New Altair SimSolid solution settings for thin walled solids
Altair SimSolid uses Solution settings to control analysis accuracy. These are applied either a globally to the full assembly or locally to individual parts. Read on to find out about our new Solution setting for thin walled solids.
The second solution quality level is Detailed. This will provide four adaptive solution passes and also has additional solver logic to refine stresses more completely. A best practice is to use this setting on local parts where additional stress detail is desired.
The third solution quality level is Custom. This is an expert mode that allows individual control of all solution settings. This should only be used for parts with unusual characteristics or when fine degree of control is desired.
Individual controls include:
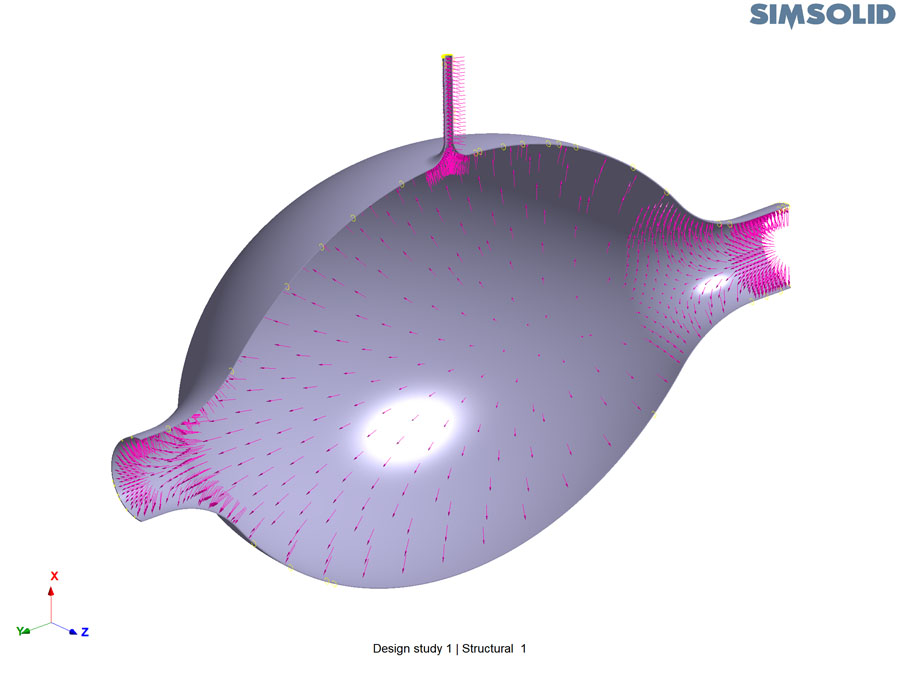
This is a challenging problem. The geometry is very thin and doubly curved. In traditional FEA, this is typically solved using shell elements. Shell elements are complex to define. In addition to the usual meshing tasks, the user must create a mid-surface from the solid, the shell elements must be oriented correctly and locally thicknesses applied. In Altair SimSolid all that is required is local solution settings.
First, here is the problem solved with standard settings.
