Greening the Future of the Automotive Industry, by Ford Technical Fellow of Sustainability Dr. Debbie Mielewski
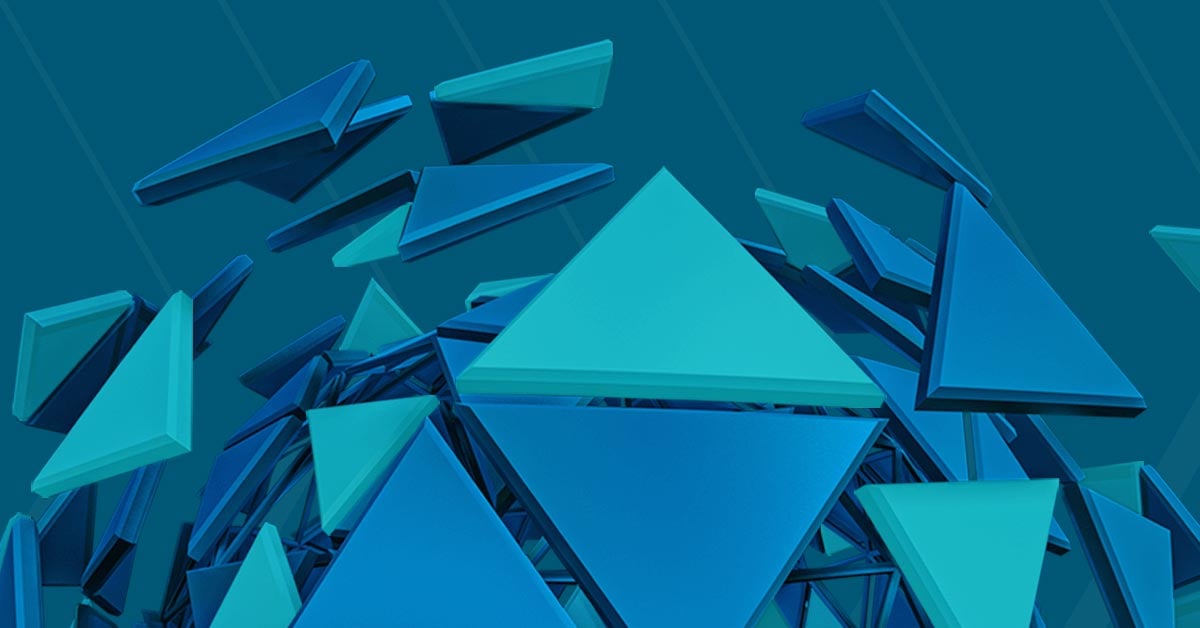
Ford's Sustainability group has worked passionately to reduce the impact of Ford Motor Company’s materials on the environment for the past 20+ years. Following a big success with developing and implementing soy-based foam in 2007, the material was migrated onto every Ford North American-built vehicle. This was the beginning of many other successes in using plant-based materials, including wheat straw bins on the Ford Flex, kenaf armrests on the Escape, rice hull wiring channels on F-150, tree-based composites on Lincoln armrests and console substrates, and even a coffee chaff composite developed in partnership with McDonald’s Corporation. These new materials offer many benefits in addition to being “greener”. They can be significantly lighter in weight, more fire resistant, have better sound and vibration absorption, provide desperately needed revenue to farmers, and help us to use our resources much more efficiently. What’s not to like?
Recently, Ford has committed to reaching carbon neutrality by 2050, with the hopes of reaching that goal even earlier. As a result, we have expanded our work on sustainable materials to include developing more sustainable manufacturing processes. I will share with you several of our early successes in sustainable materials and some new ideas in reducing Ford’s manufacturing carbon footprint and participation in the new, circular economy.
Presented as part of Altair's 2021 Future.Industry Conference.