formnext: The Future of Additive Manufacturing is Here and Now
When I first entered the formnext 2018 show floor on Tuesday last week, I realized right away that there was a lot to learn at this year’s edition of the leading global event on additive manufacturing. With a strong focus on 3D printing solutions, the 2018 trade show also takes its visitors beyond the well-known AM applications, putting on display modern hybrid manufacturing methods such as AM + casting, forming, and extrusion. All this and so much more was to be discovered and ready for me to explore the depth of innovation modern manufacturing has to offer.
The starting point for me was of course to visit our spacious company booth offering space for Altair as well as for APWORKS, M&H CNC Technik, and RSC Engineering. It was rewarding to see the collaboration of great companies and customers that made formnext such a fantastic event. It was a great pleasure to share the booth space and to present our solutions as well as the latest stunning results of their simulation projects side by side. Yet, the Altair discoveries didn't stop at the Altair booth. It started before the entrance of the trade show with the first impression of VDMA booth, where the Working Group AM showed a complete process chain from concept to application, in which we provided the showcase and covered the design for additive manufacturing part of the process. Walking around the trade show floor more products were to be discovered, all designed with our software and/or our help - all #InspiredByAltair.
Products #InspiredByAltair – Exhibition Pieces throughout formnext
While most of the exhibitions pieces at the Altair booth demonstrating the results of simulation-driven design were examples of 3D printing, the benefits of simulation-driven design also became obvious when looking at other manufacturing methods. One example at the booth to demonstrate how to develop for casting was the optimdoor from Sogeclair. This airplane service door was realized through investment casting from a printed pattern that was structurally optimized to consider complex loading and assure high accuracy and weight savings.
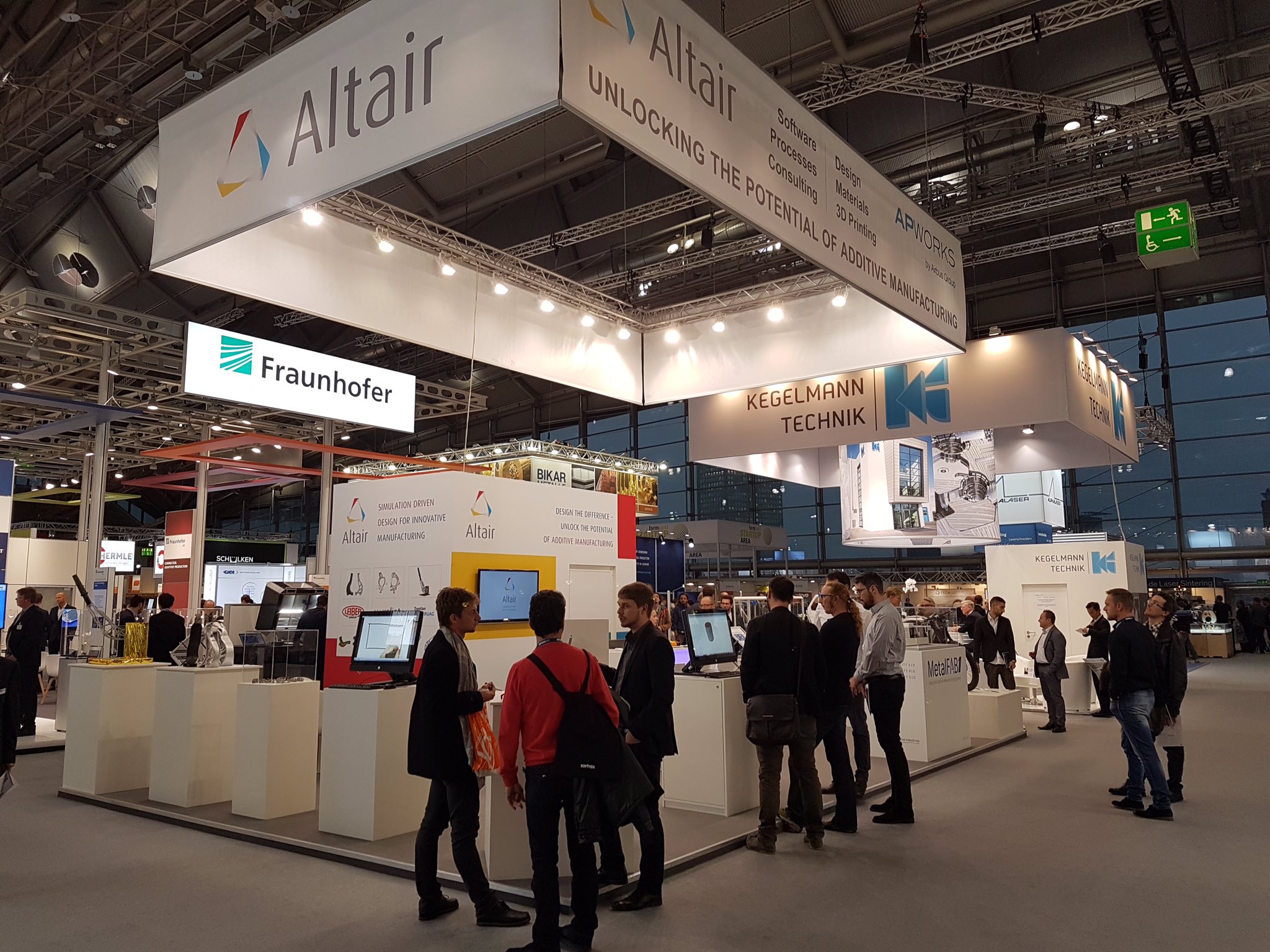
Nonetheless the most fascinating exhibition piece for me was the redesign of an aerospace bracket, presented by M&H CNC Technik. The starting challenge was the high number of loading situations the bracket had to endure. When re-designing the part, the engineers needed the bracket to keep its former stiffness but wanted to reduce weight and material used. The achievements were significant, with accomplishing their goals and reducing the production waste by 91 %! While these results were excellent, most visitors including me were even more fascinated by the fact that by means of this exhibition piece the entire development process was