Digital Debunking: Muscle Car Mods
As we enter fall and get ready for winter, many of us gearheads who have been socially distancing behind the wheel of a classic or performance car will have to start socially distancing in the garage instead. One popular accessory for our performance-oriented pursuits is frame/chassis bracing. Adding a brace to your vehicle is a relatively straightforward and inexpensive modification project, and they come in many forms such as strut tower braces and subframe braces (they’re also definitely cheaper than orthodontic braces!). The idea is that the stiffer the chassis, the more control you have over the tuning of the suspension. Additionally, with a stiffer chassis, you could theoretically expect to better handle higher loads from bigger, stickier tires. If you are trying to launch off the line or clip the apex of a corner, a stiffer chassis is a good thing. In this post we will quantify the real value of a few different braces on a virtual pony car. Are they just bling or are they functional?
Three different types of braces were evaluated: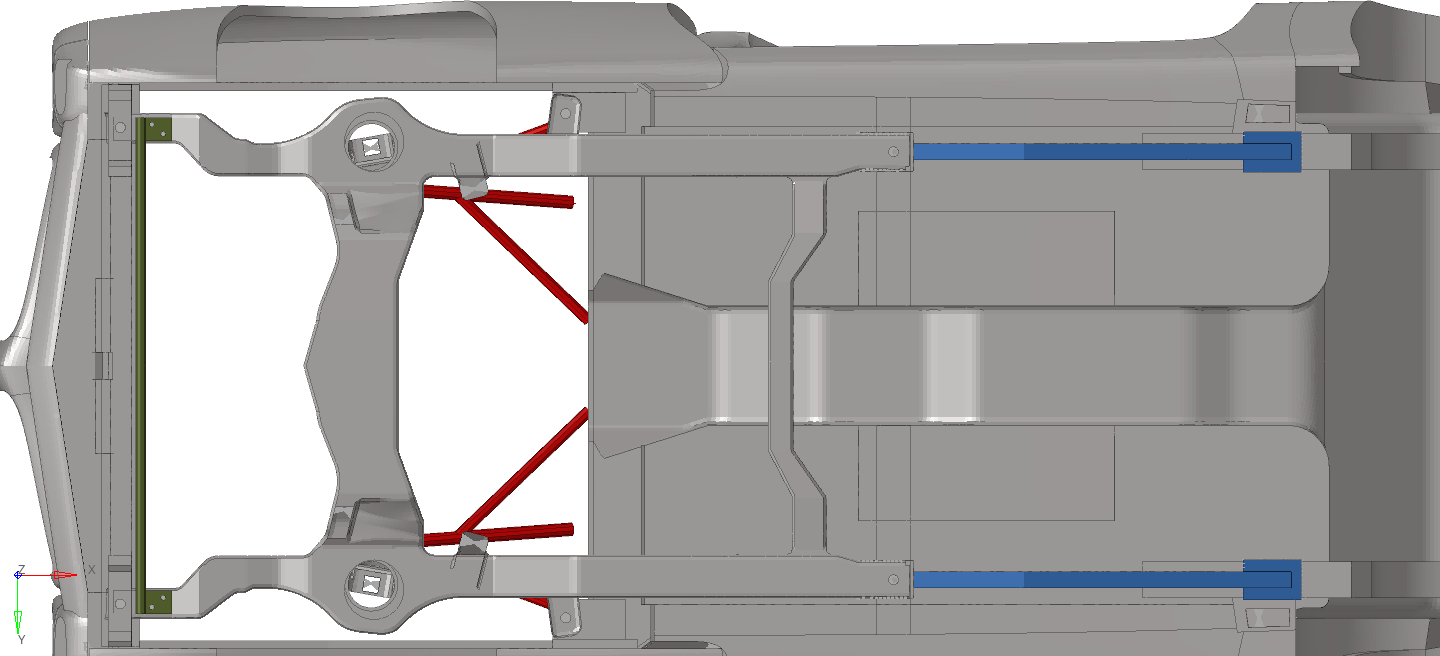
Cowl and subframe connector bracing
[embed]https://altair-2.wistia.com/medias/mnqw74rjn8[/embed]
[embed]https://altair-2.wistia.com/medias/u73ehqlsa1[/embed]
Once baseline studies without any bracing were run, HyperWorks was used in conjunction with HyperStudy to run Design of Experiments (DoE) optimizations to examine ideal gauges for the different braces and understand sensitivity of the stiffness and modal responses to the brace gauge variables.
