What a Swiss Army Knife Tells Us About Efficient Simulation

On the Simulation of Injection Molded Short Fiber-Reinforced Plastic Parts
This guest contribution on Innovation Intelligence is written by Dr. Wolfgang Korte, Managing Director at PART Engineering, developer of CONVERSE. PART Engineering is a member of the Altair Partner Alliance.
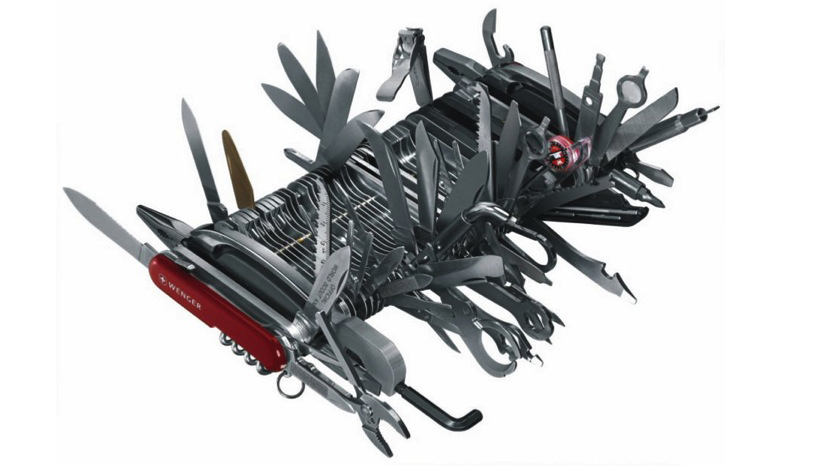
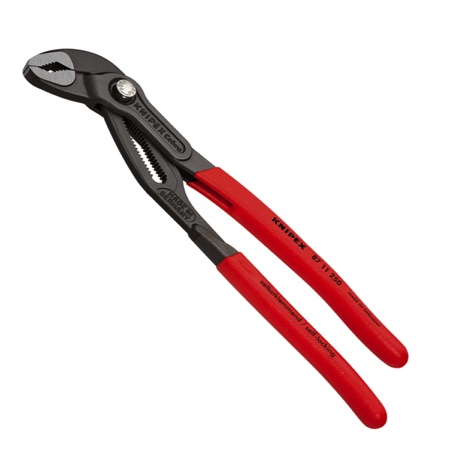
If we were presented with a serious issue and given the knife in figure 1 (left) as the solution, most of us might smile and conclude that it would not be our first choice to fix the problem. An experienced craftsman would choose a tool specialized for the issue at hand (figure 1, right), which would appear to be common sense. However, when it comes to the simulation of technical plastic parts, things are not as clear.
Most engineers are intimidated at first by the complex mechanical behavior of plastics compared to metals, assuming that complex models and software tools are necessary to simulate plastics properly. In reality, most of the same effects shown are known to happen in both metals and plastics: namely, nonlinearity, plasticity, anisotropy, creep and temperature-dependent behavior. The main difference is that for plastics, these effects may be observed more readily as they manifest with moderate temperatures whereas for metals, much higher temperatures are typically required for the effects to appear.
However, this does not mean that all of the effects above must be considered in order to make a proper assessment of the part’s mechanical performance. In fact, it is the other way around. The more effects that are taken into account, the more opportunity there will be for erroneous calibration of the model or for misjudgment of the results achieved. Appropriate material properties are a prerequisite for such sophisticated approaches, which are most often not available in practice. A basic assumption would be that if the chosen modeling approach needed more than the material properties obtained from a simple short-term tensile test, one should think twice whether the effort is truly required in order to answer the question that is asked with finite element (FE) analysis. In such cases, a smart experimental approach is often the far more reliable and efficient way.
In most real-life cases the Pareto principle applies: 80 percent of the benefit can be achieved with 20 percent of the effort, and vice versa. However, the model should be balanced in complexity by remaining as simple as possible, without omitting necessary information. For instance, if rate-dependency is an issue, e.g., in drop or crash test analysis, this has to be considered and cannot be neglected.
When this principle is applied to the finite element analysis (FEA) of injection-molded short-fiber-reinforced parts, the anisotropy with material properties at temperature of application should at least be considered. If the loads are so high that the material failure limit is exceeded, plasticity should be taken into account. For load cases where failure due to vibration and fatigue is assumed, a linear elastic material model is often suitable.
CONVERSE by PART Engineering is an easy-to-use, reliable and fast software tool for short-fiber-reinforced components which enables the user to consider all relevant effects in order to assess stiffness and strength of such parts properly. CONVERSE takes the information provided by an injection molding simulation, transfers it to a downstream mechanical simulation of the component and provides a ready-to-use FE input deck with all the material properties required to run the simulation.
Figure 2A shows an application example of an automotive headlight bracket made of a plastic containing 30 percent glass fiber. CONVERSE user VALEO Lighting Systems aimed to determine the eigenfrequencies of the part. When compared to an isotropic modeling approach, the CONVERSE approach, which considered the fibers, achieved much better predictions (Figure 2B), with an average difference of 6 Hz for the first four eigenfrequencies simulated, compared to 45 Hz for the isotropic approach.
The simulation is just as fast and stable as more typical simulations due to its usage of solver built-in material models. Therefore, parallelization can also be used to the same extent as the solver is capable and no licenses are drawn during the simulation. The software is easy enough to use that it is even relevant for the occasional user.