made visible. After defining the requirements and which part of the structure may not be changed the bracket was topology optimized to reduce weight. In the next step – the simulation of the printing – the position of the finished product can be changed to use the space of the printer most efficiently with the least production waste. After finding the best printing position another round of optimization is needed because the printing process will have other strains to the object than when it is used. Especially the thermal and material properties during printing need to be considered e.g. the stiffness or the design of the part might need to be changed so it doesn’t break while being manufactured.
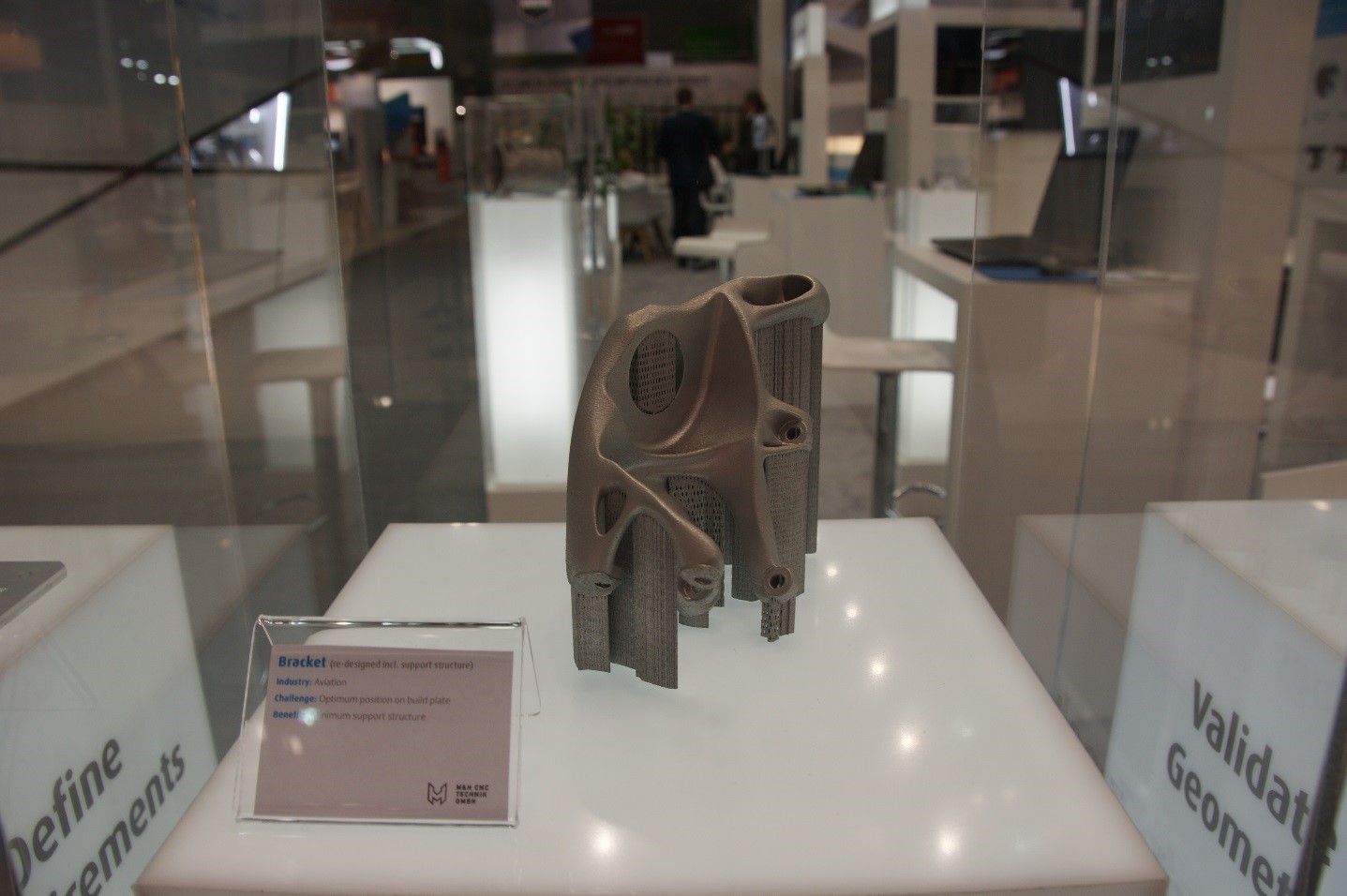
Did you know the support structures that you see in the image aren’t there to fill the whitespace, so the part doesn’t collapse during printing but are required to make sure it doesn’t curve up because of the heat? And that this, too, should be simulated? I didn’t. Thanks to talks with Altair Experts at the booth, I do now!
Prumundus Challenge: Awarding the Best
One highlight of every year's formnext is the international design competition “Purmundus challenge” for which we have the honor of sponsoring the prizes. A total of 34 finalists competed for a chance to win the coveted Purmundus challenge trophy. The challenge is hosted and organized by Cirp GmbH and formnext.
