Why Moving to Hardware Is So Challenging in Motor Control Development
In just about every industry, manufacturers are pushing the pace of innovation through the development of smart, connected products. But for all the benefits they afford consumers, these smart products’ complexity has made it harder for design and manufacturing teams to ensure their reliability and bring them market as fast as possible.
As electrification and e-mobility trends accelerate, these challenges are particularly acute when developing motor control systems, especially in code development and the transition from schematic design and virtual validation into the hardware of the physical product.
Increasing Development Complexity
The more complex a product is, the more time designers need for development and simulation. This leaves little time for moving from the virtual space into tangible hardware. Manual coding for motor control firmware is a tedious, time-consuming process, and it also increases the likelihood of error.
But firmware development tools like Altair® Embed® can speed up the process by reducing errors using automatically generated firmware, conducting continuous testing at each development phase, and by easily migrating algorithms to other microcontrollers.
Embed is model-based design software for developing algorithms for complex embedded systems. Offering deep support for the most popular on-chip peripherals, Embed’s libraries and algorithms for electric motor control provide the starting point to accelerate embedded motor control projects for any type of sensored or sensorless electric motor, including AC induction, brushless DC electric motor (BLDC), permanent magnet synchronous motor (PMSM), brushed DC, internal permanent magnet (IPM), or stepper motors.
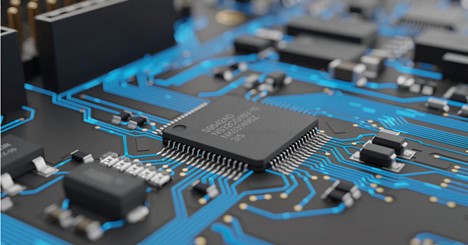
Debugging from Testing and Verification
The testing and verification phase of motor control development can present additional hurdles, but hardware-in-the-loop (HIL) simulation helps mitigate many of these risks by budgeting overrun and development slow-downs. HIL is a technique where real signals from a controller are connected to a test system, adding the complexity of the plant under control to the embedded system test platform. This lets users simulate of thousands of possible scenarios without the cost and time associated with actual physical testing.
With HIL, users can test the electronic control unit (ECU) before the actual plant that it will control is available. They can also create fault conditions and eliminate the risk of damaging the plant. Additionally, users can test the ECU with the plant running in off-design conditions.
In Embed, users can simulate the controller and plant to easily tune the control offline, then use integrated HIL to debug and tune the control on the embedded target. The interface offers multi-parametrized testing, interactive tuning for what-if studies, high-speed data collection, and most importantly, doesn’t require specialized real-time simulation hardware.
Embed provides ready-to-use libraries for motor control strategies combined with a fast debugging capability. The visual environment uses block diagrams to design, simulate, analyze, and automatically generate efficient code that can be downloaded, executed, and validated directly on target hardware. Additionally, deep support is available for the on-chip peripherals of STMicroelectronics’ STM32 family of 32-bit microcontrollers, reducing design iterations and errors, and reducing costs.
Streamlining Embedded System Design
In the constant race to accelerate motor control development, it’s key to create a process which transitions from diagram to code seamlessly. In one unified environment, Embed makes this possible through the automatic generation of field-oriented control algorithms, simulation of motor and power electronics controllers, full on-chip peripheral support, and system validation using advanced HIL methodologies.
To learn more about using embedded system design software to take advantage of best-in-class STM32 chips, check out our free webinar hosted by us and STMicroelectronics.