
Power Electronics and Motor Drive Software | Altair® PSIM™
PSIM provides solutions to a variety of power conversion-related applications, from automotive to aerospace, electronics, energy, and electric utilities. PSIM empowers users in every stage of the product design process, from concept verification to rapid control prototyping and hardware implementation.
Learn More About PSIM
Quick Power Supply Design
Power supplies are the backbone of the electrified world. Converter requirements, advancements in semiconductor devices, magnetics, topologies, and control techniques require dynamic, accurate, and purpose-built power electronics simulation tools.
PSIM solves today’s power supply designers’ key challenges. PSIM can evaluate multiple topologies and converter operation characteristics, switching speed and its impacts, power loss and efficiency, electromagnetic interference (EMI) filter design and operation, and it can provide control design and implementation all in one intuitive, connected environment.
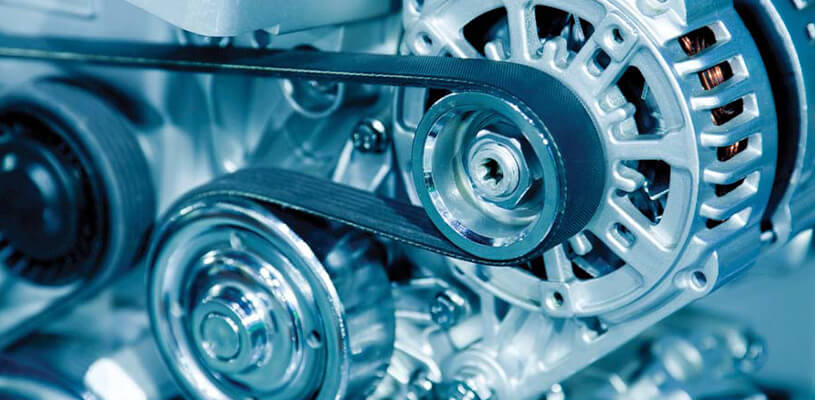
Comprehensive Motor Drive System Analysis and Design
Users need the industry’s best tools for motor drive design, simulation, and analysis – that’s why PSIM should be any team’s choice to speed up and simplify the motor drive design process.
PSIM helps users overcome the most common challenges that engineers face in the motor drives field, including:
- Motor performance evaluation,
- Controller design of current/speed/torque feedback loops (sensored or sensorless control, FOC/DTC), and
- Power converter sizing and design

Non-Ideal Device and EMI Simulation
Users don’t always need a realistic switch transition for their design work. But voltage/current overshoot, electromagnetic interference (EMI), and other transient interactions can be the difference between a finished product and a prototype that winds up in failure.
Users can utilize PSIM’s non-ideal switch models to understand:
- Voltage/current overshoot
- Conduction EMI
- Gate drive requirements
- Long cable interactions
- Other high-frequency interactions with parasitic inductors and capacitors
The addition of many small L and C values – combined with high-frequency ringing – can cause numerical instability, and users need a robust solve engine like PSIM.
How can we help you accelerate your electronic systems development?
Contact Us
Multi-Level Converters
Modular multi-level converters (MMCs) are becoming more important as the grid grows smarter and renewables play an ever more important role. Simulating them poses unique challenges for power electronics designers because of their diversity. Simple multi-level converters and MMCs can have very few switches while more complex systems can have hundreds. This means teams must carefully consider losses, efficiency, controllability, harmonics, and interactions with other local converters.
With so many aspects to consider, teams can’t spend time waiting around for each simulation to finish – with PSIM, users can handle them efficiently, accurately, and quickly.

EV/HEV Powertrain Systems
Power electronics and motor drives are at the heart of EV/HEV powertrain systems.
With PSIM’s Design Suites, teams can set up and start simulating an HEV powertrain system in no time. This helps system engineers, hardware engineers, and control engineers study the system’s aspects and speed up the development process.

