How the Combination of IoT and Simulation Play a Role in Industrial Machinery Design
Today’s engineers face unprecedented challenges when designing industrial machinery. There is a growing expectation that new designs will increase cycle speed and improve yields, while delivering and commissioning these machines faster than ever before. The primary goal of any machine building project is to achieve perfectly running production of high-quality products. Complexity is rising dramatically in traditional mechanical and electrical design domains and software plays an increasingly important role as industry sees the value of building accurate virtual prototypes and streaming data from connected equipment, ensuring a seamless production earlier in the development process to help assess and improve product profitability.
Combining IoT with Simulation
Technology such as Internet of Things (IoT) is being harnessed in this sector, making products smart and gathering previously untapped data to inform future operations and optimization efforts. Having access to this data allows manufacturers to closely monitor their equipment and machinery, proactively servicing those systems to avoid or minimize downtime.
Implementing an IoT strategy should be carefully thought out, however. One approach to making a product IoT-ready is to apply many sensors to the equipment without much foresight about sensor placement or what to do with the newly acquired data. As a result, companies become overwhelmed with the amount of data produced making it difficult to organize effectively, leading to inaction or stagnation.
To avoid this, a progressive alternative involves simulating the operation of machinery while taking measurements from virtual sensors. This allows engineers to determine the correct configuration for proactive maintenance, identify the type of sensors to use and where to place them, and reduce the number of sensors, if necessary. Additionally, this approach makes it possible to understand what specific indicators should be monitored and why. There are also instances in which placing sensors onto equipment is simply not feasible. If parameters in a manufacturing process or the operation of a plant cannot be measured or sensed, simulation can provide an alternative.
For example, the exact temperature distribution in a brake can be predicted from rotations per minute (RPM) and braking behavior, whereas a temperature sensor in the brake disc would be a complicated undertaking. In this way, plants or manufacturing processes can be mapped as a simulation and conditioned with real input variables, thus providing deeper insights into the process as "virtual sensors."
Building accurate prototypes of industrial machinery and associated systems requires dedicated software that joins development disciplines with purpose driven simulation. System development tools such as Altair® Activate® connect with virtual commissioning environments through the functional mockup interface (FMI) standard, making it possible to combine the control sequence with the actual behavior of the machine, ultimately allowing virtual commissioning and reducing the time investments at the customer facility.
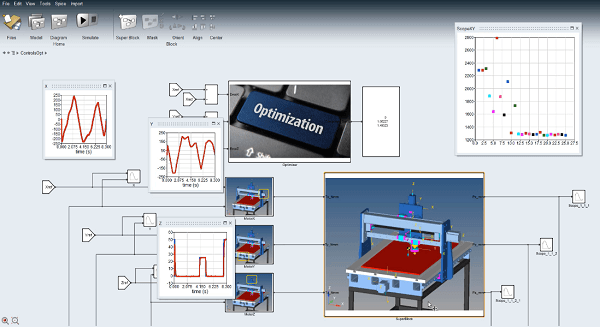
Understanding the detailed behavior of machine elements is also necessary to reduce unwanted vibration and perform topology optimization. With Altair® MotionSolve™, a multi-body simulation tool, process accuracy can be achieved faster, improving the productivity of handling systems, machines, and the production line. By assessing realistic motion-induced loads and environmental effects, engineers and designers can be confident that their products, when made and operated, will perform reliably, meet durability requirements, and not vibrate excessively or fail from fatigue. For a more detailed explanation of how simulation can be used to meet machine builders’ needs, read this article.
Predicting Remaining Useful Life
When pairing data from either physical or virtual sensors with technologies such as artificial intelligence (AI) and machine learning (ML), companies can analyze the resulting data and identify anomalies that correlate to events manufacturers want to avoid. Tools such as Altair® SmartWorks™ enable manufacturers to harness the full power of AI, analytics, and IoT with Altair’s next generation, cloud-native enterprise data ecosystem.
ML and stream processing technology are powerful solutions for remaining useful life (RUL) analysis, for example. Manufactures can use the large amounts of data produced by sensors combined with human inspections of finished pieces to train ML algorithms. The ML tools can then proactively alert operators when a tool is approaching its end of life, allowing manufacturers to schedule the replacement for a convenient time. Stream processing algorithms can also process all the sensor data being generated by any number of production machines, make on-the-fly comparisons with historical data, and increase the accuracy of ML algorithms.
Incorporating this technology into industrial machinery design allows manufacturers to gain a better understanding of data produced from either physical or virtual sensors, making a closed engineering loop approach possible. To learn more about predicting remaining useful life, read this flyer.
Data Visualization
Altair’s data visualization tools use stream processing and visualization of real-time and time series data. This data can be used to create customized real-time dashboards to track KPIs and chart trends and anomalies. The data can also feed into Altair® Knowledge Studio®, which uses ML and AI to enable data exploration and predicative analytics on the field data. Ultimately companies don’t just need better engineering data - they need ways to access the collective insights of the entire development process, synthesize mechatronic models, requirements analytics, and sensor data from the field, all to drive business decision-making.
The world of industrial machinery design is complex. To achieve the best possible design, multiple design and data processing tools need to be used. Altair’s integrated product and process simulation tools allow a holistic view of the system from different roles to ensure perfectly running production. When combined with our dynamic IoT toolset, effective industrial machine designs can be realized, saving time and money for manufacturers.
Click below to read more about digital transformation for the industrial machinery sector.
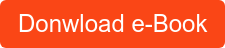