The Secret to Creating a Winning Component
Recently, Altair, Click2Cast, HBM nCode, and Voxeljet teamed up to tackle the challenges of lightweight design in mold manufacturing. The team successfully created an innovative design and manufacturing process for a wheel carrier, which enhances performance and efficiency with 3D printing and Simulation-Driven Design process by using solidThinking Inspire, Click2Cast and HBM nCode. The achievement was realized with the Precision Casting Center and now won “Component of the Year” Award in Best of British Casting at end of last year hosted by the Cast Metals Federation for its remarkable and innovative design that can change the mold manufacturing industry.

The successful processes, 3D printed mold pattern, and finally component cast from aluminum were presented and displayed for the first time at Hannover Messe last year, and sparked great recognition and discussions. During the project, designers and engineers focused on creating a new shape for the wheel carrier that would be equal in mass while performing significantly better than the original. The design was first defined by topology optimization using Inspire, applying the most severe load cases. Fatigue simulation was then performed with nCode DesignLife, and finally casting simulation was handled with Click2Cast. The optimized results were sent to Voxeljet for 3D printing of the molds.
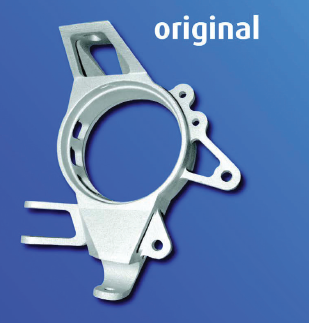
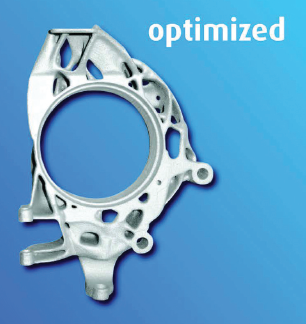
By using Simulation-Driven Design process and 3D printing, we were able to leverage the full potential of lightweight design while significantly improving performance. Congratulations to the well-deserved award! We are proud to be a part of this innovation, as the design will push manufacturing technology forward and offer many benefits for the industry.
Read more about the project, and visit Altair from February 23-27 at METAV in Düsseldorf (hall 15/F49), Germany, where the component and the processes, as well as other design innovations for 3D printing will be presented.

The successful processes, 3D printed mold pattern, and finally component cast from aluminum were presented and displayed for the first time at Hannover Messe last year, and sparked great recognition and discussions. During the project, designers and engineers focused on creating a new shape for the wheel carrier that would be equal in mass while performing significantly better than the original. The design was first defined by topology optimization using Inspire, applying the most severe load cases. Fatigue simulation was then performed with nCode DesignLife, and finally casting simulation was handled with Click2Cast. The optimized results were sent to Voxeljet for 3D printing of the molds.
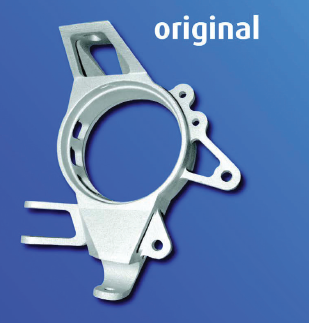
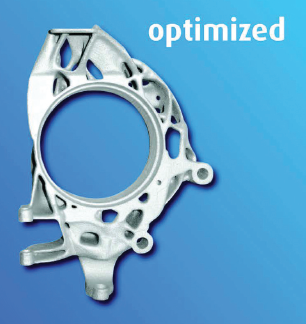
By using Simulation-Driven Design process and 3D printing, we were able to leverage the full potential of lightweight design while significantly improving performance. Congratulations to the well-deserved award! We are proud to be a part of this innovation, as the design will push manufacturing technology forward and offer many benefits for the industry.
Read more about the project, and visit Altair from February 23-27 at METAV in Düsseldorf (hall 15/F49), Germany, where the component and the processes, as well as other design innovations for 3D printing will be presented.