Design the Difference - Unlock the Potential of Additive Manufacturing
Altair at formnext 2016
Additive manufacturing is one of the hottest topics in manufacturing today. Everybody talks about it, and there is basically no engineer that hasn't been asked by his or her boss if a part could not be printed instead of using traditional methods to manufacture it. At formnext 2016 last week in Frankfurt, Germany, additive manufacturing was an integral part of the event. There was an almost overwhelming amount of information on additive manufacturing available and no matter whether someone was new to the topic or already very experienced in applying this new manufacturing method, every visitor could learn something new.
Hall 3.1. was filled with hardware providers, consultants, and material experts demonstrating their solutions. Altair was one of the few software providers present on the show floor, adding its experience in design, optimization, and simulation to the presented solution spectrum. Altair shared the exhibition space with its partner Airbus APWorks, a company that stands for the development of completely new components and products by leveraging the triad of re-engineering, material optimization, and 3D printing.
With the theme "Design the Difference - Unlock the Potential of Additive Manufacturing", Altair presented the latest versions of its simulation software suite HyperWorks® 14.0, and concept design and optimization tools solidThinking Evolve® and Inspire® 2016, with an overall focus on new design processes for the development and manufacturing of innovative products.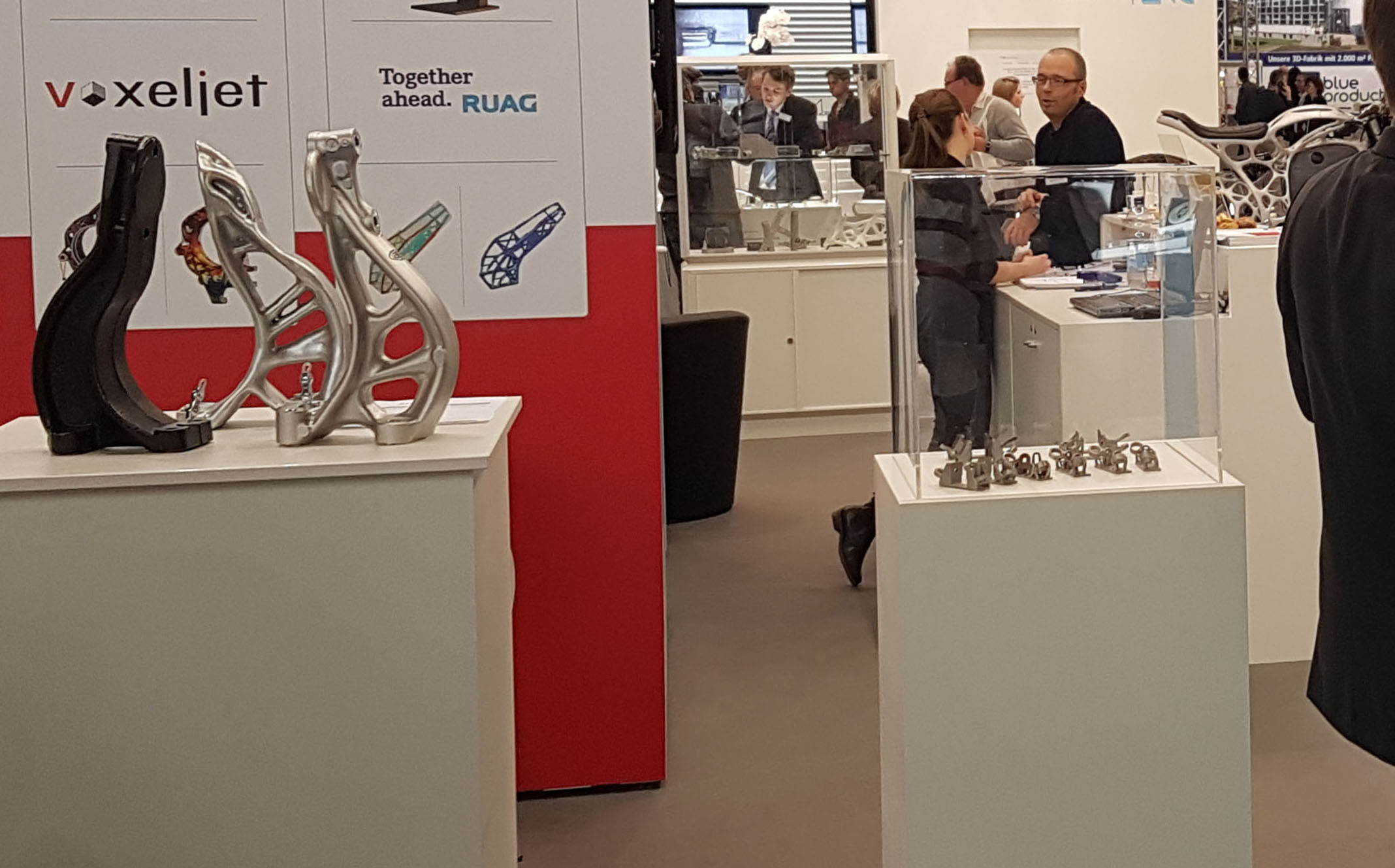
Highlights at the booth were Altair's Simulation-driven Innovation™ approach, the development process chain of the Airbus APWorks’ Light Rider, the world's first prototype of a 3D printed electric motorcycle, the 3D printed antenna bracket by RUAG Space, and a bracket for a low pressure gas turbine redesigned and manufactured by Sintavia. Attendees also gained insight into the development and manufacturing processes of a cast aluminum component, developed jointly with Altair’s partners HBM nCode and voxeljet.
