8 Questions to Ask When Building Your Thermal Model

Thermal modeling can be particularly challenging because setting up your thermal simulation can be different every time. Meanwhile, you seek to balance competing priorities within your design. "It should be lightweight! Durable! Affordable!" the list of hopeful attributes is extensive so some compromise will have to occur. You can better decide where those accommodations can be made with an accurate thermal model.
Even though each problem you may face has its unique challenges, you will ask yourself some standard questions every time you go to set up your model. If you are cognizant of these issues, you can save time and create an effective model.
So what questions should you be asking yourself?
Level 1: This type of model can show you directional change. If you make a design change, you can expect to see the temperature increase or decrease.
Level 2: This type of model will show A/B comparisons and will demonstrate a quantitative amount of change (i.e., the temperature changes 5 degrees).
Level 3: Can give you an absolute answer, delivering simulation results that can be replicated in your physical set up.
If you already know the problem you are facing, a directional model may be all that you need to confirm a design change. If you need to know how big of a design change to make, you may want to have a thermal model that can compare a few iterations. Taking the time to model a Level 3 thermal simulation is only necessary when you are completing a comprehensive model for a new design. This type of simulation will allow you to get real answers from your model, making your prototyping and testing phases more predictable. To learn more about our thermal modeling software, TAITherm, check out our eBook here.
Once you know what kind of solution you are looking for, you can model the appropriate level of detail.
For a vehicle where the underbody is your area of interest, the primary heat sources are the engine, radiator, and exhaust system. The primary heat sink would be the cool, ambient air moving past the vehicle and your expected heat transfer paths might be radiation heat from the exhaust system, convection heating or cooling from the underhood air, convection cooling from the fresh ambient air, conduction through mounting points, and radiation to/from the road.
Some extreme boundary conditions experienced by a vehicle only last for a short time, such as a diesel particulate filter (DPF) active regeneration. In this scenario, the filter surface temperature is very hot and radiates to the surrounding components. If a steady-state analysis is done using the peak DPF heat rates or assigned surface temperatures and a boundary condition, the temperatures of interest will be over predicted. While such worst-case simulations can help produce robust and safe designs, they can be unnecessarily heavy and expensive since they were designed based on an unrealistic worst-case scenario. Running a transient simulation will allow designers to accurately predict the true use cases and peak temperatures to best optimize the vehicle for both cost and durability.