Static and modal torsional stiffness and bending simulations
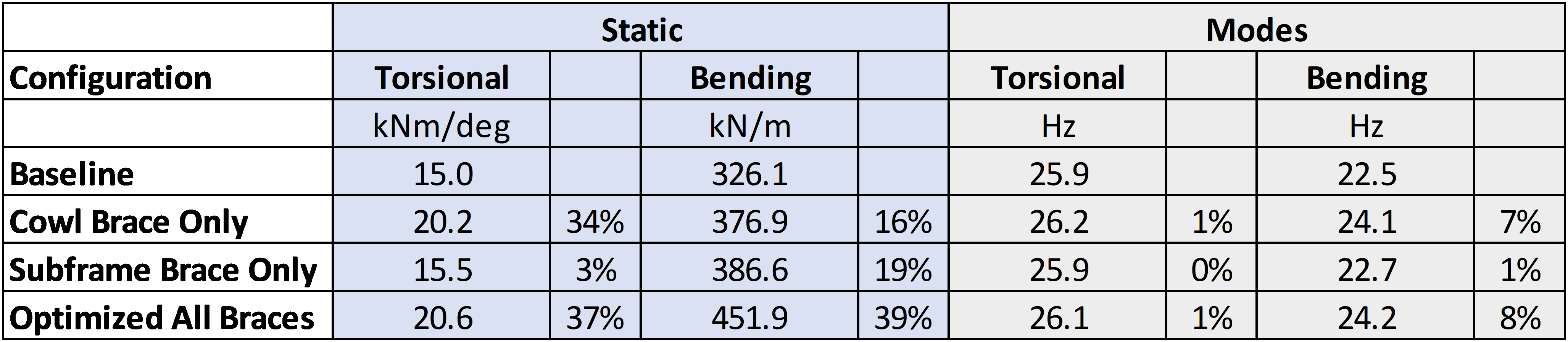
Looking at the change in stiffness and mode values show the addition of the brace yields positive results. A 2 hertz (Hz) bump in the first bending mode is significant and is an indicator that we are adding efficient mass. In addition, it is beneficial to install both the cowl and subframe brace to get the biggest bump in static bending stiffness, an increase from 19% to 39% static bending stiffness.
The Pareto chart from the gauge DOE shows which brace thickness changes had the largest impact. For static bending, that was the subframe connector, and for torsional stiffness and modes, the cowl brace was dominant.
Stress plots for static twist and bending
Comparing stress plots of static twist and bending runs show the change in load path due to the brace additions. The cowl brace adds substantial stiffness, however, the local connections on the cowl brace show stress increases from 45 to 251 Megapascals (MPa) when only the cowl brace is installed. By using this in conjunction with the subframe brace, stress drops to 225 MPa. On top of the substantial increased stiffness achieved by using both cowl and subframe braces, the combination also distributes stress more efficiently, increasing the fatigue life of the installation.
