
Altair® HyperMesh® Applications
Altair® HyperMesh® provides effective, easy-to-learn workflows that leverage domain knowledge and increase team productivity, enabling the efficient development of today’s increasingly complex and connected products.
Solution- and domain-specific workflows span a growing number of engineering applications, including fatigue analysis, concept design optimization, design exploration, crash and safety, noise, vibration, and harshness (NVH), and computational fluid dynamics (CFD) modeling. Each provides an intuitive, meticulously designed user interface that caters to each user profile while remaining consistent and straightforward.
Learn More About HyperMesh
Model Build and Assembly
HyperMesh includes an end-to-end model build and assembly modeling environment, going from CAD to multi-disciplinary simulation models. Dedicated workflows for parts, subsystems, and connectors facilitate representation, revision, and configuration management during the assembly and analysis process. The included Altair libraries enable seamless distribution of tasks and collaboration between teams both local and remote.

Optimization-enabled Design Space
The HyperMesh design space workflow streamlines the model build process for topology optimization. The complete toolkit includes an automotive-only non-design space library, collision detection, and a fast and efficient voxel Boolean mesh engine. Users can explore model variants in seconds, enabling quick package space changes. In addition to automotive BIW architecture studies, it supports design space local and global modeling for generic subsystems in different industries.

Design Exploration
Gaining insight into product performance has never been easier. With the HyperMesh design explorer, users can easily setup and execute design of experiments (DOE) and optimization studies, learning which attributes contribute the most to the different performances, review, plot, and compare results from multiple runs, and ultimately identify optimal designs. The quick and easy setup process is solver independent, yet fully integrated with Altair’s structural analysis solutions.

AI-Powered Engineering
Integrated AI-powered technology within HyperMesh unlocks limitless potential for gaining insights, accelerating predictions, and improving engineering decisions. Geometric deep learning identifies shape and performance relationships for any physics to deliver predictions up to 1000x faster than traditional solver simulations. This physicsAI technology trains models from historical data without the limits of parametric studies.
Additionally, shape recognition technology recognizes patterns and shapes in CAE models. Extracting features from geometry for classification and grouping significantly reduces the need for manual intervention early in the build process, paving the way for the rapid generation of high-fidelity CAE models. And expert emulation can automate optimization by training and deploying models that emulate the decision-making of experienced users. This approach ensures that subjective design factors are effectively integrated into the optimization process.
How can we help streamlining your modeling and visualization workflows?
Contact Us
Computational Fluid Dynamics (CFD)
A dedicated, optimized CFD simulation environment is part of HyperMesh, offering a consistent interface for all of Altair’s CFD solvers. The end-to-end workflows streamlines model setup with advanced geometric modeling and editing, extensive physics coverage, as well as automated meshing with light memory footprint. It includes direct solver execution and post-processing all within the same intuitive, easy-to-learn user interface.

Crash and Safety
HyperMesh includes a tailored environment to efficiently assist crash and safety engineers in model building, starting from CAD geometry and finishing with a runnable solver deck in Altair® Radioss® and other third-party solvers. From dummy positioning and seat mechanisms to airbags and seat belt routing, it provides an end-to-end analysis workflow that streamlines the setup of impact simulations in accordance with different regulations.

Fatigue and Durability
HyperMesh also features an easy-to-learn fatigue and durability analysis workflow. Developed on a solver-neutral framework, it provides a comprehensive toolset for durability analysis, directly interfacing with all the major finite element analysis (FEA) and multi-body simulation (MBS) results files. With an embedded material library, it enables the prediction of fatigue life under repetitive loadings experienced in a wide range of industrial applications. In addition, it supports signal processing, weld certification, and norm-based fatigue analyses.

Noise, Vibration, and Harshness (NVH)
HyperMesh offers a broad range of functionality for NVH engineers, designed to reduce the simulation cycle time and free CAE analysts to focus on optimizing product design and performance. Particularly suited for automotive applications, the HyperMesh workflow makes full-vehicle NVH simulation possible in the most advanced, most streamlined form. Multiple, interchangeable, and dynamic representations of the model are easily managed along with global loadcases, post-processing, and advanced NVH diagnostics. With it, users can easily perform and evaluate robust design studies of the global NVH performance.
Featured Resources

