Digital Debunking: The Man with the Golden Gun – Is It Possible to Complete the Famous James Bond Corkscrew Jump?
The year was 1973 in rural Thailand on the set of James Bond film The Man with the Golden Gun. As eight cameras pointed eagerly at British stuntman Loren “Bumps” Willard in his modified AMC Hornet X, ambulance crews, divers, and cranes sat ready and waiting to spring into action should the worst happen. Willard pointed the iconic car at the specially designed yet precarious looking wooden ramp and sped up to 40 mph, launching it across a narrow river and successfully rotating 270 degrees, landing perfectly on the other side. Despite Roger Moore’s awful Southern accent and the questionable whistle sound effect added post-production, this one-take marvel was one of the most daring and memorable stunts in cinematic history. In fact, we love it so much we decided to recreate it using Altair products.
The Story of the Stunt
The aptly dubbed "astro-spiral jump" had been performed before the Bond film by U.S. racing driver Jay Milligan the previous year at the Houston Astrodome. The legend goes that Milligan contacted the Bond producers with the stunt who promptly copyrighted
it to prevent it from appearing in other preceding films. Wise actions considering how synonymous the astro-spiral jump has become with James Bond. Performing this stunt in a controlled environment and pulling it off on a movie set however are two
completely different things. The movie producers couldn’t exactly rely on a trial and error approach.
To avoid potentially dangerous and costly physical trials, the producers turned to Raymond R. McHenry, the brains behind a mathematical
model called the highway-vehicle-object simulation model (HVOSM). This model is based on the fundamental laws of physics combined with empirical relationships derived from experimental test data such as tire and suspension characteristics. After compiling
definitive physics models about how cars worked, moved, and crashed, the HVOSM showed promising results at predicting the behavior of a car during such a stunt and was used to calculate important parameters such as the angle of the launch and landing
ramps, ideal vehicle speed, and roll velocity (230 degrees/second if anyone’s interested). McHenry even published the results of his model in a paper. Considering the lack of computational power in the 1970s compared to today, this is impressive to say the least.
Behind the Scenes
An important aspect of this stunt is that the AMC Hornet X used was modified. A roll cage was installed, along with a central steering position, and perhaps most importantly, a fifth contact point in the form of a rigid wheel positioned between the two rear wheels. This fifth contact point meets the end of the launch ramp to create enough torque along the Y-axis, making it possible to achieve the desired pitch angle.
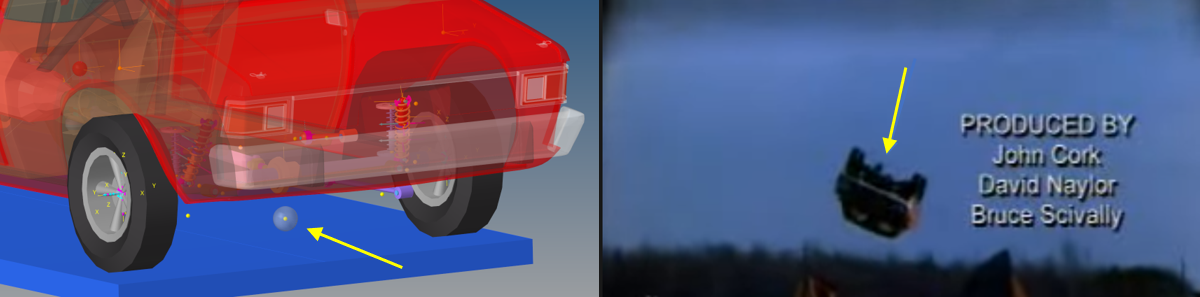
As you can see below, without this fifth contact point the stunt ends in disaster:
Recreating the Stunt – The Car
To accurately represent the car we used Altair® MotionSolve®, our 3D multi-body system simulation tool that predicts the dynamic response and optimizes the performance of products that move. We also took as many vehicle parameters into account as possible based on available AMC Hornet X data. The total car weight was set to 1450kg, allowing 1300kg for the base weight, 70kg for stunt vehicle modifications, and 80kg for the driver weight. The wheelbase was set to 2.7 meters, along with a suspension setup that included a front independent double wishbone with rear solid axis. Parameters of the springs, shock absorbers, and bump stop reinforcements were based on typical values from a standard car, with the fine tuning of these values being made to match the behavior of the stunt car.
Recreating the Stunt – The Ramps
As you can imagine, the angle of these ramps plays a critical role in the success of the stunt and as previously established, a 230-degree rotation of the vehicle was needed. Because of this, the ramp dimensions and angles used in our simulation were reversed engineered to be as accurate as possible, resulting in a successful 250-degree rotation per second of the vehicle. Using Altair® HyperMesh®, our market-leading, multi-disciplinary finite preprocessor, the launch and landing ramp surfaces were created and meshed with triangle elements known as TRIA. This was so that MotionSolve could assign the elements as a tire interaction surface.
