Monash Motorsport Continues to Win with Altair OptiStruct® and 3D Printing
Continuous improvement is a significant thrust in elite competition: small incremental changes can yield important performance gains on race day. As an example, Monash Motorsport has steadily improved its race car's performance since the team's first Australian SAE Student Racing competition in 2000. Today, with six consecutive victories in the Australasian competition, a strong performance in the European Formula Student competition, and a number 7 world ranking, Monash Motorsport is pushing to develop even faster, lighter, better, and more innovative vehicles while keeping development time and costs low. Altair solver OptiStruct®, part of the comprehensive computer-aided engineering (CAE) suite HyperWorks®, has been and continues to be a critical ingredient in the team's success.
Monash Motorsport is a completely student run organization consisting of 70 student designers, constructors, and drivers for open wheel race cars in Formula SAE from Monash University in Clayton, Victoria, Australia. Formula SAE is the world’s largest student engineering design competition organized by SAE International, with over 500 teams worldwide. The Formula SAE series provides a valuable opportunity for students to gain applied product development skills and business experience by walking through the entire process of designing, building, testing, and competing with a race car.
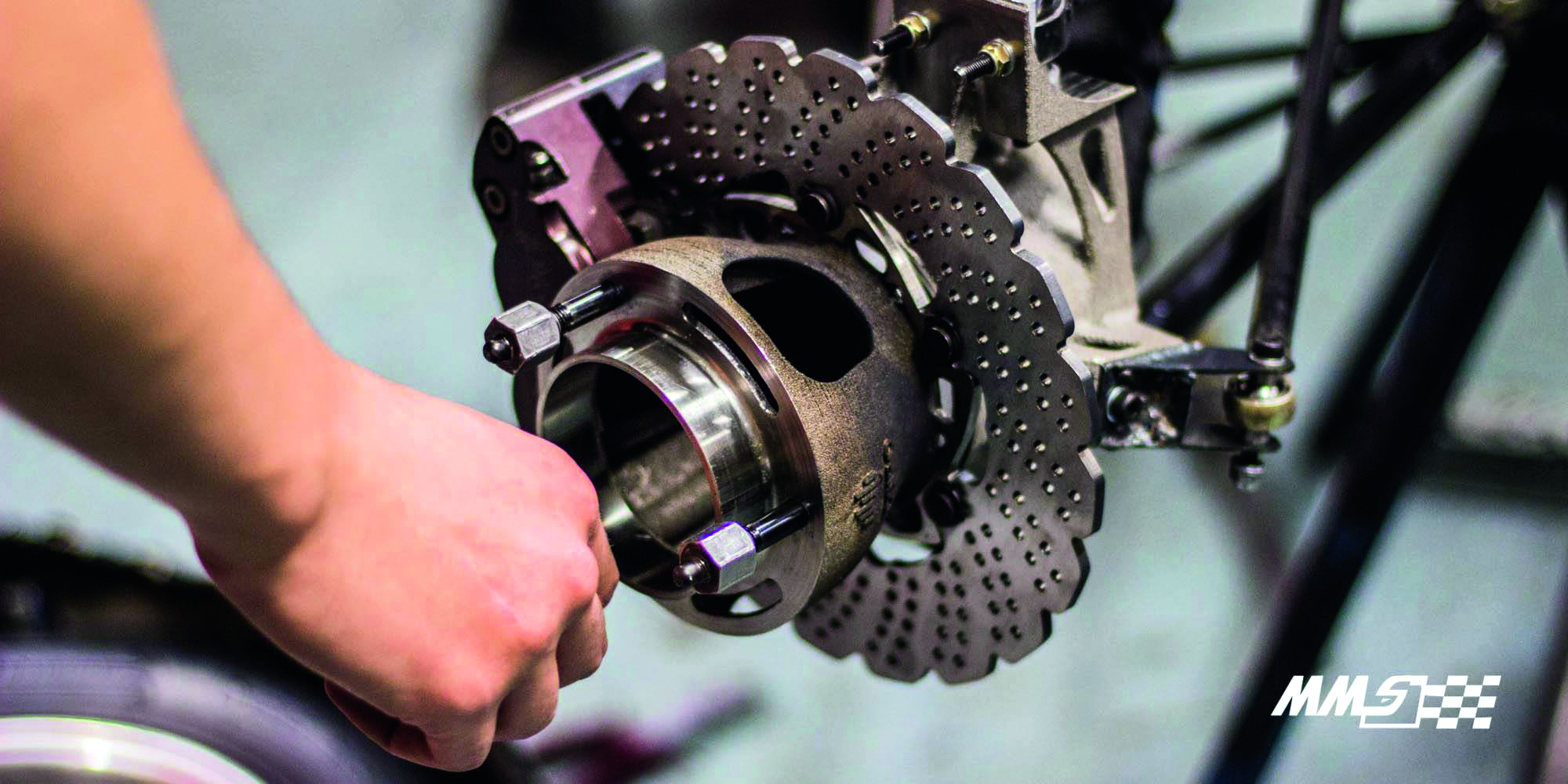
The Monash Motorsport team faced new weight and performance challenges at the end of 2013. In order to stay competitive, the team needed to develop a faster, lighter, and better performance race car while lowering development time and costs. Intending to leverage the benefits of 3D printing, students used Altair OptiStruct to optimize an initial prototype a rear hub design from the previous year's entry.
