E-Motor Design Using Multiphysics Optimization
The powertrain of electric vehicles must be developed to consider and finally fulfill an increasing number of internal, customer and legal requirements and must be developed with increasing ambitions concerning target fulfillment. The classical development strategies foresee individual development routes for different requirements and different organizational structures to be responsible for the fulfillment of different requirements. Thus, the development takes place in several parallel disciplines where negotiations and unfavorable compromises concerning attribute performance are common to reach a final acceptable design. More integrated and holistic development strategies will be necessary in the future to better meet future requirements without significant sacrifices on target fulfillment. Optimization methodologies and processes offer opportunities to support such integrated development strategies. However, such optimization strategies must be designed to account for different requirements resulting from different physical phenomena simultaneously, i.e. multiphysics optimization.
Porsche AG is responding to the challenge of e-mobility by developing high performance electric powertrains which will meet every Porsche standard in terms of performance, fuel efficiency, driving dynamics, and everyday practicality.
Altair is a software and consulting company with the vision to transform product design and organizational decision making by applying simulation, optimization, and high-performance computing throughout product lifecycles. Altair is leading in defining, developing, and integrating simulation-driven design process and methodology at automotive OEMs.
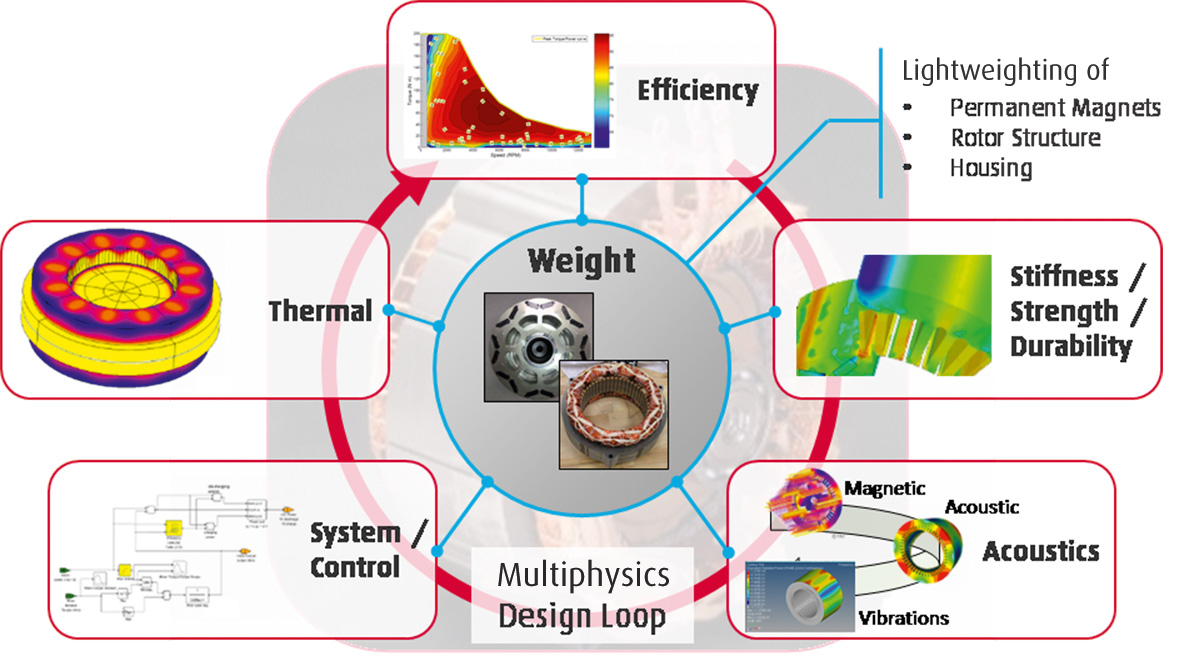
This paper offers insights on how the advanced drivetrain development team at Porsche AG, together with Altair, has approached the challenge of improving the total design balance in e-motor development. The classical motor efficiency/power design problem is coupled with other physics to account for thermal effects, structural boundary conditions and vibrations. Additional effects of the inverter on the motor performance will also be evaluated by integration of both controls and physical modeling. The objective of the design optimization is to maximize torque and power under defined driving conditions. Simultaneously, rotor stresses, motor vibrations and motor temperature must be kept within certain limits. The design process account for both individual motor design points (e.g. max torque) and evaluation in standardized driving cycles using reduced order models based on data provided by full-order models in the Altair suite of tools. It will be shown how different physics simulation and optimization tools.