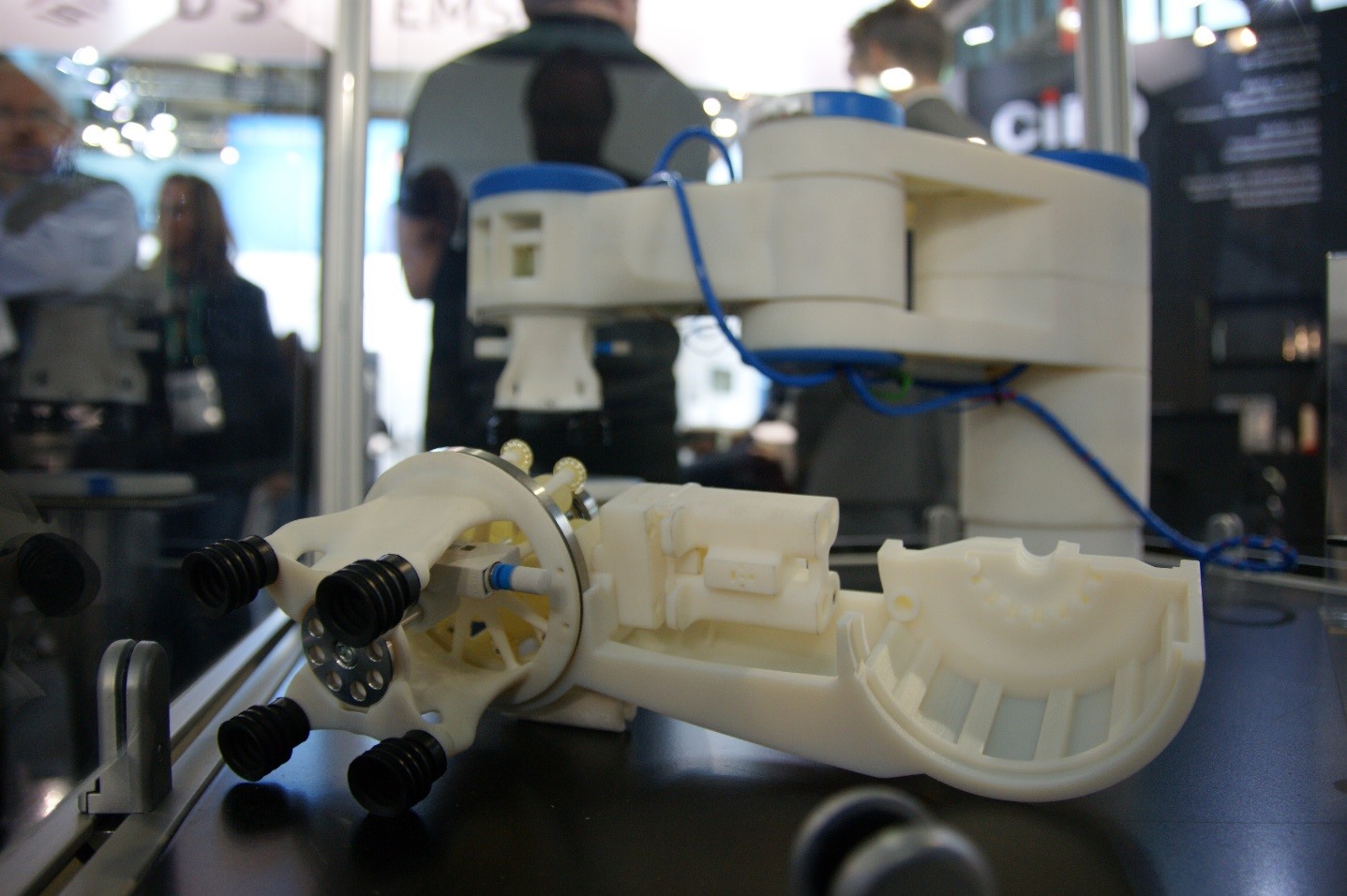
Next to the contributions to the challenge a DIMAP (Digital Materials for 3D Printing= research project was presented at the CIRP/ Purmundus booth. for which For this project Cirp and FESTO developed a vacuum gripper using Altair Inspire™ and was produced by Stratasys with Polyjet Technology. In this project, the special focus was on the durability of the materials and their capability to endure high load cycles as you find them in factory automation applications.
Endless AM possibilities
formnext is an amazing trade show with many great projects and possibilities on two floors. It's a can't miss event for anyone in the additive manufacturing industry and it was a great privilege to have attended. Attendees learned about our simulation-driven design approach throughout the show floor and about the endless possibilities of modern manufacturing. formnext shows us how future products will look and what they will be able to do. We are looking forward to formnext 2019!
