Simulation of a Moving Soccer Field
This guest contribution on Innovation Intelligence is written by Katja Juschka, Marketing and Sales Manager at FLUIDON. FLUIDON’S DSHplus software provides a simulation environment specialized on the dynamic non-linear calculation of complex hydraulic and pneumatic systems and components. DSHplus is available through the Altair Partner Alliance.
The Veltins-Arena in Gelsenkirchen, Germany, is famous for outstanding soccer games. To enable a superb soccer game, the field must be in top condition. The arena planners have guaranteed this with a fabulous technical trick: when no games are scheduled, the entire grass field is moved outside the stadium. The complete playing field with a total weight of 11.400 t can be moved in and out of the stadium over a distance of 300m in four hours. This allows the grass playing surface to grow outside under normal conditions and it does not get damaged during indoor events such as concerts.
How Does a Playing Field Move?
The soccer field is pushed or pulled over 16 slideways with a Teflon coating. The motion is supported by several hydraulic modules including pumps, reservoirs, valves and cylinders that move in position control with a master-slave-structure. The whole move is done step by step, alternating a push/pull stroke with a retracting stroke. The challenge for the hydraulics and control is to get very even and steady movement of all cylinder drives independent of supply pressure, friction and other disturbances.
With such a cost-intensive project, it is worthwhile to be on the safe side by utilizing simulation programs. Simulation supports the design of such challenging tasks. As in real life with hardware, models of hydraulics and control can be delivered by different suppliers and have to be put together for a system simulation. For this additional challenge, co-simulation is the tool of choice. In order to calculate this typical application for synchronous control, the entire system is divided into a hydraulic-mechanical system and a control system. The hydraulic-mechanical system is set up in DSHplus, whereas the control system is set up with solidThinking Activate®.
Modeling the Hydraulics Actuator Systems with DSHplusHydraulic-mechanical systems can be built up in DSHplus to describe real systems. For this application, a hydraulic system with excitation of actuators was created. Afterwards, the model can be used for troubleshooting, system optimization or co-simulation with, or embedded export to, other programs such as solidThinking Activate. For export, the model is prepared with inputs for valve signals, external load and eccentricity as well as outputs for cylinder strokes. The data is transferred via FMI (Functional Mock-up Interface) and the hydraulic model is exported as FMU (Functional Mock-up Unit). The FMU file includes the hydraulic-mechatronic model, solver, parameters and descriptions.
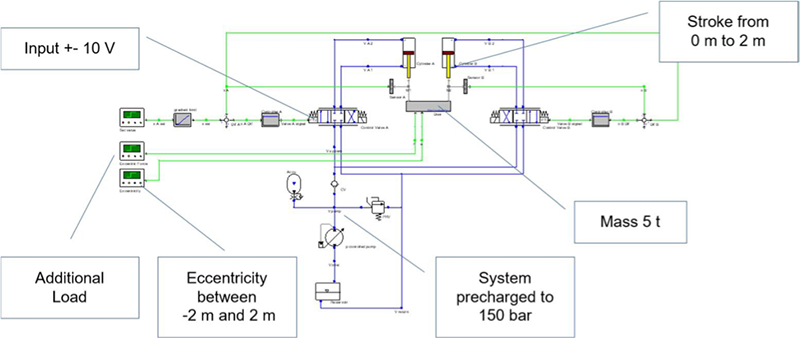
Modeling the Control System with solidThinking Activate
The hydraulics model exported by DSHplus is from now on seen as a black box, simulated within solidThinking Activate.

The connections to the hydraulic model must be set correctly to optimize the control in Activate. In the various control components, a controller can be found to reject disturbances and react fast enough to input changes. After first parameterization of the model, few steps for optimization are needed to gain optimized results.
Solution HighlightsBy offering an easy to use graphic based modeling concept for dynamic, nonlinear 1D-system simulation, DSHplus enables the user to:
- Model hydraulic systems in any desired level of detail
- Simulate the dynamic behavior of hydraulic systems
- Link DSHplus models with other software via FMI for model exchange or co-simulation

DSHplus is able to support the general engineering of hydraulic systems with simulation models with typical system level detail as well as with high-fidelity physical models.
As part of Altair’s Partner Alliance, DSHplus offers multiple options to exchange data and to interface with programs in the HyperWorks suite.For more information on FLUIDON’s work at the Veltins-Arena check out this webinar recording
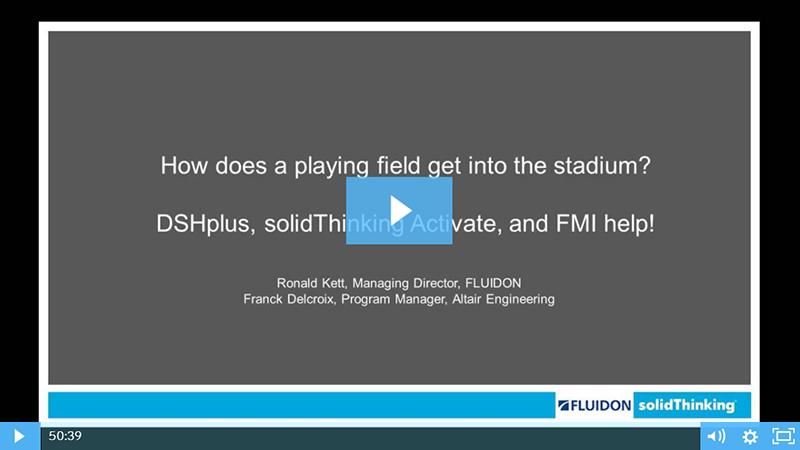