Static stress loading results
Check out a more detailed summary of the results below:
[video width="1920" height="1080" mp4="/videos/default-source/news-videos/DetailedResults_StaticPlusMoviesInline.mp4"][/video]
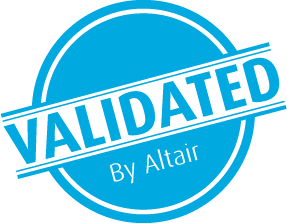
Three different types of braces were evaluated:
- Cowl/shock tower bracing (Red): Meant to triangulate subframe to main body
- Subframe connector bracing (Blue): Connects front subframe to rear frame essentially creating a full frame
- Frame lateral connector (Green): Meant to improve reaction to cornering loads. Included as a control to compare sensitivity
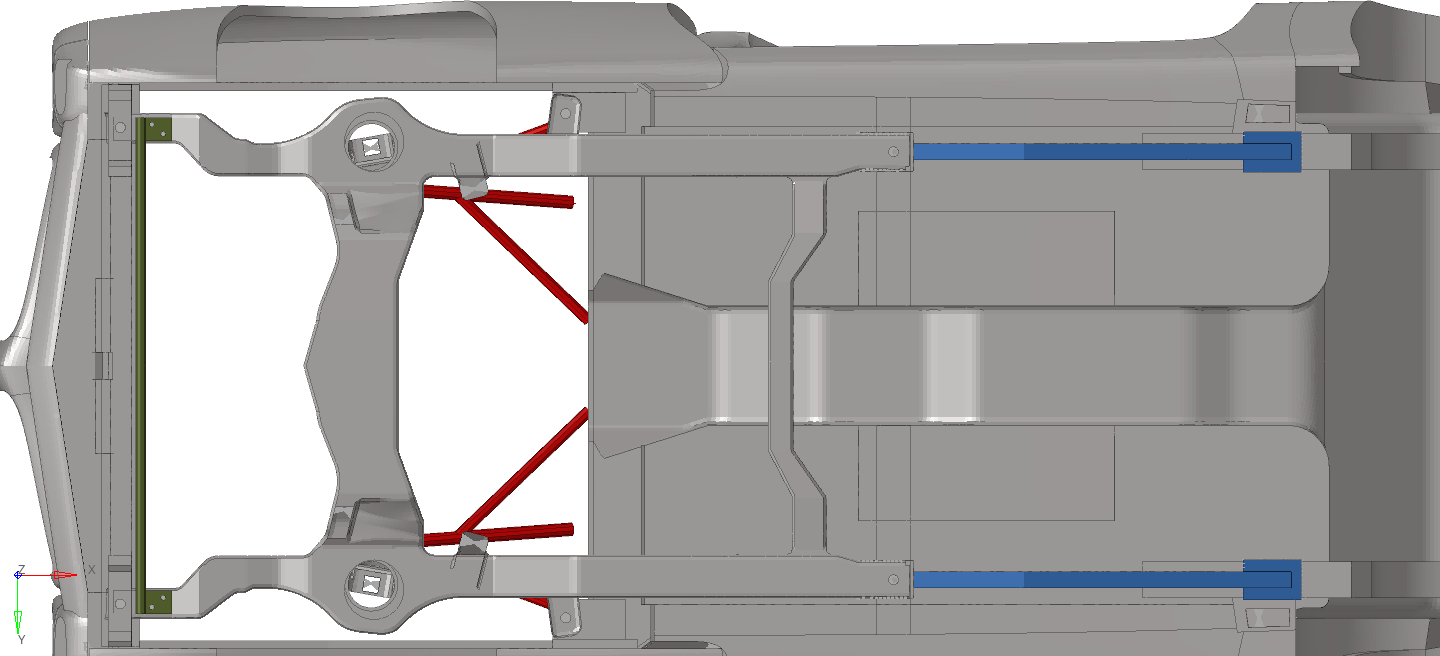
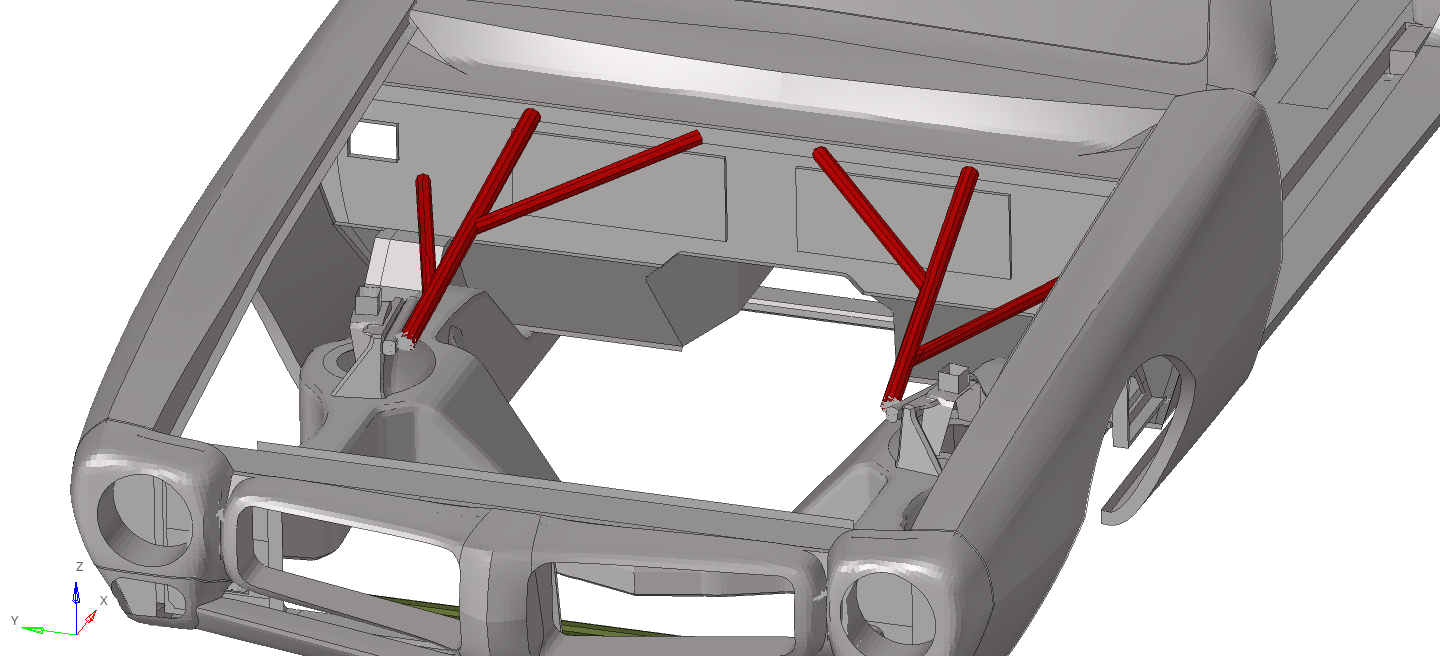
Creating the Geometry
While learning to use the geometry tools within Altair InspireTM, specifically Polynurbs, it seemed like a great way to model the swoopy shapes of a muscle car’s exterior without a lot of the burden of typical parametric CAD surfacing. Inspire is made for defeaturing existing CAD to prep for optimization, create early geometry for concept analysis, and to generate solid geometry from optimization outputs. In this case, we don’t want or need Class A surfaces for tooling, just a representative shape that’s close enough to make A-to-B comparisons on design concepts. Once the basic surfaces were generated, the logical next step was to run some analysis to see what effect the braces would have on the chassis stiffness.[embed]https://altair-2.wistia.com/medias/mnqw74rjn8[/embed]
Simulating and Optimizing Chassis Stiffness
Once the concept CAD was generated, Altair HyperWorksTM was used to set up the analysis; in this case, twisting and bending analysis on a test rig and a Free-Free modal analysis. These are typical benchmarks used to compare across designs in the automotive industry. Given the conceptual nature of the model, it provided a relatively complex, but less than perfect CAD set to test some of HyperWorks’ new workflows.[embed]https://altair-2.wistia.com/medias/u73ehqlsa1[/embed]
Once baseline studies without any bracing were run, HyperWorks was used in conjunction with HyperStudy to run Design of Experiments (DoE) optimizations to examine ideal gauges for the different braces and understand sensitivity of the stiffness and modal responses to the brace gauge variables.