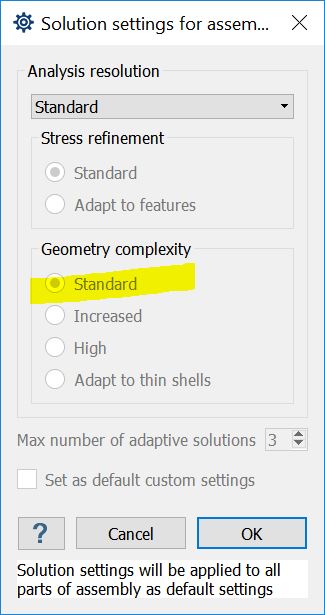
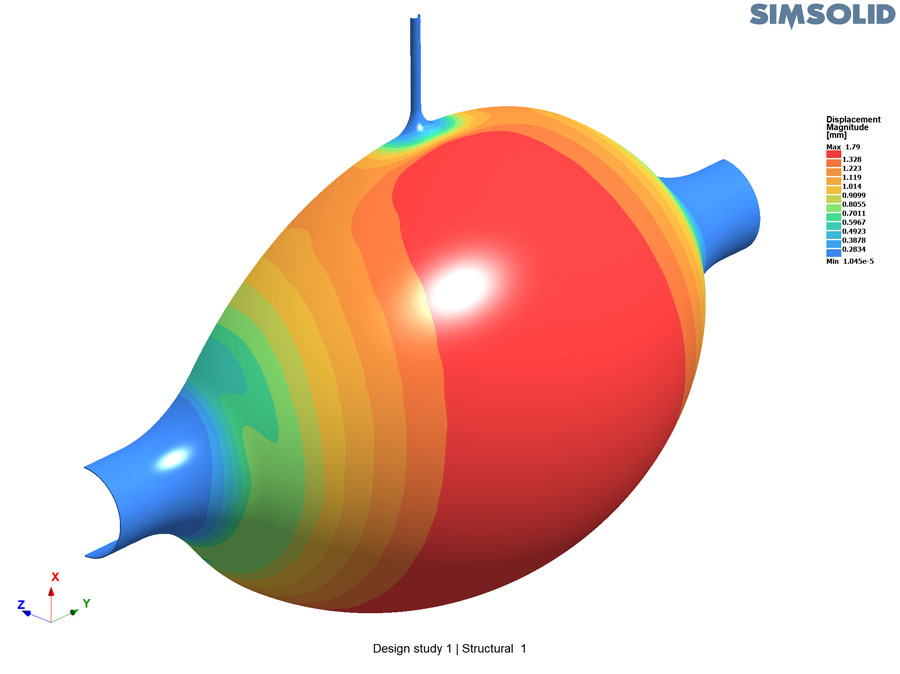
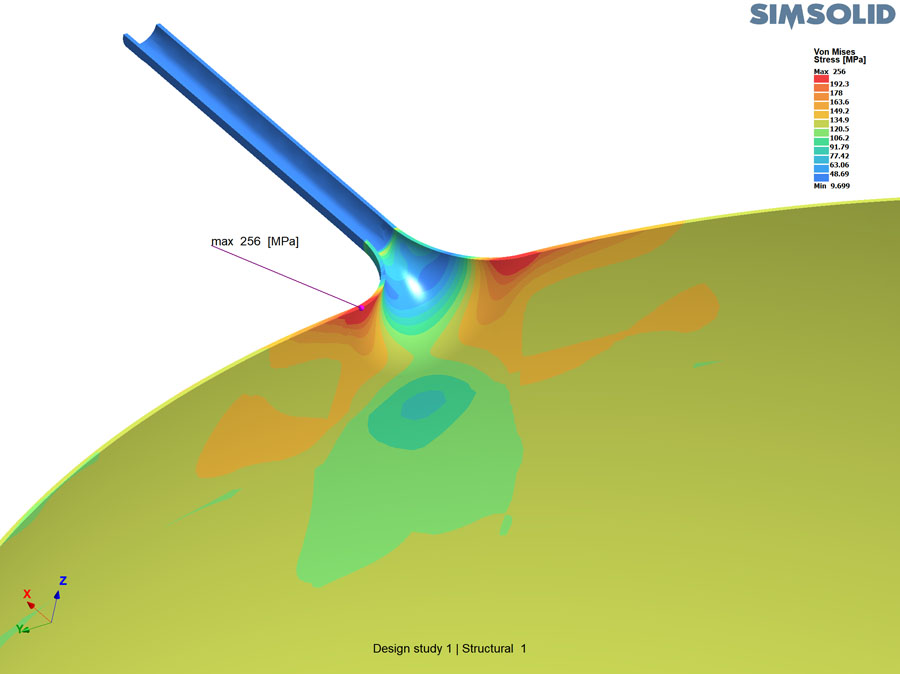
Note that while the reactions and load paths are OK, the stresses and displacements need refinement.
Now, switch to the new Adapt to thin shells geometric complexity setting.
