Building for Safety and Security in Skyscrapers
A constant challenge for architects and structural designers is ensuring wind, weather, and seismic loads won’t create excessive vibrations on tall buildings that can unnerve occupants and cause structural damage. To mitigate these hazardous vibrations, engineers use tuned mass dampers (TMD), or dynamic damper technology.
Hermann Frahm first introduced the concept of tuned mass dampers in 1909 to reduce the rolling motion of ships at sea. Today, TMD technology is most commonly used in tall, narrow structures and bridges. Architects, engineers, and developers install these devices to prevent serious damage in high-rise buildings that experience vibrations from weather or ground-floor loads.
One of the most visible applications of TMD technology is in Taiwan’s Taipei 101 skyscraper. Thanks to its principles, Taipei 101 can move five feet in any direction, which decreases its sway by up to 40%. And big skyscrapers need big technology – Taipei 101’s monstrous steel tuned mass damper pendulum weighs an astonishing 728 tons. TMD technology is also common in high-rise-heavy cities like New York City and Dubai where tall towers loom over nearly every passerby.
But how do tuned mass dampers work? In essence, it suppresses vibration on the sides of a structure by connecting an auxiliary mass to the structure with an appropriate spring and vibrating it. Often, these are composed of three main parts: a moving mass, a pendulum or springs, and damping elements. The principle of the technology is to transfer the vibration energy of an object to a dynamic vibration absorber by adjusting the absorber to resonate at the same frequency as the building’s natural vibration.
With today’s high-powered simulation tools, it’s possible to virtually analyze the effects of these vibrational loads and how effective a tuned mass damper will be in decreasing those vibrations. This allows designers and engineers to optimize the system before the structure is built.
With Altair® OptiStruct®, engineers at Altair simulated how well a dynamic vibration absorber could suppress vibrations from an earthquake. Using a building model based on an OptiStruct sample model found in Figure 1, the team conducted a transient response analysis to study how a building’s vibrations change depending on the presence or absence of a tuned mass damper.
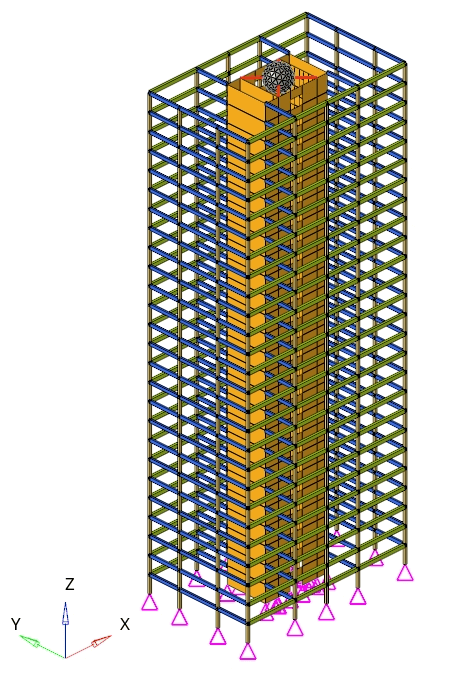
Since tuned mass dampers are designed to absorb the kinetic energy generated by a structure’s vibration, they work best when installed in an area within the building that has the largest vibrational amplitude. In this case, the amplitude of the upper part of the structure will be largest, so it’s most effective to install the tuned mass damper on the roof. In this model, as shown in Figure 2, the team placed a concentrated, 100-ton mass to the center of the top floor with a horizontal spring. Since the spring is equivalent to a rigid body in the vertical direction, it looks like a mass body placed on a hard floor without friction, held horizontally.
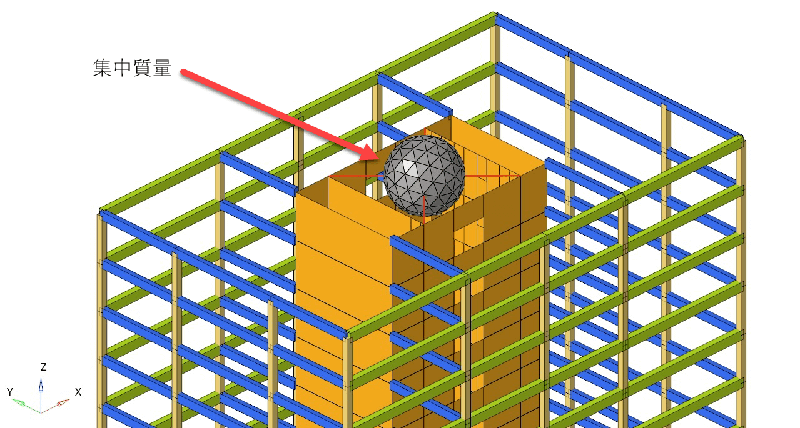
To see how buildings react to vibrations without TMD technology, the team performed a natural vibration analysis without a dynamic vibration absorber. Looking at the results, we see bending toward the building’s Y-axis occurred at 0.476Hz as the primary mode, as shown on the left side of Figure 3. The secondary mode was 0.559Hz due to X-axis bending, as shown on the right side of Figure 3. Next, the team had to determine spring constant so the dynamic damper would vibrate in the same direction at the same frequency.
