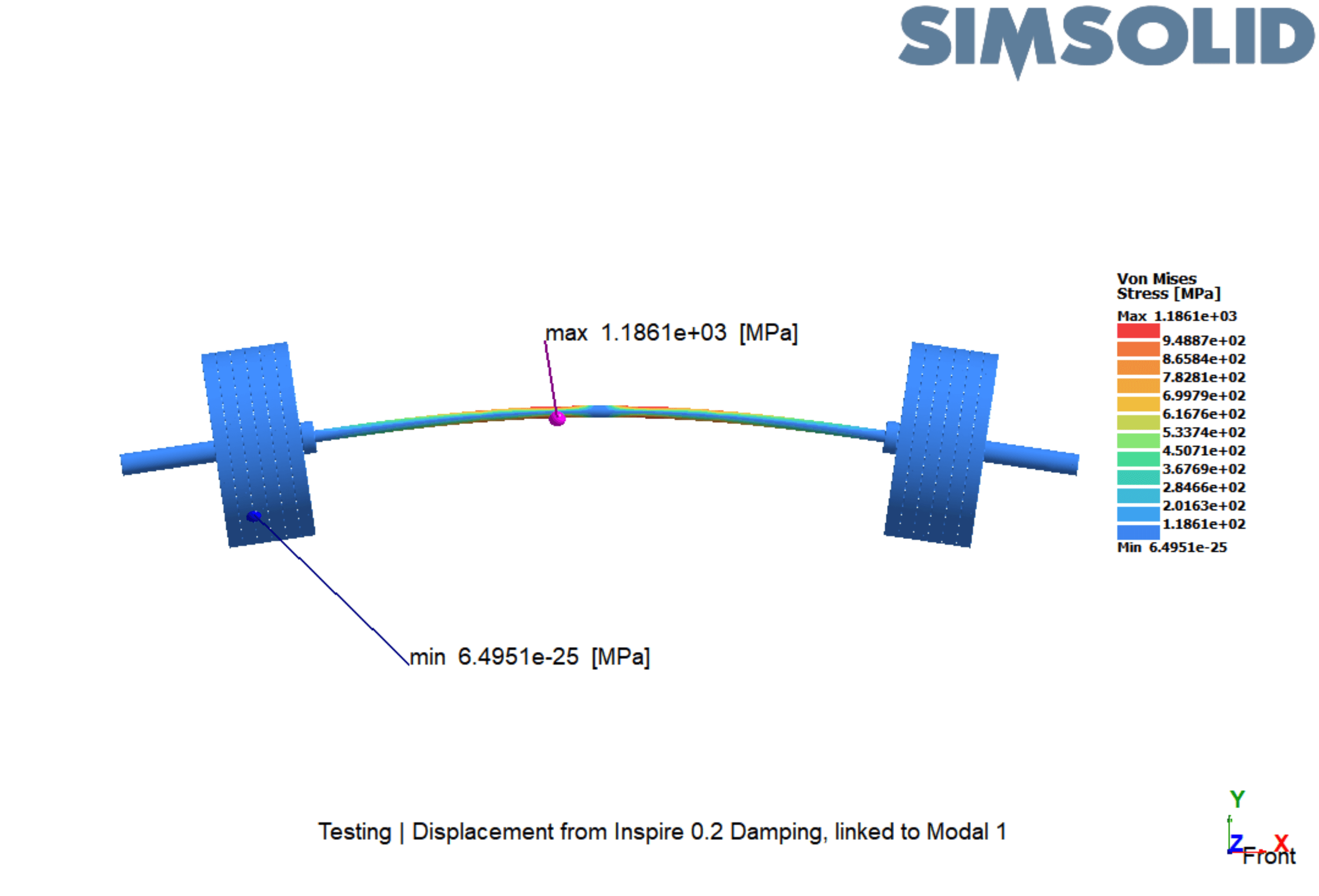
Instead of an immovable support at the middle of the bar, virtual bushings were applied to the model to simulate hands holding the bar throughout the lift. Stiffnesses were tuned to allow for rotation about Z (bar flex), but support in all other degrees of freedom, allowing for more realistic deflection and stress.