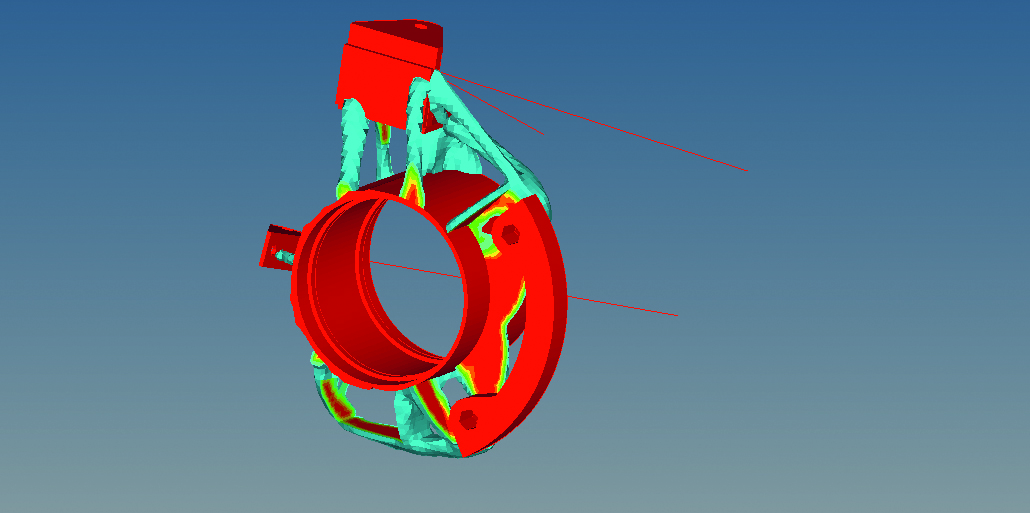
First, engineers created a design space in OptiStruct to perform a number of topology optimization runs, which enabled the development of a stiffer and lighter component structure. A working CAD design was generated and validated with a finite element analysis, enabling Monash Motorsport to achieve significant weight savings on an already light upright design. Total combined weight savings was approximately 30% while offering greater stiffness and safety than the previous design.
The team's dedication to innovation extended to the manufacturing process. Using 3D printing, the team used less than half of the titanium material typically used, taking less time to produce and meeting all performance requirements. As a result, Monash Motorsport won its sixth consecutive FSAE-Australasia title, becomiong the first team in Formula SAE history to take home six consecutive victories at a single competition!
Click here to read more about Monash Motorsport’s success.