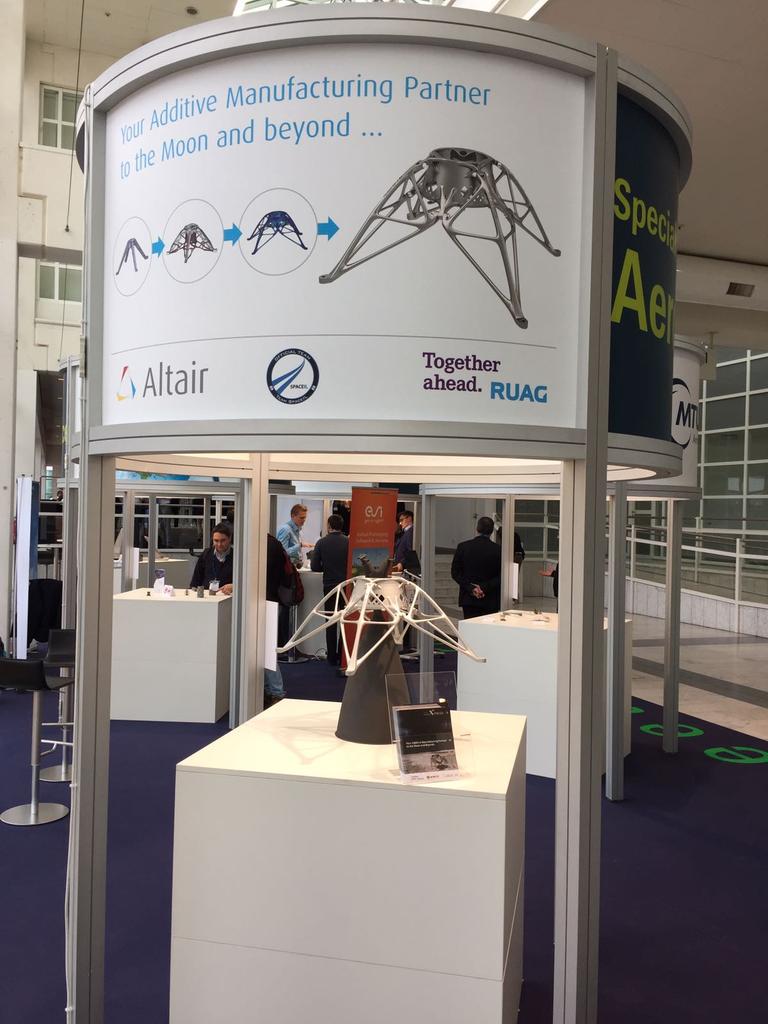
The Light Rider is an amazing example of the importance of the design process in creating complex structures that are light, strong, cost-efficient and additively manufactured. Its complex branched hollow structure could not have been realized with conventional manufacturing methods such as welding or milling, and its entirely new design could only be realized thanks to topology optimization and the use of Scalmalloy®, a high performance aluminum alloy developed by Airbus for metal 3D printing. In addition to the development process presented by Altair, APWorks showed the actual motorcycle at their part of the booth. Here visitors could get a firsthand experience of what the 3D printed motorcycle frame with its design inspired by nature looks and feels like.