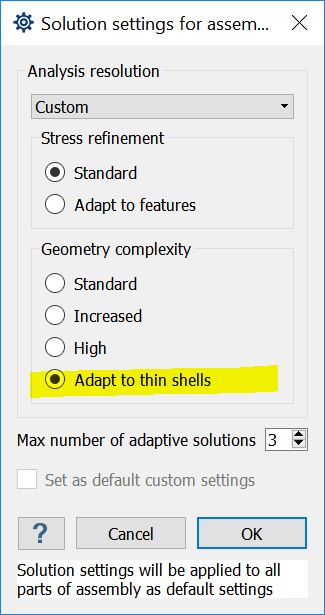
Here the local displacements are captured in full detail. and the stress distribution is refined. Comparing this to a traditional FEA shell solution we find the results are within 1% and the distribution of displacement and stress identical.
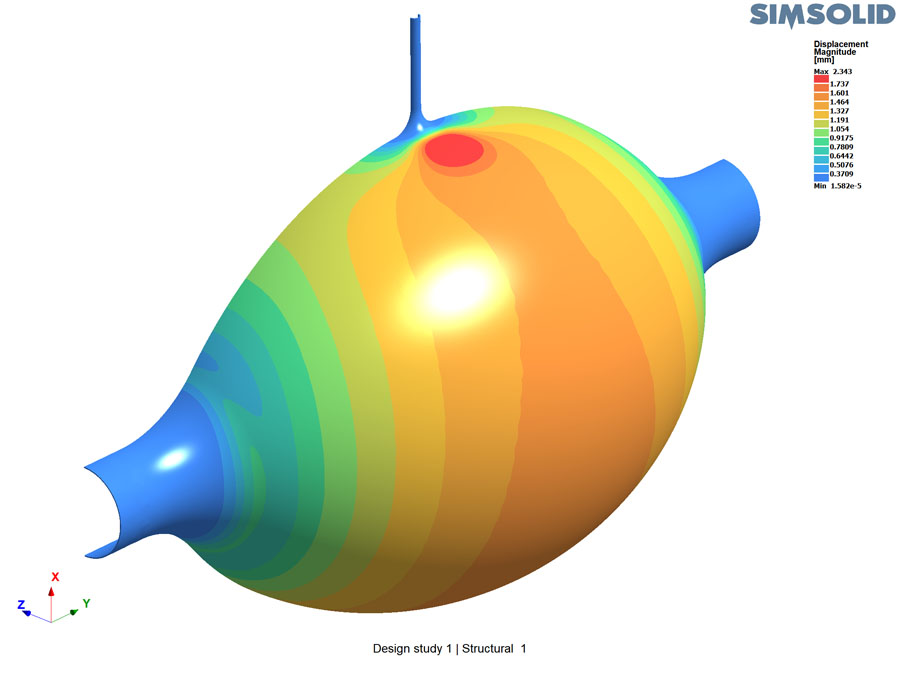
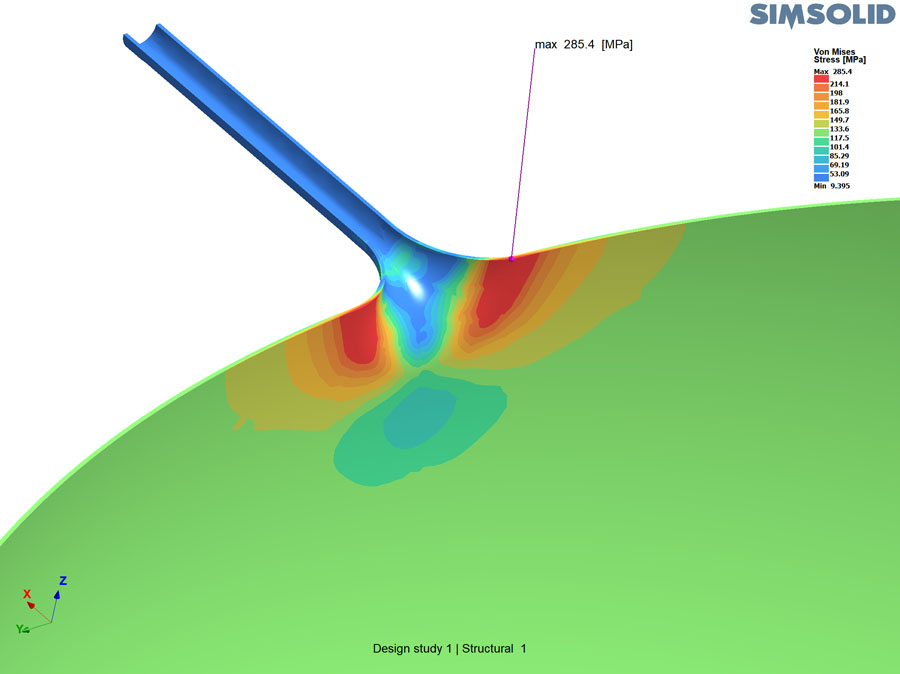
Finally, here is an animation of the deformed shape.