This guest contribution on Innovation Intelligence is written by Dr. Wolfgang Korte, Managing Director at PART Engineering, developer of CONVERSE. PART Engineering is a member of the Altair Partner Alliance.
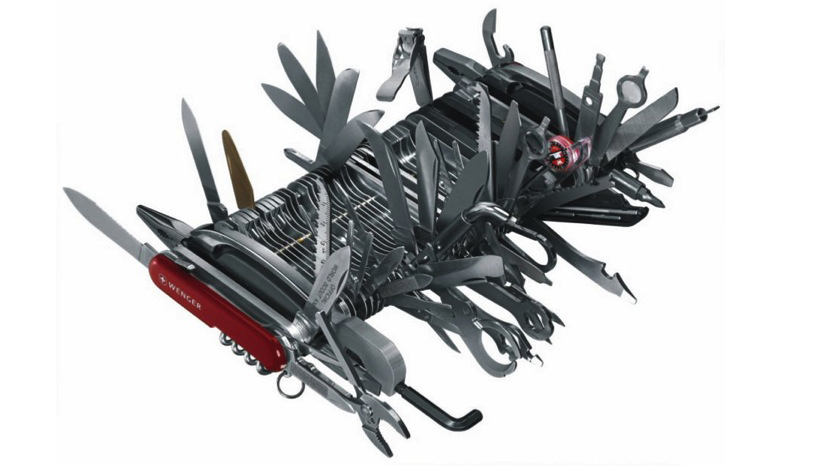
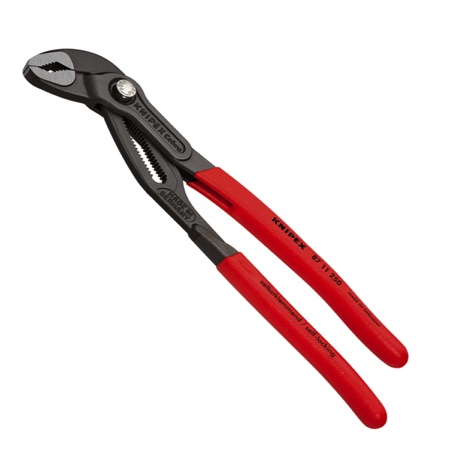
If we were presented with a serious issue and given the knife in figure 1 (left) as the solution, most of us might smile and conclude that it would not be our first choice to fix the problem. An experienced craftsman would choose a tool specialized for the issue at hand (figure 1, right), which would appear to be common sense. However, when it comes to the simulation of technical plastic parts, things are not as clear.
Most engineers are intimidated at first by the complex mechanical behavior of plastics compared to metals, assuming that complex models and software tools are necessary to simulate plastics properly. In reality, most of the same effects shown are known to happen in both metals and plastics: namely, nonlinearity, plasticity, anisotropy, creep and temperature-dependent behavior. The main difference is that for plastics, these effects may be observed more readily as they manifest with moderate temperatures whereas for metals, much higher temperatures are typically required for the effects to appear.
However, this does not mean that all of the effects above must be considered in order to make a proper assessment of the part’s mechanical performance. In fact, it is the other way around. The more effects that are taken into account, the more opportunity there will be for erroneous calibration of the model or for misjudgment of the results achieved. Appropriate material properties are a prerequisite for such sophisticated approaches, which are most often not available in practice. A basic assumption would be that if the chosen modeling approach needed more than the material properties obtained from a simple short-term tensile test, one should think twice whether the effort is truly required in order to answer the question that is asked with finite element (FE) analysis. In such cases, a smart experimental approach is often the far more reliable and efficient way.
In most real-life cases the Pareto principle applies: 80 percent of the benefit can be achieved with 20 percent of the effort, and vice versa. However, the model should be balanced in complexity by remaining as simple as possible, without omitting necessary information. For instance, if rate-dependency is an issue, e.g., in drop or crash test analysis, this has to be considered and cannot be neglected.
When this principle is applied to the finite element analysis (FEA) of injection-molded short-fiber-reinforced parts, the anisotropy with material properties at temperature of application should at least be considered. If the loads are so high that the material failure limit is exceeded, plasticity should be taken into account. For load cases where failure due to vibration and fatigue is assumed, a linear elastic material model is often suitable.
CONVERSE by PART Engineering is an easy-to-use, reliable and fast software tool for short-fiber-reinforced components which enables the user to consider all relevant effects in order to assess stiffness and strength of such parts properly. CONVERSE takes the information provided by an injection molding simulation, transfers it to a downstream mechanical simulation of the component and provides a ready-to-use FE input deck with all the material properties required to run the simulation.
Figure 2A shows an application example of an automotive headlight bracket made of a plastic containing 30 percent glass fiber. CONVERSE user VALEO Lighting Systems aimed to determine the eigenfrequencies of the part. When compared to an isotropic modeling approach, the CONVERSE approach, which considered the fibers, achieved much better predictions (Figure 2B), with an average difference of 6 Hz for the first four eigenfrequencies simulated, compared to 45 Hz for the isotropic approach.
The simulation is just as fast and stable as more typical simulations due to its usage of solver built-in material models. Therefore, parallelization can also be used to the same extent as the solver is capable and no licenses are drawn during the simulation. The software is easy enough to use that it is even relevant for the occasional user.