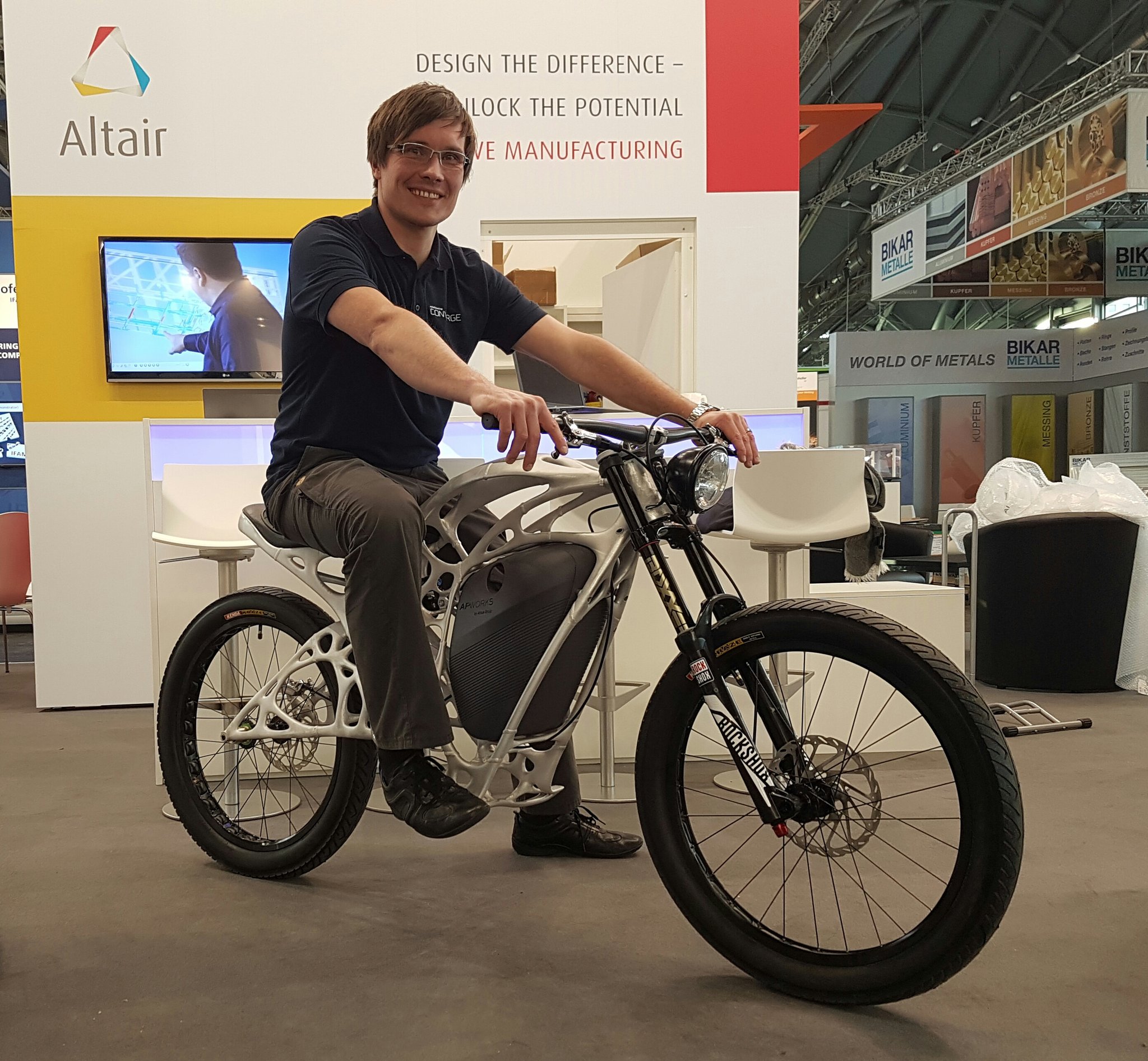
Furthermore, Altair presented several other products and components jointly with other partners. All presented exhibition pieces were designed, developed, and optimized with Altair solutions. Among these were the so called "spider bracket", a lattice structure component for architectural applications, as well as the Robot Bike, both presented at the Renishaw booth and SpaceIL's Moon Lander, developed and printed by RUAG Space for SpaceIL's participation in the Google lunar XPRICE, presented in the Aerospace show. Exhibition pieces at the Altair booth also included best use cases for traditional manufacturing methods, such as casting or welding. The presented examples were the LEIBER bracket and the technology demonstrator of a casted wheel carrier.
