Controlling Altair SimSolid solution accuracy
Using Altair SimSolid, it is very easy to setup and run a structural simulation. Geometry simplification and editing is not required and there is no laborious, error prone, meshing steps to worry about. Although Altair SimSolid does not have a mesh, there are a number of other, much simpler, ways to control solution accuracy at both a global and part local level. In the following, we will explore how this is done.
The Solution settings dialog is used to specify solution accuracy control values. This is accessed in one of two ways. First, use the “Settings > Solution settings” menu to define global accuracy values that apply to the whole model. Second, select one or more parts and use the right mouse button (RMB) pop-up menu “Part solution settings” to set part local control values that will override the global settings.
In either case, a dialog similar to the following will appear.
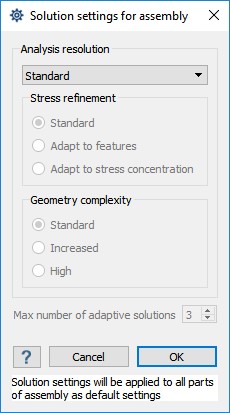
From the dialog, three analysis resolution levels are possible – Standard, Detailed and Custom.
The default setting is Standard. This will provide three adaptive solution passes and is intended to provide the best trade-off of solution speed to solution quality. In most cases, this will be all that is required for general deformation, stresses and load path calculation. A best practice is to always start with this setting.
The second solution quality level is Detailed. This will provide four adaptive solution passes and activates the “Adapt to features” function (see below), to refine stresses more completely. A best practice is to use this setting on local groups of parts where additional stress detail is desired.
