How Did Simulation Help Felix Rosenqvist Walk Away From His Crash at the Detroit Grand Prix?
The recent Detroit Grand Prix was filled with the usual adrenaline-fueled excitement you’d expect from an IndyCar Series race, complete with intense overtakes and high-speed chases. One driver however was reminded just how dangerous this sport can be. As Felix Rosenqvist prepared to swing around turn six, his car lost traction and smashed into the tire-lined concrete barrier, thankfully avoiding any major injury. Check out the video below to see. Word of warning, it’s not an easy watch.
Designing race cars includes a range of computer-aided engineering (CAE) tasks including the meshing of parts and full vehicles, finite element analysis (FEA) of components, crash test simulations, optimization, and computational fluid dynamics (CFD)
for wind resistance analysis. As a result, every single part of the vehicle is designed and optimized and then verified via crash test and aerodynamic performance simulations. This verification process aims to fulfill the rigorous testing requirements
of the Fédération Internationale de l’Automobile (FIA) before a physical prototype is even considered.
Finding the Balance
While speed and skill may ultimately win the race, ensuring the safety of the driver
is imperative, creating an additional layer of complexity that engineers must consider. The holy grail of race car design is one that is strong and lightweight. This ensures the performance of the car is competitive while simultaneously
ensuring the safety of the driver.
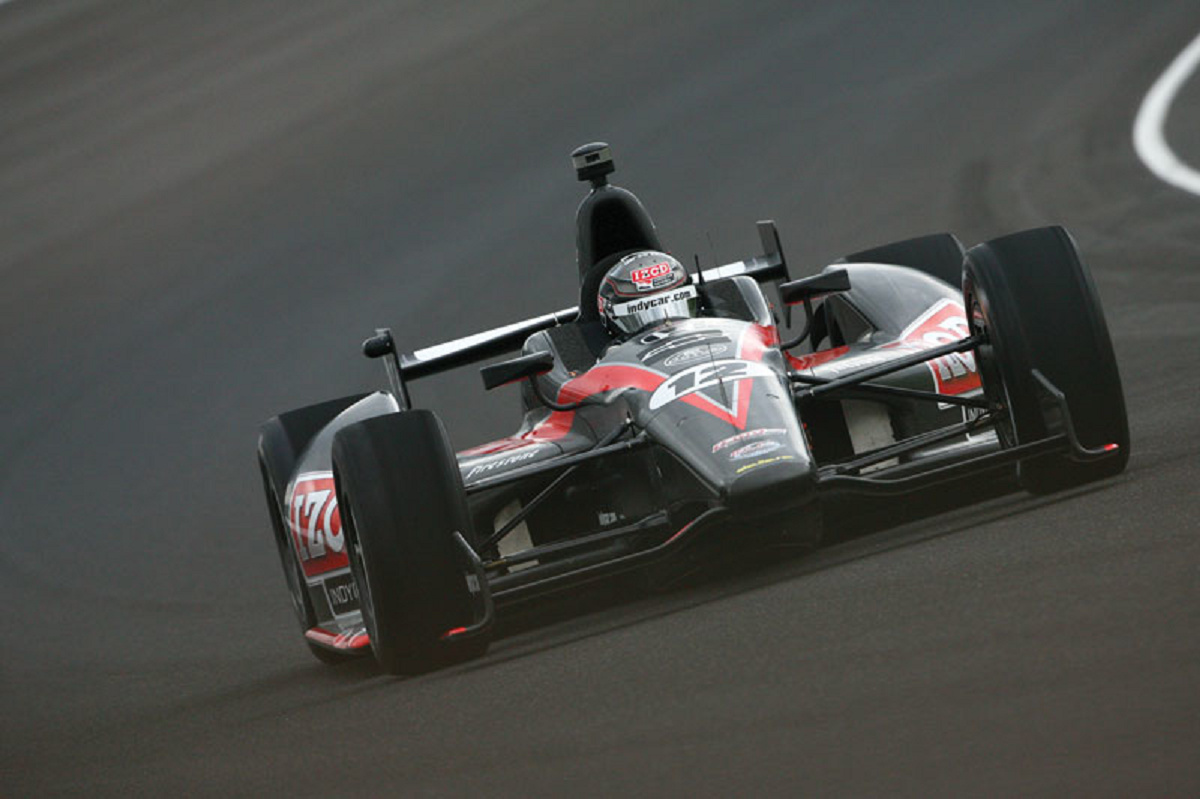
Use of innovative materials represents a significant variable in the weight and strength equation. Options include high-strength steel, stainless steel, aluminium-alloy, and composite structures. Composites, while extremely strong and lightweight, introduce a high level of complexity for CAE analysis, particularly for crash simulation. Various shapes and types of composites (woven, uni-directional) must be modeled and manufactured differently. Behaviors are difficult to predict as the physical phenomena are very complex. A significant amount of data is necessary to perform the analysis, and specialized expertise and software is required.