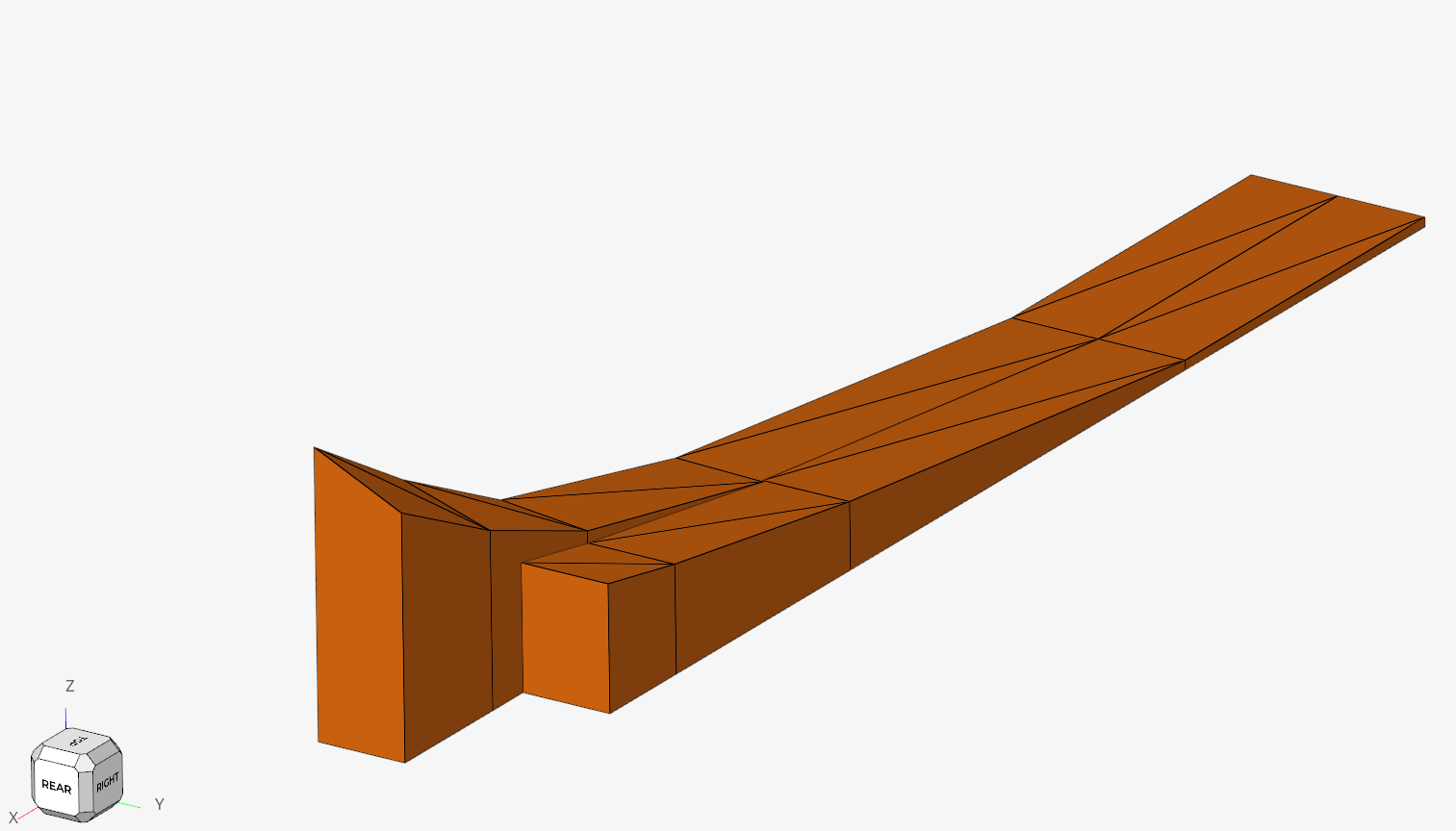
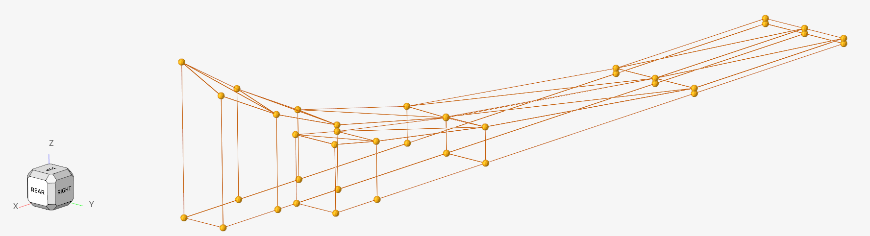

For the tire modelling, the Pacejka model was used to capture the vertical and lateral dynamics, with the friction coefficient reduced to 60% to mimic the old tires and country road surface present in the Bond film.
The result of these combined factors is a successfully simulated Astro-Spiral Jump!
Adding the Hollywood Touch
Whilst performing these simulations provided us with a successful recreation of the astro-spiral jump, the next step would be to render our results using Altair® Inspire™ Studio. Inspire Studio is a solution for innovative designers, architects, and digital artists to create, evaluate, and visualize designs faster than ever before. With unrivaled flexibility and precision, its unique construction history feature combined with multiple modeling techniques empowers users throughout the creative process. The final product is a fantastic looking rendering that we’re sure Raymond R. McHenry himself would be impressed with:
Our investigation into this world-famous stunt has been an interesting one. McHenry’s groundbreaking HVOSM model, along with the pure driving skill of Willard, made cinematic history and deservedly so. Using our multi-body dynamics, finite element preprocessor, and 3D design and rendering tools, we were able to establish that this stunt is only possible with a specially modified car consisting of a fifth contact point, such as the AMC hornet used in the real stunt. Without this, you’ll end up shaken and stirred.
