Mastering Material Data Management
The risk of oversimplifying materials infrastructure and inputs
There are many tasks that involve material data in a product life cycle. As companies look to build their materials knowledge infrastructure, they pull together teams comprising of diverse users of material data. While many users of material data in an enterprise may have less stringent needs that are easier to satisfy, quite often, the bottle neck in the functionality of an enterprise materials information structure is faced by the R & D teams involved in product design. It is important that the most demanding product development team be well-represented, or they will use software ancillary to the knowledge core, weakening its very purpose.It is also clear, that designing a common materials core, arriving to the many decisions, and its implementation, take time. Meanwhile, product development must continue. Matereality has a solution for the interim, which satisfies even the most exacting consumers, and is seamlessly extensible to an enterprise solution for when a consensus is reached. It is important not to oversimplify materials, or its infrastructure in the age of digital engineering.
Accelerate the pace of product development and eliminate the typical risks from unmanaged material data.
Product design requires many fine skills in the use of CAD and FEA, CAE solvers. It requires an understanding of what the product must do. It requires an appreciation for the economies in material use, a balance between weight, and product’s attractiveness and durability. In addition, must a design engineer also know everything about how materials behave and how that may impact their product’s functionality? Matereality software for materials eases this requirement since it was created by a team of experts on testing materials for product design who well-understand the importance of material inputs.Matereality faces regular requests for material libraries to contain the data for product design solver inputs. These libraries are available at little or no cost online, and in handbooks, and have some limited value during initial try outs. However, today’s project team leaders are quite determined to keep the use of such generic material inputs out, and allow only sequestered material data that is relevant and approved for their product design group’s use. Why?
As you download a material data file into your product design simulation solver, consider this:
You are sending your body measurements for an expensive suit fitting. You would not commission the suit with only approximate body dimensions based on your height, age, and weight (analogy: properties of materials based on class, subclass, test conditions unknown, standards unknown). If you want a perfect fit you know that you must take precise measurements. Why then would a simulation engineer embark on a product design project without the most precisely defined material properties for the exact material within, and the conditions the product will see? With digital engineering, there is a further risk that when there is a discrepancy in the inputs, the resultant misfit may not be immediately visible.
The risk of using material data that are not true for your material, or for the conditions that your product will see, can result in a design that may come close, but not exact. For some products, the misfit may not be critical. For others, it could be disastrous. It would be a risk to use properties for an unconditioned material when designing a fuel tank, for example. Matereality’s visual Compare feature allows users to see the extent to which their material’s properties change under different conditions. DatapointLabs’ experts on materials testing have demonstrated variability in material properties at ambient and high temperatures, and with or without prior fuel soaking (presented in paper title “A concept for the collection and presentation of material properties for diverse applications”; Hubert Lobo, NAFEMS, 2003).
Matereality Workgroup Material DatabasePro, available via the Altair Partner Alliance, is designed to enable best practices when using materials information in product design. It serves all kinds of material data for a diverse body of consumers in a workgroup or an enterprise.
Matereality Workgroup Material DatabasePro on APA helps manage the risk of materials input in product design. It provides the means to build a database of well-defined material properties accessible to all team members, on your materials and your product conditions. When you are considering using any piece of data, you can look at the data certificate for details about its suitability and reliability. Having ready access to accurate, approved material properties reduces the risk of use of inappropriate material data.
A well-managed database also enhances productivity and pays for itself. From within Matereality Workgroup Material DatabasePro on APA, your materials are plugged into Hyperworks, and ready to deploy into your product design. When collaborating teams populate this Workgroup with existent CAE Material files, or use inbuilt software to create RADIOSS and other material files, create Master material files for Hyperworks, all team members can access the same exact material cards. They see what you see. See gaps in data? You can order DatapointLabs’ Testpaks, and receive material cards for your material and conditions directly into your workgroup’s database. Accelerate the pace of product development and eliminate the typical risks from unmanaged material data.