[video width="2128" height="1600" mp4="https://www.simsolid.com/wp-content/uploads/2017/08/thin-shell-anim.mp4"][/video]
Altair SimSolid's unique formulation is capable of solving assemblies with a variety of part shape and scales. All done on the original, un-simplified, CAD geometry. So next time, you need to solve an assembly with shells, use this new convenient solution setting.
Types of Solutions settings
The default setting is Standard. This will provide three adaptive solution passes and is intended to provide the best trade-off of solution speed to solution quality. In most cases, this will be all that is required for general load path calculation. A best practice is to always start with this setting.The second solution quality level is Detailed. This will provide four adaptive solution passes and also has additional solver logic to refine stresses more completely. A best practice is to use this setting on local parts where additional stress detail is desired.
The third solution quality level is Custom. This is an expert mode that allows individual control of all solution settings. This should only be used for parts with unusual characteristics or when fine degree of control is desired.
Individual controls include:
- Stress refinement – this setting controls the methodology used to refine stresses. Here you can set an optional "Adapt to features" methodology that uses more aggressive adaptivity for stress distribution in local feature areas. A best practice is to use this locally on a part by part basis. Applies only to structural linear and nonlinear statics, this is not used in modal or thermal analyses.
- Geometry complexity – Options include: Standard, Increased, High and the new Adapt to thin shells. This setting represents the initial density of the equations used on a part by part basis. For most parts Standard is the best choice. In most cases, this only needs to be increased for parts with extreme aspect ratios such as long narrow parts or thin complex curved shells. The new Adapt to thin shells has additional checks for curvature and thickness. Use this setting for sheet metal or stamped typed parts. Again, this is best done on a part by part basis. Increasing the geometry complexity globally will slow down solution time.
- Max number of adaptive solutions – Altair SimSolid is an adaptive solver that makes multiple solution passes. With each pass, the equations are solved, global and local error measures are calculated and based on these measures, the equations are locally enriched. Increase this value to increase accuracy. Typical values are 3 to 6 passes.