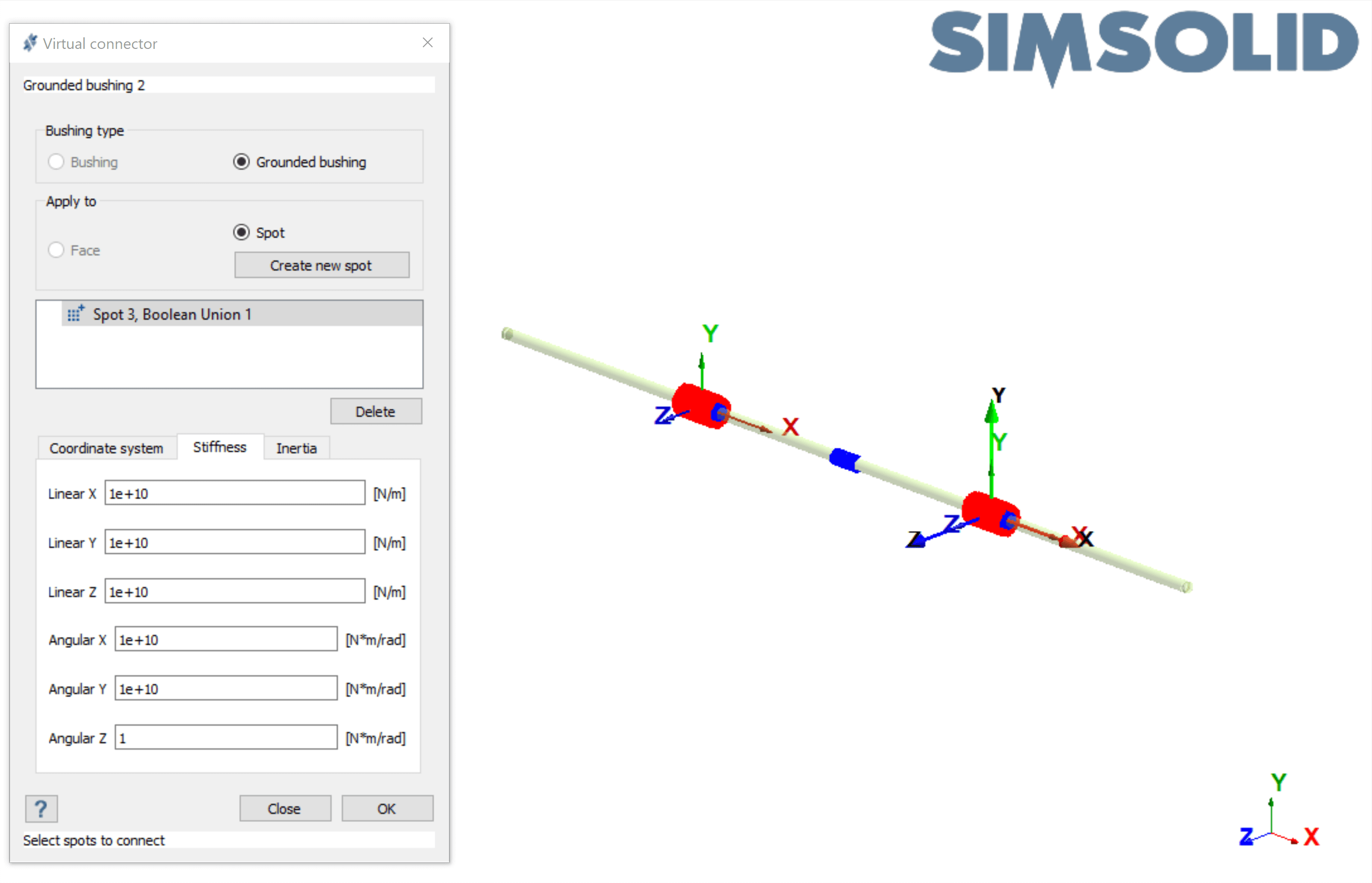
Because we couldn’t use a base excitation with the bushings (no immovable support to excite), the accelerations from the Inspire Motion run were used instead to apply the inertia as if it was moving.