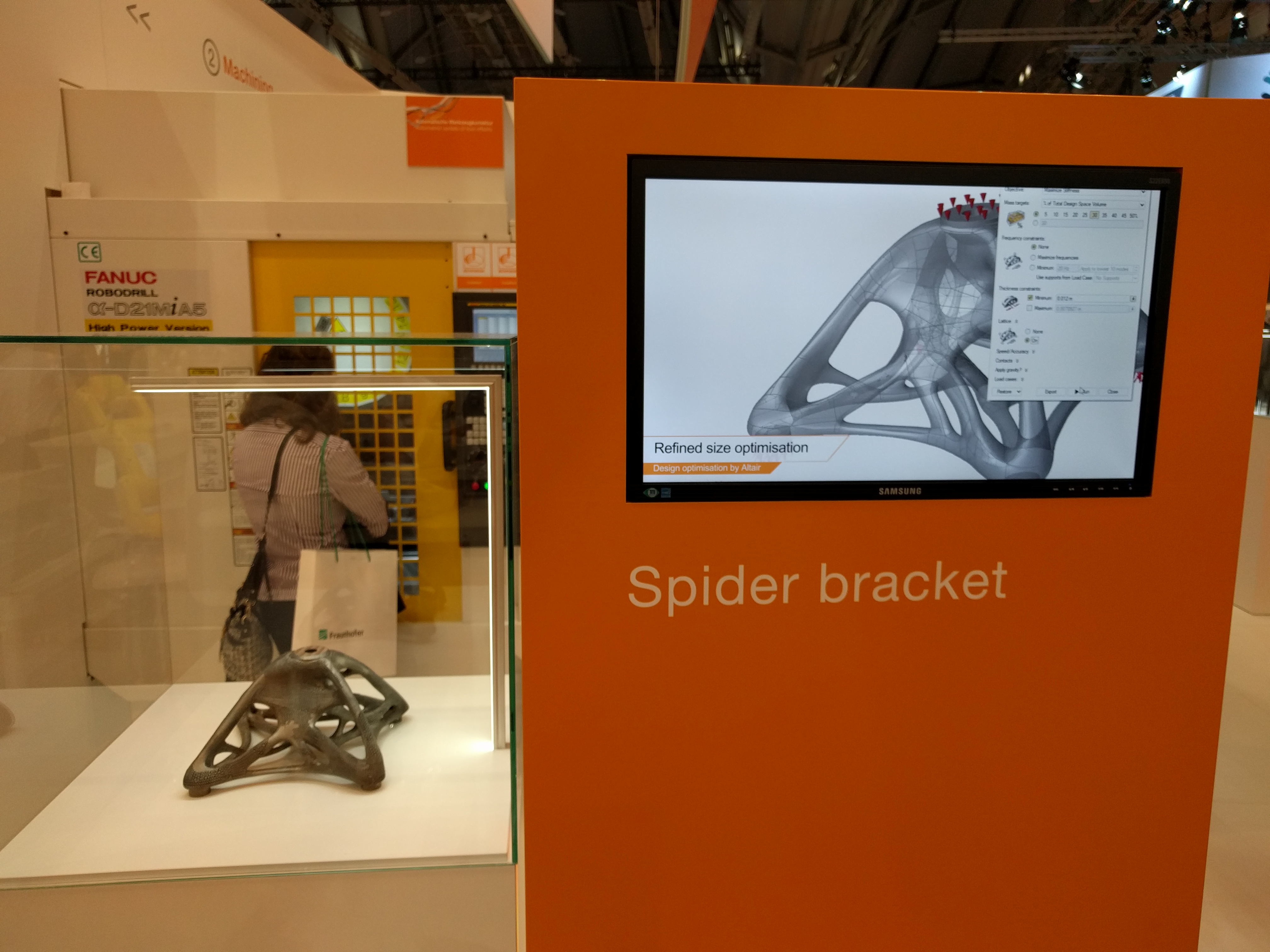
Learn more about Altair's solutions for traditional and additive manufacturing and check out the Altair HyperWorks resource library for more success stories like the Light Rider, Robot Bike, and LEIBER bracket.
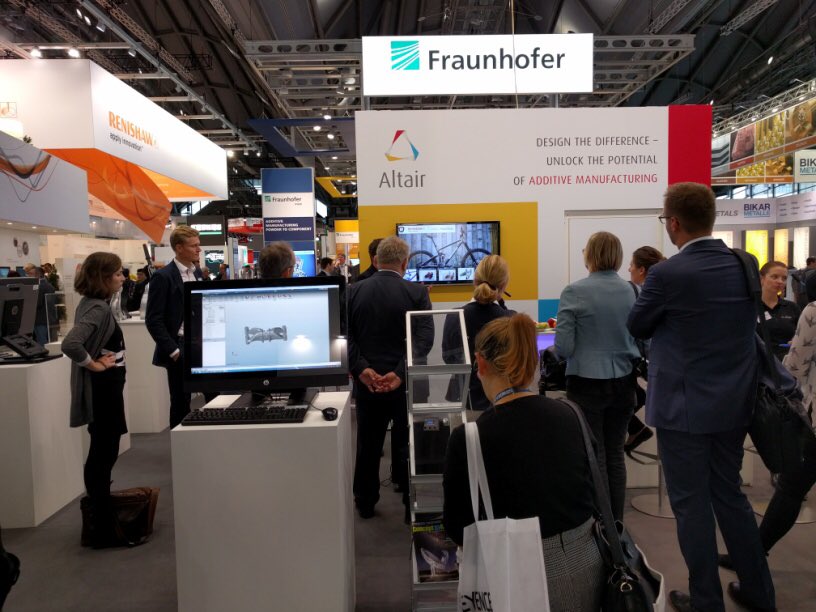
Additive manufacturing is one of the hottest topics in manufacturing today. Everybody talks about it, and there is basically no engineer that hasn't been asked by his or her boss if a part could not be printed instead of using traditional methods to manufacture it. At formnext 2016 last week in Frankfurt, Germany, additive manufacturing was an integral part of the event. There was an almost overwhelming amount of information on additive manufacturing available and no matter whether someone was new to the topic or already very experienced in applying this new manufacturing method, every visitor could learn something new.
