Simulation-Driven Technology Showcased to International Composites Community at JEC World 2018
For those involved with composite materials in Europe and beyond, the annual JEC expo in Paris is a sure sign of spring. For the sixth consecutive year, Altair exhibited at JEC that took place in early March 2018. The JEC expo in Paris, having grown steadily over the years to become the current mega event, is now considered the largest composites industry show in the world, with over 1,300 exhibitors and some 42,000 visitors during the three days. The exhibitors represent the different players in the composites value-chain, including equipment and tool manufacturers, raw material and intermediate product producers, and services providers. About 80% of the visitors come from Europe, while Asian visitors form the second largest group.
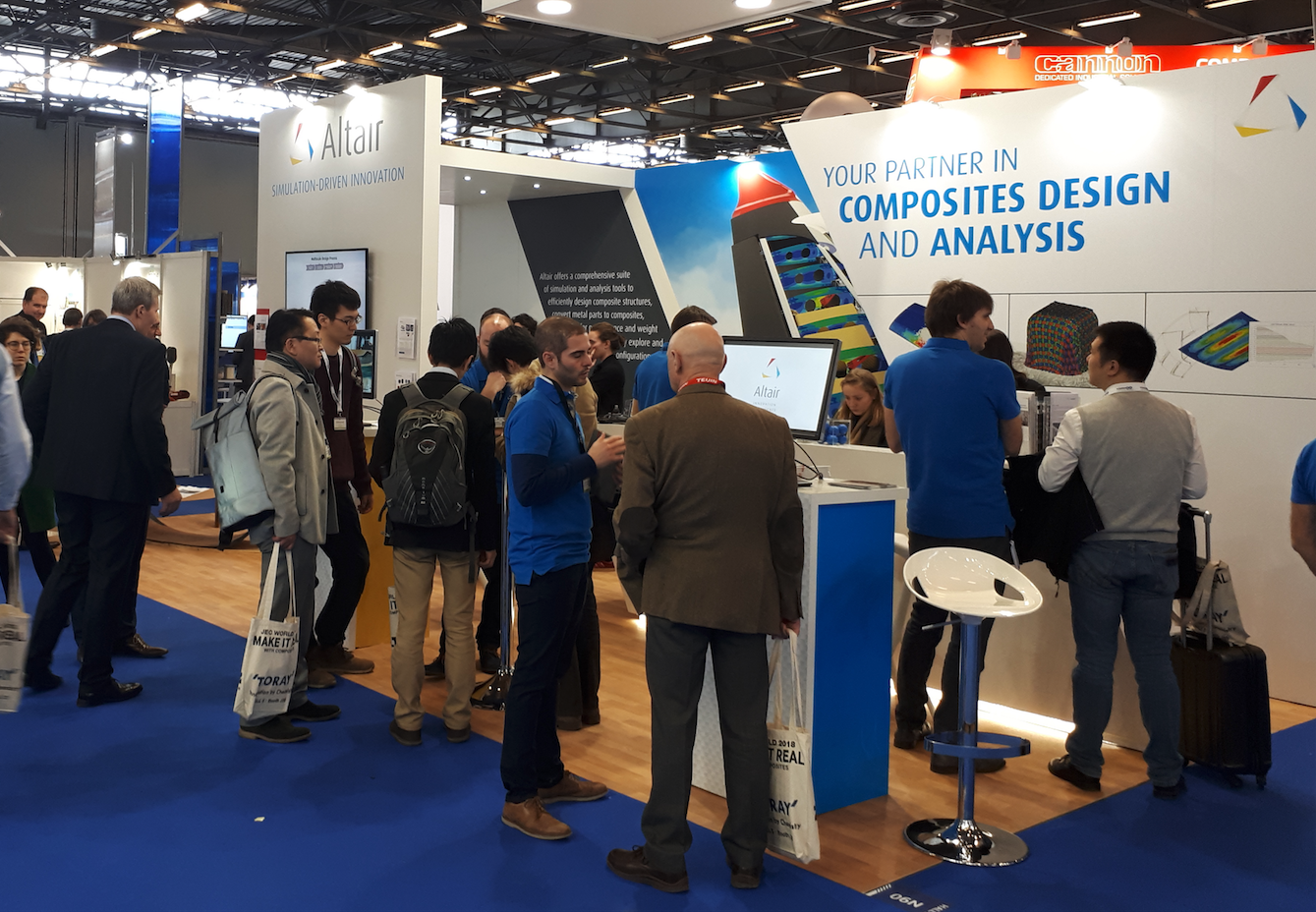
A global effort at Altair, our marketing staff and technical experts from different countries met with customers and prospects, seamlessly managing spontaneous encounters with booth visitors over the course of the 3-day event. The average JEC visitor is not a simulation engineer, hence sometimes it takes time to understand the needs and desires of the composite designer or manufacturer. Quite often when asked about how the part or product in question is designed to meet the mechanical requirements, the answer is “we just build it”. As we work towards advancing simulation-driven design, this underlines the complexity of designing a composites part where the choice of materials and processing methods to meet cost and production rate targets are often the primary drivers.