Adapt to thin shells example
To examine the effect of Altair SimSolid's new Geometric complexity settings, we performed a static analysis of the following complex thin walled part. All three outlets are fixed and a symmetric slider constraint is applied to the plane of symmetry. The tank is internally pressurized with a 1 MPa pressure load.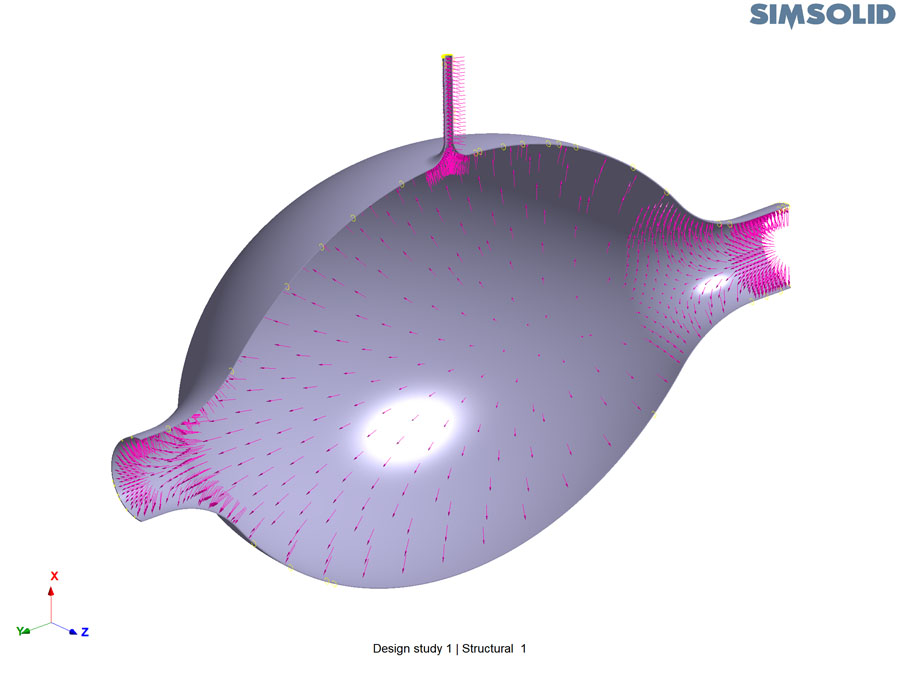
This is a challenging problem. The geometry is very thin and doubly curved. In traditional FEA, this is typically solved using shell elements. Shell elements are complex to define. In addition to the usual meshing tasks, the user must create a mid-surface from the solid, the shell elements must be oriented correctly and locally thicknesses applied. In Altair SimSolid all that is required is local solution settings.