With the theme "Design the Difference - Unlock the Potential of Additive Manufacturing", Altair presented the latest versions of its simulation software suite HyperWorks® 14.0, and concept design and optimization tools solidThinking Evolve® and Inspire® 2016, with an overall focus on new design processes for the development and manufacturing of innovative products.
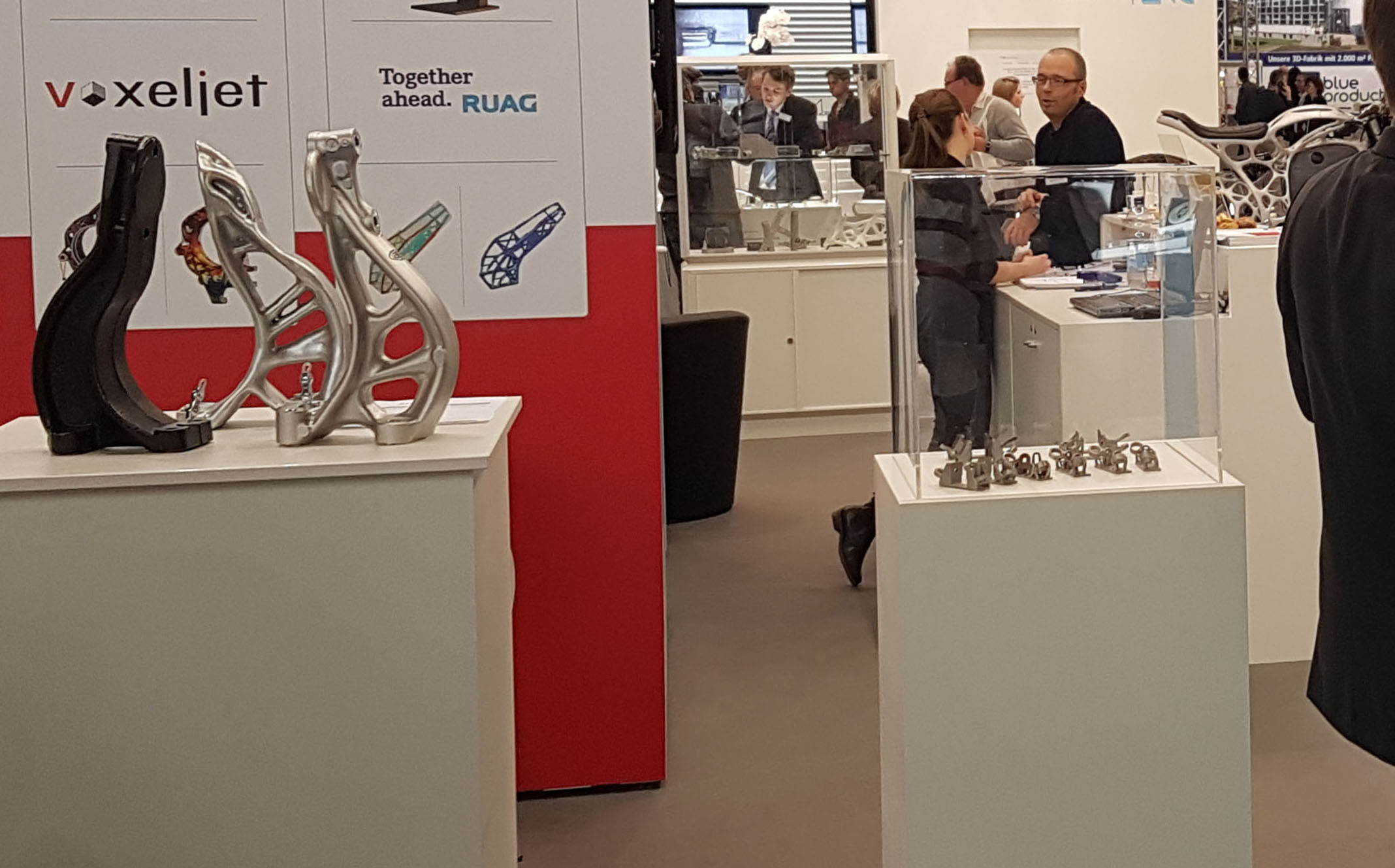
Highlights at the booth were Altair's Simulation-driven Innovation™ approach, the development process chain of the Airbus APWorks’ Light Rider, the world's first prototype of a 3D printed electric motorcycle, the 3D printed antenna bracket by RUAG Space, and a bracket for a low pressure gas turbine redesigned and manufactured by Sintavia. Attendees also gained insight into the development and manufacturing processes of a cast aluminum component, developed jointly with Altair’s partners HBM nCode and voxeljet.
