Wind Energy Startup Maximizes Sustainability with Simulation
Global efforts to reduce greenhouse gas emissions and tackle the adverse effects of climate change have been underway for some time, bolstered by recent international treaties like the Paris Agreement. As part of this effort, large automotive companies like Ford have started using environmentally friendly plant-based materials to build many of their car parts – arm rests sourced from trees and wiring channels sourced from rice hull, for example. These materials, in addition to being greener, weigh less, are more fire resistant, and absorb sound and vibration more efficiently than their previous iterations. The verdict is in: Sustainable designs last longer and save money because they produce less waste and require less energy throughout the manufacturing process.
Without a doubt, replacing plastic components with alternative materials is a huge step forward, and it’s clear that simulation-driven design is playing an outsize role by helping people develop cleaner products and better technology that harnesses renewable energy.
Spanish startup Vortex Bladeless offers an innovative way to harness energy from wind using different and exciting characteristics. Conventional wind turbines prove wind is an excellent source of energy, but there are challenges inherent in wind power that restrict its application. The Vortex Tacoma counters these restrictions, and the secret lies in its unique design. Instead of a traditional fan-like turbine, the Vortex Tacoma is a tubular structure with a carbon fiber rod in the middle and alternator roughly at the halfway point. It stands perpendicular to the wind and generates electricity via oscillation and therefore doesn’t require gears, breaks, or oil. Its innovative design reduces its operational noise and minimizes its impact on local wildlife. Additionally, they can operate closer to one another than conventional turbines, raising a group’s generation capacity.
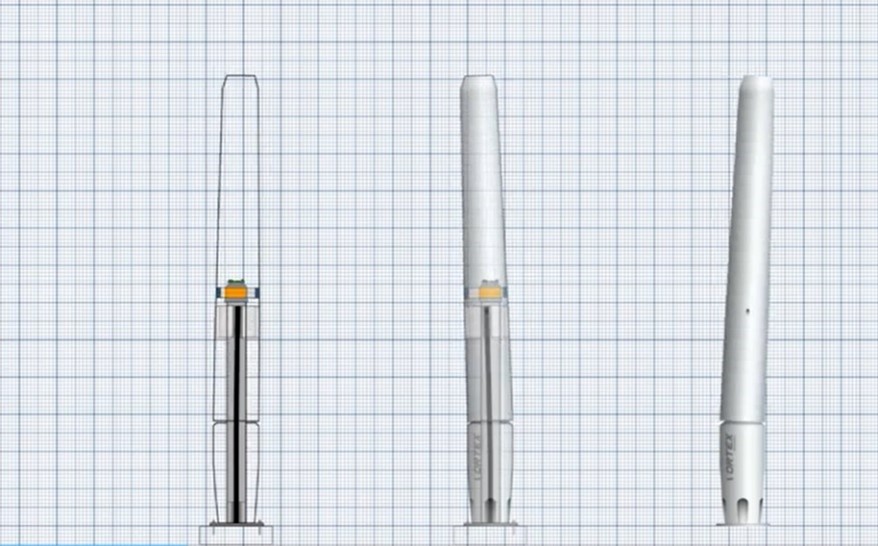
Finite Element Analysis and Computational Fluid Dynamics
The collaboration between Vortex Bladeless and Altair started with a technical project to simulate the device’s aerodynamic behavior. Altair engineers performed a fluid-structure interaction study with Altair® CFD™, our computational fluid dynamics (CFD) solver. They also used Altair® OptiStruct®, our linear and non-linear structural optimization software, to build models that let engineers predict the movement of Vortex Bladeless at different wind intensities.
Electromagnetic Analysis
Vortex Tacoma generates electricity through an alternator system that consists of static and moving parts made of coils and magnets. Using Altair® Flux®, the teams ran simulations studying the amount of electromagnetic flux traveling through the alternator’s center coil. Additionally, they used Flux to study the amount of energy produced in real time.
Another of this machine’s features is its ability to change its rigidity to adapt to wind characteristics without mechanical or manual intervention. Different environmental conditions require different setups in terms of mass distribution and rigidity. The teams used Flux to test this system’s effectiveness and ensure it had an optimal response rate.
Lifespan and Fatigue
One of renewable technology’s key pillars is lifespan. Producing durable, reliable equipment reduces the need for replacement parts and additional materials. Because the team wanted to ensure its durability, Vortex Bladeless used Altair® SimSolid® to study the fatigue of the wind turbines’ carbon fiber rods. SimSolid makes it easy to analyze the different forces applied to this component. As such, the team used the simulation’s results to predict the number of years the equipment can last under specific loads and in different environments.
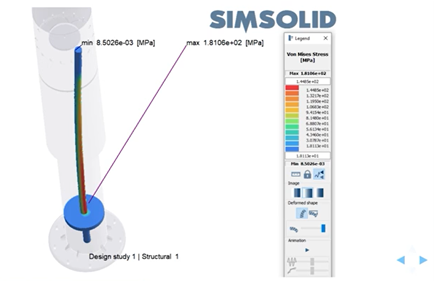
To learn more about how Altair has helped Vortex Bladeless analyze and design its bladeless wind turbines, check out this video.