[video width="852" height="480" mp4="/videos/default-source/news-videos/ExhibitionPieces2.mp4"][/video]
The starting point for me was of course to visit our spacious company booth offering space for Altair as well as for APWORKS, M&H CNC Technik, and RSC Engineering. It was rewarding to see the collaboration of great companies and customers that made formnext such a fantastic event. It was a great pleasure to share the booth space and to present our solutions as well as the latest stunning results of their simulation projects side by side. Yet, the Altair discoveries didn't stop at the Altair booth. It started before the entrance of the trade show with the first impression of VDMA booth, where the Working Group AM showed a complete process chain from concept to application, in which we provided the showcase and covered the design for additive manufacturing part of the process. Walking around the trade show floor more products were to be discovered, all designed with our software and/or our help - all #InspiredByAltair.
Products #InspiredByAltair – Exhibition Pieces throughout formnext
While most of the exhibitions pieces at the Altair booth demonstrating the results of simulation-driven design were examples of 3D printing, the benefits of simulation-driven design also became obvious when looking at other manufacturing methods. One example at the booth to demonstrate how to develop for casting was the optimdoor from Sogeclair. This airplane service door was realized through investment casting from a printed pattern that was structurally optimized to consider complex loading and assure high accuracy and weight savings.
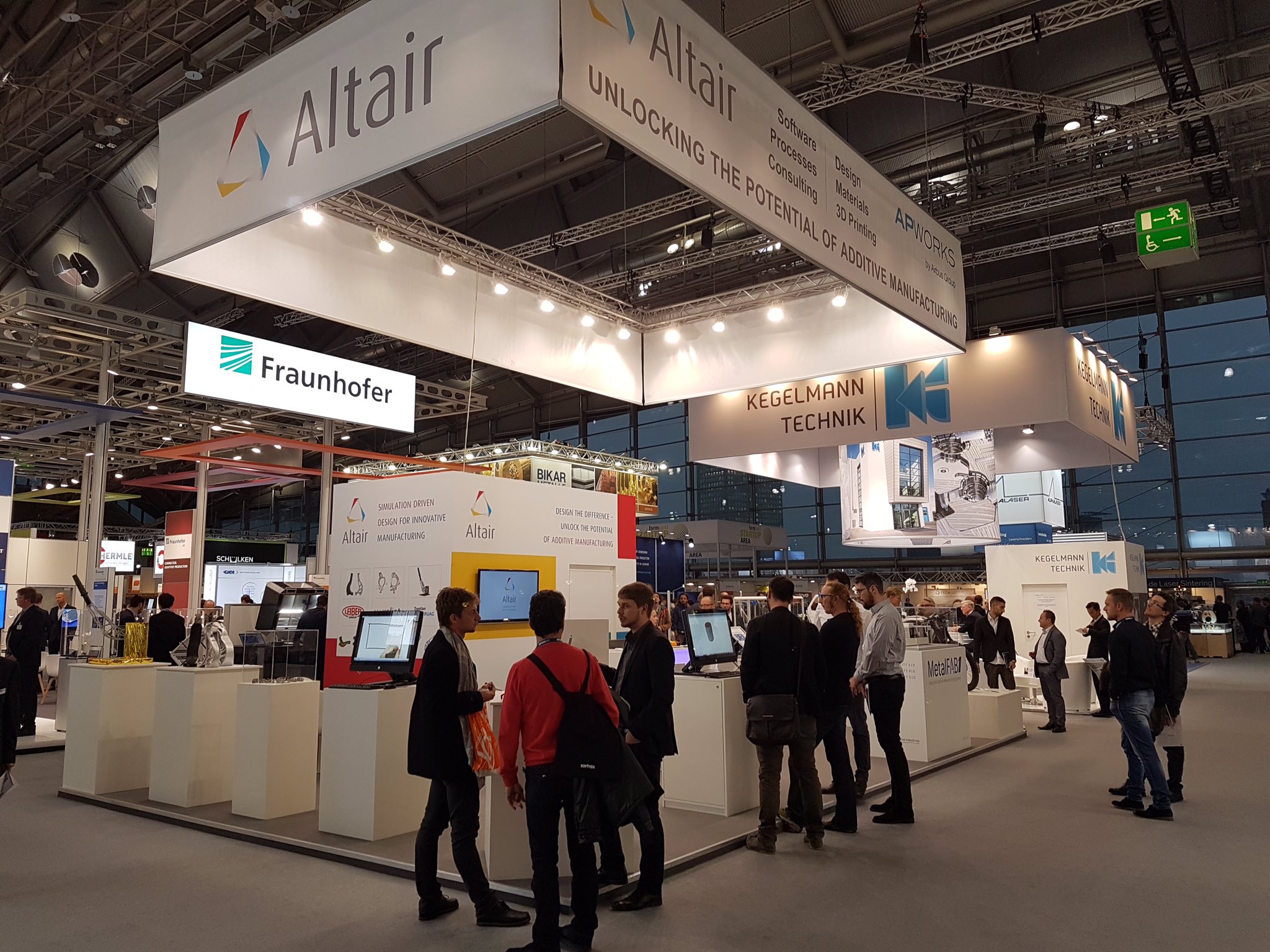
Nonetheless the most fascinating exhibition piece for me was the redesign of an aerospace bracket, presented by M&H CNC Technik. The starting challenge was the high number of loading situations the bracket had to endure. When re-designing the part, the engineers needed the bracket to keep its former stiffness but wanted to reduce weight and material used. The achievements were significant, with accomplishing their goals and reducing the production waste by 91 %! While these results were excellent, most visitors including me were even more fascinated by the fact that by means of this exhibition piece the entire development process was made visible. After defining the requirements and which part of the structure may not be changed the bracket was topology optimized to reduce weight. In the next step – the