To concretize the message of how our simulation tools help in composites design, we showcase examples of products designed with the help of Altair software at the booth. This year the showpiece was the “Sella chair”, an innovative wood-carbon construction by Atanas Zhelev and Mariya Korolova (Digital Architects, Austria) combining ultra-thin, lightweight, large-span, 3D curved structures to meet the demands of modern organic elegant designs. Altogether, composites for architectural applications was one of our themes this time and was further highlighted by Atanas’s presentation at the Altair arranged conference.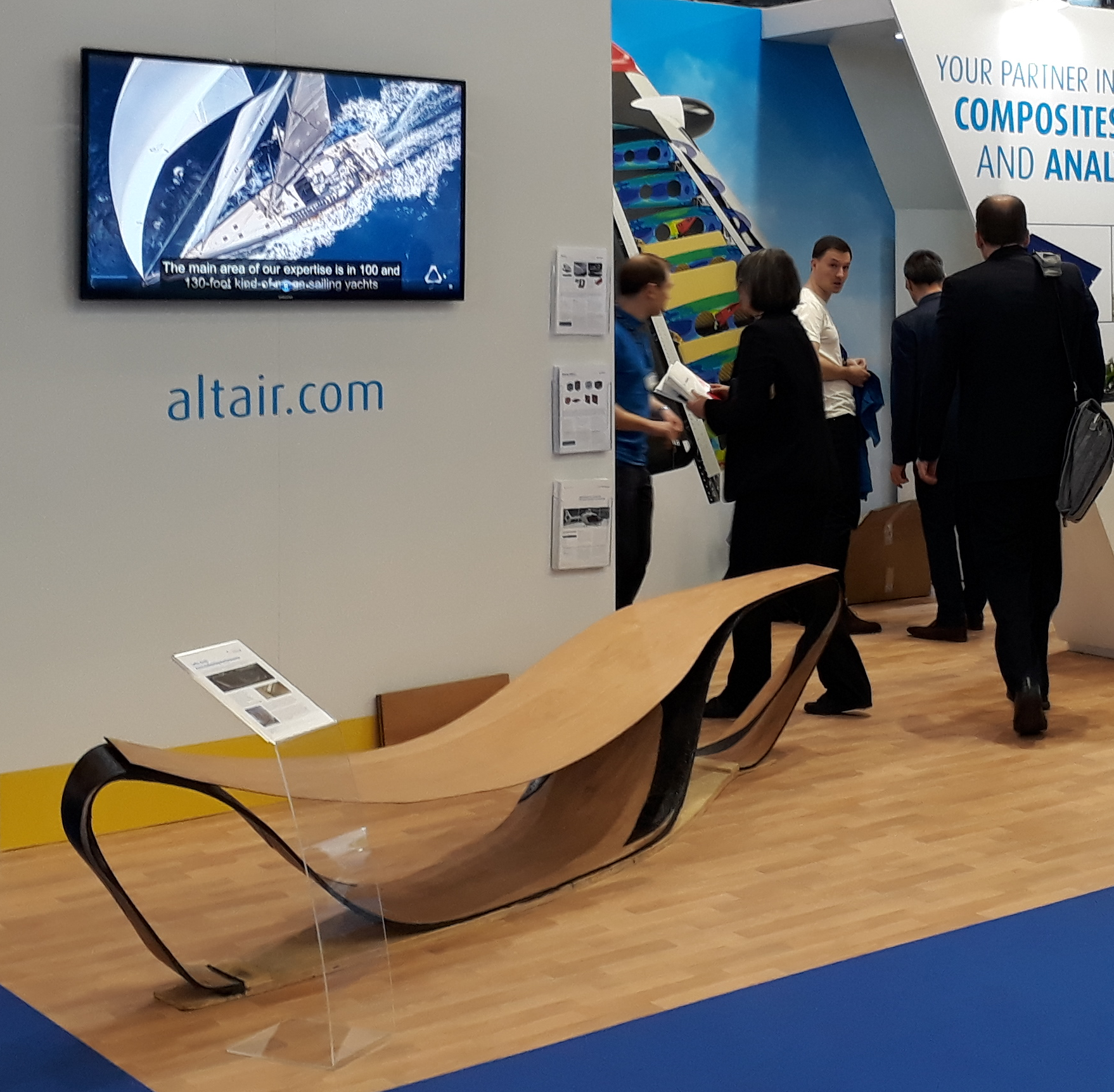
Besides our presence at the expo with a good-sized booth, following last year’s success, Altair hosted a conference session titled “Simulation-driven Design for Composites” within JEC. Given last year’s high attendance at Altair’s simulation conference at JEC, this year we moved to the Agora, a larger auditorium located within the exhibition hall. The setup was good in terms of accessibility and technical arrangements. The always inspiring “How does Altair make a difference?” video opened the event with a volume level of a rock concert, attracting the attention of attendees even outside the auditorium. Despite the larger space, the hall was packed throughout the two-hour event.
The opening presentation of the conference was by Jeff Wollschlager, Senior Director - Composite Technologies at Altair. It is a challenge to describe the entire Altair HyperWorks® platform for composites design, optimization, and simulation in just twenty minutes. The offering consists of composites specific tools Multiscale Designer for materials modelling, ESAComp™ with a composite materials database and stress toolbox features, and the core HyperWorks tools with composites specific features