Top 10 Common Mistakes in Fatigue Analysis
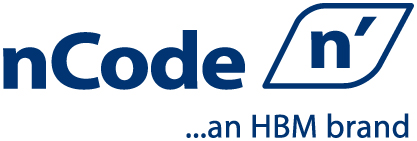
This guest post on Innovation Intelligence is written by Kurt Munson, Engineering Manager at HBM-nCode, developer of nCode DesignLife. HBM-nCode is a member of the Altair Partner Alliance.
Product durability is important both to the consumer and the engineer. The consumer who bought the part wants it to last a long time. The engineer who designed the part wants it to perform to specification. A number of you know this professionally because it’s something you think about on the job – predicting structural durability accurately.
The need to understand fatigue life has led to powerful analysis tools that allow prediction and management of product life. nCode software helps engineers understand product performance, accelerate product development and improve design in a broad range of industries - answering questions like "how long will it last?" or "will it pass the test?" before a prototype even exists. This allows us to explore how durability is influenced by a dizzying array of variables – material, loading, manufacturing, etc. A clever engineer can use these powerful analysis techniques to satisfy product durability challenges.
But how do we get the right answers? How do we ensure that the analysis is worthwhile? How do we keep ‘gotchas’ from surprising us?
The answer is this: we need to focus on making the most of fatigue analysis by eliminating common mistakes. A common mistake is highlighted by the often-asked question: “Should I use the stress-life (SN) or strain-life (EN) method for my part?” These two methods are commonly confused. They seem so similar! After all, aren’t stresses and strains pretty much the same thing – a structural response?
Dig around and you’ll find that the difference boils down to high-cycle and low-cycle fatigue. The stress-life method doesn’t apply to low-cycle fatigue – a regime that we often design in due to cost and weight challenges. The decision regarding which fatigue method to use is important!
Watch this 30-minute video in which we’ll steer you clear of common mistakes in fatigue analysis - and discuss best practices.
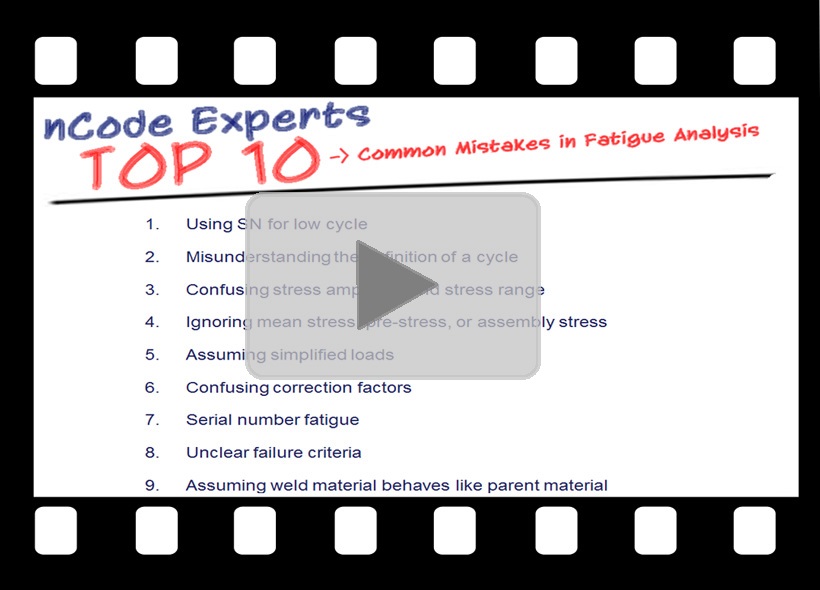
Product durability is important both to the consumer and the engineer. The consumer who bought the part wants it to last a long time. The engineer who designed the part wants it to perform to specification. A number of you know this professionally because it’s something you think about on the job – predicting structural durability accurately.
The need to understand fatigue life has led to powerful analysis tools that allow prediction and management of product life. nCode software helps engineers understand product performance, accelerate product development and improve design in a broad range of industries - answering questions like "how long will it last?" or "will it pass the test?" before a prototype even exists. This allows us to explore how durability is influenced by a dizzying array of variables – material, loading, manufacturing, etc. A clever engineer can use these powerful analysis techniques to satisfy product durability challenges.
But how do we get the right answers? How do we ensure that the analysis is worthwhile? How do we keep ‘gotchas’ from surprising us?
The answer is this: we need to focus on making the most of fatigue analysis by eliminating common mistakes. A common mistake is highlighted by the often-asked question: “Should I use the stress-life (SN) or strain-life (EN) method for my part?” These two methods are commonly confused. They seem so similar! After all, aren’t stresses and strains pretty much the same thing – a structural response?
Dig around and you’ll find that the difference boils down to high-cycle and low-cycle fatigue. The stress-life method doesn’t apply to low-cycle fatigue – a regime that we often design in due to cost and weight challenges. The decision regarding which fatigue method to use is important!
Watch this 30-minute video in which we’ll steer you clear of common mistakes in fatigue analysis - and discuss best practices.
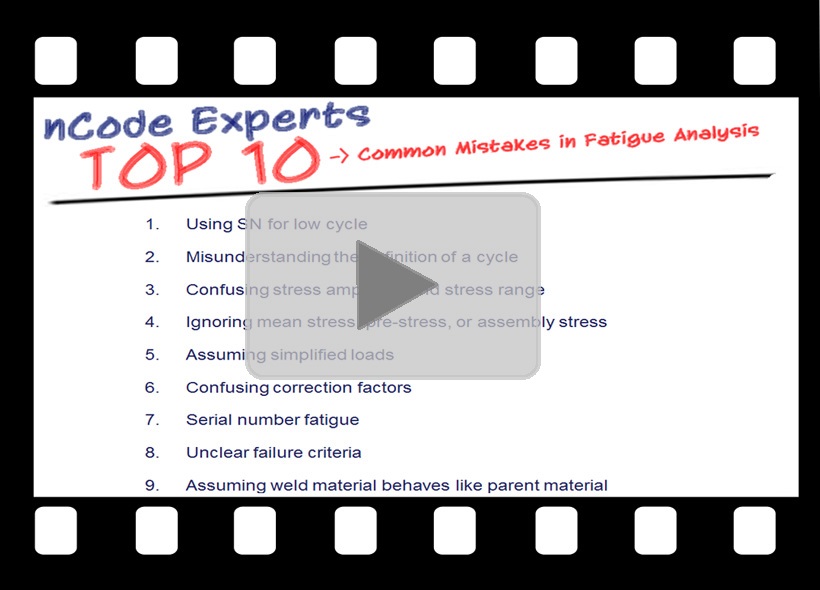