Applying Big Analysis Power to Small Components: Solenoid Valve Simulation with AI-Augmented Multiphysics
A solenoid valve is a simple on/off valve commonly used in air compressors, pumps, industrial water control, and car wash and laundry equipment. Available in a wide range of pressure ratings and sizes, they are used in fluid power pneumatic and hydraulic systems to control cylinders, fluid power motors, or larger industrial valves. These important, if often overlooked, components are made up of two basic functional units – the valve body and the solenoid electromagnet, which when energized or deenergized shuts off or allows flow through the valve orifices.
Compared to many other highly complex components that engineers are tasked with designing and validating through simulation, the humble solenoid valve might appear inconsequential by comparison. Why focus on optimizing something that seemingly has little room for improvement?
Often, product engineers view the function of a solenoid valve through a limited computational fluid dynamics (CFD) lens. By optimizing the flow path through the valve, you’ve optimized the component. But the actuation of the valve also plays an important role for reliability and safety. The actuation problem, however, is much more complex, requiring an understanding of the interaction between magnetics, hydraulics, fluid dynamics, and mechanics. To optimize the solenoid valve actuation, a multiphysics approach is needed to consider all forces, leading to an optimal design of the entire system.
Using System Modeling to Set Up Multi-Disciplinary Analysis
Altair Activate® is an open and flexible integration platform for comprehensive system of systems simulation. Based on a hybrid block diagram modeling environment for signal blocks, object oriented physical components, and electric and electronics systems, Altair Activate® allows multiphysics analysis throughout the development cycle.
Applied to the solenoid valve analysis, Activate® allows engineers to bring together mixed fidelity models from all domains – electromagnetics, mechanics, hydraulics, and fluid dynamics, into a unified simulation of the entire system. Convenient parameterization and simulation control allows engineers to visualize and adjust essential settings, boundary conditions, and sub-models.
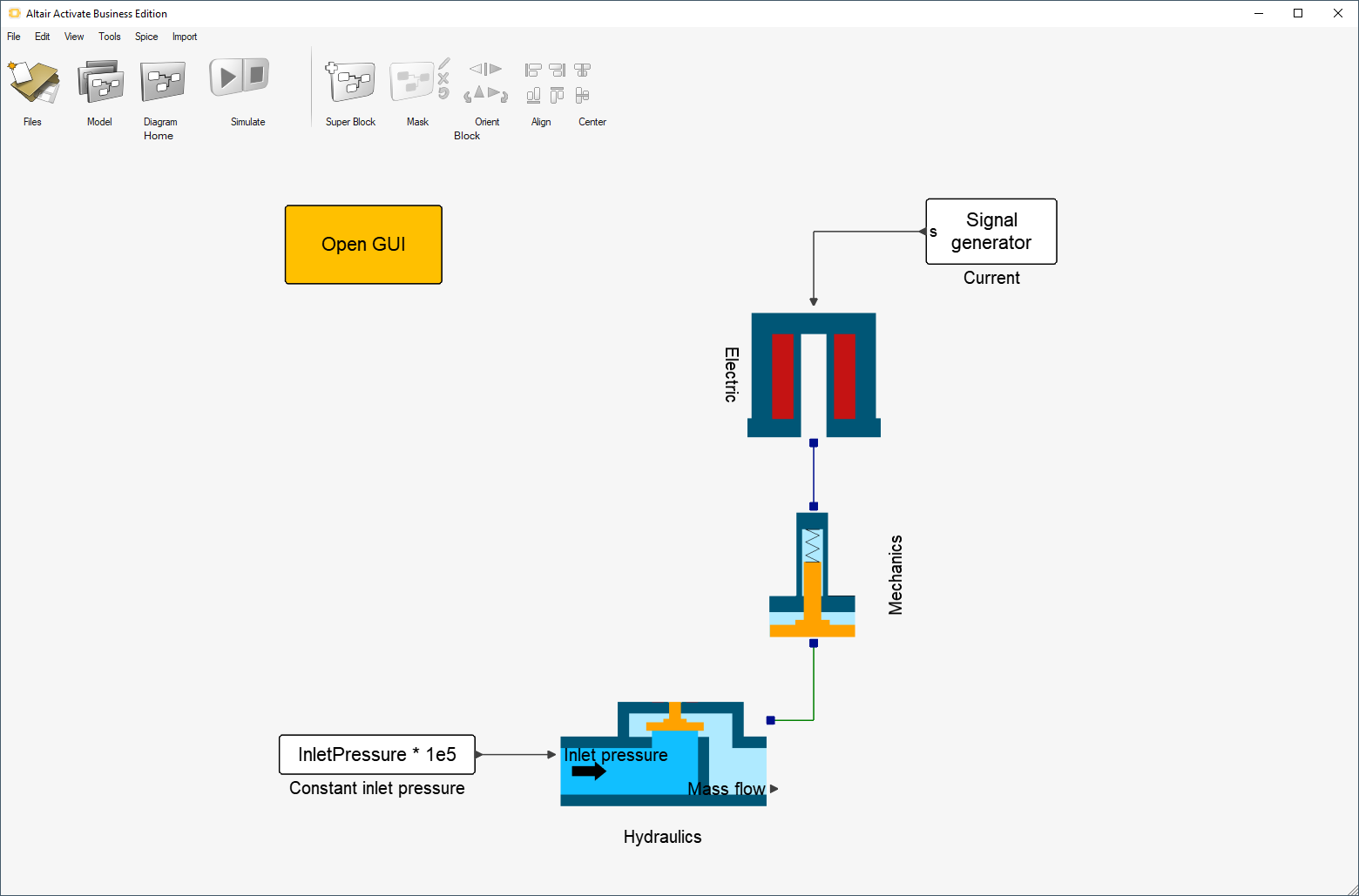
Mechanics
Within Activate®, Modelica Standard Library (MSL) is used to model the mechanics of the mass of the valve’s plunger and spring. Magnetic force, pressure forces, and flow forces can be calculated in their own domain model and added to the connections.
