Manufacturers Need to See Operations at the Pace of Innovation
More than 100 years after Henry Ford first adopted assembly line production, the pace of manufacturing continues to accelerate. For example, one of India’s leading motorcycle brands now takes just 18 seconds to roll out each new bike.
In a competitive global market, the search for efficiency has to be relentless. But there’s a flipside to the sheer speed of modern manufacturing. If something goes wrong, the costs can multiply just as fast. In terms of rectifying problems such as machine downtime, production bottlenecks, and product defects, it really is a case of every second counts.
Imagine a build quality issue going undetected for just 24 hours in the aforementioned motorcycle factory. That’s nearly 25,000 less-than-perfect bikes on their way to customers. In turn, that means nearly 25,000 prospective warranty claims. And the long-term damage to brand reputation could well prove even more costly.
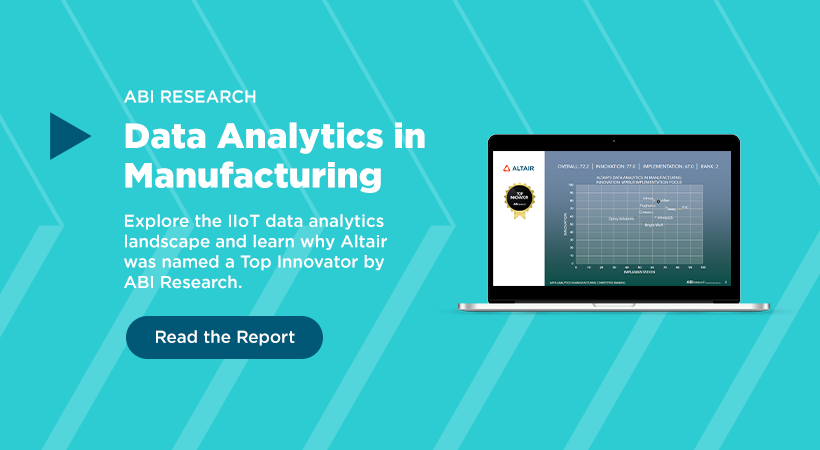
Prior to the emergence of smart manufacturing, even the most sophisticated approaches to dealing with such challenges amounted to little more than firefighting. So, when a warranty claim is lodged, it’s a case of laboriously working backwards to trace the source of the problem. Dealing with production inefficiencies is similarly retrospective. Historical data from cells, systems, and processes is analyzed manually to identify root causes. And planned maintenance schedules are routinely based around what’s happened in the past, not what’s happening now.
That’s why smart manufacturing’s ability to identify and respond to issues as they happen is a game changer. In our last feature article, we highlighted the need for a multi-stage approach to converting data into actionable insight. But it’s equally important for that insight to be delivered in real-time.
At Altair, we understand this. Altair Panopticon™, our stream processing and visualization solution for real-time and time series data, is deployed in numerous trading floor applications. That’s an environment in which business really is measured in fractions of seconds. Now, the benefits of Panopticon are increasingly being recognized by the manufacturing sector as well.
What can Panopticon, and our other smart manufacturing solutions, deliver? Essentially, it’s about harnessing machine learning (ML) and artificial intelligence (AI) to spot anomalies in data (both historic and real-time) and link them to the outcomes impacting quality and productivity. But this is not autonomous control. As we also stressed in our last article, successful smart manufacturing strategies are shaped by domain expertise. They are designed to support, not replace, the people who understand the shopfloor.
That’s why good data visualization is another vital asset. In the age of the citizen data scientist, analytics needs to be accessible and intuitive. Democratization is at the heart of our mission, and is reflected in solutions that are highly customizable to individual requirements. Without any need for coding, dashboards can be created that elegantly deliver information to the people who best know how to apply it.
In a world in which motorbikes can be made faster than a loaf of bread, manufacturers need to keep up with the pace of innovation. Written by Chad Jackson, chief analyst and researcher for Lifecycle Insights, our new smart manufacturing e-book offers expert guidance on improving asset uptime, reducing warranty costs, and increasing manufacturing throughput. To download your complimentary copy, click here.