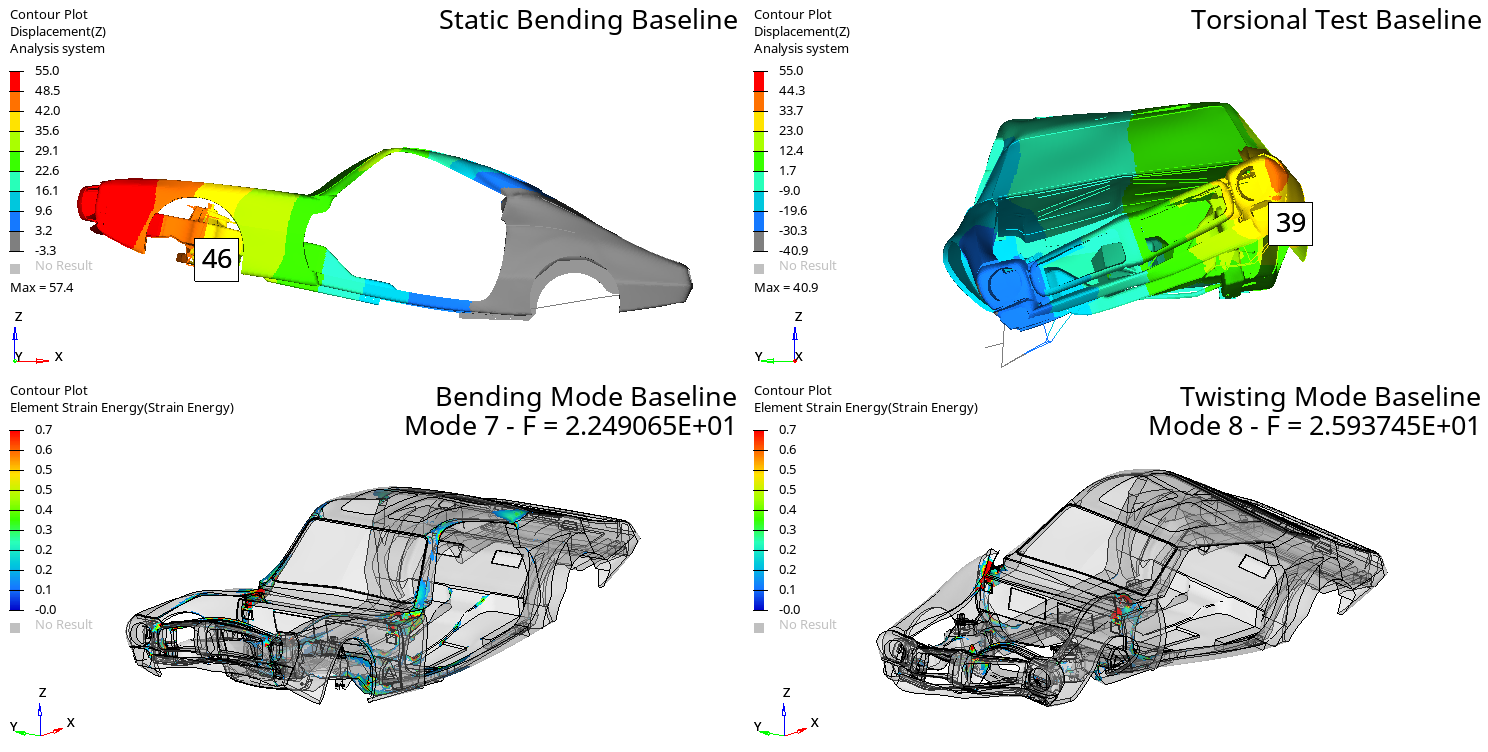
The Results
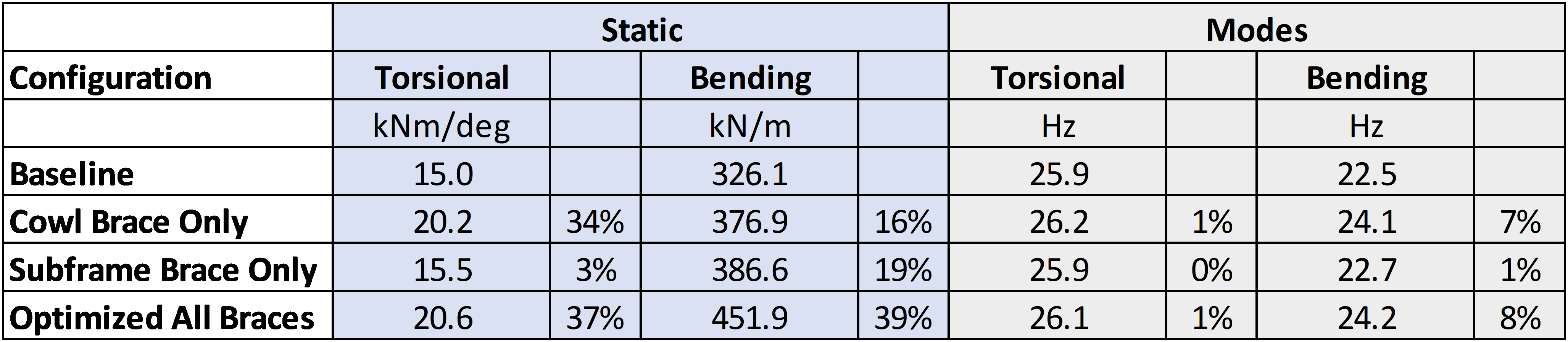
Looking at the change in stiffness and mode values show the addition of the brace yields positive results. A 2 hertz (Hz) bump in the first bending mode is significant and is an indicator that we are adding efficient mass. In addition, it is beneficial to install both the cowl and subframe brace to get the biggest bump in static bending stiffness, an increase from 19% to 39% static bending stiffness.