such as HyperMesh® and HyperView® for modelling and visualization, finite element solver OptiStruct® with unique composites optimization features and RADIOSS® for impact and crash simulation. For manufacturing simulation, HyperWorks also offers ply draping capabilities. Despite the multitude of different applications available, they all fulfill their distinct function in the design process and communicate with each other when moving from concept design to design validation through the different steps in between.
Atanas Zhelev, Chief Architect of Digital Architects, Austria, continued with a presentation on the design of the Varna Regional Library. The design involved use of a carbon reinforced wooden composite façade system. Altair ESAComp was used extensively in the design of the layered wood-carbon elements. Composites are making their way to architectural applications thanks to their desirable properties, such as corrosion resistance and light weight combined with stiffness and strength. Moreover, composites offer means to create aesthetically-pleasing structures with organic shapes that would not be possible to accomplish with traditional construction materials.
In his presentation, “A Process for Composite Box Structure Optimization”, Benjamin Trarieux of Airbus France addressed the concept design of an aircraft wing box like structure to reduce weight while considering constraints coming from production, cost, and maintenance – all important for the aircraft industry. The presented design methodology consists of four main steps: topology, concept definition, shape optimization, and assembly parts optimization. The topology part for determining main load paths utilizes Altair OptiStruct. The design of experiments and optimization capabilities of HyperStudy® are put in use in the later stages of the process.