Dallara Automobili is an Italian chassis manufacturer that designs with safety in mind. Several prominent drivers have gone on record to attribute their survival after potentially fatal crashes to the company’s design innovation. While speed is always paramount in racing, the company is committed to pushing the boundaries of what can be done from an engineering perspective to protect the driver. They use Altair HyperWorks™, a comprehensive open-architecture CAE software containing pre- and post-processing tools, multiple physics solvers, and optimization capability.
HyperWorks includes a tailored environment to efficiently assist crash and safety engineers in model building, starting from CAD geometry and finishing with a runnable solver deck in Altair Radioss™. From dummy positioning and seat mechanisms to seat belts routing, it provides an end-to-end analysis workflow that streamlines the setup of impact simulations in accordance with the different regulations.

Dallara was awarded a contract to supply IndyCar teams with the “survivor cell," a core rolling chassis called the IndyCar Safety Cell. As part of its research and development process, Dallara focuses on structural analysis. Investigating the behavior of materials under stress allows engineers to simulate the performance of any number of different metals, plastics, and composite structures in vehicle components.
By exploiting the power of HyperWorks, finite-element analysis (FEA) and optimization methods are efficiently utilized to conduct trade-off studies, find optimal structural layout configurations, choose materials, and, most importantly, improve the safety of the vehicle.
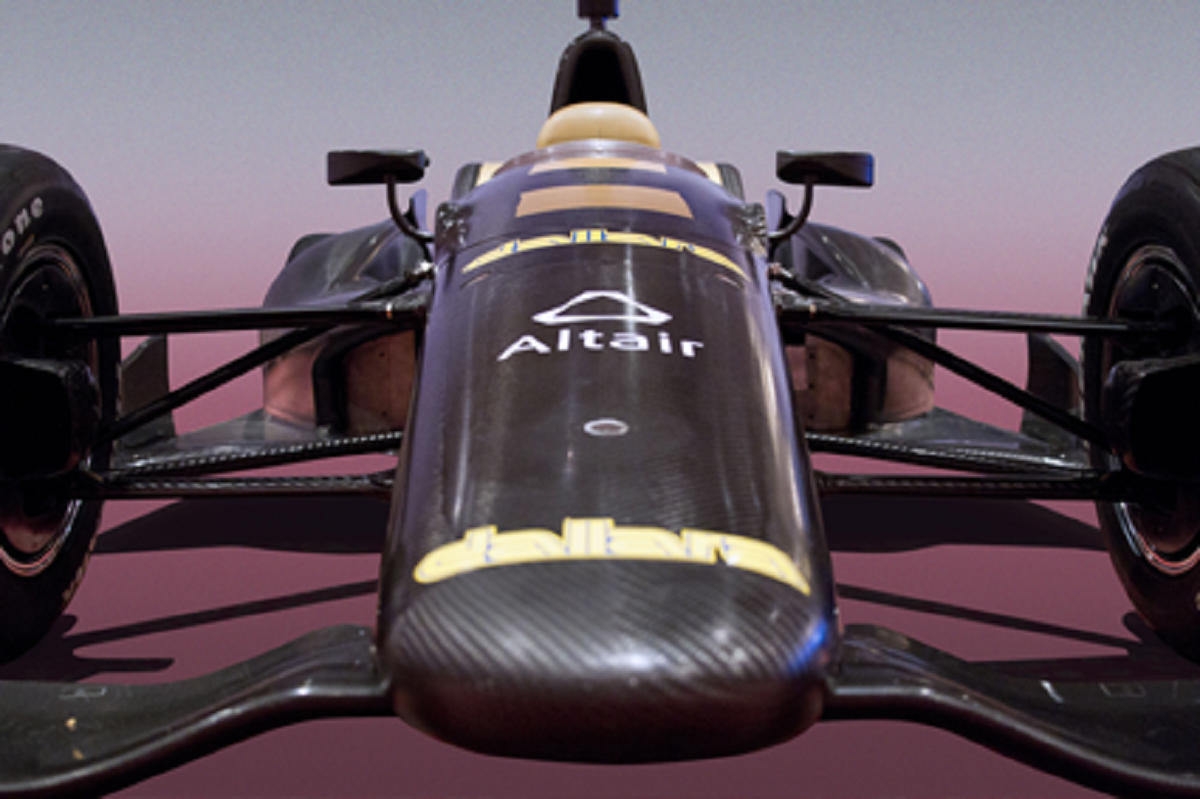
Test-Ready
The total racing package must conform to IndyCar rules and regulations. Computer simulation in conjunction with indoor and track testing helps Dallara meet the series’ homologation tests.