Brought back into SimSolid for a transient dynamics study, the damping was set to 0.3 and 0.5 to compare the impact of both simulation runs. During the 0.3 damping run, a stress result of 612 MPa was found, with quick stress peaks during the largest movements of the lift. The bar could withstand these stresses at very short impulses with no issue. Though in reality, this movement was most likely still slightly underdamped.
During the 0.5 damping run, stress results were 545 MPa, showing that more damping led to less deflection, meaning less stress.
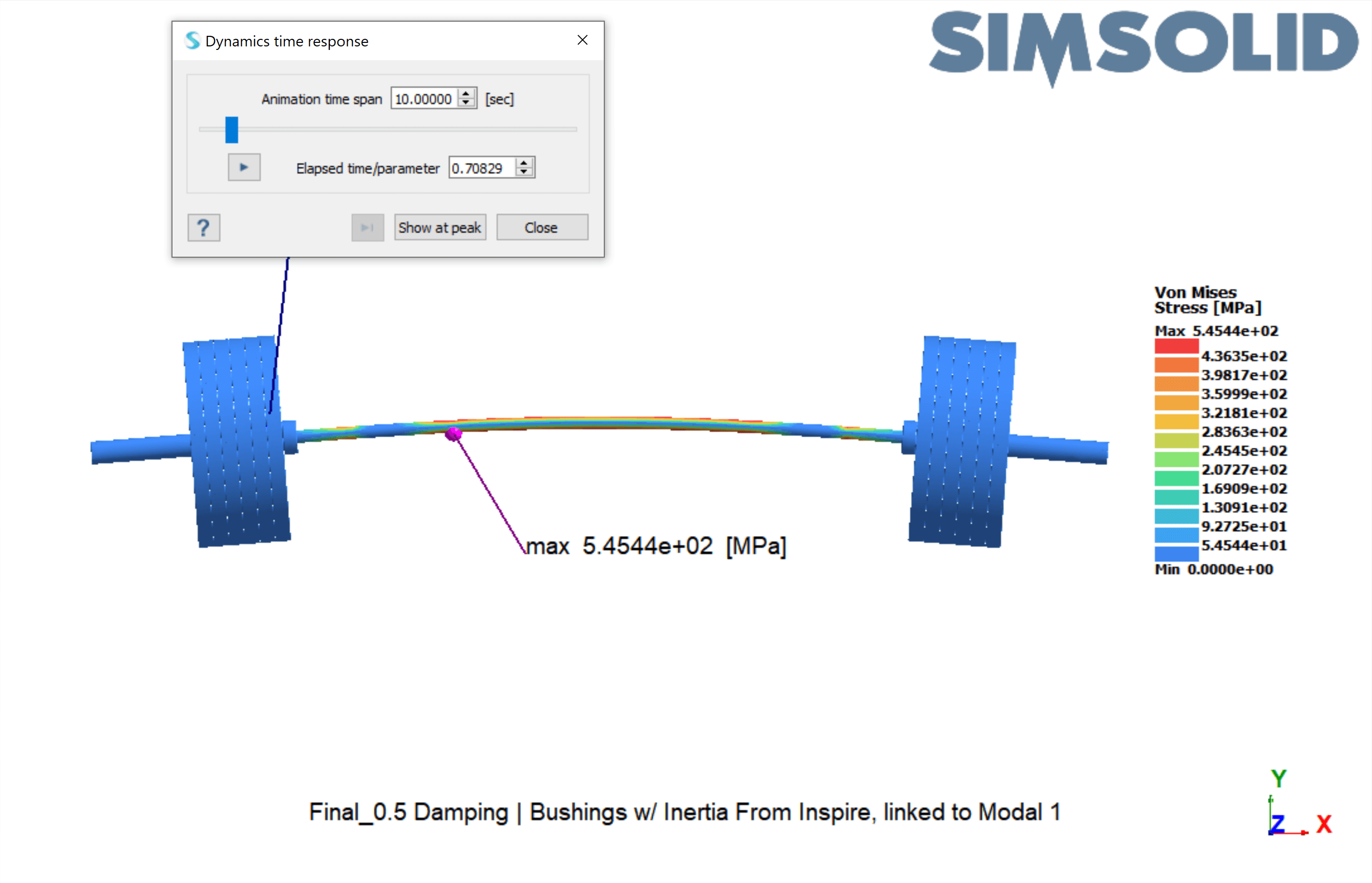
The stress results over the time of the lift presented that the full motion included very quick peaks and a static stress of around 220 MPa.