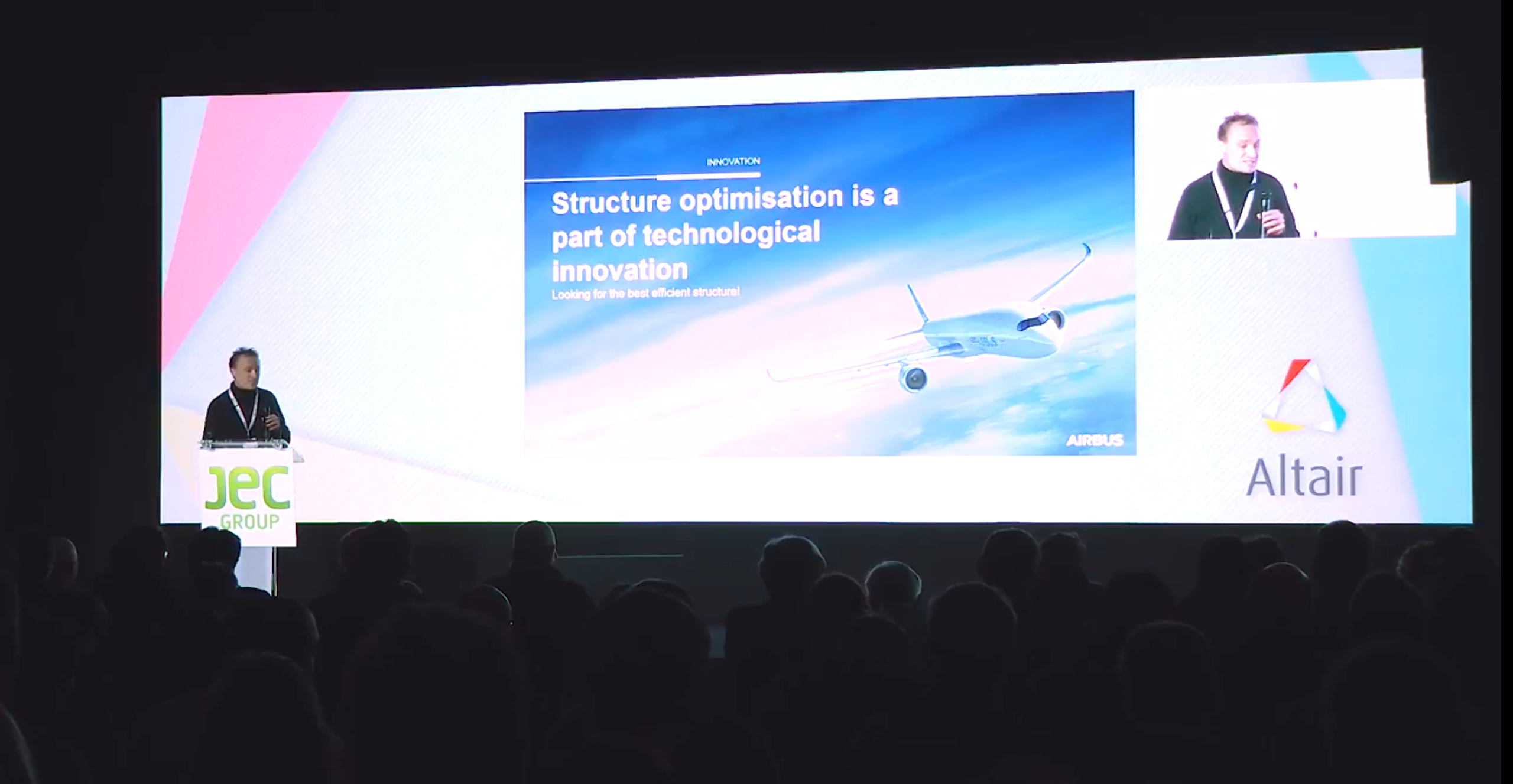
Moving to somewhat more unorthodox composites applications, Juan Pedro Ramirez, RADIOSS expert at Altair France, told us about the “Balloo Project: Crash Resilient Lightweight Fuel Tank Development for Aerospace Applications”. In a project with a French company Pronal and various partners, RADIOSS was successfully applied to a challenging simulation of a drop test of a flexible fuel tank made of elastomer matrix composite, thus giving means to improve the crash resilience through simulation-driven design.
While the aerospace industry is clearly the number one in the use of high-performance composites today, the automotive industry is a close follower, not least because of the changing paradigm with electric and gas vehicles. The car body is the apparent place for further lightweighting to meet emission targets and thus motivates increased use of composites. But in the automotive industry cost and production cycle times are also of utmost importance. The drive to overcome these issues results in various concepts by different car manufacturers and their designers. Chris Hamar, Chief CAE Engineer at Gordon Murray Design, UK, made an introduction to their iStream concept that utilizes steel or aluminum frame with glass or carbon reinforced composite panels. With the choice of materials, this hybrid structure concept scales to different price ranges of cars. At Gordon Murray Design, Altair simulation tools are utilized in broad scale to meet the design targets.
The concluding presentation of the Altair conference at JEC was given by Denis Espinassou, Polymers & Composites Engineer at CETIM, France. In a project with ONERA, “QSD - Optimization Software for Design to Cost” has been developed for thermoplastic composite optimization. This is a good example of how new automated manufacturing methods combined with advanced design approaches, utilizing Altair OptiStruct, can be used to meet the industrial needs of simultaneous lightweighting and cost reduction.