Design Explorer: Driving the Simulation Process using Artificial Intelligence
In this presentation, Ira Goldstein, Director of Product Management for Simulation & Design Development at Altair, will showcase the Design Explorer, which is a user-friendly design ideation workflow that facilitates multi-run simulation setup, execution, and interpretation. Integrated seamlessly into the modeling environment, the Design Explorer allows users of the Altair HyperWorks platform to quickly and efficiently evaluate design changes, perform designs of experiments, and run optimizations.
The presentation will also explore how artificial intelligence (AI) is being integrated into the product design process, with a particular focus on how it can help in decision making, reduce human error, and even inspire new inventions. Advanced machine learning techniques can be used to train exploration-generated data, making the Design Explorer a natural environment for the convergence of simulation and AI. Attendees can expect to gain a better understanding of the Design Explorer workflow and learn how AI is being incorporated into the process.
Presented as part of Altair's 2023 Future.Industry conference.

Machine Learning in Engineering
When applied to engineering, Machine Learning can be a powerful tool to aid in a range of applications, from faster finite-element (FE) model building to optimizing manufacturing processes and obtaining more accurate results from physics-based simulations. Although incorporating this collection of technology is relatively new in the field of engineering, Altair has made leaps forward in this space to provide users with the tools they need to make a difference.

Unleash the Power of AI for Generative Design
Generative Design represents an innovative and exciting new workflow within the HyperMesh Design Explorer, set to debut in HyperMesh 2024. AI algorithms in Generative Design help process the multi run topology optimization results and intelligently organize them into similar family of designs so that engineers can quickly select the best for a detailed design evaluation.
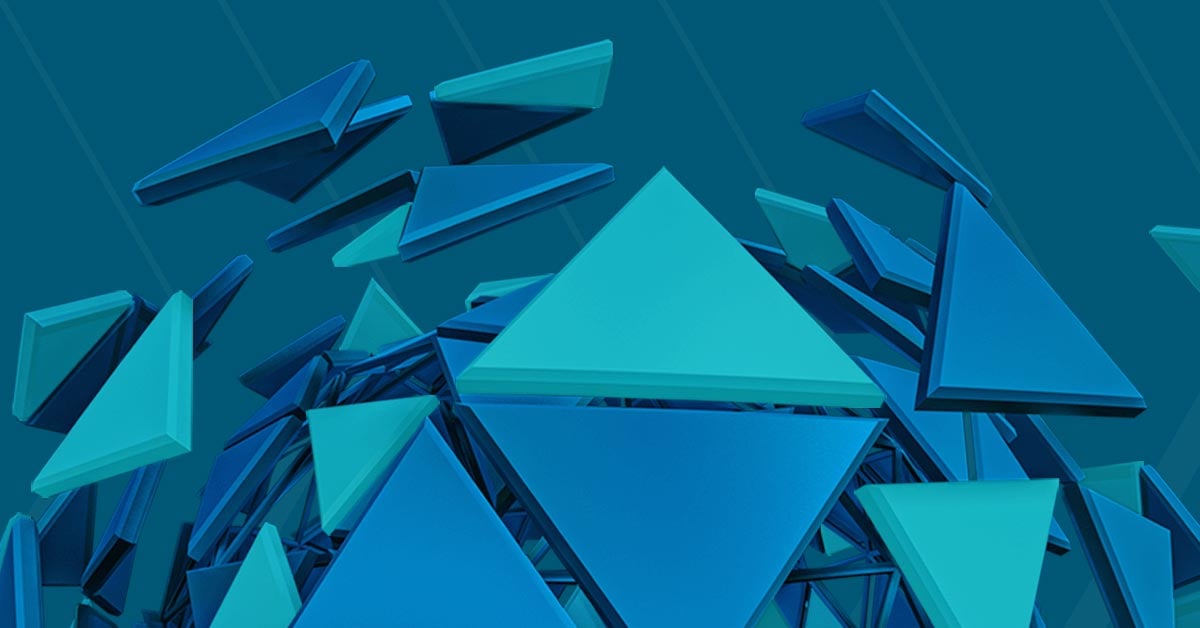
Efficient Simulation Data Processing in HyperWorks
In this session we will highlight how Altair HyperWorks supports efficient data processing and visualization, thereby helping users to make decisions faster. From the simulation-driven design workflow, fully integrated with HyperWorks’ model build functionalities, to the high-performance visualization and reporting of simulation results, HyperWorks provides the best framework to visualize, process, and report data
Presented as part of Altair's 2021 Future.Industry Conference.