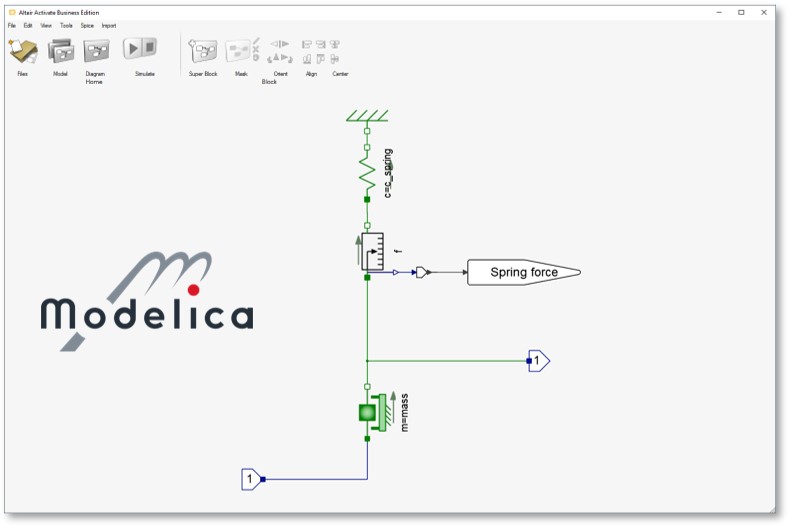
Electromagnetics
The electromagnetic analysis is solved using Altair Flux®. Flux captures the complexity of electromechanical equipment to optimize their performance, efficiency, dimensions, cost, or weight with precision, bringing better innovation and value products to end users. Flux® simulates magneto static, steady-state and transient conditions, along with electrical and thermal properties. Because of the tight integration between Activate® and Flux®, users can perform high-accuracy electromagnetic co-simulation or choose to run quicker simulations by leveraging look-up tables or functional mock-up units (FMUs).
CFD
In the hydraulic part of the valve, two aspects are important – flow and forces. Forces are generated by static pressure, but also by locally decreasing dynamic pressure (flow forces). The model is represented by a combination of hydraulics components and the results of simulation from the Altair CFDTM general-purpose Navier-Stokes solver.
Look-up tables are used for the flow and forces that represent the steady-state behavior. The flow is modeled and solved using fixed conditions, exploring several plunger positions and different flows. The results of those steady-state simulations are transferred to a look-up table, where the combined data can be examined to determine the mass flow and forces depending on pressure differences and plunger positions.
For a more accurate representation of the phenomenon, dynamic reduced-order models (ROMs) are then utilized to represent the solenoid valve’s transient fluid dynamics behavior.
Artificial Intelligence for Dynamic Reduced-order Model Generation
Reduced-order models are useful for incorporating detailed 3D simulation into a more computationally efficient 1D envi
ronment for system-level study. Simulation tools like Altair CFDTM and Altair Flux® allow for detailed investigations of time-variant non-linear systems, but because of long simulation runs, analysis is typically focused on a component or subsystem. In the case of a complete system simulation however, it is often sufficient to reduce component behavior to its interaction with the complete system, improving solver run time while still providing sufficiently accurate results.
Leveraging Altair’s romAI artificial intelligence tool, 3D simulations can be used as training data for generating dynamic ROMs. Only a few 3D simulation runs are required, as this approach requires less training data than traditional data-driven methods. romAI can work with any solver and produces highly accurate results when operating within the training space and is even stable and useful for extrapolation outside the space. The same machine learning technique can also be used for system identification purposes when starting from test data.
By leveraging romAI for the solenoid valve simulation, users get the best of both worlds – accuracy of 3D models with the speed of 1D models. This is achieved through a few simple steps.
- Perform transient 3D simulation – Choose the excitation so that the expected operating conditions of the ROM are covered.
- Extract the training data from the 3D simulation – Choose the input, output and state variables the ROM should represent. A small enough output time step should be selected to catch the system frequencies you want to capture. The input, output and state variables should then be stored for every time step into a CSV file.
- Run the machine learning module – Specify the number of hidden layers, neurons, etc., then use the built-in tools to examine convergence and accuracy. When satisfied, test romAI with the dedicated block available in Altair Activate®.
- Use the ROM in Activate for system simulation
romAI process for solenoid valve CFD simulation
romAI vs. CFD results – Solenoid valve hydraulic
Results of the AI-Augmented Multiphysics Analysis
Activate® proved to be an ideal integration platform for the multi-disciplinary system simulation of the solenoid valve, including its electromagnetic, fluid dynamics, and mechanical properties. The Activate® model can be used for both quick design studies and detailed dimensioning of the component system. romAI also helped to integrate the transient CFD with high speed while still providing sufficient accuracy.