The Right Model, for the Right Decision, at the Right Time

It may seem intuitive that the accuracy of your results will increase as model fidelity increases. But applying that logic to every simulation scenario can be detrimental to your product design process. Relevant and timely models for concept design, product engineering, and detailed analysis need different levels of complexity and data. Determining the model fidelity that best addresses a particular challenge within the context of the overall design cycle is pivotal for manufacturers looking to tackle multiple physics problems and increase decision-making speed and confidence.
All models are wrong, but some are useful.
This quote from renowned statistician George E.P. Box has become ubiquitous because it applies to a wide variety of scientific models. There’s no such thing as a universally “good” or “bad” model – there are only models that are well-suited or ill-suited to answer the question at hand. A vehicle chassis team may only need a simple motor model to incorporate into studies of a detailed chassis design, and vice versa, the motor team requires a complex motor model, but only a simple chassis to gain an understanding of the interoperability of the two components. Giving teams access to the right model at the appropriate fidelity makes processes run smoothly across the entire development cycle.
Taking a purpose-driven approach that considers 0D, 1D, and 3D simulations is the best way to extract maximum value from your design and engineering processes. To put this approach into practice, there are key considerations every product developer should weigh to ensure they’re using the right model, for the right decision, at the right time.
If all you have is a hammer, everything looks like a nail.
The first trap many product designers fall into is trying to use tools that don’t fit the purpose of the particular analysis. Understandably, when a company invests in a high-fidelity modeling software, their inclination is to think of it as a magic bullet for all of their simulation needs.
But the fact is high fidelity 3D simulation needs a lot of data to produce useful results. It’s a tool best suited for refining and validating a design that’s already been evaluated and tested during the initial design and development phases. Applied too early in the process, and without the necessary data to guide the analysis, 3D modeling must make assumptions which causes it to struggle to produce realistic results. If you’re struggling to populate the model, or if you’re only using data from last year’s part, this might be a sign that your simulation is over its necessary fidelity.
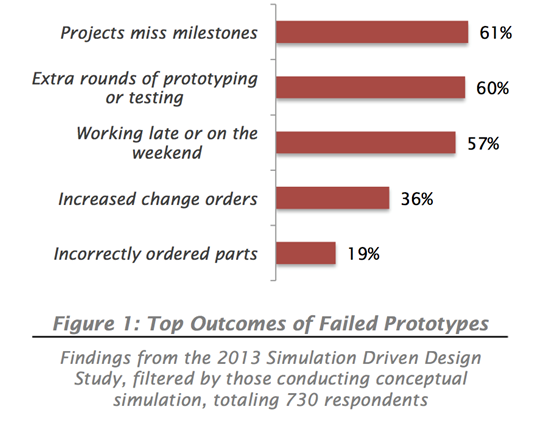
Time isn’t the main thing. It’s the only thing.
Time to market is one of the most direct drivers of profitability, but improvement can only be accomplished through a series of smaller choices made throughout the development process.
Pre-processing, especially for high-fidelity analysis, can be tedious and can increase the chance of human error. Modeling and visualization workflows in Altair® Simulation automate repetitive tasks so engineers can focus on interpreting results, not defeaturing and mesh refinement.
In addition to the engineer’s workload, computational time is also an important factor that drives profitability. Reduced-order models are useful to incorporate multiple, highly detailed 3D simulation results in a more computationally-efficient 1D environment. By combining reduced-order models and detailed CAE analysis with process automation, Altair provides workflows for early system models, mixed-fidelity simulations, and multiphysics validations.
Finally, artificial intelligence (AI) is creating new possibilities for design optimization. Physics-based, simulation-driven design augmented with machine learning-based AI-powered design can create high-potential designs earlier in development cycles. Altair® DesignAITM lets organizations scale their existing expertise and realize the value of archived simulation data to solve their most challenging problems faster.
By applying the same physics-based tools used for verification from concept to design, and through to sign-off and guided by machine learning using organizational specific constraints, Altair DesignAI quickens design convergence by rejecting low-potential designs earlier in development cycles. Augmenting traditional design exploration with machine learning-based AI streamlines early design decisions and directs design teams to the most viable models for detailed validation.
A straight line is the shortest distance between two points.
Just as a direct path is the fastest way to reach a destination, the least complex model is the most direct path to answer a design question. Sometimes, engineers get bogged down with details – adding model complexity often creates “noise” that complicates and slows the design cycle.
Compartmentalization and verticalization are two tactical approaches that can help companies explore their designs more efficiently and reach design decisions faster. By compartmentalizing analysis, companies can optimize each physics discipline independent of outside factors. Armed with a comprehensive understanding of a specific discipline and the tolerance of acceptable outcomes, companies can incorporate results more easily into system-level study.