In a competitive global market, the search for efficiency has to be relentless. But there’s a flipside to the sheer speed of modern manufacturing. If something goes wrong, the costs can multiply just as fast. In terms of rectifying problems such as machine downtime, production bottlenecks, and product defects, it really is a case of every second counts.
Imagine a build quality issue going undetected for just 24 hours in the aforementioned motorcycle factory. That’s nearly 25,000 less-than-perfect bikes on their way to customers. In turn, that means nearly 25,000 prospective warranty claims. And the long-term damage to brand reputation could well prove even more costly.
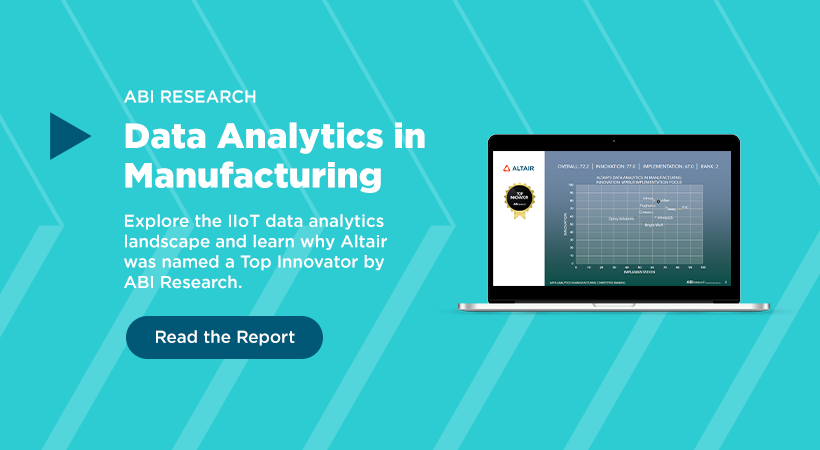
Prior to the emergence of smart manufacturing, even the most sophisticated approaches to dealing with such challenges amounted to little more than firefighting. So, when a warranty claim is lodged, it’s a case of laboriously working backwards to trace the source of the problem. Dealing with production inefficiencies is similarly retrospective. Historical data from cells, systems, and processes is analyzed manually to identify root causes. And planned maintenance schedules are routinely based around what’s happened in the past, not what’s happening now.
That’s why smart manufacturing’s ability to identify and respond to issues as they happen is a game changer. In our last feature article, we highlighted the need for a multi-stage approach to converting data into actionable insight. But it’s equally important for that insight to be delivered in real-time.
At Altair, we understand this. Altair Panopticon™, our stream processing and visualization solution for real-time and time series data, is deployed in numerous trading floor applications. That’s an environment in which business really is measured in fractions of seconds. Now, the benefits of Panopticon are increasingly being recognized by the manufacturing sector as well.
What can Panopticon, and our other smart manufacturing solutions, deliver? Essentially, it’s about harnessing machine learning (ML) and artificial intelligence (AI) to spot anomalies in data (both historic and real-time) and link them to the outcomes impacting quality and productivity. But this is not autonomous control. As we also stressed in our last article, successful smart manufacturing strategies are shaped by domain expertise. They are designed to support, not replace, the people who understand the shopfloor.
That’s why good data visualization is another vital asset. In the age of the citizen data scientist, analytics needs to be accessible and intuitive. Democratization is at the heart of our mission, and is reflected in solutions that are highly customizable to individual requirements. Without any need for coding, dashboards can be created that elegantly deliver information to the people who best know how to apply it.
In a world in which motorbikes can be made faster than a loaf of bread, manufacturers need to keep up with the pace of innovation. Written by Chad Jackson, chief analyst and researcher for Lifecycle Insights, our new smart manufacturing e-book offers expert guidance on improving asset uptime, reducing warranty costs, and increasing manufacturing throughput. To download your complimentary copy, click here.