Evaluating Tire Design and Performance of Agricultural Machinery for Soil Interaction Using Altair EDEM™
Guest post by Heron Dionisio and Anderson Calhabeu, Brometeon Tyre Group
The use of agricultural machinery such as tractors, grain harvesters and trucks are often attached to problems with their impact on the soil and, consequently, on the cultivation of new crops. In that theme, the tire plays an important role since it is the component responsible for providing enough traction to the system and for preventing the soil from becoming damaged or over compacted.
For many years, Prometeon Tyre Group has been using the finite element method (FEM) to develop and test truck, bus, agricultural, and off-road tires. As part of a recent collaboration between Prometeon and Altair, we were able to simulate tire-soil interaction in deformable terrain where the soft soil was modelled as a bed of particles in EDEM, the market-leading discrete element method (DEM) software.
EDEM provides a wide variety of options to set up a model enabling the evaluation of tire design and performance regarding different characteristics like traction and self-cleaning capabilities, even with the tire being a rigid geometry.
One key aspect of simulating tire operation is to model realistically its interaction with the soil. The tire footprint is the portion of the tire’s tread that makes contact with the soil surface. Therefore, it is necessary to have its true representation in the virtual environment.
Prometeon worked with Altair to develop a representative soil material model, initially based on a material model taken from the Generic EDEM Material Model database, taking into consideration tire-soil normal pressure-sinkage response and particle scale for resolving tire tread patterns. Consequently, the simulation of a tire loaded against a sandy soil was set up in EDEM in order to reproduce a laboratory test. The tire footprint geometry was scanned and rebuilt in the computer. We also measured the penetration of the tire into the sand as the vertical force was applied.
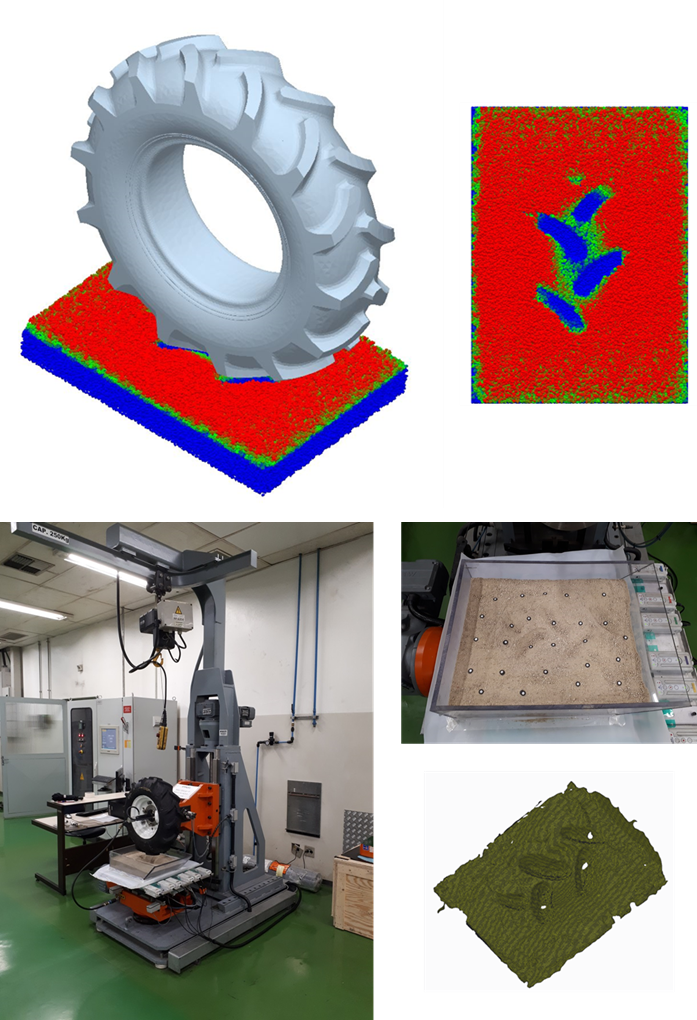
The discrete element model showed good correlation to the experimental results after the calibration of material properties of the soil particles. Despite the difficulty of measuring the footprint dimensions correctly, differences between the real and the virtual model were approximately 3-4 mm.
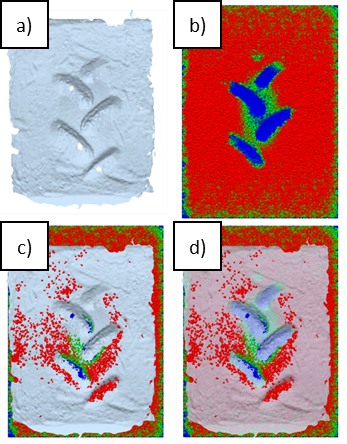
Once the soil material was calibrated as well as its interaction with the tire, we could move forward and work with dynamic analyses. These can be used to observe the effects of a rolling tire on a soil and how these effects change according to the tire work conditions like its vertical load, longitudinal speed and so on.