Knowing the answers to these questions will set you up for a more successful simulation. It is still complicated, but that's why we as an industry are always looking to create better processes. Understanding what inputs you need to collect and the level of detail you need to model them can help you create your most efficient, accurate model.
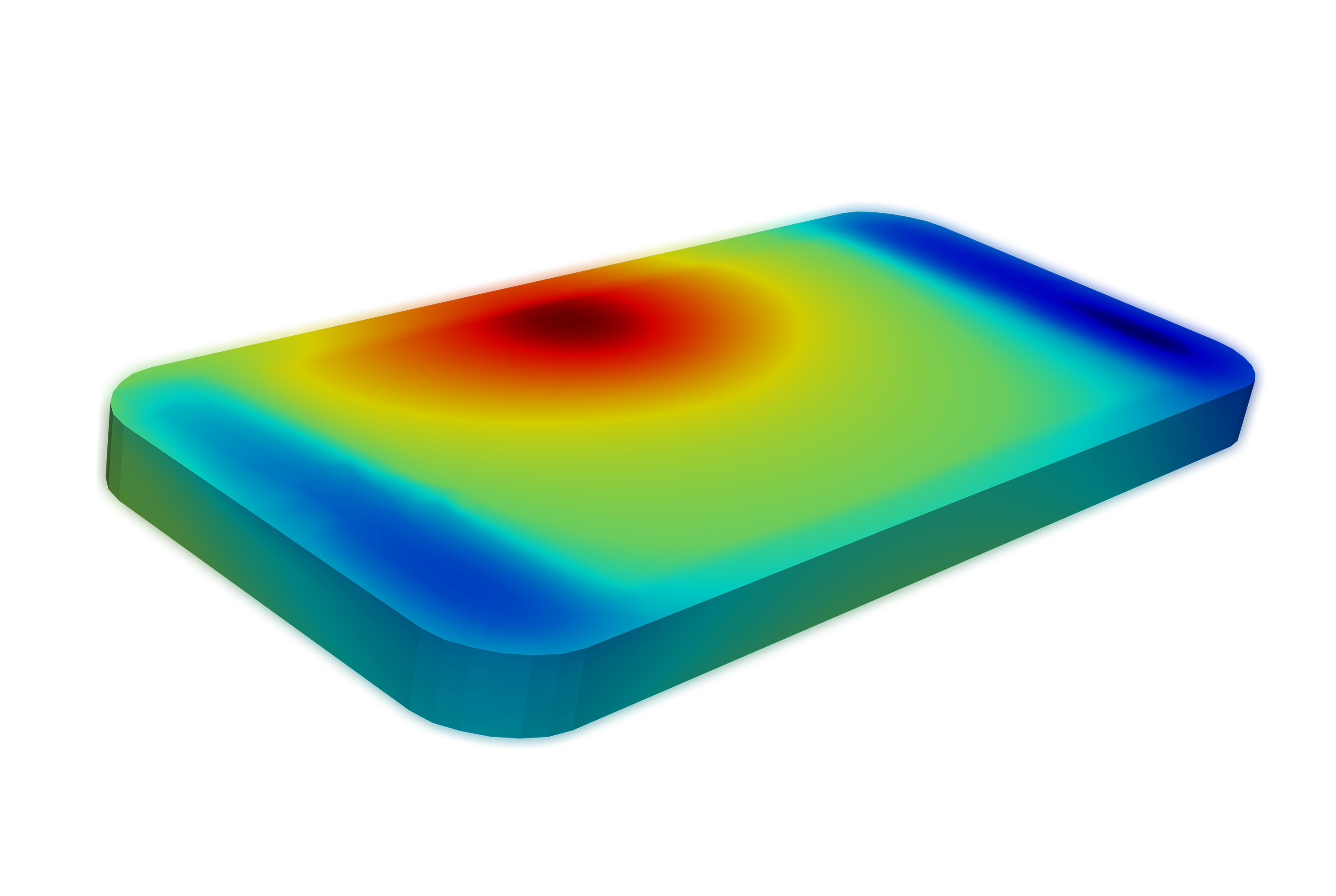
This guest contribution on the Altair blog is written by Erin Norton, Content Marketing Specialist at ThermoAnalytics Inc. TAITherm software by ThermoAnalytics is a professional thermal simulation tool for comprehensive CAE analysis of both steady-state and transient-heat transfer conditions. TAITherm is available through the Altair Partner Alliance.
Even though each problem you may face has its unique challenges, you will ask yourself some standard questions every time you go to set up your model. If you are cognizant of these issues, you can save time and create an effective model.
So what questions should you be asking yourself?
- How accurate of a thermal model do I need?
Level 1: This type of model can show you directional change. If you make a design change, you can expect to see the temperature increase or decrease.
Level 2: This type of model will show A/B comparisons and will demonstrate a quantitative amount of change (i.e., the temperature changes 5 degrees).
Level 3: Can give you an absolute answer, delivering simulation results that can be replicated in your physical set up.
If you already know the problem you are facing, a directional model may be all that you need to confirm a design change. If you need to know how big of a design change to make, you may want to have a thermal model that can compare a few iterations. Taking the time to model a Level 3 thermal simulation is only necessary when you are completing a comprehensive model for a new design. This type of simulation will allow you to get real answers from your model, making your prototyping and testing phases more predictable. To learn more about our thermal modeling software, TAITherm, check out our eBook here.
Once you know what kind of solution you are looking for, you can model the appropriate level of detail.
- What are my areas of interest?
For a vehicle where the underbody is your area of interest, the primary heat sources are the engine, radiator, and exhaust system. The primary heat sink would be the cool, ambient air moving past the vehicle and your expected heat transfer paths might be radiation heat from the exhaust system, convection heating or cooling from the underhood air, convection cooling from the fresh ambient air, conduction through mounting points, and radiation to/from the road.
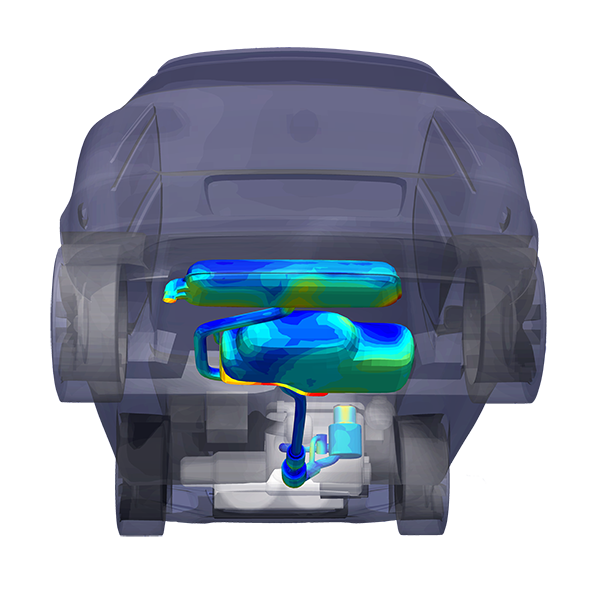
- What geometry should I include?