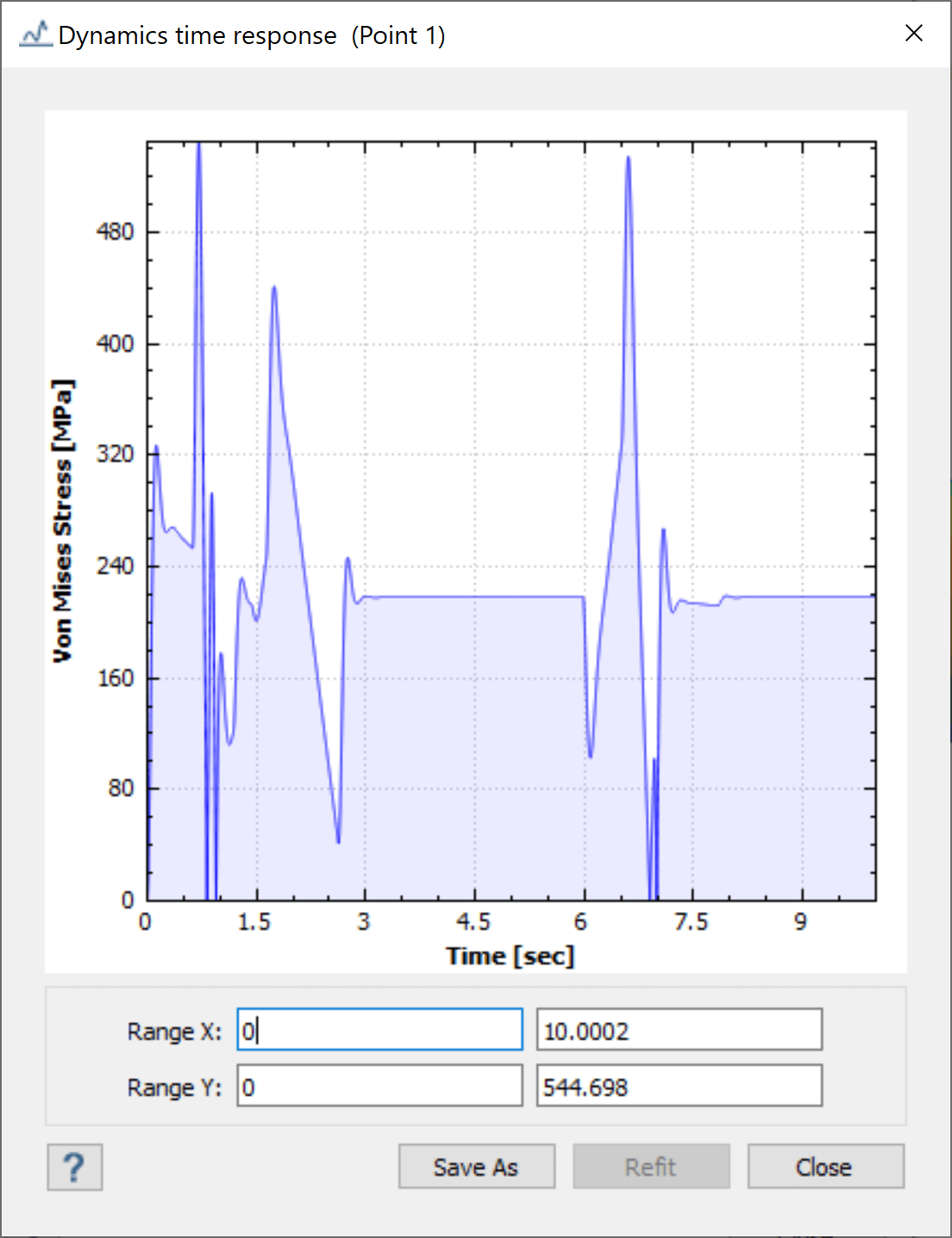
SimSolid dynamically simulated the stresses imparted on a barbell during a world-record clean and jerk movement, showing that the barbell was up to the task of supporting this massive weight. Most barbells have a strength rating of >1000 MPa, meaning they won’t break until stresses exceed that rating. Some also have surface coatings and treatments to help with grip on the bar but can also increase the durability and strength of the bar at the surface.