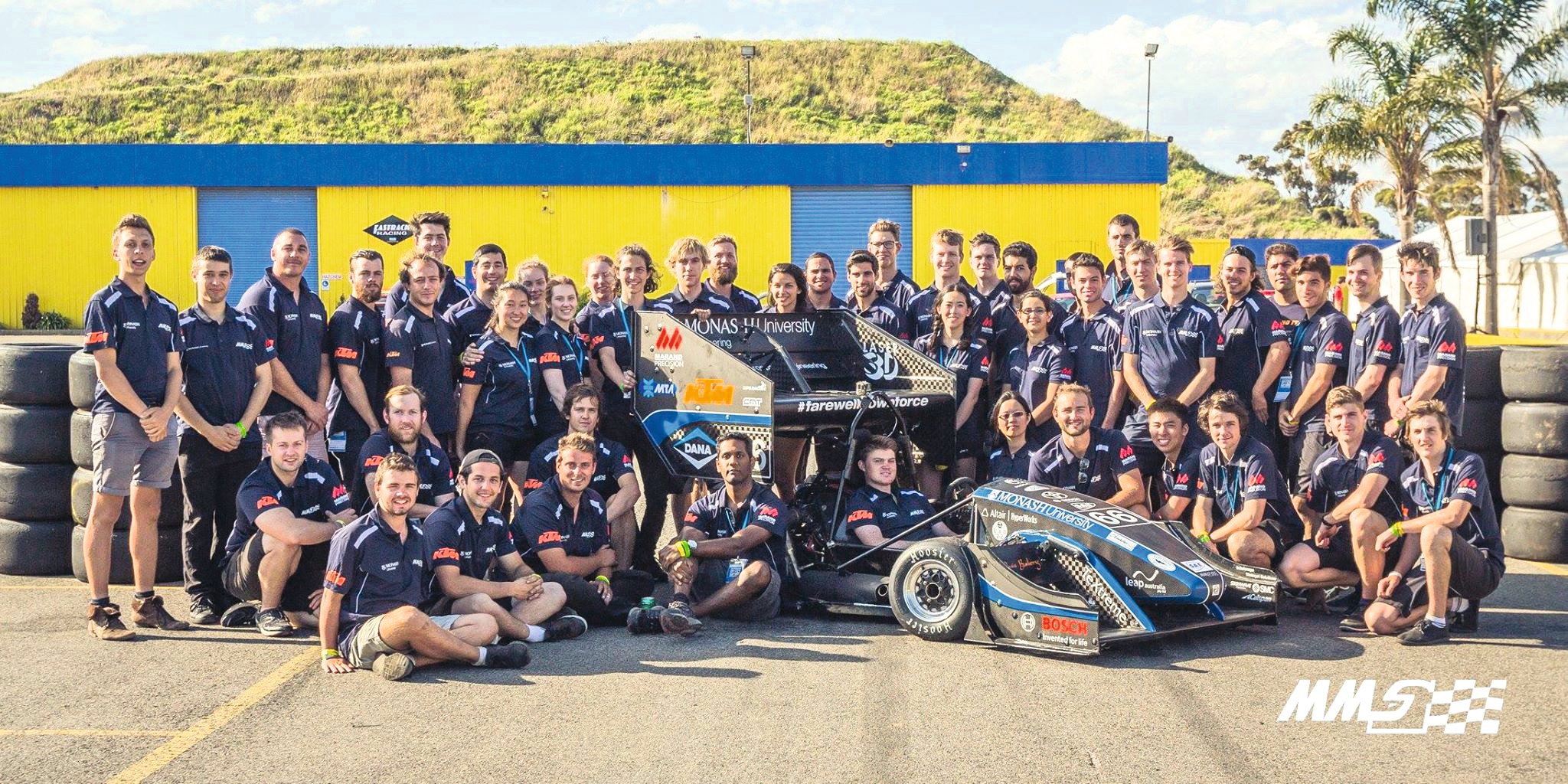
Monash Motorsport is a completely student run organization consisting of 70 student designers, constructors, and drivers for open wheel race cars in Formula SAE from Monash University in Clayton, Victoria, Australia. Formula SAE is the world’s largest student engineering design competition organized by SAE International, with over 500 teams worldwide. The Formula SAE series provides a valuable opportunity for students to gain applied product development skills and business experience by walking through the entire process of designing, building, testing, and competing with a race car.
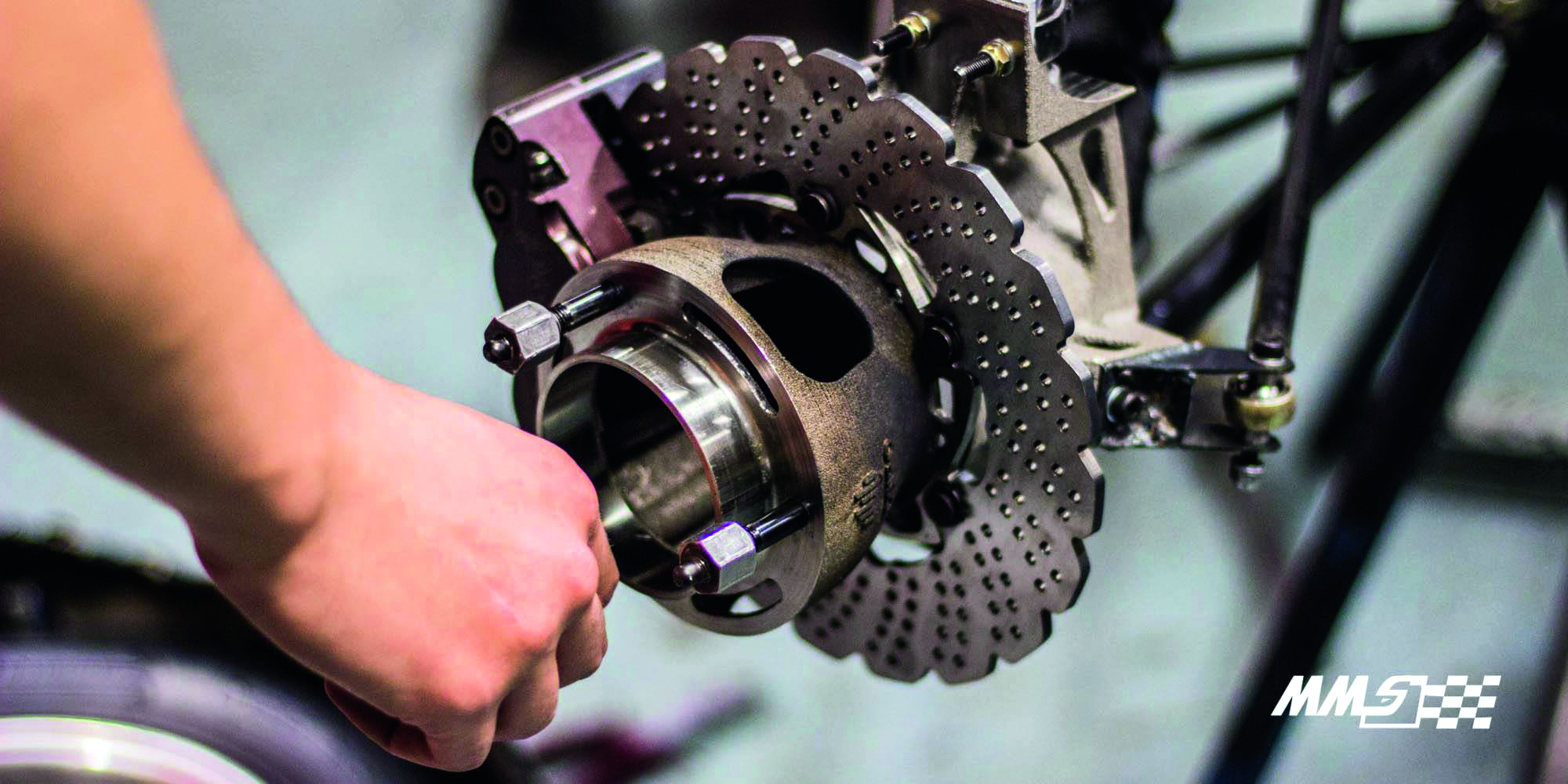
The Monash Motorsport team faced new weight and performance challenges at the end of 2013. In order to stay competitive, the team