Whilst we will surely be back next year at JEC World to present the latest in simulation-driven design of composites, in the meantime why not get a full picture of our offering at the 2018 Global Altair Technology Conference, also in Paris, in October?
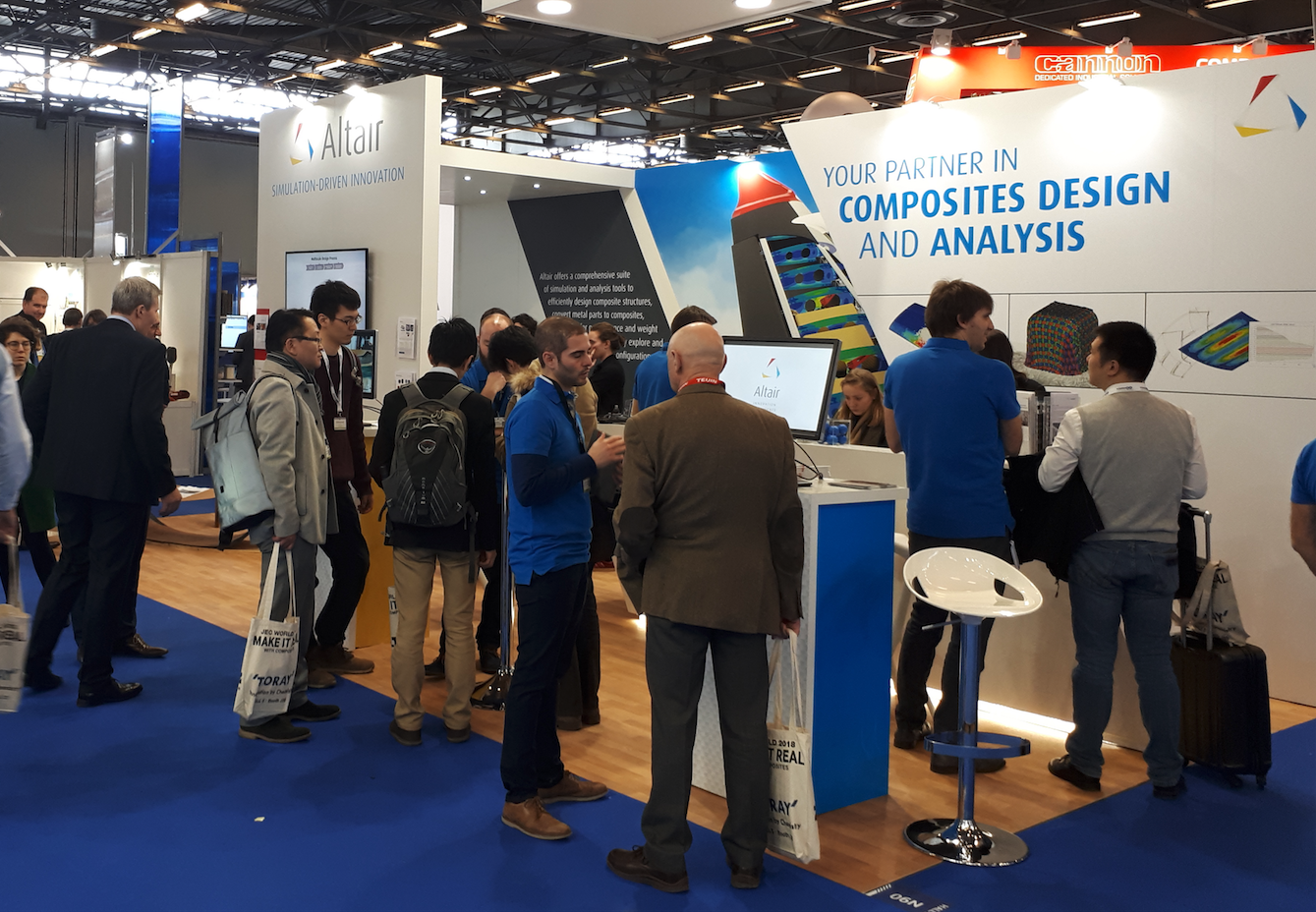
A global effort at Altair, our marketing staff and technical experts from different countries met with customers and prospects, seamlessly managing spontaneous encounters with booth visitors over the course of the 3-day event. The average JEC visitor is not a simulation engineer, hence sometimes it takes time to understand the needs and desires of the composite designer or manufacturer. Quite often when asked about how the part or product in question is designed to meet the mechanical requirements, the answer is “we just build it”. As we work towards advancing simulation-driven design, this underlines the complexity of designing a composites part where the choice of materials and processing methods to meet cost and production rate targets are often the primary drivers.