The Pareto chart from the gauge DOE shows which brace thickness changes had the largest impact. For static bending, that was the subframe connector, and for torsional stiffness and modes, the cowl brace was dominant.
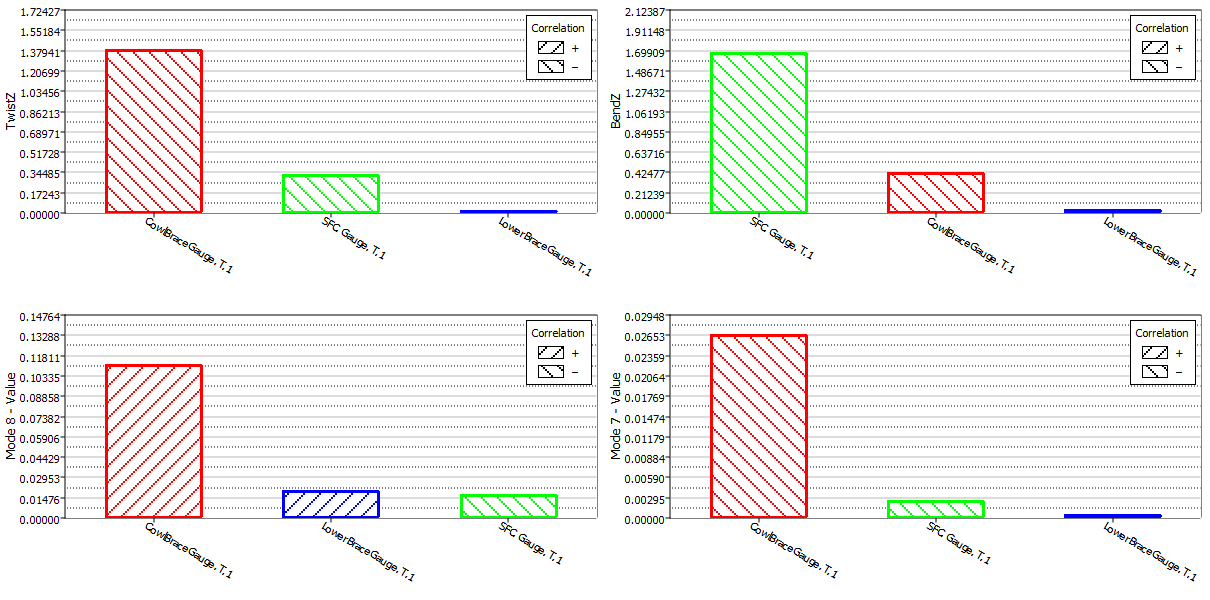
Comparing stress plots of static twist and bending runs show the change in load path due to the brace additions. The cowl brace adds substantial stiffness, however, the local connections on the cowl brace show stress increases from 45 to 251 Megapascals (MPa) when only the cowl brace is installed. By using this in conjunction with the subframe brace, stress drops to 225 MPa. On top of the substantial increased stiffness achieved by using both cowl and subframe braces, the combination also distributes stress more efficiently, increasing the fatigue life of the installation.