Verticalization is another tactic that focuses engineering work within the bounds of a common structure. In addition to simplifying modeling and simulation work to the physics affecting one component of a larger design, verticalization lets companies incorporate mixed fidelity models into their workflows from multiple domains.
Altair® eMotor Director is an example of how verticalization can increase efficiency. This multiphysics simulation, design exploration, and system-level optimization framework was designed for the development of electric vehicle powertrains. Classical development strategies often take place among several parallel disciplines where negotiations and unfavorable compromises are needed to reach a final design, but eMotor Director employs an integrated and holistic development strategy that lets manufacturers meet performance requirements and maximize vehicle range.
The process begins with domain experts from electromagnetics, durability, NVH, and cooling providing their 3D simulation models. From there, the Altair eMotor Director platform joins all high-fidelity attribute models together in a 1D system model and identifies the best design considering the attribute targets. The tool supports target negotiation, provides trade-off information, and explores “what if” scenarios. Then, the optimized design decision information is fed back to the design and attribute teams for fine tuning and vehicle-level study.
You build a foundation brick-by-brick.
There are no shortcuts to good design, but there are steps companies can take to be more systematic in their approach. For instance, instead of increasing the number of complex multi-disciplinary analyses at the latter stages of design, companies can gain system-level product performance insights quicker using mixed-fidelity system modeling, which uses data and simulations already at hand.
Systems modeling tools connect compartmentalized analyses and feed multi-disciplinary system optimization. Altair Pulse® is a tool that orchestrates meaningful models and increases decision-making confidence and speed. It facilitates model simulation at mixed fidelity, incorporating 1D and high-fidelity 3D models together to paint a holistic picture of the system. Altair eMotor Director, which uses Altair® Flux®, Altair® OptiStruct®, and Altair® Activate® as its solvers, is based on the Pulse framework.
Pulse enables further exploration with Model-based Systems Engineering (MBSE), where product-level system simulation, multiphysics, data analytics, and functional requirements are integrated with SysML to find trade-offs among conflicting requirements and to determine optimal system specifications.
Model-based systems engineering is often pigeon-holed as an aspirational activity reserved for huge enterprises developing products on long timelines. Without the burden associated with some MBSE implementations, property-based requirements and specification models can be efficiently created as system design models that remain useful for downstream performance validation and design decision-making.
Altair enables actionable MBSE, which lets engineers take a practical approach to model-based development and couples accurate product-level simulation with functional requirements so your system model can be used to find trade-offs among conflicting requirements. It also determines optimal system specifications and serves as the Authoritative Source of Truth for virtual product development activity.
At various stages in the development process, engineers face fundamental questions of what they want to get out of a model: What fidelity do they need to accomplish this goal, and what criteria will they use to measure success. A digital thread answers these questions by creating 1D digital representations of product simulation, data analytics, and functional requirements. Altair’s open-architecture systems engineering tools create this digital thread to connect product development processes from concept formulation through to product release. Utilizing MBSE, 1D digital representations simultaneously support parts represented in multiple fidelities and can be transferred, reviewed, modified, and optimized through collaboration with cross-functional teams, giving designers access to models at the fidelity needed for the particular analysis at every stage of the development process.
Give ordinary people the right tools, and they will design and build the most extraordinary things.
It’s great to equip your organization with the knowledge and processes to perform analysis at the appropriate fidelity for each stage in the development cycle, but there’s one final hurdle that often accompanies this shift in practices – access to technology. Traditional licensing models make it difficult to build a comprehensive toolbox within a reasonable budget at a scale that accommodates users at all levels of design and development.
Simulation best practices are only possible if design engineers and analysts can utilize the software they need, when they need it. The Altair Units unified licensing system gives users access to every Altair product and the power to solve on any scale. Customers have full access to all of Altair’s software instantly, including more than 150 Altair and partner products, and they can run these applications on-demand locally, in the cloud, or in a hybrid setup.
And by consolidating the software environment, customers can use the same licenses for many different applications. Users can run a variety of pre- and post-processors simultaneously on a machine while only drawing units for the most valuable product, and solver instances also level on desktop to offer unmatched value. With a pool of sharable units that customers can use to access multiple products, license consolidation with Altair Units manages costs and eliminates many restrictions floating within a zone.
The power to orchestrate meaningful models boosts organizational decision-making confidence and speed. To learn more about implementing the right model, for the right decision, at the right time, visit https://www.altair.com/simulation-2021-2/.