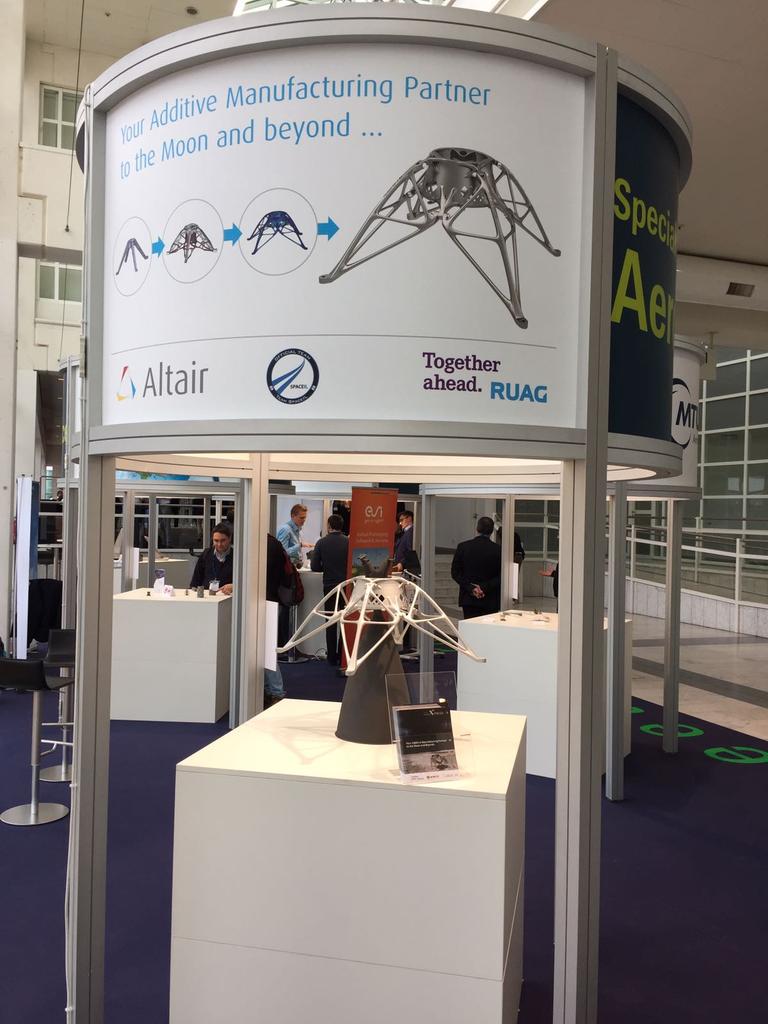
The Light Rider is an amazing example of the importance of the design process in creating complex structures that are light, strong, cost-efficient and additively manufactured. Its complex branched hollow structure could not have been realized with conventional manufacturing methods such as welding or milling, and its entirely new design could only be realized thanks to topology optimization and the use of Scalmalloy®, a high performance aluminum alloy developed by Airbus for metal 3D printing. In addition to the development process presented by Altair, APWorks showed the actual motorcycle at their part of the booth. Here visitors could get a firsthand experience of what the 3D printed motorcycle frame with its design inspired by nature looks and feels like.