To perform a more detailed structural analysis on the barbell, Altair OptiStruct was used to model the initial setup of the bar. The total mass including the bar and weights was 280 kilograms, roughly equaling the mass of the bar and weights during the world record lift.
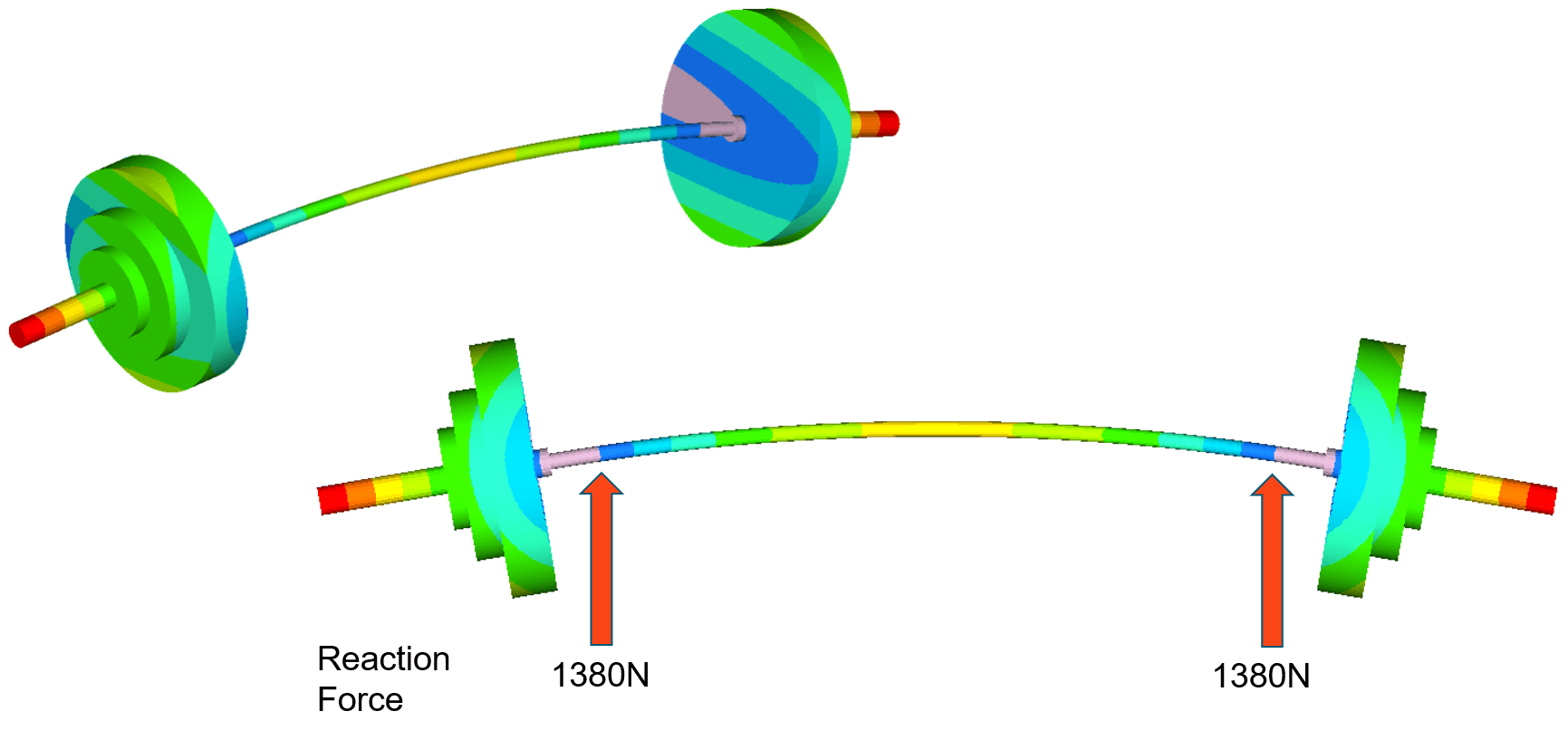
From these simulation images, in order to actually lift the barbell, the athlete would need to provide an upward force greater than 1380 N in each arm. Once the athlete applies that force and brings the barbell above their head, he/she can reduce the magnitude of the upward force to be exactly the same as the barbell’s magnitude to reach equilibrium. This proves that not only does it matter how much weight is lifted, it’s also just as important how fast the weight is lifted to correctly complete the lift.