needed to develop a faster, lighter, and better performance race car while lowering development time and costs. Intending to leverage the benefits of 3D printing, students used Altair OptiStruct to optimize an initial prototype a rear hub design from the previous year's entry.
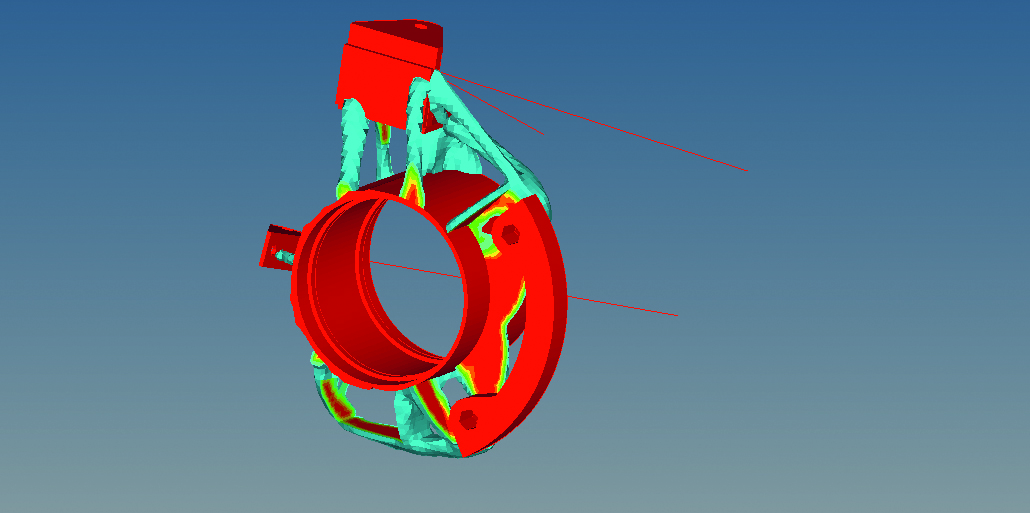
First, engineers created a design space in OptiStruct to perform a number of topology optimization runs, which enabled the development of a stiffer and lighter component structure. A working CAD design was generated and validated with a finite element analysis, enabling Monash Motorsport to achieve significant weight savings on an already light upright design. Total combined weight savings was approximately 30% while offering greater stiffness and safety than the previous design.