The third solution quality level is Custom. This is an expert mode that allows individual control of all solution settings. This should only be used for parts with unusual characteristics or when a fine degree of control is desired. Note that improperly setting values here may make the solution run a long time without any apparent change in accuracy. Caution is recommended when changing these values.
Individual custom controls include:
To get more information on local stresses, the Detailed setting is used. Select one or more parts, use the RMB menu to access the Part solution settings dialog and select Detailed in the analysis resolution pull-down. Now rerun the analysis. This simple two-step process is a fast and easy way to get both overall response and detailed local stress information.
Users wanting even more control can use the Custom setting to increase the number of adaptive passes. Open the global Solution settings dialog, increment the maximum number of adaptive passes and rerun the simulation. Repeat to examine convergence.
To illustrate how this works, consider the following model of a single plate with many small holes subjected to a simple axial load. Here are the results using default solution settings.
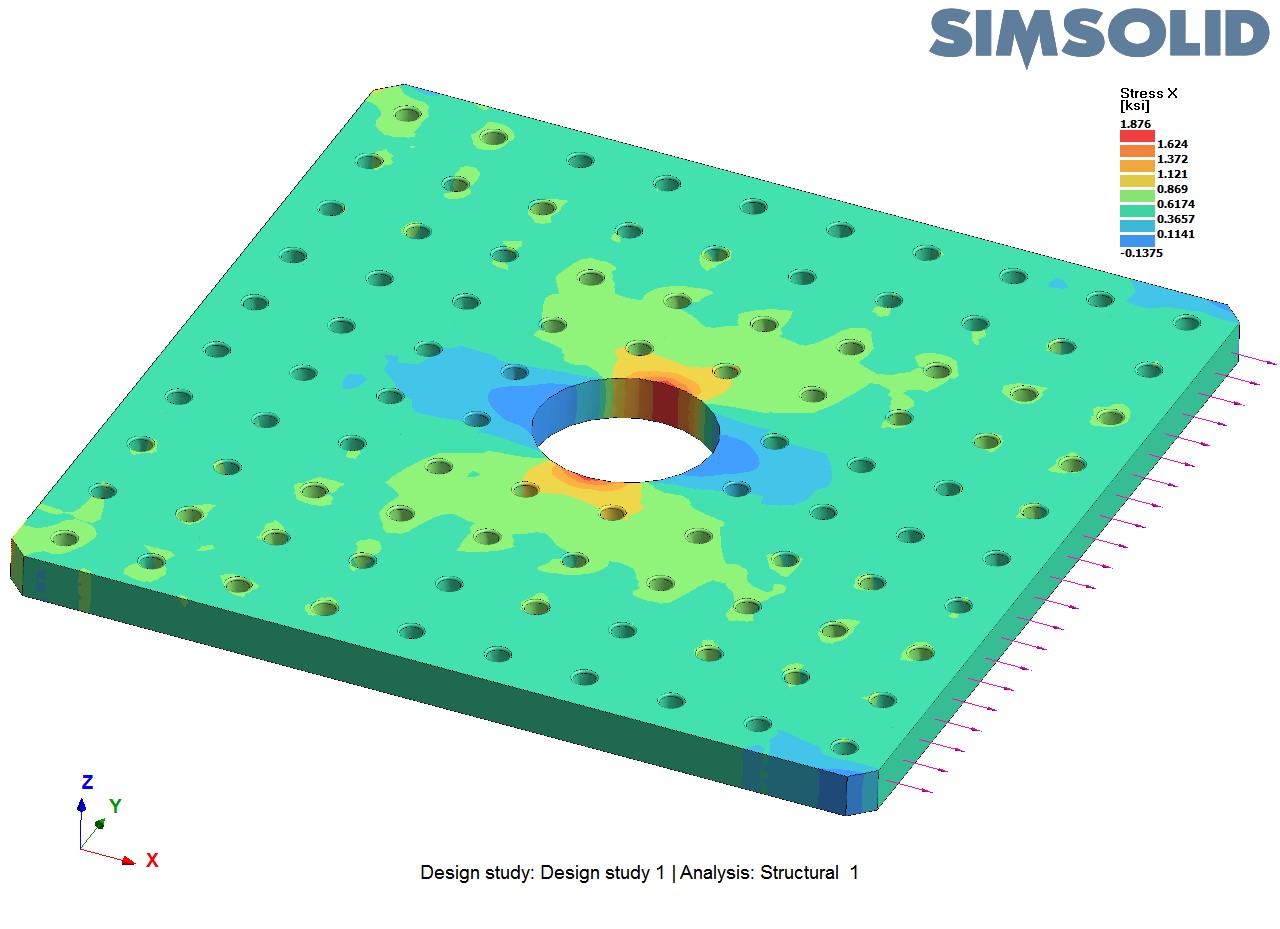
This runs very fast (under 10 seconds) and captures the overall deformation and stress state. However, some stress concentration detail is missing in the small holes. To calculate this effect, go to the solutions setting dialog, select Custom then select the Adapt to stress concentration refinement option and rerun the solution. This stress refinement approach adds special functions that model stress concentrations in cylindrical holes. Now the solution appears as:
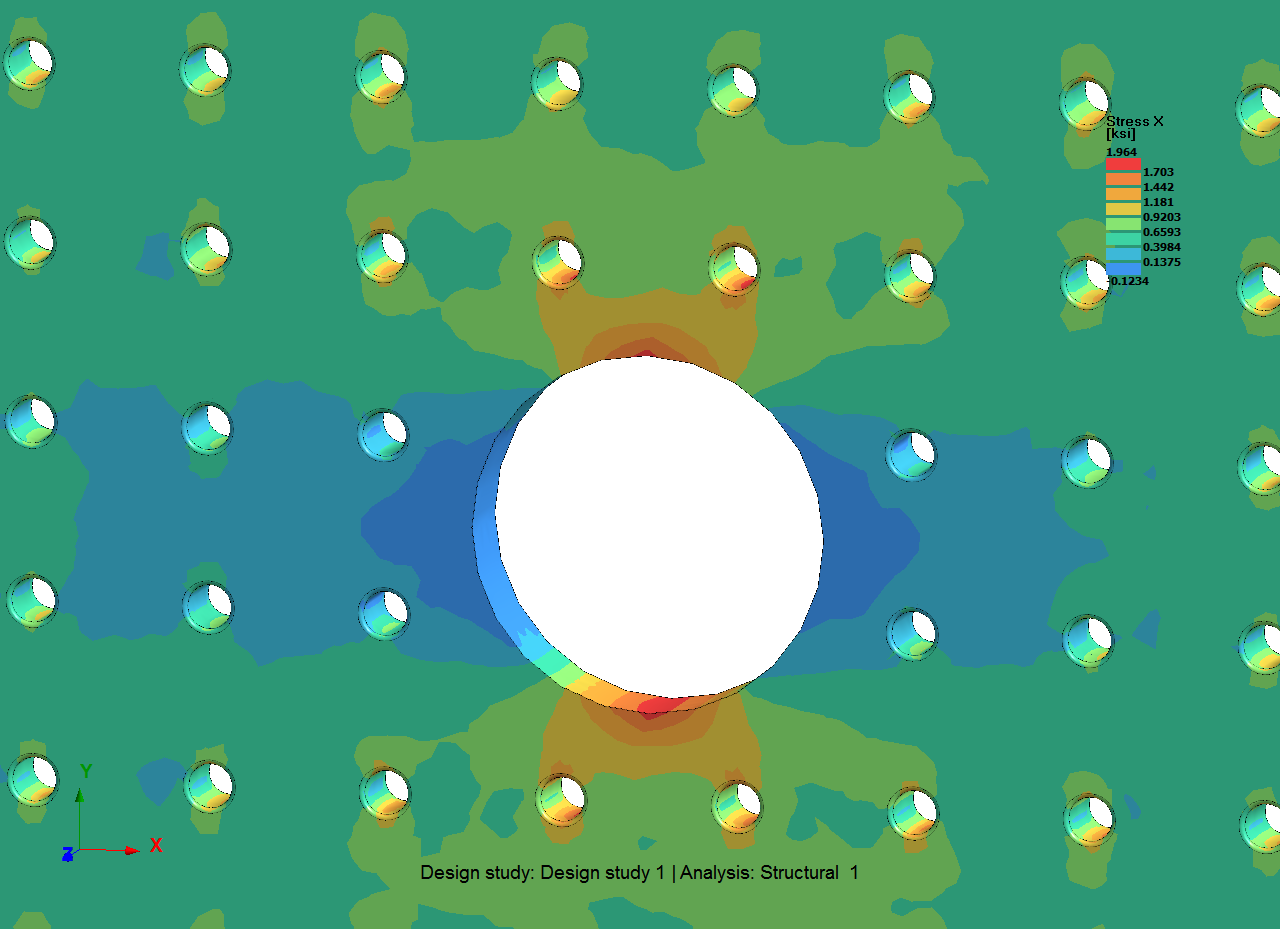
While the overall stress level has not changed substantially, there is now more detail of the stress concentrations in the small holes. This enhanced solution was done on a complex part with 96 small holes including fillets in only 14 seconds. Best of all, it was done without have to spend time doing detailed mesh seeding refinement around each hole as is the case with traditional FEA.
While local cylindrical hole refinement functions offer a fast and accurate way to drill in on stress details, they are only a beginning. As Altair SimSolid becomes more integrated with CAD, these functions will be expanded to more and more geometry types. This high level direct geometry approach has the potential to be faster and more accurate than the simple element based approaches in other FEA products. Go ahead and try it for yourself.
The Solution settings dialog is used to specify solution accuracy control values. This is accessed in one of two ways. First, use the “Settings > Solution settings” menu to define global accuracy values that apply to the whole model. Second, select one or more parts and use the right mouse button (RMB) pop-up menu “Part solution settings” to set part local control values that will override the global settings.
In either case, a dialog similar to the following will appear.
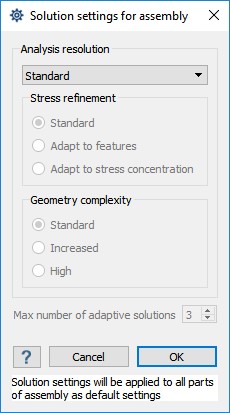
From the dialog, three analysis resolution levels are possible – Standard, Detailed and Custom.
