Featured Client: Simulations Impacting Life Changing Products
Allan F. Mogensen, aka “Mogy”, Industrial Engineer and proponent of work simplification coined the term “Work Smarter…Not Harder” in the early ‘30s, forever changing the way we think about doing things.
Oh I know. There is a plethora of opinions and interpretations about the working hard vs. working smart dichotomy. There is however, no doubt that this principle - applied in its simplest sense - is completely meaningful in the role technology has played in simplifying many a task in our everyday lives, introducing an amazing level of efficiency to their performance. In fact technological solutions so subtly permeate just about every facet of our routine lives, making it so much easier than yesteryears, that we don't even think about it as we go about our business.
The medical field is an excellent example. Groundbreaking advancements have dramatically improved the quality of services, medical procedures, equipment and efficiency in administration for health care. Computational modeling and simulation, is on the verge of revolutionizing the field of medical devices. Modeling techniques allow computer models to eliminate bad ideas and refine the good ones long before they leave the drawing board. The computer models essentially anticipate the performance of cutting-edge medical devices for usage in various patient groups, ensuring that they are safe, effective, and can reach physicians and patients as quickly as possible.
Our featured client this month is NuVasive Inc., Based in San Diego, California, NuVasive is a medical device company focused on the design, development and marketing of products for the surgical treatment of spine disorders. Ranking no. 3 in the US spine industry, they specialize in minimally disruptive surgical procedures and are the pioneers of lateral access spine surgery with eXtreme Lateral Interbody Fusion (XLIF®). Through innovative technological advancements, NuVasive has successfully progressed major spine surgery to where many patients have experienced extraordinary results—they are often walking the same day of surgery, experiencing reduced blood loss, spending less time in the hospital, and being able to return to to work within four to six weeks (versus the traditional six months).
Correlation of Expensive Physical Testing
Computer modeling within the medical device industry is advantageous because it eliminates specimen variability, reduces testing time, and allows for the evaluation of designs under the same anatomical conditions. The anatomic geometry needed to be obtained from a CT scan and develop a finite element model that could evaluate the biomechanical stability of different interbody cage footprints that is typically performed using cadaveric testing. Since bone geometry is unique to each individual, and bones are not symmetric, a manual hexahedral (HEXA) meshing approach needed to be established in order to build models with a repeatable process.
Pre-processing with HyperMesh®
The vertebral bodies of the lumbar spine needed to be hex meshed and seamlessly connected to the posterior region using tetra elements. With the solid meshing capabilities of HyperMesh and its powerful morphing tool they were able to quickly model the lumbar, while satisfying their analysis requirements. “HyperMesh allowed me to quickly create high quality models that can evaluate the biomechanics of the human lumbar spine”, said Jeff Harris, Senior Engineer, Computational Biomechanics at NuVasive, Inc.
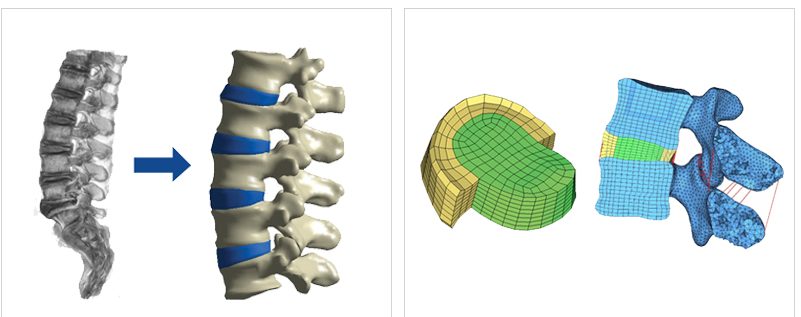
The manual HEXA meshing approach process included the use of HyperMorph module to project elements onto geometry in exact areas. In addition, the geometry needed to be partitioned specifically to flow the HEXA elements together so as not to create mismatched element sizes and aspect ratios. Although this process was created from standard lines, project, and ruled meshing tools, it took advantage of HyperMorph functionalities where they could change the mesh patterns to match any new shape. This was a customized process using the existing tools in HyperMesh to fit the customer’s needs in this unique application.
Lead Time reduction using HM for Complex Meshing
NuVasive’s use of HyperMesh to HEXA mesh human vertebrae is now routinely used within their structural simulation department.
They are currently using computational modeling using HyperMesh to anticipate the performance of medical devices when they are used in various patient groups. Typical run times of simulation have been reduced from almost 12 hours to only 4 hours.
By providing these new finite element analysis (FEA) models to device engineers, they are ensuring cutting-edge devices are safe and effective, and that they can reach the physicians and patients as quickly as possible.