- How detailed should my geometry be?
- What component properties do I need to include?
- What is the component made of
- How thick is it
- What is the components emissivity
- What boundary conditions are specific to your scenario
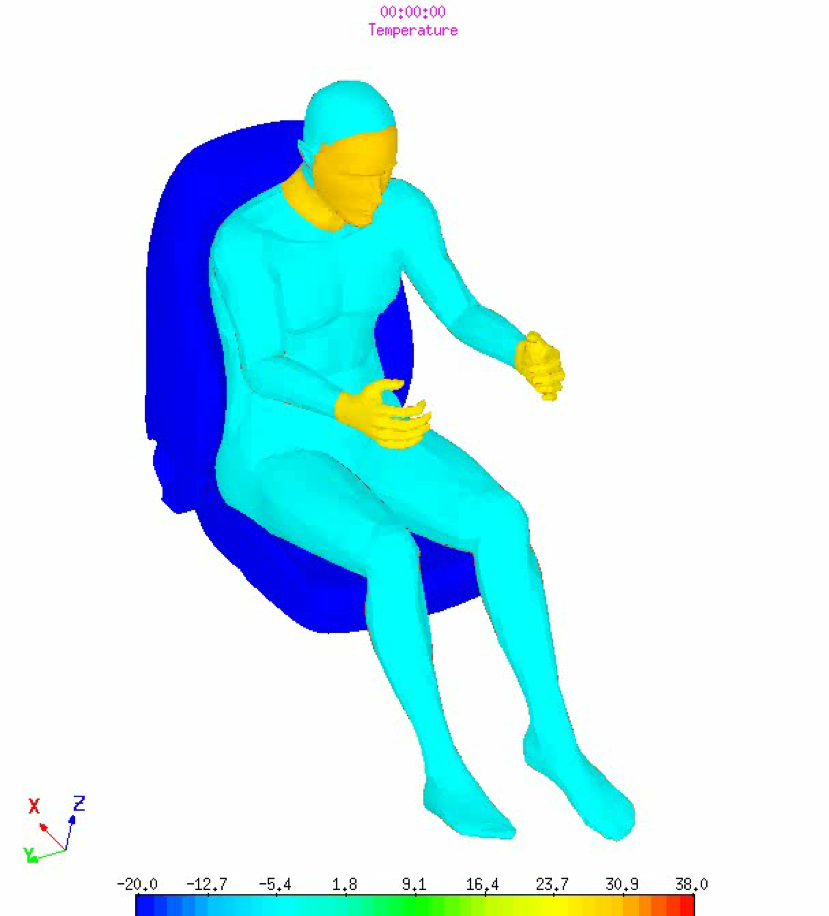
- How should I set-up my heat sources?
- Should I run a steady-state or transient simulation?
Some extreme boundary conditions experienced by a vehicle only last for a short time, such as a diesel particulate filter (DPF) active regeneration. In this scenario, the filter surface temperature is very hot and radiates to the surrounding components. If a steady-state analysis is done using the peak DPF heat rates or assigned surface temperatures and a boundary condition, the temperatures of interest will be over predicted. While such worst-case simulations can help produce robust and safe designs, they can be unnecessarily heavy and expensive since they were designed based on an unrealistic worst-case scenario. Running a transient simulation will allow designers to accurately predict the true use cases and peak temperatures to best optimize the vehicle for both cost and durability.
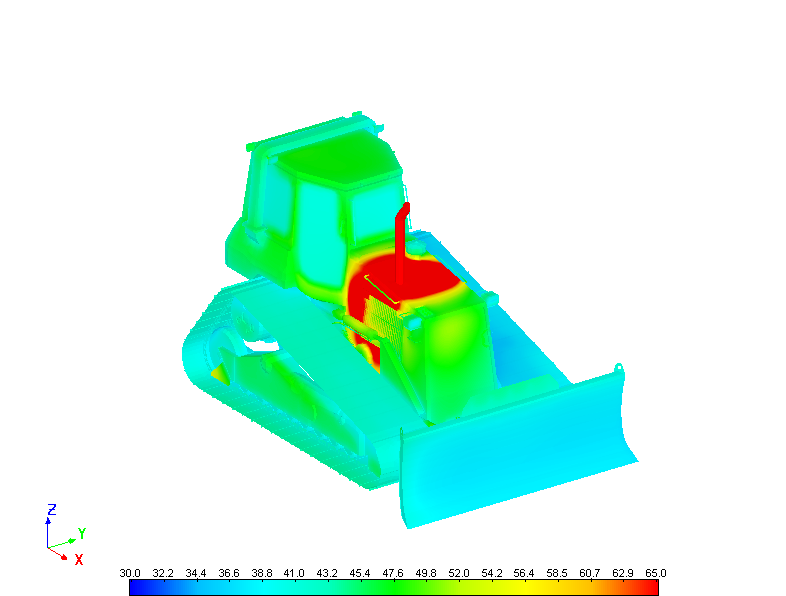
- In what kind of environment will my simulation take place?