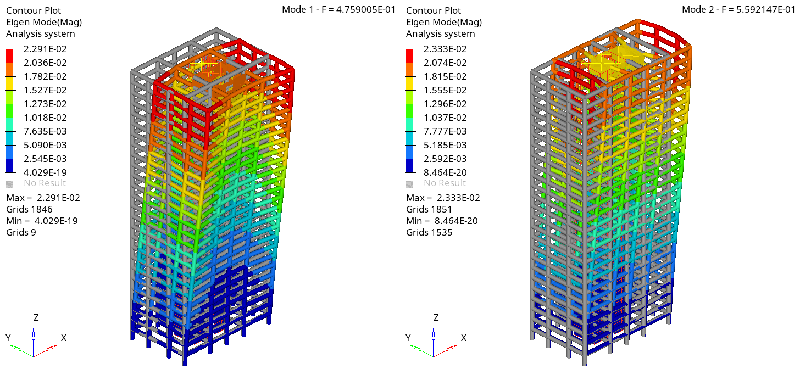
The team calculated the frequency of natural vibration using the following formula:
- f = 1 / (2π) √ (k / m) f: natural frequency k: spring constant m: mass
- Spring constant in the Y direction from f = 0.476Hz, m = 100ton k Y = 894.0KN / m
- Spring constant in the X direction from f = 0.559Hz, m = 100ton k X = 1,234.4KN / m
In this model, four springs supported the mass, so the team determined each spring needed a spring constant of 1/4 of the above.
As an input condition to calculate the impact load, the ground where the building is fixed was moved 1 meter along the Y-axis for the first 0.1 seconds, then returned to the original position at the next 0.1 seconds and held there. In the simulation shown in Figure 4, the left side was simulated without a tuned mass damper, and the right side with one. The team exaggerated the actual amplitude by a multitude of five so it was easier to visualize the deformation.
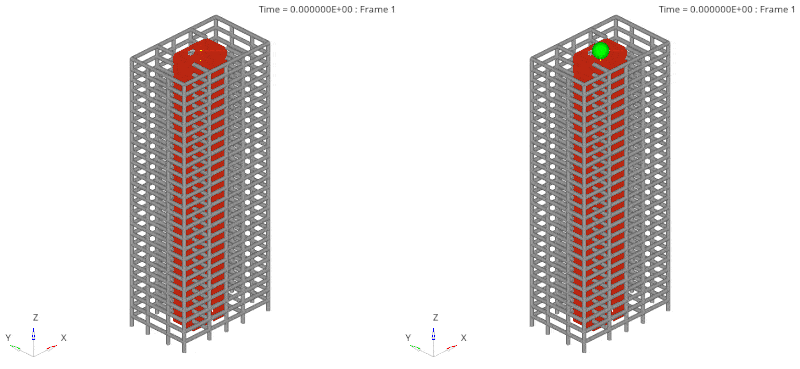
Figure 5 displays a graph that compares the time history of the Y-axis displacement of the top of the building with and without a tuned mass damper.
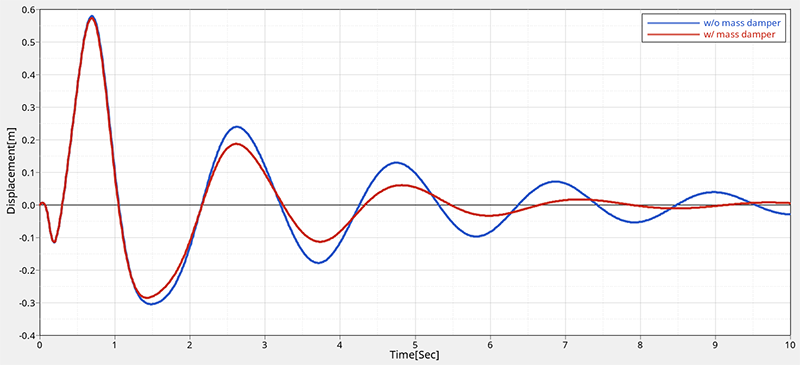
The blue line represents the building without a dynamic damper, and red represents the building with one. As we can see, the initial amplitude was almost the same – but after that, the effect of the dynamic vibration absorber appeared, and it proved its worth in a very short time.
The transfer of kinetic energy to the tuned mass damper reduced the overall structural vibration, so there was almost no effect immediately after the input was applied. Through the team’s OptiStruct analysis, they could see exactly how TMD technology suppresses the vibrational impacts of wind and weather loads. With OptiStruct, engineers can streamline their workflows using a single model, and can analyze multiple strength and vibrational attributes during similar studies.
The architecture, engineering, and construction (AEC) industry requires accurate modeling and design tools to ensure projects meet complex structural project needs – Altair’s single-platform suite of design and optimization tools supports designers and engineers and gets the job done. Users can easily study real-world multiphysics examples in OptiStruct since the technology provides solutions for linear and nonlinear analyses across statics and dynamics, vibrations, acoustics, fatigue, heat transfer, and multiphysics disciplines. Additional S-FRAME solutions enable engineers to further explore seismic structural analysis and ensure their projects and designs meet requirements specific to geographic regions and local seismic design codes.
To learn more, visit https://www.altair.com/optistruct/.