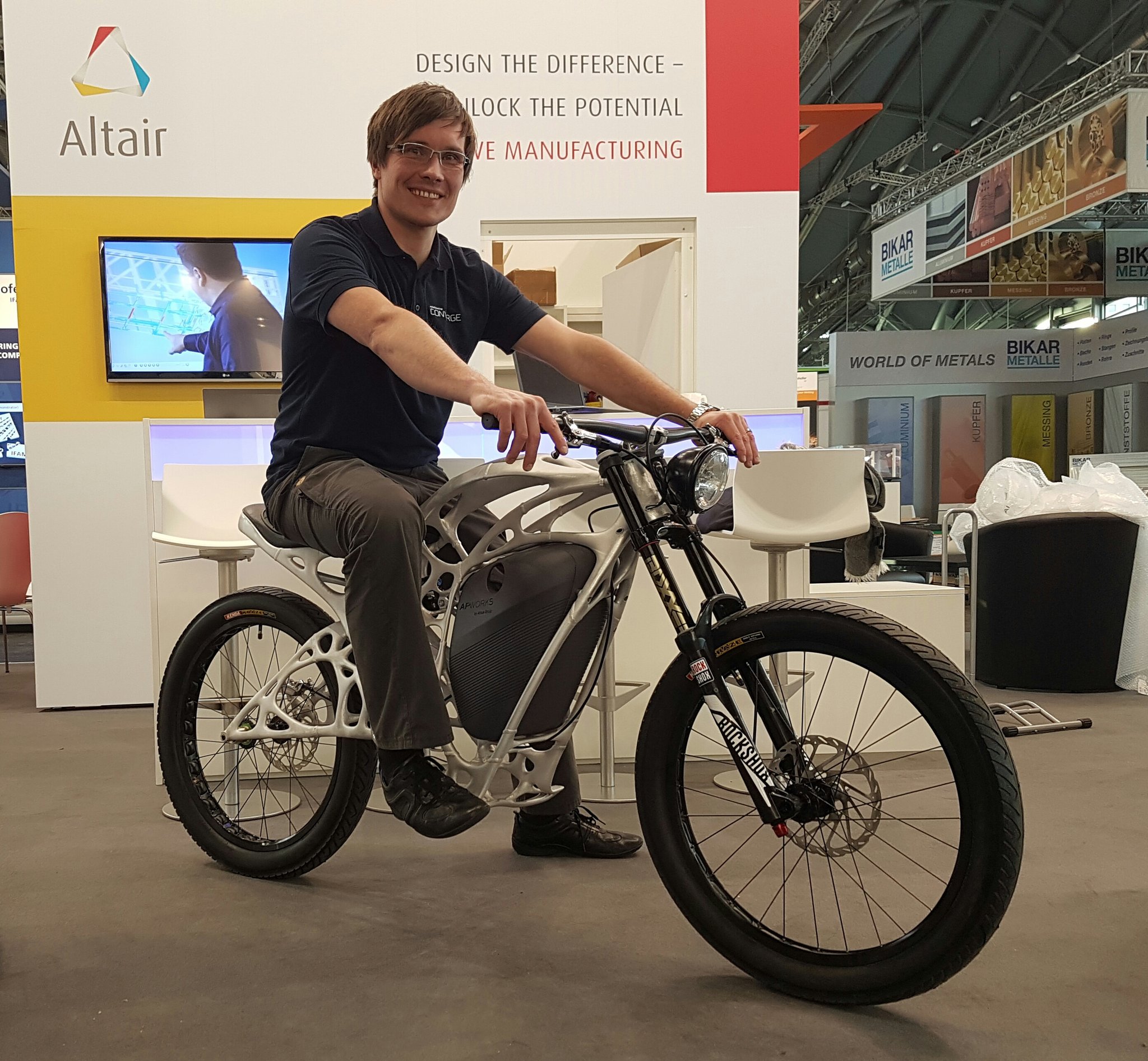
Furthermore, Altair presented several other products and components jointly with other partners. All presented exhibition pieces were designed, developed, and optimized with Altair solutions. Among these were the so called "spider bracket", a lattice structure component for architectural applications, as well as the Robot Bike, both presented at the Renishaw booth and SpaceIL's Moon Lander, developed and printed by RUAG Space for SpaceIL's participation in the Google lunar XPRICE, presented in the Aerospace show. Exhibition pieces at the Altair booth also included best use cases for traditional manufacturing methods, such as casting or welding. The presented examples were the LEIBER bracket and the technology demonstrator of a casted wheel carrier.