First, here is the problem solved with standard settings.
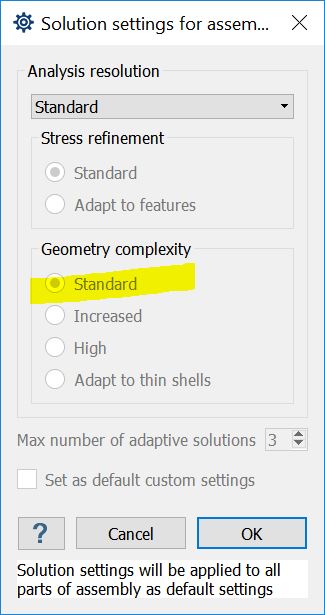
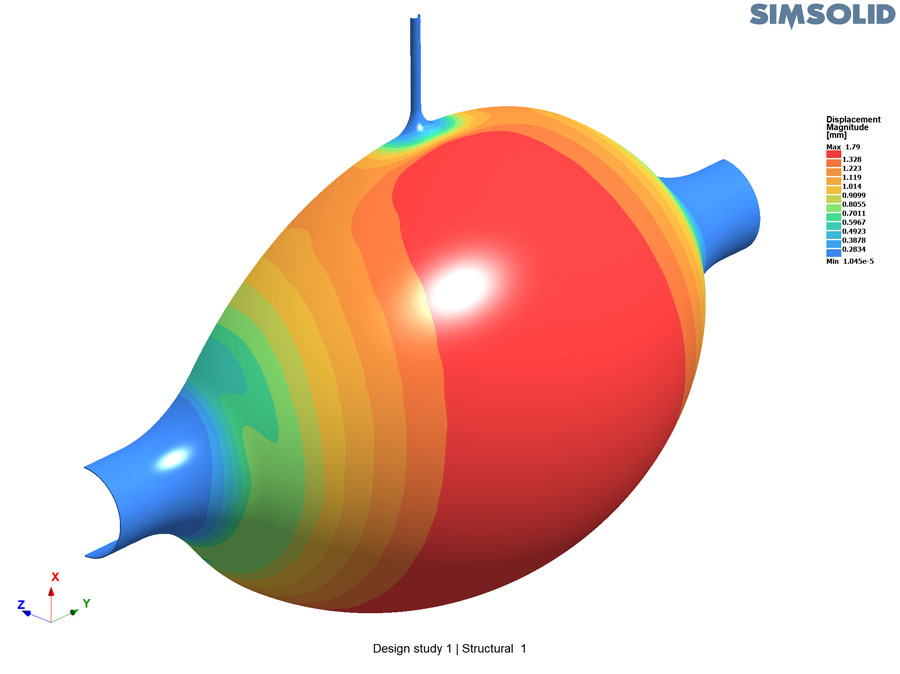
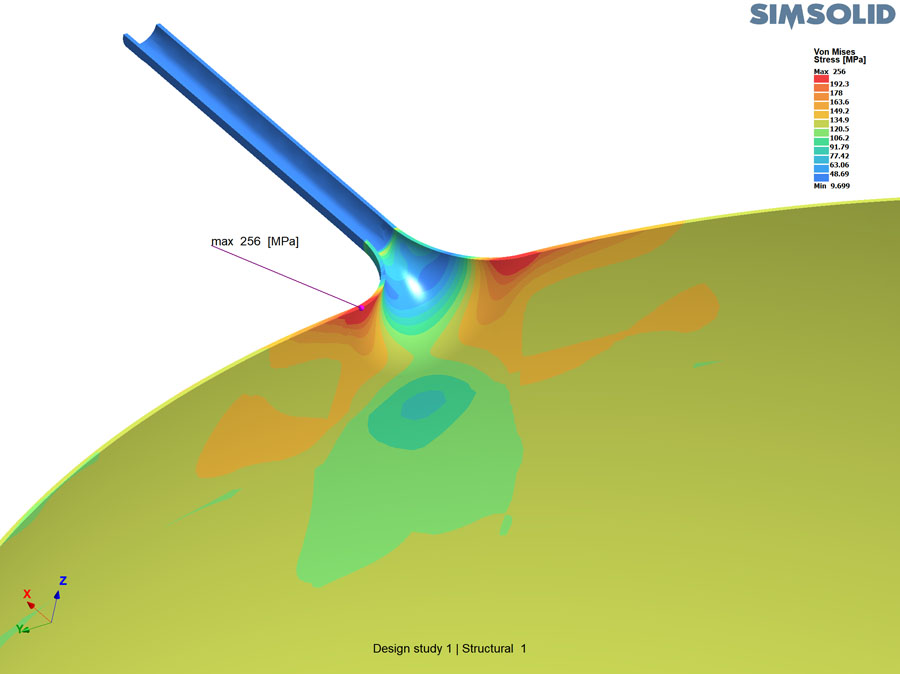
Note that while the reactions and load paths are OK, the stresses and displacements need refinement.
Now, switch to the new Adapt to thin shells geometric complexity setting.
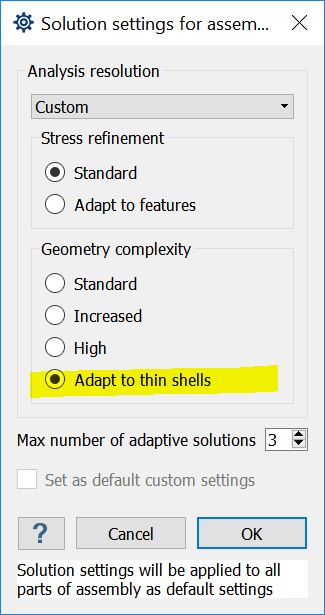
Here the local displacements are captured in full detail. and the stress distribution is refined. Comparing this to a traditional FEA shell solution we find the results are within 1% and the distribution of displacement and stress identical.
