Thermal Stability of Electric Motors
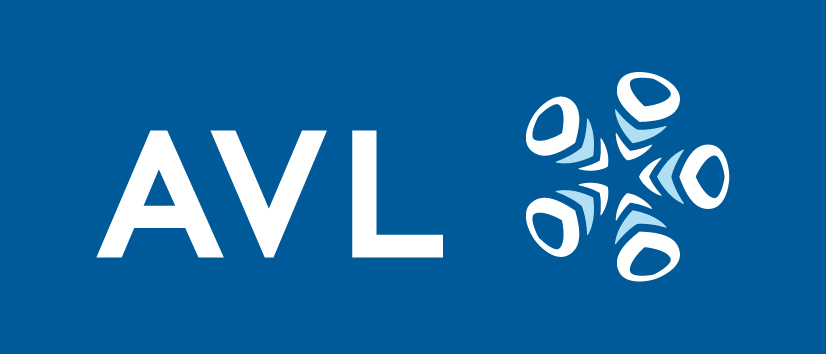
Performance and efficiency are top priorities when designing motors for electric powertrains. The electric motor development for the automotive industry faces increasing complexity regarding requirements of maximum power density and changing operating loads.
In order to meet the opposing development goals of efficiency and performance, the components of the electric motor must be designed in such a way that they can be operated at overload for a limited period of time. A deep understanding of the thermal behavior of all motor components is required to prevent failure due to overheating.
Thermal simulation is a core task in the development of electric motors. This begins with precise calculation of the electrical and mechanical losses that act as heat sources. Heat flows and temperature distributions in the motor’s structures must be taken into account as well as heat removal by the cooling medium.
The starting point of any detailed electric motor analysis is an electromagnetic calculation. AVL’s recognized simulation software AVL FIRE™ M offers the possibility to model the stator and rotor for different types of electric motors and to use this model to perform an electromagnetic field calculation. Electrical losses are then calculated from the distribution of current density and magnetic flux density.
In combination with mechanical and ventilation losses, this results in the distribution of the power dissipation densities, which serve as heat sources in the thermal analysis. In order to keep the local temperatures in the windings and magnets within the material limits, different cooling concepts are investigated. Cooling water jackets in the stator housing are widely used. However, recently oil splash cooling of the end windings and direct oil cooling in the entire winding area are becoming increasingly popular for electric motors integrated in the gearbox.
For the thermal calculation, a multi-domain model is created which includes the regions of the cooling media as well as the structural components. It allows the simultaneous calculation of the transient flow of gases and liquids, the heat transfer between fluids and structural components, and the heat transport in solids.
AVL FIRE™ M supports the fast generation of such a model with its fully automatic polyhedral mesh generator. The thermal calculation provides a detailed three-dimensional temperature field of the model and helps discover weaknesses of the cooling concept. Since operating temperatures vary in different locations, this can also influence the electromagnetic behavior of the electric motor. An exact analysis requires a tight coupling of electromagnetic and thermal calculations. The automated interface in the software facilitates this step and saves time for the calculation engineer. Due to the typical long simulation times needed for 3D calculations, this model is not suitable for a thermal simulation of a complete drive cycle.
AVL has developed a workflow that creates an AVL CRUISE™ M system simulation model out of the 3D equivalent in just a few steps. The input parameters are adjusted on the basis of the results of the 3D model. The model calibrated in this way also allows the temperature of all relevant electric motor components to be calculated quickly, but accurately for the complete range of different operating conditions. Due to real-time capability, the system model is not only suitable for the office, but also for hardware-in-the-loop and test bed use.
The result of AVL’s efforts is a fully comprehensive and detailed modelling solution for the development of electric motors that supports optimum performance, while promoting component durability at all levels of operation.