EMC Simulation during the Product Development Process
We have seen a significant increase in the number of electronic, electrical and communication systems and components in many industries during the last decade. Electromagnetic Compatibility (EMC) describes the ability of such systems and components to work correctly when they are close together. The fact that the number of electronic systems is growing has increased the number of potential EMC issues. Within EMC we refer to Electromagnetic Interferences (EMI), which are the undesired emissions of a component or system that can interfere with another system, and to Electromagnetic Susceptibility or Immunity (EMS), when referring to how immune a system or component is to external electromagnetic interferences. Depending on the nature of the electromagnetic signal, we can also refer to radiated or conducted interferences (or emissions).
EMC has become a key and sensitive topic for system and equipment manufacturers and their suppliers in a wide variety of industries, including automotive, aerospace, defense, communications, railway, consumer electronics, energy and healthcare. These organizations need to ensure their products function properly in their electromagnetic (EM) environment without introducing electromagnetic disturbances that interfere with other systems, while still fulfilling the related and growing number of EMC standards and regulations. Such regulations are developed by international bodies like IEC and ISO. While government organizations are regulating these standards, some OEMs may also have their own and stricter standards (based on the international ones).
FEKO, part of the Altair HyperWorks CAE simulation software platform, is helping OEMs and their suppliers to perform electromagnetic simulations of EMC for design, validation and analysis. In some markets, such as automotive, development processes are changing from measurement driven to simulation driven, since fewer prototypes are available and there is less time for measurement and testing.
EMC applications where FEKO is being used, include emissions, immunity, lightning effects, High Intensity Radiated Fields (HIRF), Electromagnetic Pulses (EMP), shielding effectiveness and radiation hazard, among others. These applications can be addressed efficiently thanks to FEKO’s wide set of hybridized solvers, together with the integrated cable modelling tool.
EMC on Aerospace
Analysis and protection against HIRF is a key and sensitive topic in several industries including aerospace. In this example, an aircraft is illuminated by a plane wave in free space where the electric and magnetic fields are simulated at specific points on and in the aircraft and induced currents on the cables are calculated from 100 kHz to 1 GHz. With Method of Methods (MoM) this model would require more than 1 TB of RAM to solve at the highest frequency. From the wide set of solvers available in FEKO, two possible methods to use for this problem are Finite Difference Time Domain (FDTD) and Multi-Level Fast Multipole Method (MLFMM). Resonance effects in the almost closed cavity structure at the electrical equipment bay area of the airplane can significantly increase run time if FDTD is used, whereas this is not an issue for MLFMM. In this case the problem was solved with MLFMM solver in FEKO.
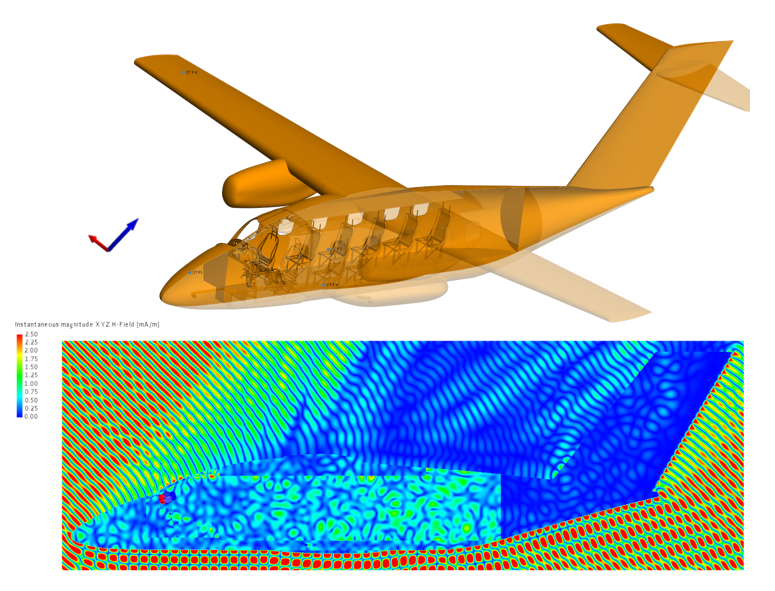
HIRF is one of the important applications in the aerospace industry, but there are other EMC effects as explained by COMAC in this case study on EM protection design for electromagnetic effects of civil aircraft or by NASA in this story where FEKO is helping to develop wireless resonant sensors that can measure and mitigate lightning strike damage to composite aircraft.
Emissions and Immunity at a Vehicle Level
In the automotive industry, the number of Electronic Control Units (ECUs), controlling the electrical systems and sub-systems in a vehicle, is growing while their potential EMC issues need to be mitigated. ECUs in the car are typically connected to cables, being such cables one of the main contributors to radiated emissions in the vehicle. FEKO has a dedicated tool for cable modelling, including a Multi-Conductor Transmission Line (MTL) solver.
The example below shows a model of a car including a windscreen antenna, cable harness and equivalent source (accounting for the radiated emissions of an ECU). Such model is built in FEKO together with the setup used to measure the radiated emissions from 30 MHz to 1 GHz at a vehicle level according to one of the EMC standards.
