Analyzing the Operation and Design of an Autogenous Mill Using Altair EDEM in Collaboration with Tega Industries
A mill is a device that breaks solid materials into smaller pieces by grinding and crushing. Comminution is an important unit operation in many processes and there are many different types of mills for different types of materials processed.
Tega Industries has more than 500 grinding mills lined in over 68 countries globally. They pride themselves in providing reliable product quality and ensuring each mill and liners are designed with each customer’s operation in mind. Their Mill Lining design is continuously improved as wear performance is simulated and monitored. Tega uses Altair EDEM to simulate the operation of their autogenous mills as it enables them to increase the mill’s capacity and throughput, improve grinding efficiency, reduce mill down time and lower the liner cost per ton of grind. As part of recent collaboration with Tega, a simulation of a full-scale mill was set up in EDEM in order to show the type of analysis that can be performed with the software. The simulation was run on a single high-level GPU card.
EDEM provides a wide variety of options enabling advanced mill design and operation optimization:
The ore rheology at different sections along the mill can be analyzed, allowing visualization of the key regions such as the ‘grinding’, ‘shoulder’ and ‘impact’ regions. EDEM accurately shows how these regions vary depending on parameters such as the fill level and RPM, traditionally decided empirically during the mill’s operation.
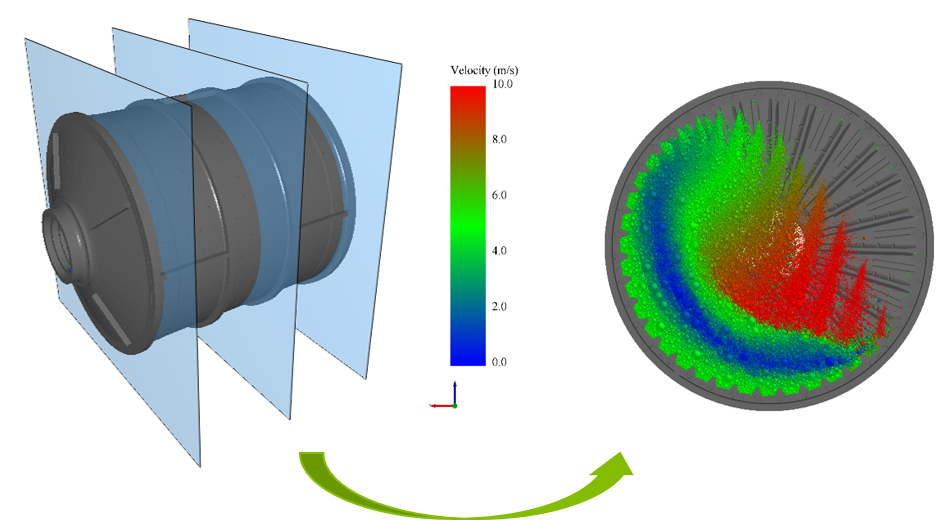
The pressure and forces experienced as well as the wear on the mill’s liners can also be obtained using EDEM, enabling optimization and better planning for each mill’s maintenance.
Since a full-scale mill was simulated, the velocity magnitude of particles across the mill’s drum (left to right) could be easily visualized. Specifically, the particles flowing in the mill have a ‘positive’ velocity, most of the particles in the middle of the drum do not travel across, and the particles at the grate have a ‘negative’ velocity due to bouncing back into the drum.
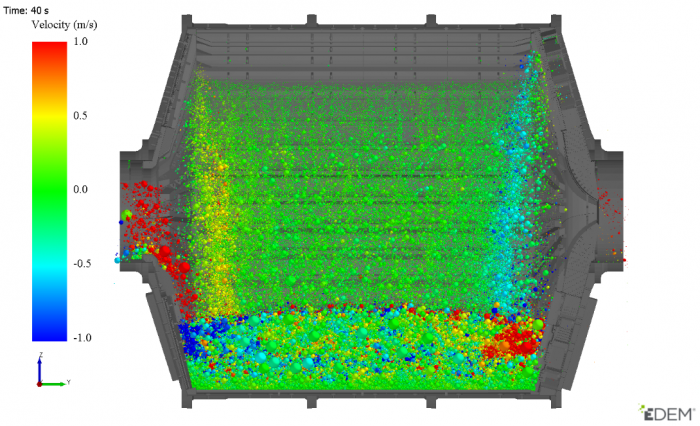
By using custom sensors in the EDEM Analyst, the discharge and volumetric flow rates can be measured, as well as the undesirable carry-over effect, providing useful data for the mill’s operator and/or designer.
Users can also benefit from using ‘EDEMpy’ for mill analysis: a Python library for post-processing and analysis of EDEM data. Specifically, Python was used to analyze the data and assess the mill’s design by quantifying how many of the particles had exited the drum and then flowed back during the simulation, an analysis not possible with standalone DEM software. Also, histograms with each particle’s collision energy in the mill were plotted, providing crucial insight for the mill’s performance.
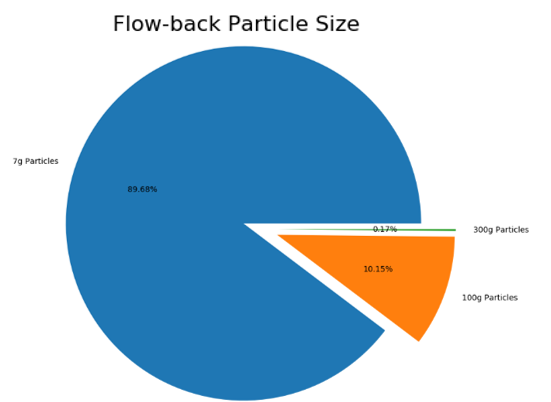
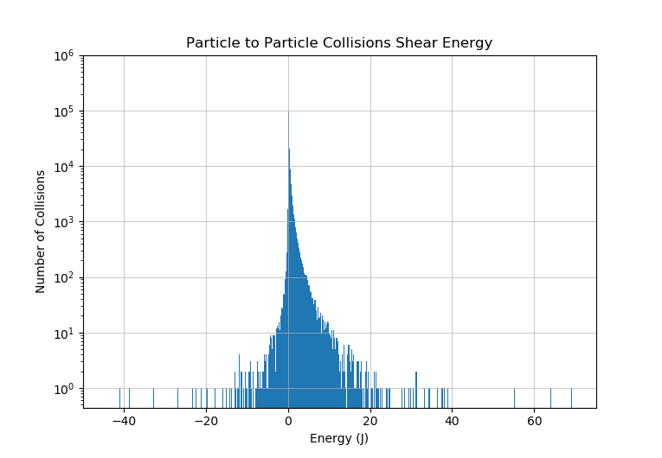
For even further analysis it is possible to simulate ore breakage using the Tavares Breakage Model. More information on this model can be found in this article.
Here is a video showing the full-scale mill simulation and analysis:
IN SUMMARY, EDEM provides a range of benefits for Autogenous Mills:
- EDEM’s GPU solver allows the simulation of a full-scale mill with even a single GPU in reasonable timeframes.
- The milling process parameters such as the mill’s RPM and fill level can be simulated and optimized.
- The mill’s liner design can be optimized, as well as the grate and discharger for different applications.
- Comminution in the mill’s drum can be accurately modeled using the Tavares Breakage Model
- Advanced post-simulation analysis can be achieved using EDEMpy for quantifying the mill’s flow-back and analyzing the particle collision energies.
- An overall decrease in the plant’s operating costs can be achieved as a result of optimized mill liner design and operation.
To see more examples of applications of EDEM in the mining and metals industry visit this page.