Sports Physics: Space-age Advanced Materials Give Tennis Players a Competitive Edge
During the late 1970s and early 1980s, professional tennis players began making the switch from wood racquets to graphite. This lighter material provides athletes greater control and allows them to swing faster to generate power and spin.
Wilson Sporting Goods Co. is one of the world’s leading manufacturers of high-performance sports equipment. Gold medalists including America’s Serena and Venus Williams and Great Britain’s Andy Murray used Wilson racquets to reach the highest peaks of their sport.
In the world of sports, the competition is fierce and the relationship between an athlete and their equipment can provide the winning advantage over an opponent. With that dynamic association in mind, Wilson Labs, the innovation hub at Wilson, invents, designs, and engineers game-changing products, employing state-of-the-art sports technologies and expertise. In its Racquet Sports business, Wilson Labs' innovation initiatives include material enhancements, mechanical enhancements, and changes to physical parameters of the racquet to fit evolving trends of the player’s game.
Today most racquet frames are made from lightweight graphite or graphite composites that incorporate materials such as titanium, Kevlar, or fiberglass, giving added levels of frame flexibility. The performance and behavior of these advanced materials, however, can be difficult to predict without the use of finite element analysis software (FEA).
Wilson Labs design engineers used Altair HyperWorksTM FEA tools to reduce design cycle time and enhancing product value of their laminated composite tennis racquets by taking advantage of simulation, automation, and optimization technologies.
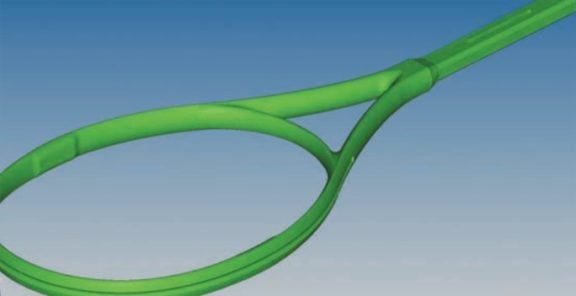
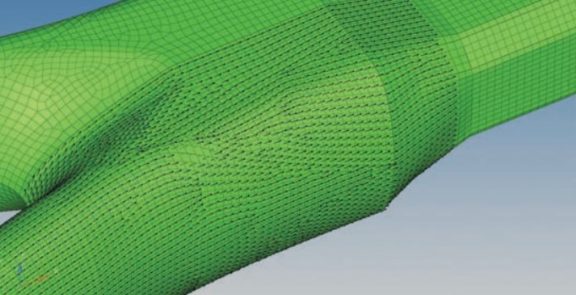
Composite simulation is used extensively in industries such as aerospace, but it was a relatively untapped resource for sporting equipment manufacturers. Wilson Labs is one of the pioneers of applying FEA in the tennis industry, recognizing its benefit as a better tool for lay-up design as well as optimization for weight, strength, stiffness, and simplicity.
For each ply of the racquet’s laminate composite construction, the lay-up document was reviewed to understand the ply location, and then surfaces were trimmed and organized. Ply thicknesses were assigned, as were material properties, loads, and boundary conditions. Several analyses were performed using the structural analysis and optimization tools in HyperWorks, and results were validated to correlate with physical test data. Testing and analyses demonstrated the close correlation between the virtual model’s behaviors and real-life behaviors.
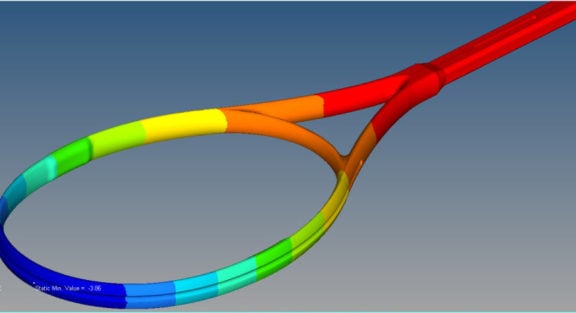
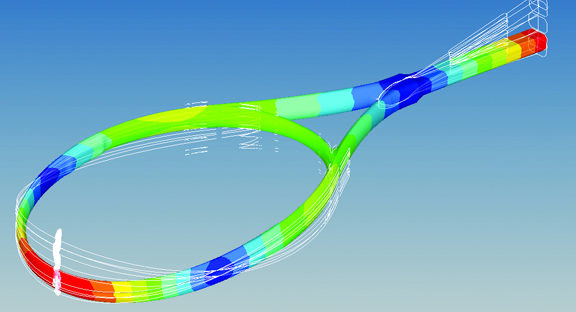
The project inspired a high degree of confidence that HyperWorks brings the accuracy required to model the tennis racquets in a virtual space, and that virtual simulation as a resource is far more efficient than manual techniques. For the performance metrics expected by Wilson Labs (mass, center of mass, dynamic stiffness, static stiffness) the results showed an error percentage of less than 4% compared to physical testing. With FEA technology in their toolbelt, Wilson believes they can bring future product designs to market faster while ensuring their equipment will perform to the high demands of professional athletes and recreational players alike.