simulation of the printing – the position of the finished product can be changed to use the space of the printer most efficiently with the least production waste. After finding the best printing position another round of optimization is needed because the printing process will have other strains to the object than when it is used. Especially the thermal and material properties during printing need to be considered e.g. the stiffness or the design of the part might need to be changed so it doesn’t break while being manufactured.
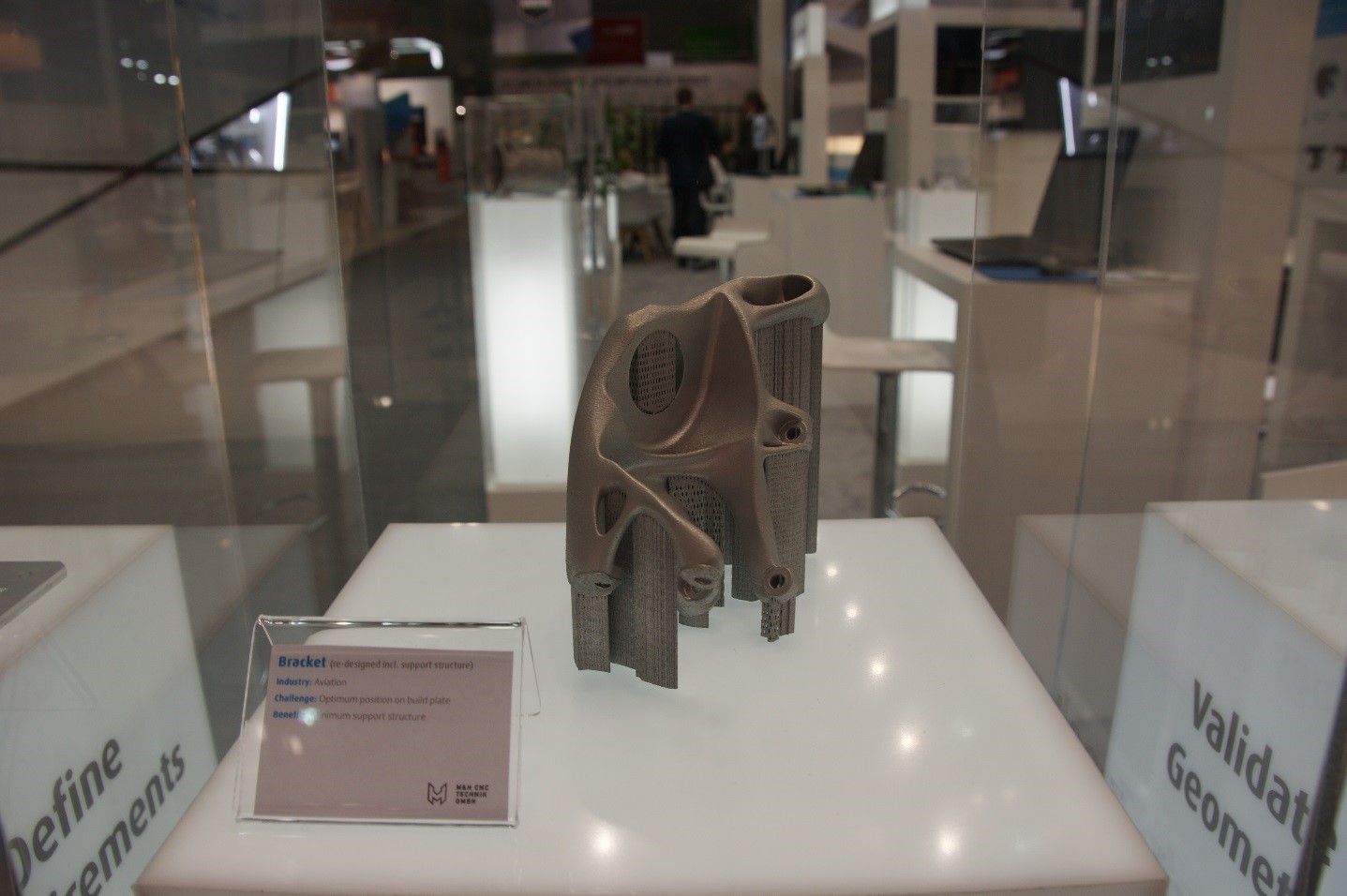
Did you know the support structures that you see in the image aren’t there to fill the whitespace, so the part doesn’t collapse during printing but are required to make sure it doesn’t curve up because of the heat? And that this, too, should be simulated? I didn’t. Thanks to talks with Altair Experts at the booth, I do now!
Prumundus Challenge: Awarding the Best
One highlight of every year's formnext is the international design competition “Purmundus challenge” for which we have the honor of sponsoring the prizes. A total of 34 finalists competed for a chance to win the coveted Purmundus challenge trophy. The challenge is hosted and organized by Cirp GmbH and formnext.