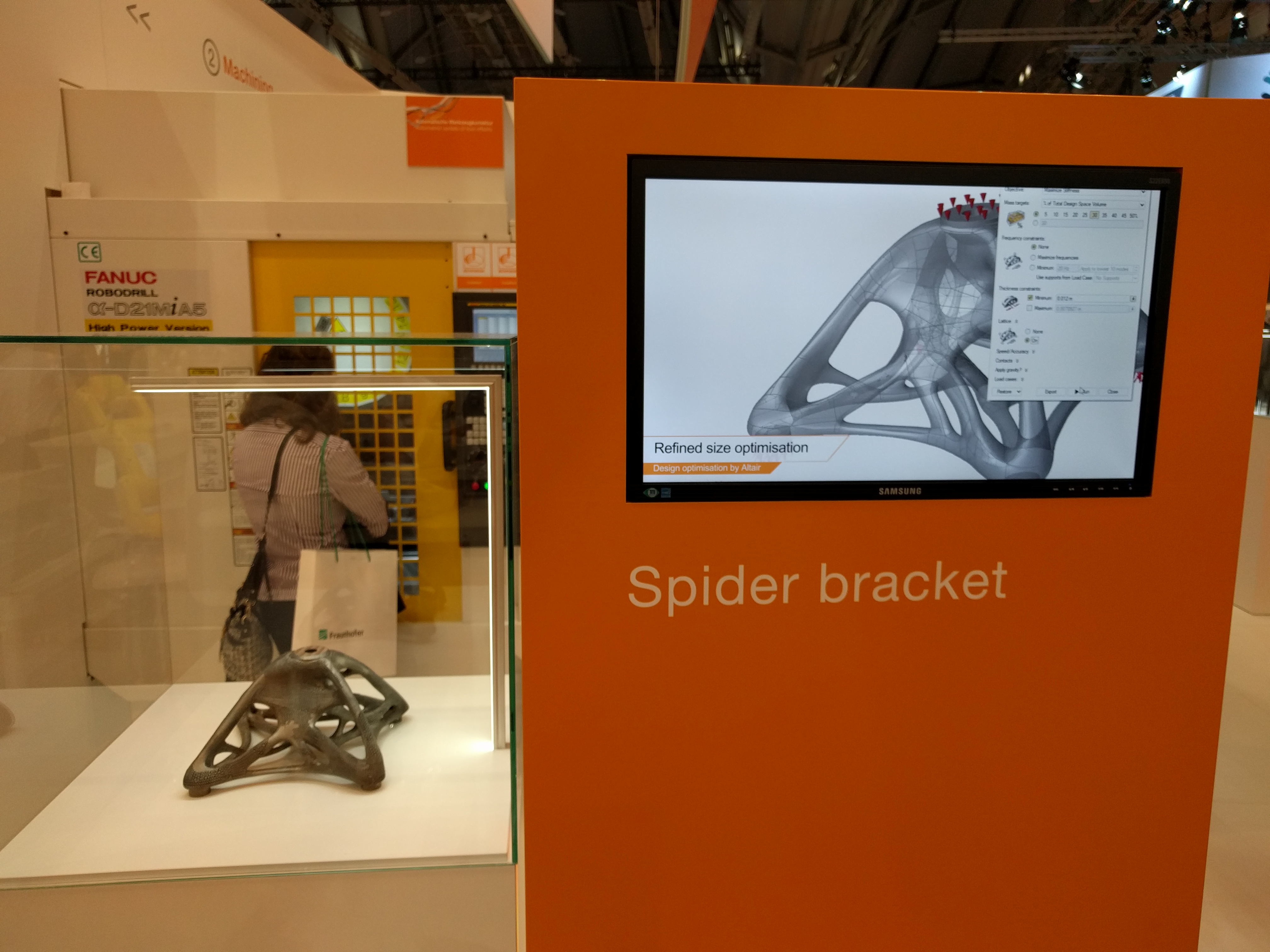
Learn more about Altair's solutions for traditional and additive manufacturing and check out the Altair HyperWorks resource library for more success stories like the Light Rider, Robot Bike, and LEIBER bracket.
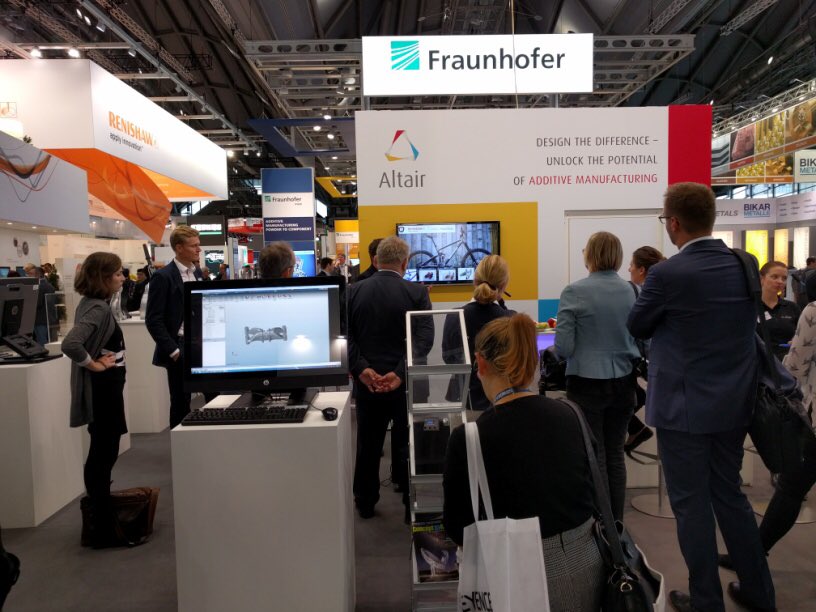