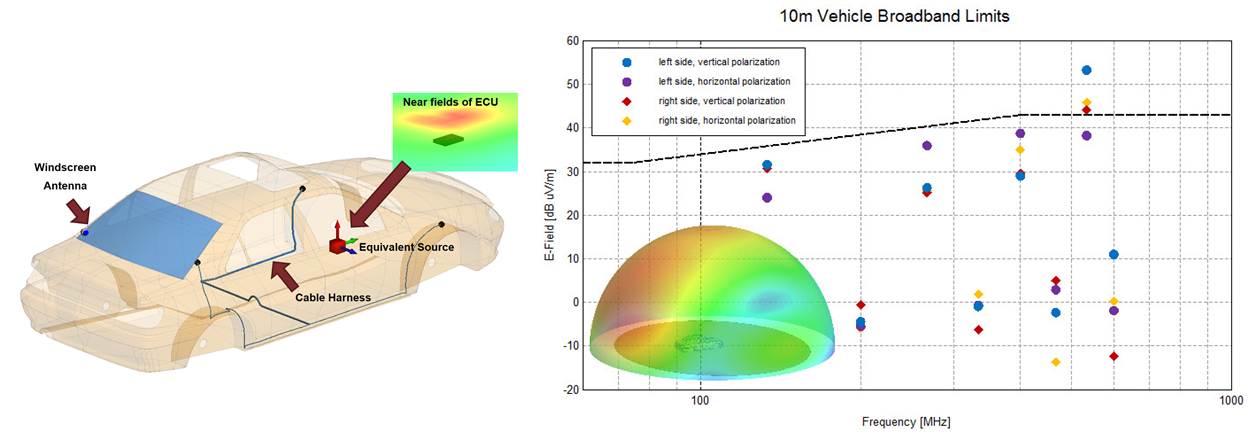
Automotive OEMs are also using EM simulation for EMC immunity at a vehicle level, immunity being key for applications like safety systems and autonomous cars.
FEKO is used for the simulation of the automotive immunity tests according to the ISO 11451-2 substitution method. In the figure below one can see the model of a sedan in FEKO and the considered simulation cases, where all eight antennas are simulated in a single run but the results are considered for each antenna separately. Also, in the figure below there is the comparison between measurements and FEKO simulations for one of the considered positions.
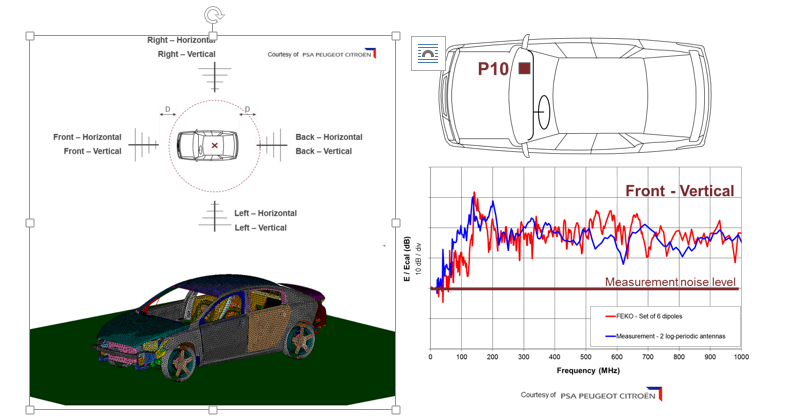
Shielding Effectiveness
Shielding is an important area of EMC across many industries and FEKO is able to compute electric and magnetic shielding factors for metallic or dielectric enclosures of arbitrary shapes with arbitrary openings or slots in them.
By analyzing the near fields and currents on shielding enclosures, the hotspots on the enclosure can be identified. This allows the geometry of the enclosure to be optimized so to reduce such hotspots, which increases the shielding factor. Another important design aspect is the possibility that FEKO is able to analyze how the different materials for the enclosure are affecting the shielding factor. Hyundai MOBIS Automotive Group explains in this story how they improved the EMC analysis process from 2D to 3D using FEKO for shielding effectiveness simulation.
Another industry where shielding is important is consumer electronics. It is of interest to calculate the shielding effectiveness of PC towers. To do that, in FEKO the tower is illuminated from the front at different frequencies and the field leakage into the tower is computed. Given the detailed geometry and the broad frequency range being covered, FDTD in FEKO is selected and results are compared at different frequencies to understand the effectiveness of the tower shielding.
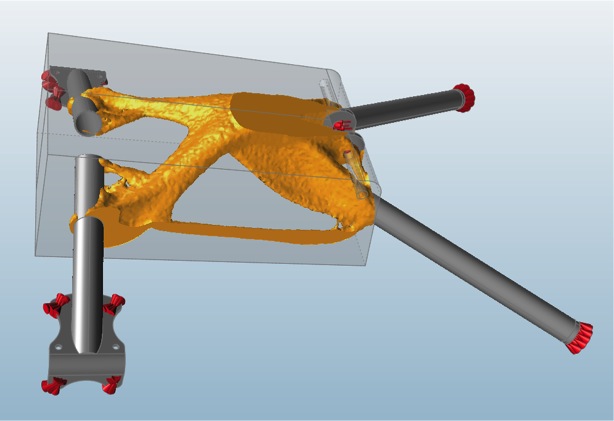
Radiation Hazard
Designers of communication equipment and system level integrators have to apply the appropriate standards in testing and validation process for their devices and systems to ensure the safety of personnel and combustible in close proximity to sources of radiation. The International Commission on Non-Ionizing Radiation Protection (ICNIRP) publishes one of the globally accepted guidelines for radiation safety of humans. These guidelines provide reference levels for field strength and basic restrictions in terms of localized peak Specific energy Absorption Rate (SAR) and whole body average SAR. Military platforms typically have to conform to field strength regulations on the Hazard of Electromagnetic Radiation to Ordnance, Fuel and Personnel (HERO, HERF and HERP). FEKO is ideally suited to radiation hazard investigations in all these scenarios.
In Conclusion
Although a lot of measurements are still being done for EMC, the number of users who have moved or want to start moving from measurement driven processes to simulation driven processes at the early stages of the product design cycle is increasing significantly. Does this mean that simulation will replace measurements for EMC? The answer is no, but EMC simulation can help to significantly reduce the number of measurements and related costs during the development and validation phases.