Sustainability in Metal Forming
This guest contribution is written by Renganathan Sekar, M.Sc., a research engineer at MFRC, the developers of the intelligent metal forming simulation software AFDEX which is available through the Altair Partner Alliance.
Recent advances in traditional metal forming processes have given rise to tremendous opportunities of expansion. Simulation-assisted development of hot stamping and cold forging processes have facilitated reduced material wastage. This is due to the ability to form much complicated, near-net shape geometries with enhanced material properties.
The industry has been progressing in areas such as new material identification and development, post-processing of metal-formed components, and lubrication systems. But all these iterative improvements aim to enhance the strength of the component. An underrated but important aspect is the component stiffness. And to achieve a stiffer component, the process design has to be optimal. So, the process engineer has to develop lighter components with high strength and high stiffness.
Figure 1: Simulation assisted process development in metal forming
An effective approach to spearheading sustainability is to pursue developments that would lead to a reduction in the overall requirement for new metal production. Here are 6 aspects of a metal forming process that could improve the manufacturing sustainability.
Number of stages in a manufacturing process cycle
This is one factor that has a massive impact on sustainability. Reducing the number of stages in a manufacturing process translates to reducing the necessary dies, lubricants and the energy consumption.
Material waste
It is a fact that every year, 25% of metal that is produced never becomes a product[1] but rather gets scrapped through the supply chain. This highlights the need for efficient metal forming technologies that can contribute to reducing this significant material wastage.
Energy consumption
Quantifying the energy consumption is one part. The total process time is another. The energy consumption is lower for certain incremental sheet forming processes. But some of the processes have a higher cycle time which is inevitable. There should be a balance between these two factors to reduce the total energy consumption.
Tooling and die systems
The manufacturing processes of these tooling and die systems have a crucial impact on the environment. It's not only about the optimal tool design anymore. The manufacturing processes for producing these tools must be efficient to boost the sustainability of the process chain.
Effects of temperature
Increasing the temperature increases the material formability, thereby reducing the forming loads and the energy consumption. The desired forming temperature must be arrived keeping in mind the energy consumed by heating systems of the workpiece and dies.
Lubrication conditions
Sustainability studies are never complete without investigating lubrication systems. Selection of lubricants in a metal forming process depends on the process type. Some processes need minimal usage of lubricants without affecting the energy consumption. Some don't. But to enable a wider shift towards sustainable manufacturing, the tribological aspects must be synergetic with the ecological factors.
Realizing manufacturing sustainability depends on thinking beyond familiar aspects: material consumption, waste management, elimination, and environmental impact. Decision making activities such as production planning and supplier selection must include sustainability as one of its criteria. This might even demand a slight tweaking of the business model. But in the long run as sustainable practices become the norm, the effort is definitely worth it.
References:
[1] http://www.ictp2017.org/sites/www.ictp2017.org/files/industry-workshop-3.pdf
Recent advances in traditional metal forming processes have given rise to tremendous opportunities of expansion. Simulation-assisted development of hot stamping and cold forging processes have facilitated reduced material wastage. This is due to the ability to form much complicated, near-net shape geometries with enhanced material properties.
The industry has been progressing in areas such as new material identification and development, post-processing of metal-formed components, and lubrication systems. But all these iterative improvements aim to enhance the strength of the component. An underrated but important aspect is the component stiffness. And to achieve a stiffer component, the process design has to be optimal. So, the process engineer has to develop lighter components with high strength and high stiffness.
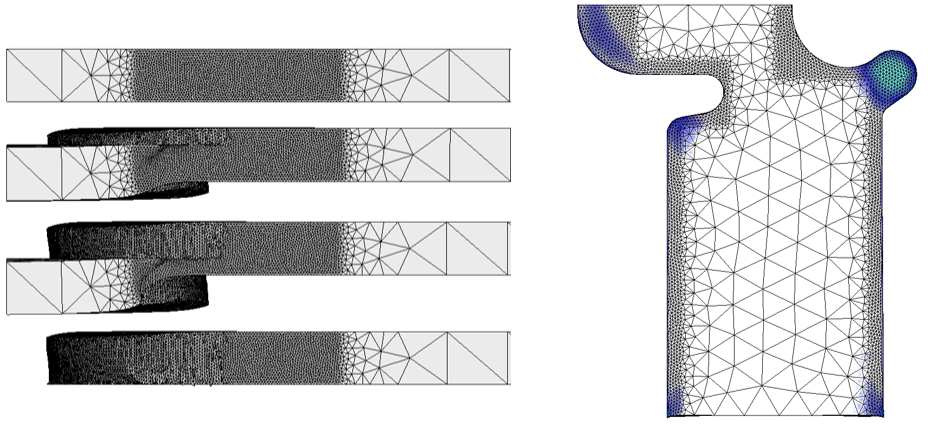
An effective approach to spearheading sustainability is to pursue developments that would lead to a reduction in the overall requirement for new metal production. Here are 6 aspects of a metal forming process that could improve the manufacturing sustainability.
Number of stages in a manufacturing process cycle
This is one factor that has a massive impact on sustainability. Reducing the number of stages in a manufacturing process translates to reducing the necessary dies, lubricants and the energy consumption.
Material waste
It is a fact that every year, 25% of metal that is produced never becomes a product[1] but rather gets scrapped through the supply chain. This highlights the need for efficient metal forming technologies that can contribute to reducing this significant material wastage.
Energy consumption
Quantifying the energy consumption is one part. The total process time is another. The energy consumption is lower for certain incremental sheet forming processes. But some of the processes have a higher cycle time which is inevitable. There should be a balance between these two factors to reduce the total energy consumption.
Tooling and die systems
The manufacturing processes of these tooling and die systems have a crucial impact on the environment. It's not only about the optimal tool design anymore. The manufacturing processes for producing these tools must be efficient to boost the sustainability of the process chain.
Effects of temperature
Increasing the temperature increases the material formability, thereby reducing the forming loads and the energy consumption. The desired forming temperature must be arrived keeping in mind the energy consumed by heating systems of the workpiece and dies.
Lubrication conditions
Sustainability studies are never complete without investigating lubrication systems. Selection of lubricants in a metal forming process depends on the process type. Some processes need minimal usage of lubricants without affecting the energy consumption. Some don't. But to enable a wider shift towards sustainable manufacturing, the tribological aspects must be synergetic with the ecological factors.
Realizing manufacturing sustainability depends on thinking beyond familiar aspects: material consumption, waste management, elimination, and environmental impact. Decision making activities such as production planning and supplier selection must include sustainability as one of its criteria. This might even demand a slight tweaking of the business model. But in the long run as sustainable practices become the norm, the effort is definitely worth it.
References:
[1] http://www.ictp2017.org/sites/www.ictp2017.org/files/industry-workshop-3.pdf