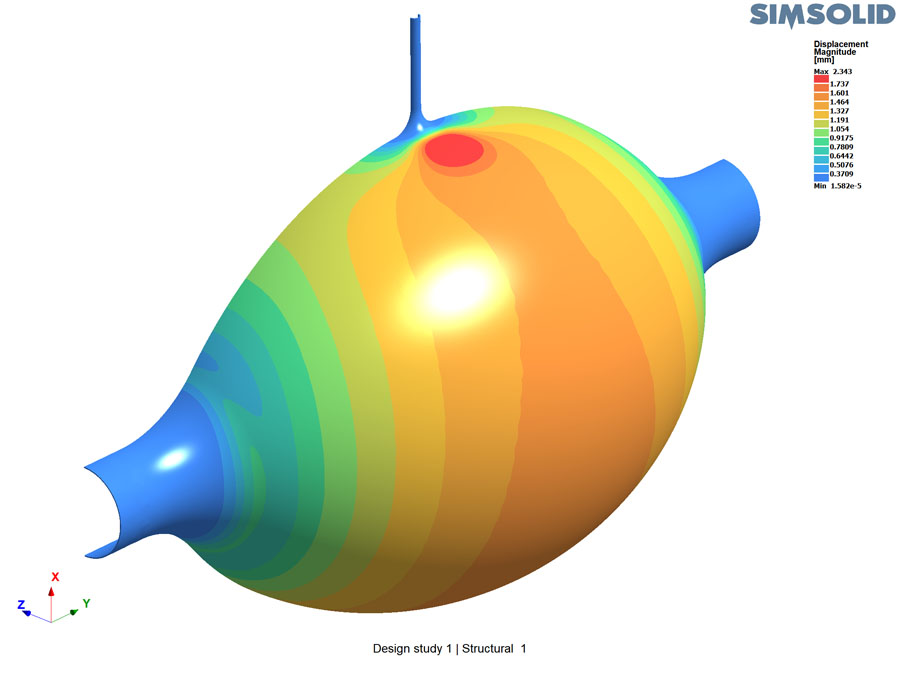
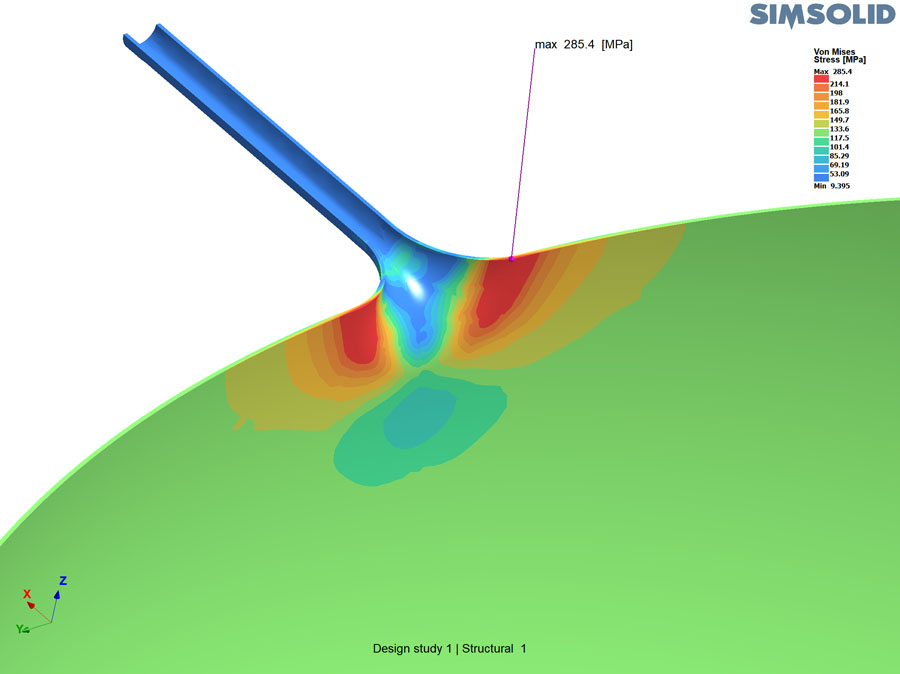
Finally, here is an animation of the deformed shape.
[video width="2128" height="1600" mp4="https://www.simsolid.com/wp-content/uploads/2017/08/thin-shell-anim.mp4"][/video]
Altair SimSolid's unique formulation is capable of solving assemblies with a variety of part shape and scales. All done on the original, un-simplified, CAD geometry. So next time, you need to solve an assembly with shells, use this new convenient solution setting.