To concretize the message of how our simulation tools help in composites design, we showcase examples of products designed with the help of Altair software at the booth. This year the showpiece was the “Sella chair”, an innovative wood-carbon construction by Atanas Zhelev and Mariya Korolova (Digital Architects, Austria) combining ultra-thin, lightweight, large-span, 3D curved structures to meet the demands of modern organic elegant designs. Altogether, composites for architectural applications was one of our themes this time and was further highlighted by Atanas’s presentation at the Altair arranged conference.
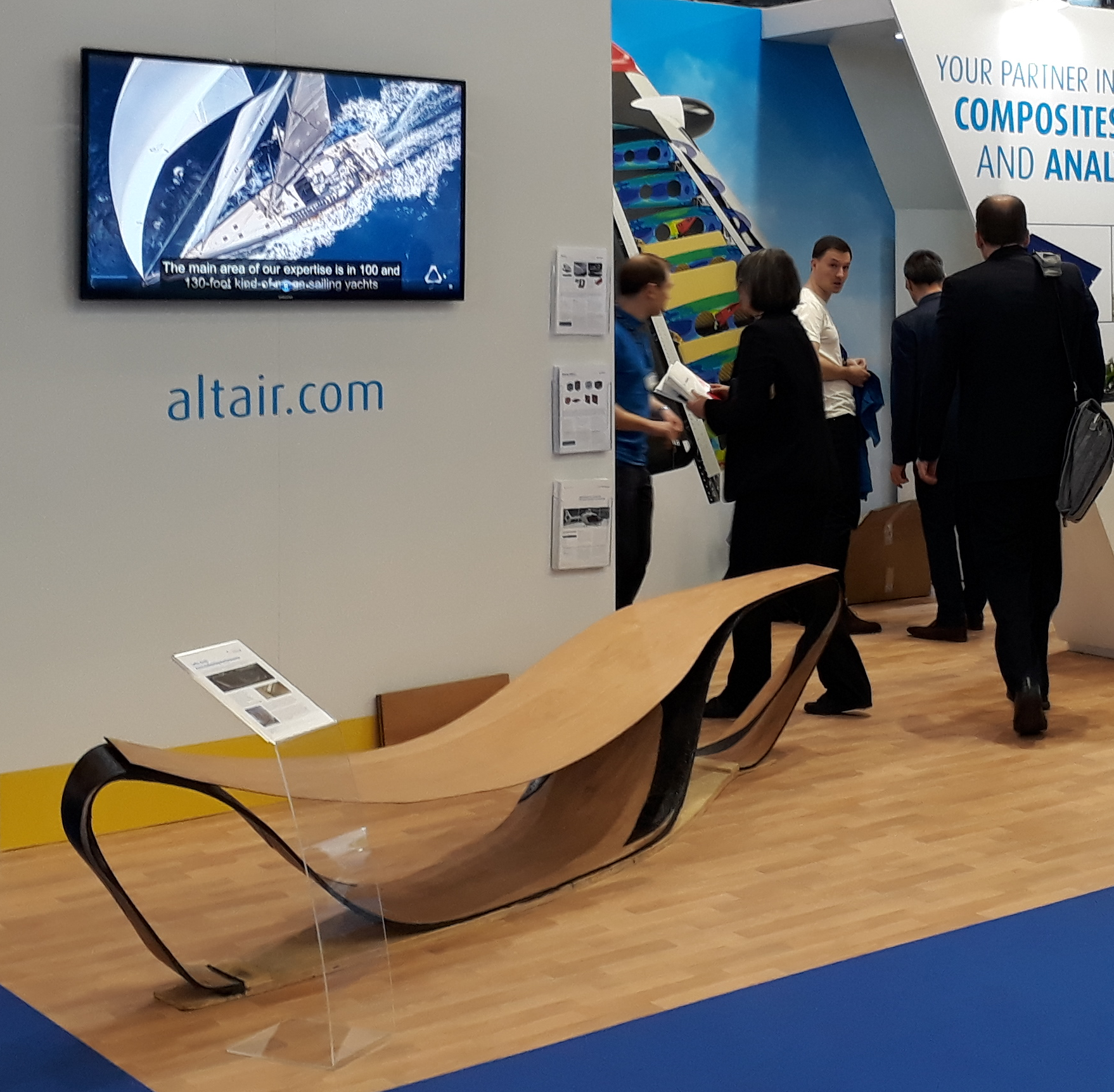
Besides our presence at the expo with a good-sized booth, following last year’s success, Altair hosted a conference session titled “Simulation-driven Design for Composites” within JEC. Given last year’s high attendance at Altair’s simulation conference at JEC, this year we moved to the Agora, a larger auditorium located within the exhibition hall. The setup was good in terms of accessibility and technical arrangements. The always inspiring “How does Altair make a difference?” video opened the event with a volume level of a rock concert, attracting the attention of attendees even outside the auditorium. Despite the larger space, the hall was packed throughout the two-hour event.
