Laminated Composites - The Original Additive Manufacturing Process
Featured Image: Daniele Pugliesi/Creative Commons. This post was originally published on the HyperWorks Insider.
There is a lot of enthusiasm around additive manufacturing (AM) these days. From high-end applications of AM like the GE fuel nozzle to the home market and hobbyists fairs, AM has captured the imagination of all of us and unleashed our creative instincts to make anything we can dream up. Many are new to the idea of Additive Manufacturing and think of it as a very new technology. However, with a little research, you can find that stereolithography was introduced 30 years ago. Further, other common processes, like selective laser sintering and fused deposition modeling are well over a decade old. The advancements today are allowing us to move from rapid prototyping to direct digital manufacturing which is leading to explosive growth in the AM industry.
If you look at the composites industry, one can claim that laminated composites are the original additive manufacturing technology. The idea behind additive manufacturing is that you build up a structure layer by layer to form the complete part, rather than the traditional subtractive process of taking a block of something and removing material. I remember cutting plies in a university lab in the 1980s and laying down the plies to create laminated structures. Before that, I remember building a fiberglass kayak as a teenager in the 1970s by laying fiberglass mats over a mold and applying the epoxy resin. Both of these can be considered additive processes.
One of the allures of additive manufacturing is that it can be mostly automated – you give the machine a design file and it builds the part. For composites, there has been a parallel effort to automate the composite lamination process. To that end, automatic tape laying (ATL), Automated Fiber Placement (AFP) and now tow steering equipment has become so advanced that you can mostly automate the process of building up a customized laminated structure. These machines are used to build very large aerospace structures and wind turbine blades and these processes are significantly speeding up the build time and ensuring more consistent quality and repeatability. New AM techniques for composites are emerging that will add more manufacturing flexibility to the fabrication of composite structures.
One of the cited advantages of AM is that it offers a lot of flexibility in the design of the part. Many designers are taking their inspiration from nature, which has evolved in such a way that its structures are very specifically and efficiently enabled to carry loads they will have to bear. The human body is a great example of efficient design.
Further, there are a lot of composites in nature – trees, plants, bones and more. Natural composites are not the quasi-isotropic laminates we commonly see employed for industrial composites. Plant fibers, for example, are aligned with the primary load paths to provide stiffness precisely where it is needed. The lengths of the fibers and their orientations are continuously varied throughout the structure.
Given the modern ATL/AFP and tow-steering equipment now in use, can we start to think of customized composite structures that are tailored and tuned, in a similar way, to specific applications? To do so, we will need design software that can help us determine where we need those fibers, what their orientations and lengths should be, as well as when to vary the fiber/matrix percentage and matrix properties. The good news is that Altair has already developed many of these tools and we continue very active development on composite structure design optimization. Much of the design optimization software, such as topology optimization, genetic algorithms, neural networks, etc., were inspired and developed to mimicnatural biological processes. Because nature is very efficient in the design of composite structures, these algorithms can help us design more efficient industrial composite structures. Using these algorithms, we can start to design composite structures that are truly optimized for function, and with automated composite manufacturing equipment, we can build up these structures in an efficient fashion.
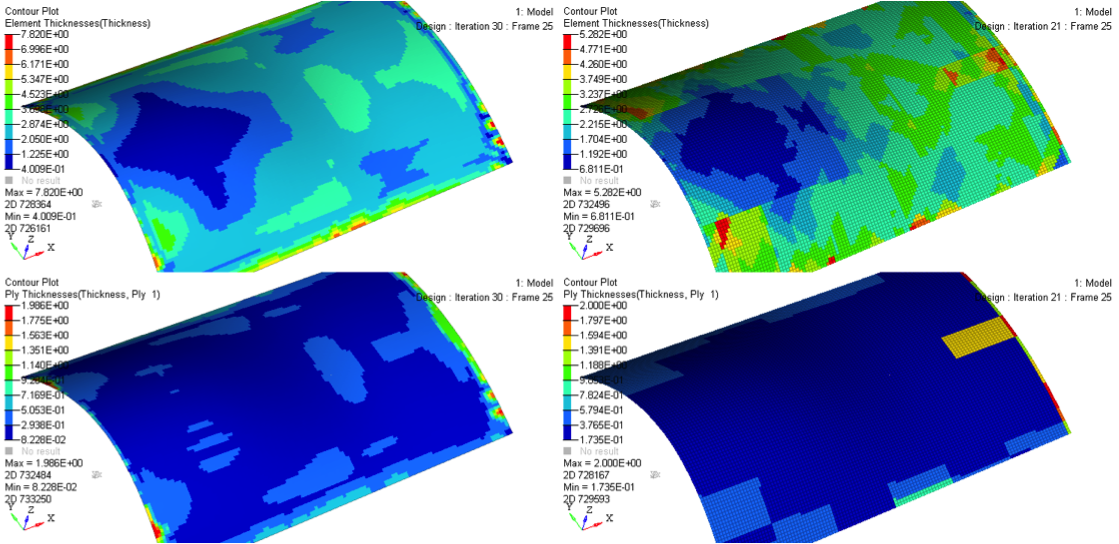
As an example of this, the figure shows an aerospace structure where composite free size optimization was applied. With this process, the shape and laminate configuration are pre-defined and OptiStruct determines the optimal layup configuration placing just the material needed in the right spot. It can determine which angle plies should dominate in a given region, where you should build up the thickness and how, and where you can get by with a fewer number of plies. With ATL/AFP equipment, we can build these types of structures with little material waste and in a very automated fashion. The result in the figure shows added plies on the right side where stresses are higher and an increase in the number of 90° plies in the thicker section. Human bones are similar in construction – added material where you see higher stresses, aligned fibers along directions of major load paths, and then tapered volume as the stress field decreases. Altair is actively working with the companies that develop the software to drive ATL/AFP machines so that we can seamlessly go from an optimized design to an optimized physical structure.
Because laminated composites can claim to be the original additive manufacturing process, it also should be the most advanced in terms of application. Given the sophisticated automated equipment now in use for composite laminate lay-up and Altair’s sophisticated optimization solutions that are available, we should truly be able to enhance our composite structural designs, moving them closer to the optimized designs that we see in natural composites all around us.
Read the original article on CompositesWorld.