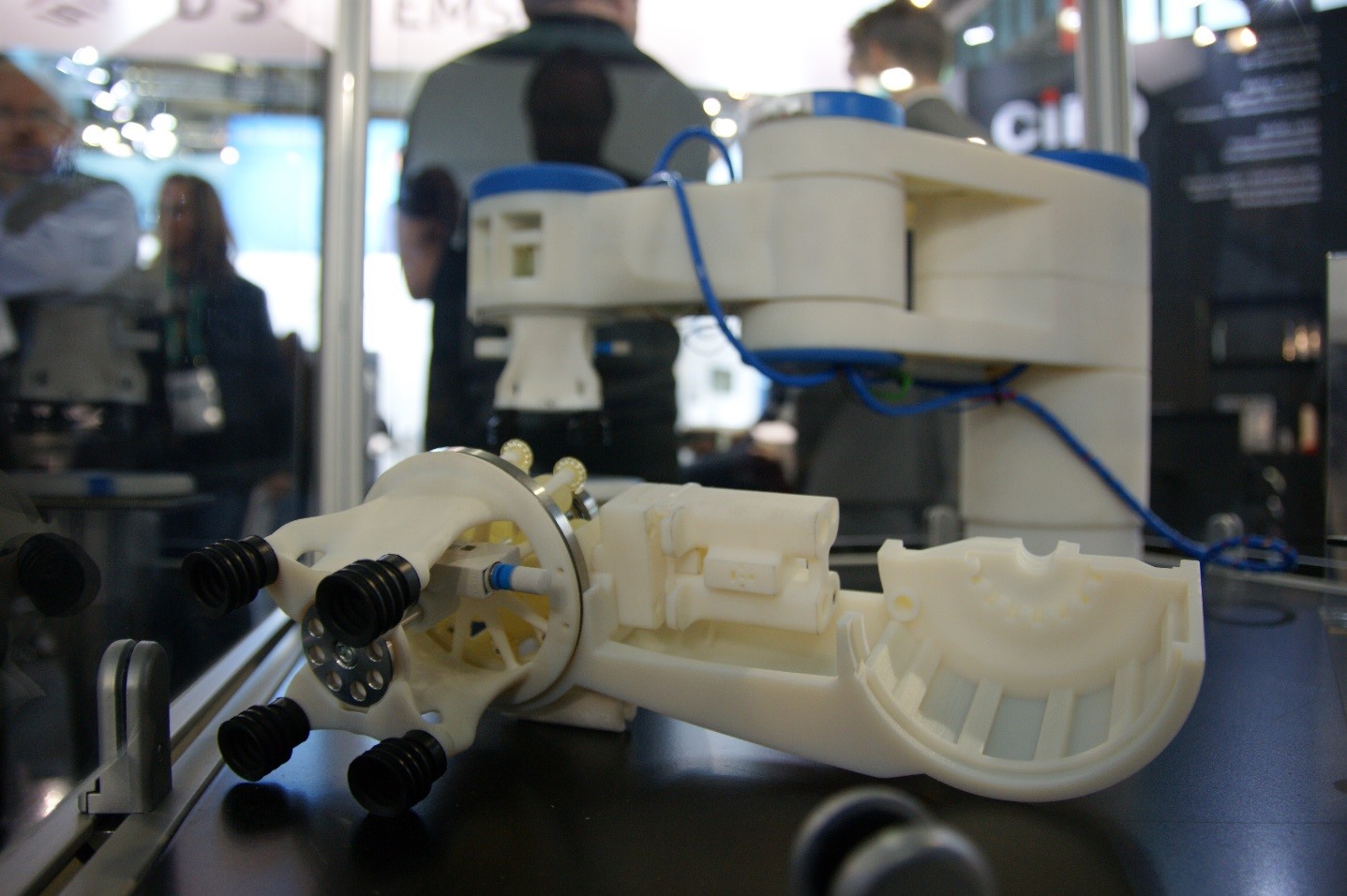
Next to the contributions to the challenge a DIMAP (Digital Materials for 3D Printing= research project was presented at the CIRP/ Purmundus booth. for which For this project Cirp and FESTO developed a vacuum gripper using Altair Inspire™ and was produced by Stratasys with Polyjet Technology. In this project, the special focus was on the durability of the materials and their capability to endure high load cycles as you find them in factory automation applications.
Endless AM possibilities
formnext is an amazing trade show with many great projects and possibilities on two floors. It's a can't miss event for anyone in the additive manufacturing industry and it was a great privilege to have attended. Attendees learned about our simulation-driven design approach throughout the show floor and about the endless possibilities of modern manufacturing. formnext shows us how future products will look and what they will be able to do. We are looking forward to formnext 2019!
[video width="852" height="480" mp4="/videos/default-source/news-videos/ExhibitionPieces2.mp4"][/video]