The opening presentation of the conference was by Jeff Wollschlager, Senior Director - Composite Technologies at Altair. It is a challenge to describe the entire Altair HyperWorks® platform for composites design, optimization, and simulation in just twenty minutes. The offering consists of composites specific tools Multiscale Designer for materials modelling, ESAComp™ with a composite materials database and stress toolbox features, and the core HyperWorks tools with composites specific features such as HyperMesh® and HyperView® for modelling and visualization, finite element solver OptiStruct® with unique composites optimization features and RADIOSS® for impact and crash simulation. For manufacturing simulation, HyperWorks also offers ply draping capabilities. Despite the multitude of different applications available, they all fulfill their distinct function in the design process and communicate with each other when moving from concept design to design validation through the different steps in between.
Atanas Zhelev, Chief Architect of Digital Architects, Austria, continued with a presentation on the design of the Varna Regional Library. The design involved use of a carbon reinforced wooden composite façade system. Altair ESAComp was used extensively in the design of the layered wood-carbon elements. Composites are making their way to architectural applications thanks to their desirable properties, such as corrosion resistance and light weight combined with stiffness and strength. Moreover, composites offer means to create aesthetically-pleasing structures with organic shapes that would not be possible to accomplish with traditional construction materials.
In his presentation, “A Process for Composite Box Structure Optimization”, Benjamin Trarieux of Airbus France addressed the concept design of an aircraft wing box like structure to reduce weight while considering constraints coming from production, cost, and maintenance – all important for the aircraft industry. The presented design methodology consists of four main steps: topology, concept definition, shape optimization, and assembly parts optimization. The topology part for determining main load paths utilizes Altair OptiStruct. The design of experiments and optimization capabilities of HyperStudy® are put in use in the later stages of the process.