Microgrid and Grid-Connected Design and Simulation
No matter if you call it smart grid, distributed generation, solid-state transformers, or microgrid, these complex systems comprised of multiple power converters, generation sources, distributed loads, and complex control schemes used to be tough to simulate. Not anymore.
With PSIM, users can design multiple converters working together covering many applications, including:
- Photovoltaic microgrids and grid-connected systems with distributed and bidirectional energy storage
- Satellite power systems with PV and battery working to power many different Point-of-Load (POL) converters
- Down hole applications in oil and gas
- Electric drivetrains with bi-directional energy storage and POL converters for planes, trains, and automobiles
Featured Resources
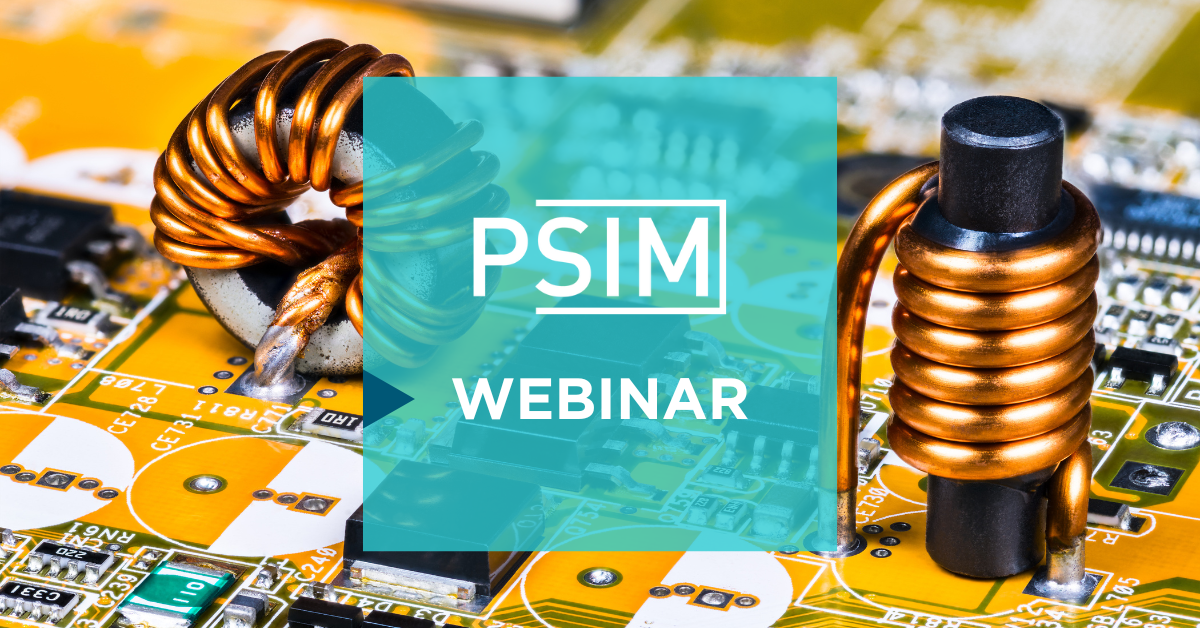
Getting Started with PSIM - Building a Buck Converter
Since Altair acquired Powersim in March 2022, many new users might ask themselves: "How do I get started with PSIM and what can it even do for me?"
Are you one of them?
Or are you already an experienced user and just want to refresh your skills and see if there are any new tips and tricks?
Either way, this webinar is right for you. Join us for a one-hour journey through the PSIM software and learn how to build a buck converter from open-loop to close-loop.
We will also give tips on how to work more efficiently with PSIM by using some shortcuts.
Main learning concepts that we will touch on:
- Library elements
- Hotkey setup
- Simulation setup
- Timestep
- Total time
- Waveform analysis
- Adding waveforms
- Saving setups
- Adding screens
- Measurements
- Changing y-axis
- Timing
- Dual/triple etc.
- Introduction to AC sweep
- Setup
- Two-loop control
- Open-loop
- Loop gain
- Parameter file use
- Variable definitions
- Sub-circuits
- Intro analysis tools
- Monte Carlo, Fault, Sensitivity
- Intro to Scripting
- Intro to other switch modes
- Thermal

Solutions for Electrification featuring PSIM and Mechanical Load Co-Simulations
This webinar shows how to leverage PSIM's motor control design tools to jump-start your electrification projects.
The motor control design suite allows non-experts and experts to quickly get a fully defined motor drive working. This can be easily modified and integrated into bigger system simulations to understand the impact of a real motor drive on system efficiency and performance. We also introduce how to use Altair Activate to link PSIM with other solvers from Altair (like MotionSolve) to provide more realistic mechanical models.
Scripting methods are being shown to solve for inverter efficiency operating points to understand the impact of design decisions on inverter losses, e.g.:
- Switching frequency
- Device selection
- PWM scheme
Co-simulations and links between PSIM and other Altair tools in this webinar include:
- Activate
- Embed
- MotionSolve

Motor Drive Power Hardware Design a Complete Design Workflow from Loss-Comparison to EMI Considerations
Designing the power stage of a motor drive poses several interesting design and optimization tradeoffs. And what makes it even more complex is that you typically require a working motor drive control algorithm to drive the motor at the shaft speed and at your developed torque set points of interest.
Some major design decisions involve:
- Comparing switching and conduction losses of specific devices
- Comparing losses and performance at different switching speeds
- Evaluate losses in different PWM schemes (DPWM, SVPWM, etc)
- Optimizing DC bus capacitor size and rating
- Determining the total system efficiency as a function of developed torque and shaft speed
- Evaluate flyback voltages under inverter faults at different operating speeds
- Conducted EMI considerations
- Linking to Simulink for co-simulation
One typical challenge is getting a working control algorithm from the control design group.
Another time-wasting activity is setting up and running the many simulations that are required to compare these dependent design variables.
And then, What if someone wants to evaluate performance at a lower switching speed?
The control loops likely need to be totally redesigned to accommodate this and then everything needs to be re-simulated.
Do you have time for this?
Using PSIM's design and automation tools we will show you how to enable even someone with little knowledge of motor control algorithms to quickly design and verify the performance of the power stage without requiring input from a separate controls group:
- Use the Motor Control Design Suite to get stable current, torque, and speed controllers for your motor and operating conditions.
- Utilize Scripting Automation to define different simulation attributes and compile interpreted results. This could save you days of back and forth with your colleagues and many hours of manual simulation setup.
- Generate motor drive efficiency maps by linking with JMAG-RT which will calculate the copper and iron losses of your motor. The iron losses are broken into eddy current and hysteresis losses.
- Convert ideal switch models into non-ideal switches and define parasitic bus inductance, common-mode capacitors, and other parasitic elements to start getting an understanding of your system's conducted EMI.
- After that, use automation again to understand the sensitivity to certain parasitic values and their impact on the differential mode and common mode noise.
- Finally, you just compare your results against your desired EMI standard to ensure compliance. If you're not compliant, use the automated filter design tool provided in the EMI Design Suite to fix it.
It almost couldn't be more convenient and easy to use.
We will demonstrate PSIM's link to Simulink as this is another typical approach to power stage design: PSIM simulates the power stage while the control is in Simulink.
PSIM functionality that we cover in this webinar:
- PSIM Motor Drive Package
- Motor Control Design Suite
- EMI Design Suite
- JMAG-RT link (MagCoupler RT module)