The team's dedication to innovation extended to the manufacturing process. Using 3D printing, the team used less than half of the titanium material typically used, taking less time to produce and meeting all performance requirements. As a result, Monash Motorsport won its sixth consecutive FSAE-Australasia title, becomiong the first team in Formula SAE history to take home six consecutive victories at a single competition!
Click here to read more about Monash Motorsport’s success.
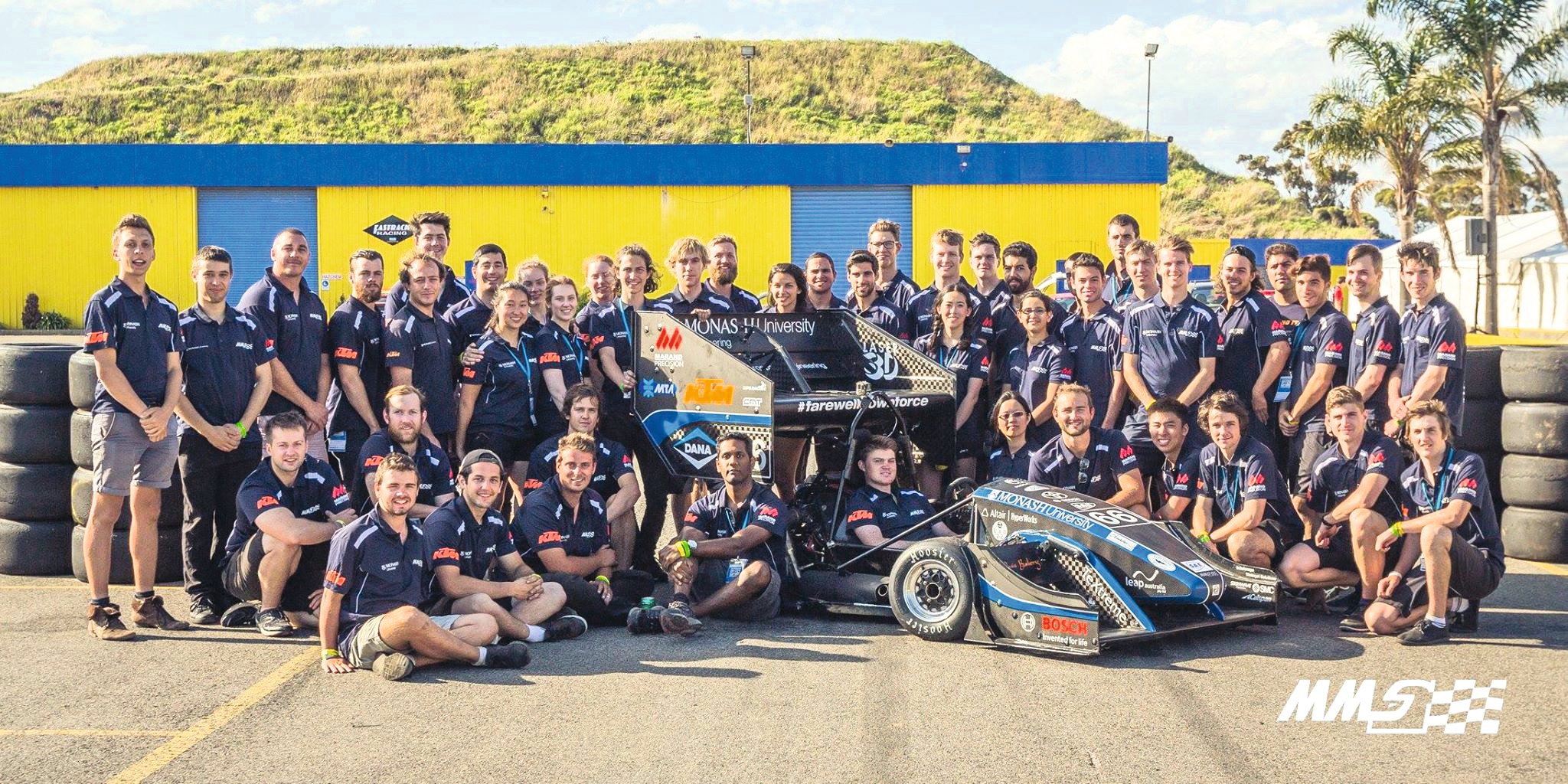