It will be shown how different physics simulation and optimization tools are combined and integrated to create a process for multiphysics e-motor optimization. Some details on coupling strategies will be discussed and It will be shown that such process has the potential to improve the total design balance compared to classical motor design methodologies. The presentation will end with summary and outlook how multiphysics e-motor development will change in the next few years.
Porsche AG is responding to the challenge of e-mobility by developing high performance electric powertrains which will meet every Porsche standard in terms of performance, fuel efficiency, driving dynamics, and everyday practicality.
Altair is a software and consulting company with the vision to transform product design and organizational decision making by applying simulation, optimization, and high-performance computing throughout product lifecycles. Altair is leading in defining, developing, and integrating simulation-driven design process and methodology at automotive OEMs.
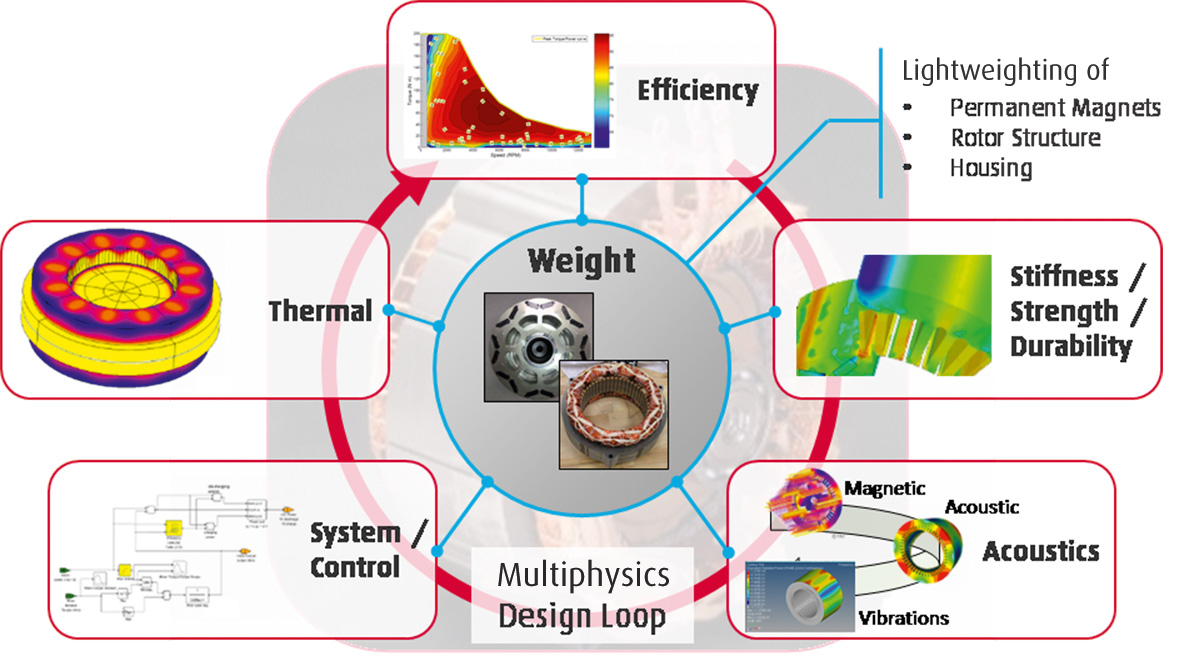
This paper offers insights on how the advanced drivetrain development team at Porsche AG, together with Altair, has approached the challenge of improving the total design balance in e-motor development. The classical motor efficiency/power design problem is coupled with other physics to account for thermal effects, structural boundary conditions and vibrations. Additional effects of the inverter on the motor performance will also be evaluated by integration of both controls and physical modeling. The objective of the design optimization is to maximize torque and power under defined driving conditions. Simultaneously, rotor stresses, motor vibrations and motor temperature must be kept within certain limits. The design process account for both individual motor design points (e.g. max torque) and evaluation in standardized driving cycles using reduced order models based on data provided by full-order models in the Altair suite of tools. It will be shown how different physics simulation and optimization tools.
It will be shown how different physics simulation and optimization tools are combined and integrated to create a process for multiphysics e-motor optimization. Some details on coupling strategies will be discussed and It will be shown that such process has the potential to improve the total design balance compared to classical motor design methodologies. The presentation will end with summary and outlook how multiphysics e-motor development will change in the next few years.