Matereality: workflow of material use in CAE and Product Development
- Create and save material files for different solvers from raw data
- Archive externally created CAE material files
- Extract properties from CAE material files
- Assemble and deploy master material files to common CAE pre-processors
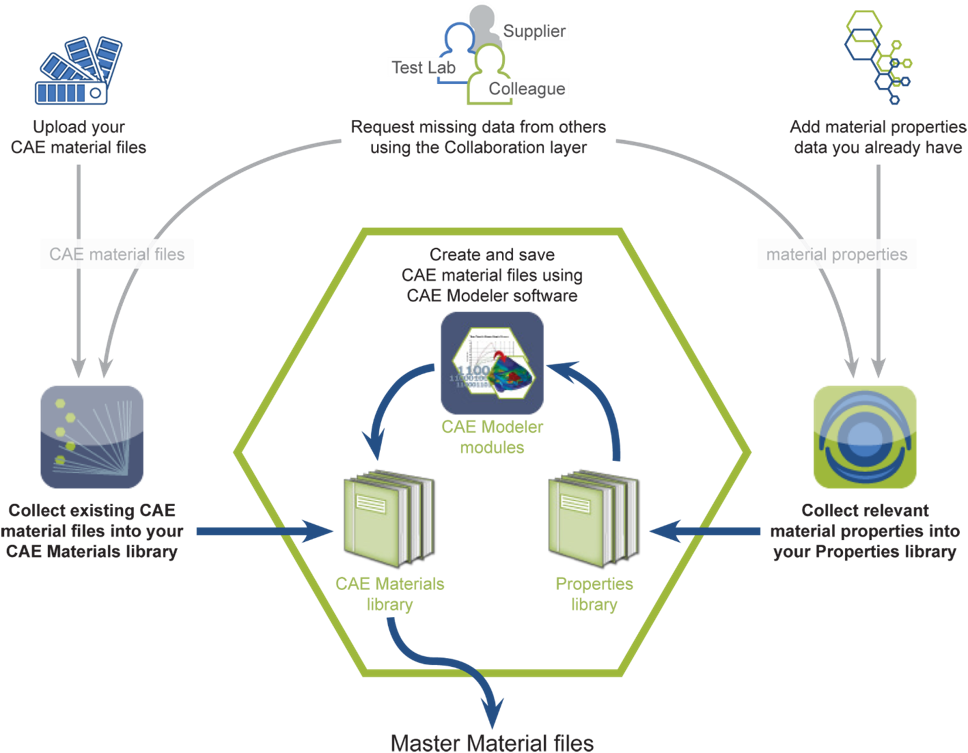
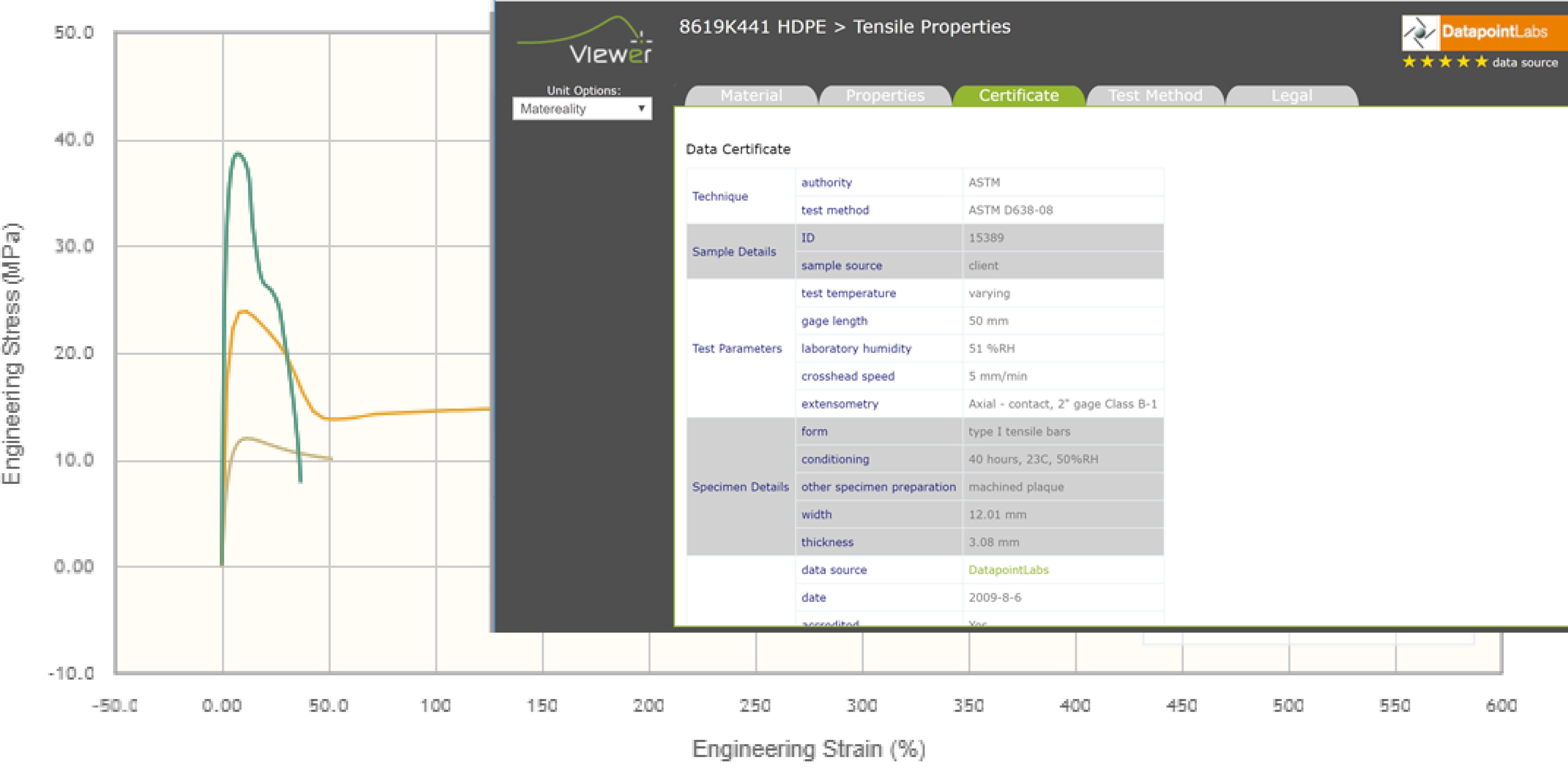
This guest post on the Altair Blog is written by Renu Gandhi, Vice President of Business Development at Matereality, developer of material management software Matereality Workgroup Material DatabasePro. Matereality is a member of the Altair Partner Alliance.