The default setting is Standard. This will provide three adaptive solution passes and is intended to provide the best trade-off of solution speed to solution quality. In most cases, this will be all that is required for general deformation, stresses and load path calculation. A best practice is to always start with this setting.
The second solution quality level is Detailed. This will provide four adaptive solution passes and activates the “Adapt to features” function (see below), to refine stresses more completely. A best practice is to use this setting on local groups of parts where additional stress detail is desired.
The third solution quality level is Custom. This is an expert mode that allows individual control of all solution settings. This should only be used for parts with unusual characteristics or when a fine degree of control is desired. Note that improperly setting values here may make the solution run a long time without any apparent change in accuracy. Caution is recommended when changing these values.
Individual custom controls include:
- Max number of adaptive solutions – Altair SimSolid employs a proprietary adaptive technology to automatically refine the solution in the areas where it is necessary to achieve the highest accuracy. The default maximum number of adaptive iterations is set to 3 for Standard and 4 for Detailed. This is a primary control to increase solution refinement. Best practice is to use this as the main control for convergence studies. This will rarely need to be set higher than 6 passes. Note the number of passes can be set on a local basis as well. The adaption does not have to be increased uniformly over the entire model.
- Stress refinement – provides options to activate additional stress refinement functions. The option, Adapt to features, uses special logic that is has more aggressive adaptivity for steep stress gradient areas in local feature areas. The option, Adapt to stress concentration, uses special function for stress concentrations in vicinity of cylindrical holes. Note, the Adapt to stress concentration option is slightly more computationally expensive to run. A best practice is to use this locally on a part by part basis. Both apply only to structural linear and nonlinear statics, they are not used in modal or thermal analyses.
- Geometry complexity – This is used to classify the overall geometric complexity of each part – Standard, Increased or High. The default is Standard. In most cases, this will not need to be adjusted manually. A best practice is to increase this locally on a part-by-part basis. This is typically only required for thinned walled solids, doubly curved shells or parts with extreme aspect ratios.
Solution controls strategies
Using these controls are extremely simple. Standard solutions settings are the default so initially nothing extra need be specified. An analysis done with these settings is intended to provide a quality initial analysis. General load paths, stress distribution, reaction forces or fundamental vibration frequencies can be easily found using this setting.To get more information on local stresses, the Detailed setting is used. Select one or more parts, use the RMB menu to access the Part solution settings dialog and select Detailed in the analysis resolution pull-down. Now rerun the analysis. This simple two-step process is a fast and easy way to get both overall response and detailed local stress information.
Solution convergence
Altair SimSolid controls solution accuracy using smart functions and a unique automatic adaptive process. In contrast to FEA, the adaptivity is driven by absolute measures of approximation errors. In Altair SimSolid, adaptivity is not an option, it is always active. In most cases, the two step process described above is all that is required to get a quality converged analysis solution.Users wanting even more control can use the Custom setting to increase the number of adaptive passes. Open the global Solution settings dialog, increment the maximum number of adaptive passes and rerun the simulation. Repeat to examine convergence.
Stress concentration example
One of the most interesting aspects of the Altair SimSolid technology is its ability to add high order functions to refine the solution field. Different functions can be used for specific types of geometry. This allows many options for doing detailed stress studies that are not always practical in traditional FEA applications.To illustrate how this works, consider the following model of a single plate with many small holes subjected to a simple axial load. Here are the results using default solution settings.
