Simulating High Pressure Die Casting with Full Process

Historically most simulations of high pressure die casting process have been done with the “biscuit” method. The biscuit method means that you are not simulating the whole process but only the shot (casting + ingate system + the biscuit), meaning that filling starts at the point where the biscuit begins.
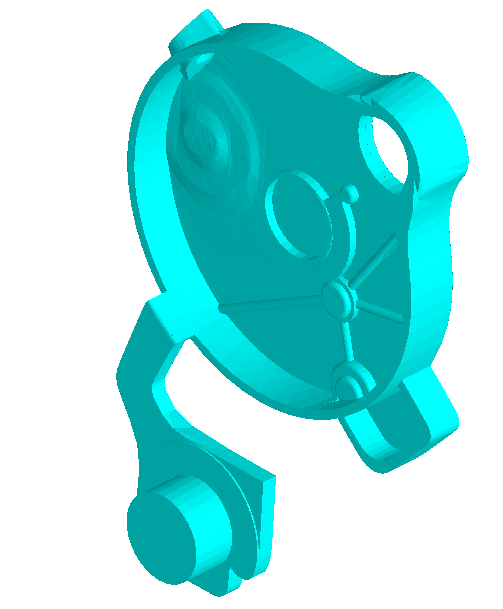
Biscuit simulation
This is a simplification that makes the simulation less accurate. The reasons for making simulations like this are:- Computer memory – A full process would need too many calculation elements and thus too much memory that was not in a normal computer. The full process adds 300 – 800mm calculation elements in x or y direction because of the length of the chamber.
- Calculations took too long to be practical with a full process.
- Many simulation programs could not properly simulate piston movement just five years ago.
- We could more accurately investigate the effect of different velocities and switch points since they now were set by millimeter piston movement instead of time or trigger points. Along with this, possible waves were detected that could potentially enclose air.
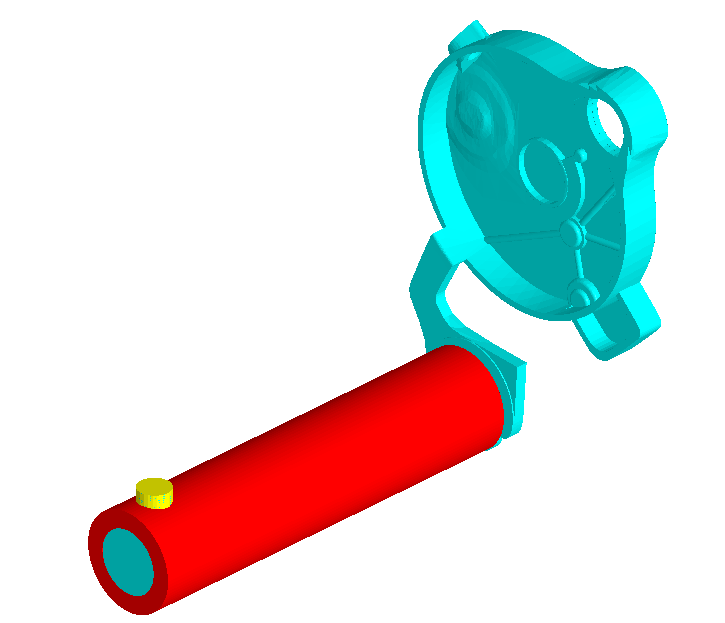
Piston movement
- Most simulation engineers have used too high pouring temperatures for their biscuit simulations. We discovered this when we started to simulate the full process with chamber filling and piston movement that the temperature drop was significantly higher than we thought. We noticed temperature drop in the chamber of up to 100°C and in some cases also over 100°C. This was later also verified at different foundries by thermocouple readings. We also found the same temperature drop in a project by the Swedish Foundry Association.
- Gas bubbles are created both during gravity filling of the chamber but also by the piston movement. These bubbles continue into the casting and contributes to the gas porosities in the casting.
- Effect of too high or too low filling ratio in the chamber could be studied. For example, a very low filling ratio results in high amount of solidification percent during the filling of the chamber.
On June 16, a webinar will be held by Johannes Jerg, founder of Jerg Engineering, addressing this part of the simulation process and namely the piston movement simulation. Register here for this webinar.