Since safety is paramount, Dallara executes computer crash simulations with Radioss, Altair’s nonlinear and linear solver that simulates dynamic loading in crash and impact studies. For the survivor cell, for example, Dallara must demonstrate that after applying a four-ton load on the nose box, nothing breaks.
In this process, engineers run multiple evaluations using Radioss. When they are satisfied with the results, they move to physical tests in the company’s factory. Then, engineers visit a test center in Milan, Italy to perform frontal test crashes. They crash the survivor cell with a dummy driver to try to replicate what could happen on the racetrack. The survivor cell must not fail. In the frontal test, the nose box has to dissipate the energy from the crash.
Dallara repeats the simulation-physical testing process for other parts of the vehicle. For example, engineers conduct rear impact structure push-off tests, in which there must be no failure of the structure or of any attachment between the structure and the survival cell; rear crash tests, in which there must be no damage to the structure behind the rear wheel axis; side impact structure push-off tests, in which there must be no failure of the structure or any attachment between the structure and the survival cell; and side crash tests, in which there must be no damage to the monocoque and no failure of any attachment of safety belts and the fire extinguisher.
Another important test is conducted on the roll hoop, a steel fabricated structure that protects drivers in rollover situations when the car is hit from the rear or side. Engineers apply 12 tons of force to the top of the hoop. There must be no structural failure in a plane 100 mm below the hoop.
Dallara also conducts a test in which it applies seven tons of force on the front area of the chassis, in front of the driver – anticipating a scenario in which one car might land on top of another. This test is not required by IndyCar, but because Dallara strives to build the safest cars, it believes it is an important test to conduct.
After all the testing is completed, engineers apply an extra safety feature to both sides of the monocoque – a Zylon composite panel consisting of multiple plies. This optimized, ballistic material has saved the lives of racing drivers on numerous occasions.
The Complexities of Composites
The IndyCar monocoque weighs 178 lbs. It is a carbon-composite structure with an aluminium honeycomb core. The side panels are fabricated with steel, and there are two aluminium CNC-machined bulkheads for the
pedals and the dash. The fuel tank is composed of carbon composites as well.
Composite materials deliver high performance, so designers are always investigating new shapes for parts and defining how different materials can be put together. The goal is to reduce weight since composite materials weigh less than aluminium or steel yet often absorb a similar amount of energy.
The physical phenomena associated with composites are complex, and there’s a lot of data necessary to perform analysis. With metals, material properties are isotropic, so the main design variable is the shape. With composites, the directional stiffness can be altered by orienting stacked plies of different fiber directions to create a laminate structure that can be tailored to meet the requirements of each part of the structure. As such, Dallara collaborates with the key raw material market suppliers to learn of new carbon fiber reinforced polymer (CFRP) material developments as well as with software developers like Altair to help virtually determine the best laminate configurations and ply orientations for the structure.
Dallara has established a multi-step process in analyzing carbon chassis structures, such as the IndyCar. Phase 1 involves model preparation. In Phase 2, engineers define materials, boundary conditions and variables for use in analysis and optimization (see Driving Design through Simulation). Results visualization and analysis are carried out in Phases 3 and 4. All of these steps are implemented within HyperWorks.
In evaluating models, Dallara examines material response for every single ply in the laminate. Material data from a lot of experimental tests is used; Dallara has been working with Altair over the last few years developing material models and new software features to meet specific requirements.
Dynamic analysis of CFRP material is multi-faceted, involving the selection of failure criteria to define damage mechanisms such as delamination and cracking, failure propagation, inertial phenomena, instability, energy absorption and strain rate effects. Radioss provides a great environment for engineers to vary material parameters and failure theories to find material models that match available test data. Once these models are defined and verified, simulations can reliably be carried out for conditions that cannot be easily tested.
With all this in mind, simulation software allows engineers and designers to produce high performing and safe vehicles that withstand the grueling forces of a race or worse, a crash. Accidents do happen, especially in high-risk sports like the Detroit Grand Prix. With extensive dynamic load analysis and design optimization capabilities, Altair’s solutions ensure the safety of the driver whilst remaining at the cutting edge of performance.