Tire simulation requires the application of kinematic boundary conditions (displacements and velocities), forces and moments at the same time. Originally, EDEM did not allow this kind of set up. For this reason, the Altair team developed two EDEM Coupling Interface applications for applying fixed angular velocity and fixed torque called “RPM Fixed” and “Torque Fixed” respectively. The team has subsequently implemented torque and force driven kinematics inside the main EDEM software.
RPM Fixed solves the issue regarding the coupling between rotational and translational motions: now, if the user applies a rotational motion to the tire geometry, it begins to move forward because of the friction that exists in the contact zone with the soil.
Both plugins also improved EDEM Dynamic Domain capabilities as it now follows tire geometry motion automatically even when forces and moments are applied. The EDEM Dynamic Domain is a very powerful feature that can save time and hence computational costs.
With an increasing number of particles, the computational cost of DEM increases. By using the EDEM Dynamic Domain it is possible to model a fraction of the total particles in a simulation by only simulating those bound inside the Dynamic Domain geometry leading to time saved due to an increase in simulation performance.
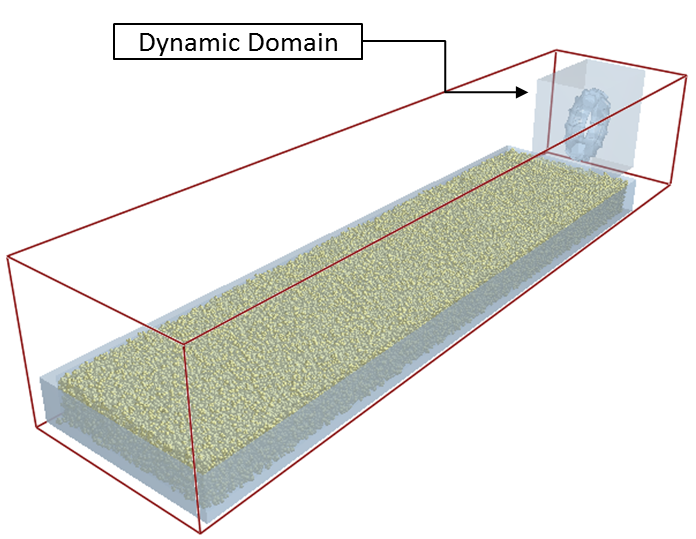
Using these features, EDEM enables the user to do a wide range of analyses such as the evaluation of the tire slip or even to estimate the impact caused by the tire in the soil by verifying the compression forces acting on the soil particles.
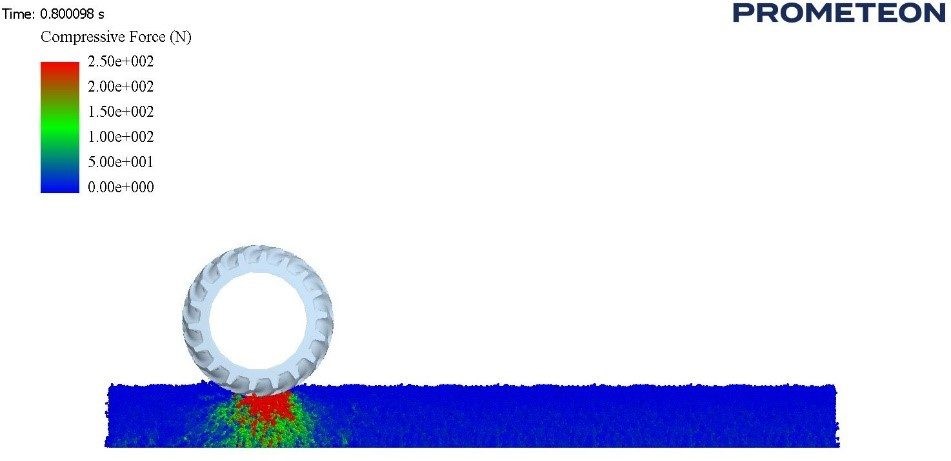
About the authors
Heron Dionisio is a research and development engineer at Prometeon Tyre Group in Brazil where he develops industrial tires and their manufacturing processes using computer simulation tools like FEA and computational fluid dynamics (CFD).
Anderson Calhabeu is the innovation coordinator at Prometeon Tyre Group in Brazil where he develops open innovation, including new materials and computational simulation for tires and industrial processes.
A note from the Altair Team
"It has been a privilege to be able to work so closely with the Prometeon team on this exciting new area for EDEM. Tire-soil interaction is a key phenomenon in determining the performance of many off-highway applications. By collaborating with the Prometeon team we have been able to understand more about how tire manufacturers design and test their products, and learn how our simulation technology can be evolved to better support their needs. This is an area we will continue to expand our capabilities and we thank Prometeon for all their work with us to date and continued support."
David Curry, principal engineer, Altair EDEM Business Development