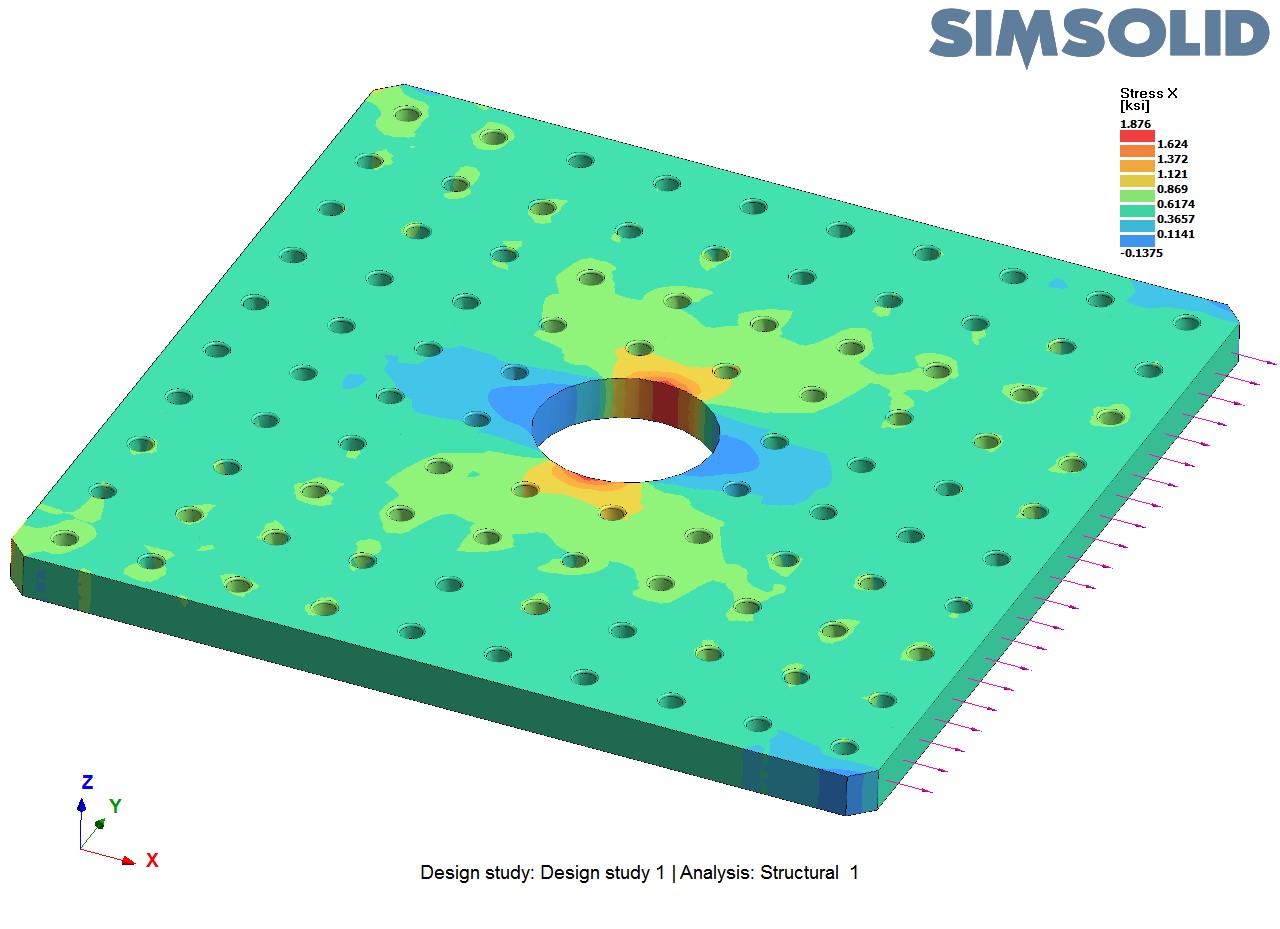
This runs very fast (under 10 seconds) and captures the overall deformation and stress state. However, some stress concentration detail is missing in the small holes. To calculate this effect, go to the solutions setting dialog, select Custom then select the Adapt to stress concentration refinement option and rerun the solution. This stress refinement approach adds special functions that model stress concentrations in cylindrical holes. Now the solution appears as:
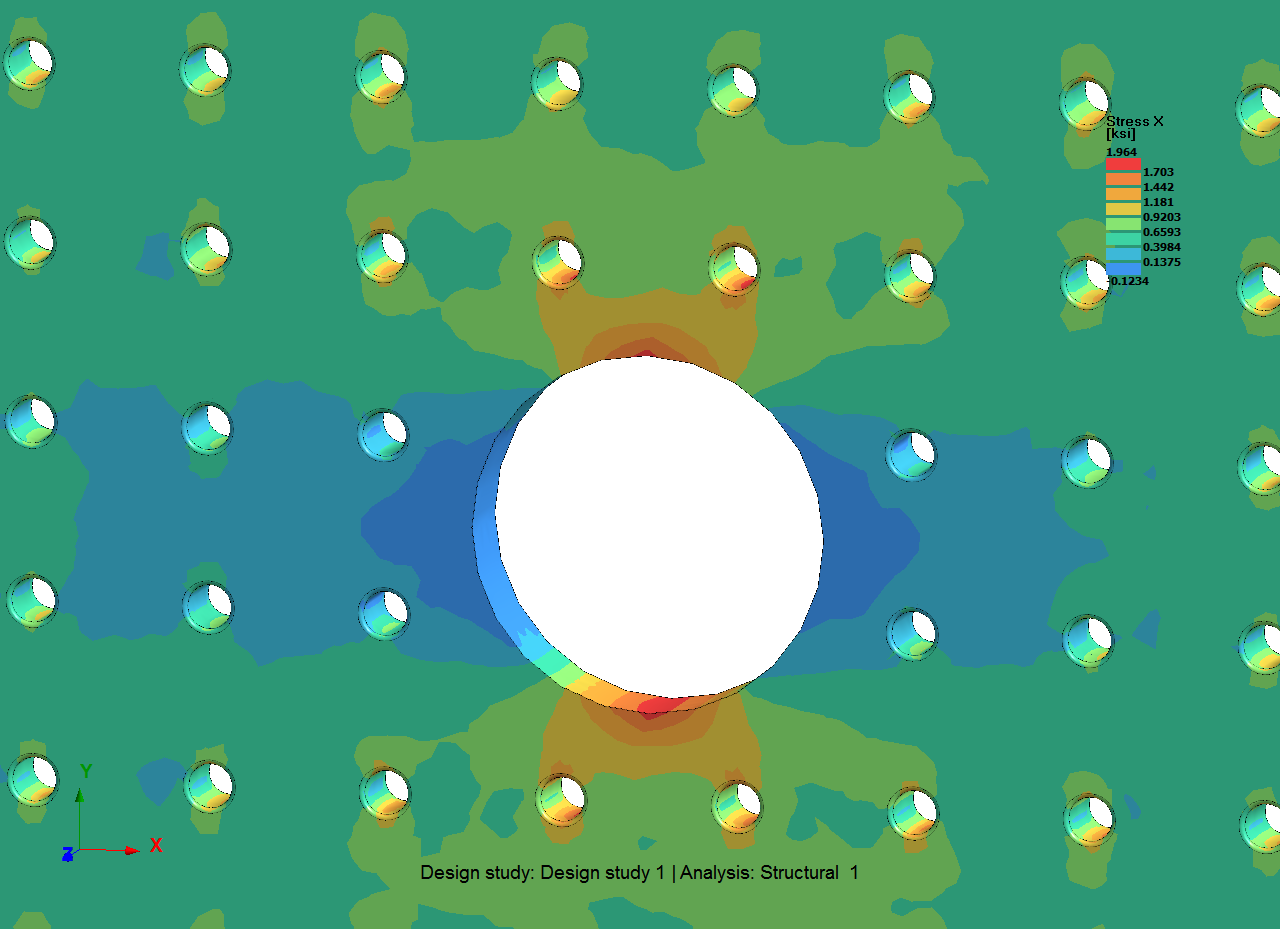
While the overall stress level has not changed substantially, there is now more detail of the stress concentrations in the small holes. This enhanced solution was done on a complex part with 96 small holes including fillets in only 14 seconds. Best of all, it was done without have to spend time doing detailed mesh seeding refinement around each hole as is the case with traditional FEA.
While local cylindrical hole refinement functions offer a fast and accurate way to drill in on stress details, they are only a beginning. As Altair SimSolid becomes more integrated with CAD, these functions will be expanded to more and more geometry types. This high level direct geometry approach has the potential to be faster and more accurate than the simple element based approaches in other FEA products. Go ahead and try it for yourself.