Once the athlete drops the barbell, considering a 2-meter drop, it would hit the ground with an average velocity of 6.32 m/s, which can cause an impact force of more than 490,000 N on a conventional floor. For safety, this shows the importance of having appropriate equipment like drop pads, where the foam filling will reduce the impact and protect the equipment, floor, and athlete’s feet.
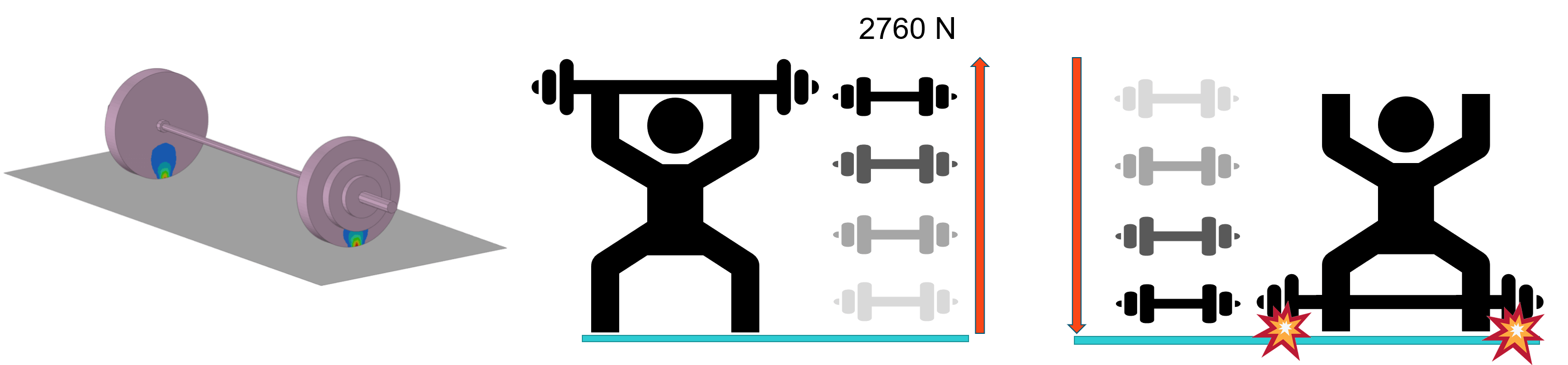
We can conclude that although the peak stresses were very high, the bar could likely withstand them due to their short duration. The key to this simulation was to set the constraints and damping to the most accurate levels possible using SimSolid’s rapid design iteration capabilities.
By studying the nonlinear motion of the bar with OptiStruct, we could observe realistic forces that would occur during the movement. OptiStruct’s proven solver capabilities provides solutions for both linear and nonlinear problems, as well as across statics and dynamics, vibrations, acoustics, fatigue, heat transfer, and multiphysics disciplines.
Eliminating the need for geometry preparation and meshing, SimSolid’s lightning-fast solver was able to produce peak responses and animation results in about thirty seconds per run. This allowed for multiple design scenarios to be quickly simulated and fine-tuned to produce real-world loading and strength conditions.
For more information on Altair’s simulation solutions, visit: https://www.altair.com/simulation-driven-design/.