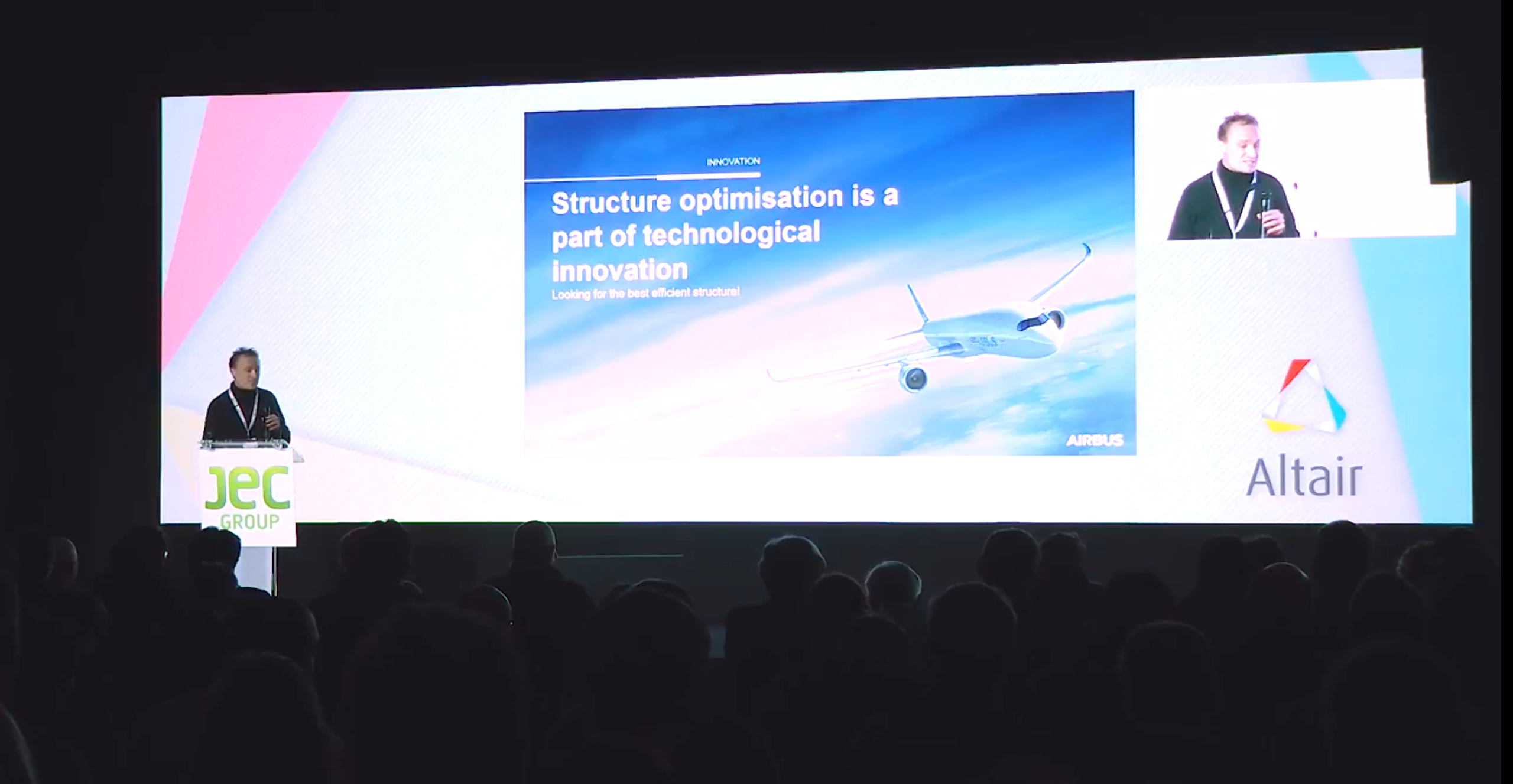
Moving to somewhat more unorthodox composites applications, Juan Pedro Ramirez, RADIOSS expert at Altair France, told us about the “Balloo Project: Crash Resilient Lightweight Fuel Tank Development for Aerospace Applications”. In a project with a French company Pronal and various partners, RADIOSS was successfully applied to a challenging simulation of a drop test of a flexible fuel tank made of elastomer matrix composite, thus giving means to improve the crash resilience through simulation-driven design.
While the aerospace industry is clearly the number one in the use of high-performance composites today, the automotive industry is a close follower, not least because of the changing paradigm with electric and gas vehicles. The car body is the apparent place for further lightweighting to meet emission targets and thus motivates increased use of composites. But in the automotive industry cost and production cycle times are also of utmost importance. The drive to overcome these issues results in various concepts by different car manufacturers and their designers. Chris Hamar, Chief CAE Engineer at Gordon Murray Design, UK, made an introduction to their iStream concept that utilizes steel or aluminum frame with glass or carbon reinforced composite panels. With the choice of materials, this hybrid structure concept scales to different price ranges of cars. At Gordon Murray Design, Altair simulation tools are utilized in broad scale to meet the design targets.
The concluding presentation of the Altair conference at JEC was given by Denis Espinassou, Polymers & Composites Engineer at CETIM, France. In a project with ONERA, “QSD - Optimization Software for Design to Cost” has been developed for thermoplastic composite optimization. This is a good example of how new automated manufacturing methods combined with advanced design approaches, utilizing Altair OptiStruct, can be used to meet the industrial needs of simultaneous lightweighting and cost reduction.
Whilst we will surely be back next year at JEC World to present the latest in simulation-driven design of composites, in the meantime why not get a full picture of our offering at the 2018 Global Altair Technology Conference, also in Paris, in October?