Knowing the answers to these questions will set you up for a more successful simulation. It is still complicated, but that's why we as an industry are always looking to create better processes. Understanding what inputs you need to collect and the level of detail you need to model them can help you create your most efficient, accurate model.
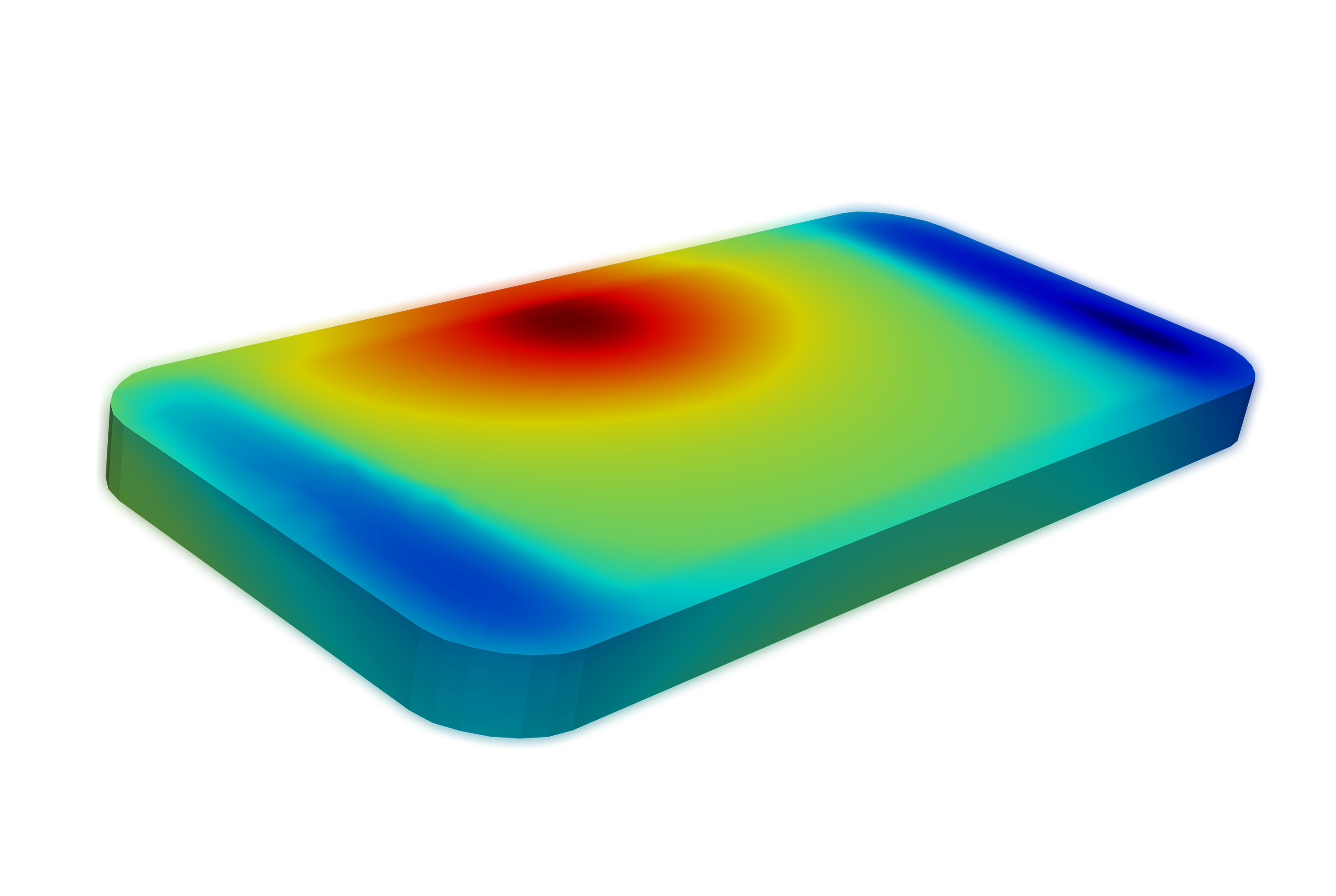
This guest contribution on the Altair blog is written by Erin Norton, Content Marketing Specialist at ThermoAnalytics Inc. TAITherm software by ThermoAnalytics is a professional thermal simulation tool for comprehensive CAE analysis of both steady-state and transient-heat transfer conditions. TAITherm is available through the Altair Partner Alliance.