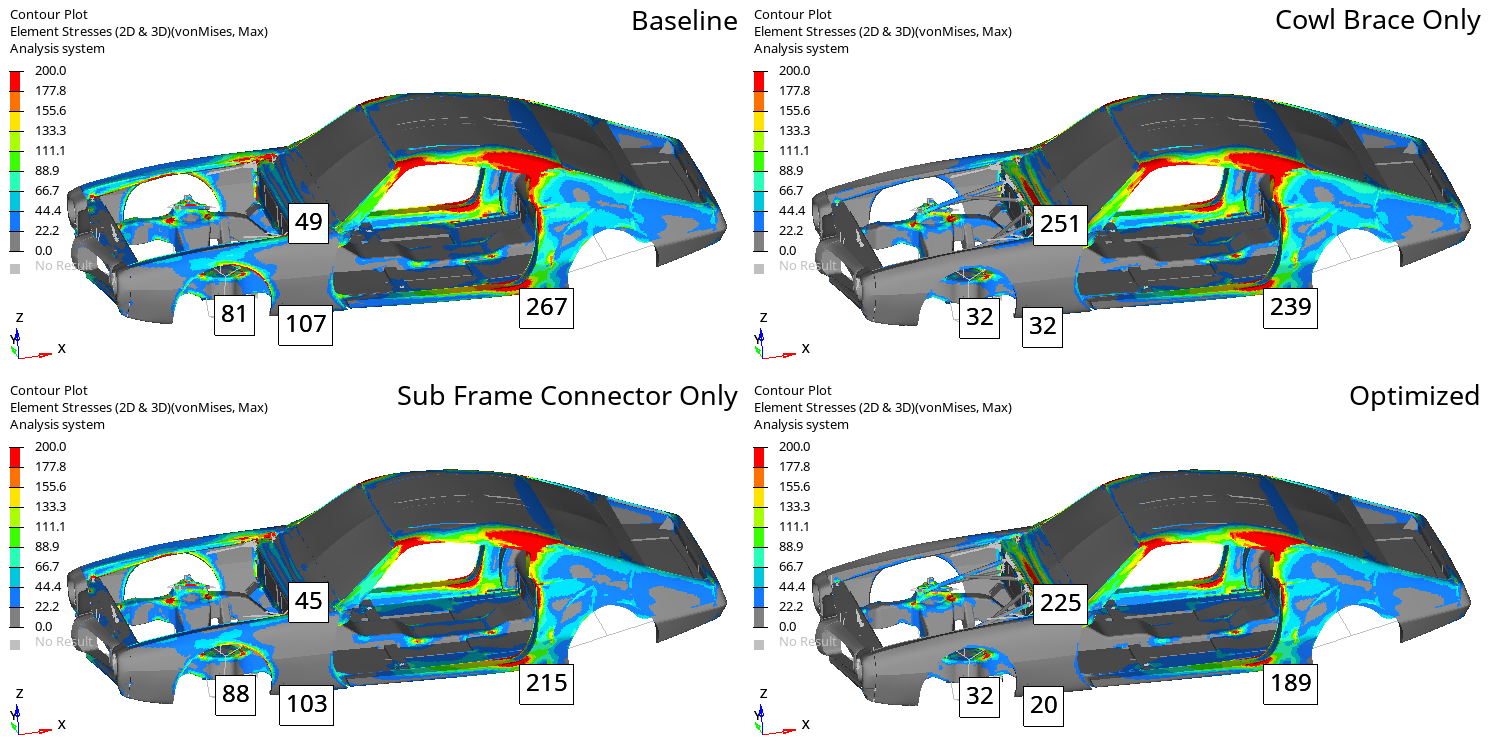
Conclusion: Bracing for Performance
Considering they are relatively inexpensive and unobtrusive to install, there is a definite improvement in performance with the addition of the cowl and subframe brace. The lower front brace could be beneficial for cornering, but sway bar loads for basics bending and stiffness of the chassis show minimal benefit. Without any hesitation, we can say these braces are not just bling; they provide real performance enhancements. Plus, they are totally legal, depending on your motorsport sanctioning body of course!Check out a more detailed summary of the results below:
[video width="1920" height="1080" mp4="/videos/default-source/news-videos/DetailedResults_StaticPlusMoviesInline.mp4"][/video]
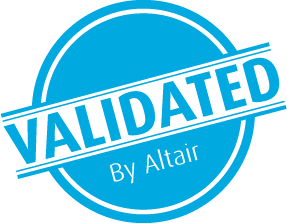