Chasing Reliability in Electronic System Design
Designing and manufacturing an electronic device that works reliably over its entire useful life is a harder challenge than it seems. Consumers simply expect that devices turn on and work every time without much thought to the complex systems that enable these miniature marvels to function. In the fast-paced electronics industry, delivering products that both excite consumers and work consistently and reliably under a variety of conditions involves a delicate dance of complex variables.
So, what are the key factors that electronic system designers scrutinize in order to design, validate, and test the reliability and robustness of devices? And what tools and workflows can these designers turn to for improving the accuracy of their predictive models, reducing the number of design iterations they produce, and increasing the speed with which they gather insights and optimize their designs?
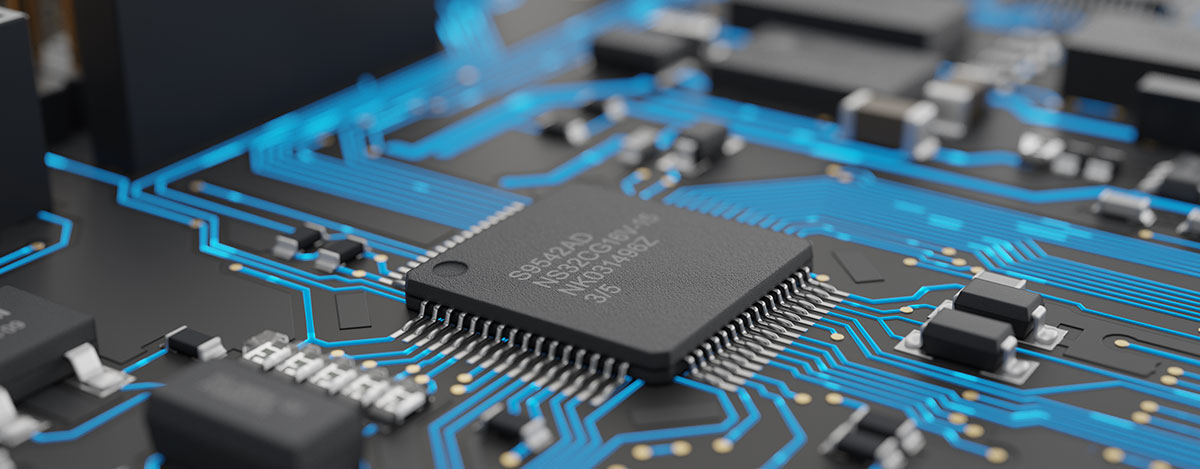
What makes electronic systems fail?
The cause of electronic system failure can take many forms, some of which may not present themselves in physical testing. Though a product may pass its final tests after manufacturing, the system could fail months or years later due to prolonged stress.
Common causes of electronic system failure include:
- Component or design issues
- Excessive heat
- Vibration
- Electromagnetic interference
- Signal or power integrity
- PCB assembly or PCB fabrication issues
Reliance on lab and field testing alone is not sufficient to ensure a robust and lasting product. Simulating years of stress is very difficult to represent accurately in test chambers and creating multiple prototypes can drastically impact time-to-market and development costs.
How can designers ensure reliability?
Simulation-driven design is a proven approach to reduce the risk of electronic system failure, helping to simulate events in hours that may take years to emerge in the field. Virtual prototyping can predict issues across the entire gamut of device performance, including signal integrity, power integrity, thermal management, vibration, shock analysis, and DFM/DFA validation.
In addition, design quality can be improved by integrating verification and electrical rule checking across the design process. Automating “best practice” design reviews early and throughout the development process helps designer engineers find problems earlier, addressing first-order verification tasks while offloading work typically assigned to domain specialists.
Improving PCB development at Samsung SDI
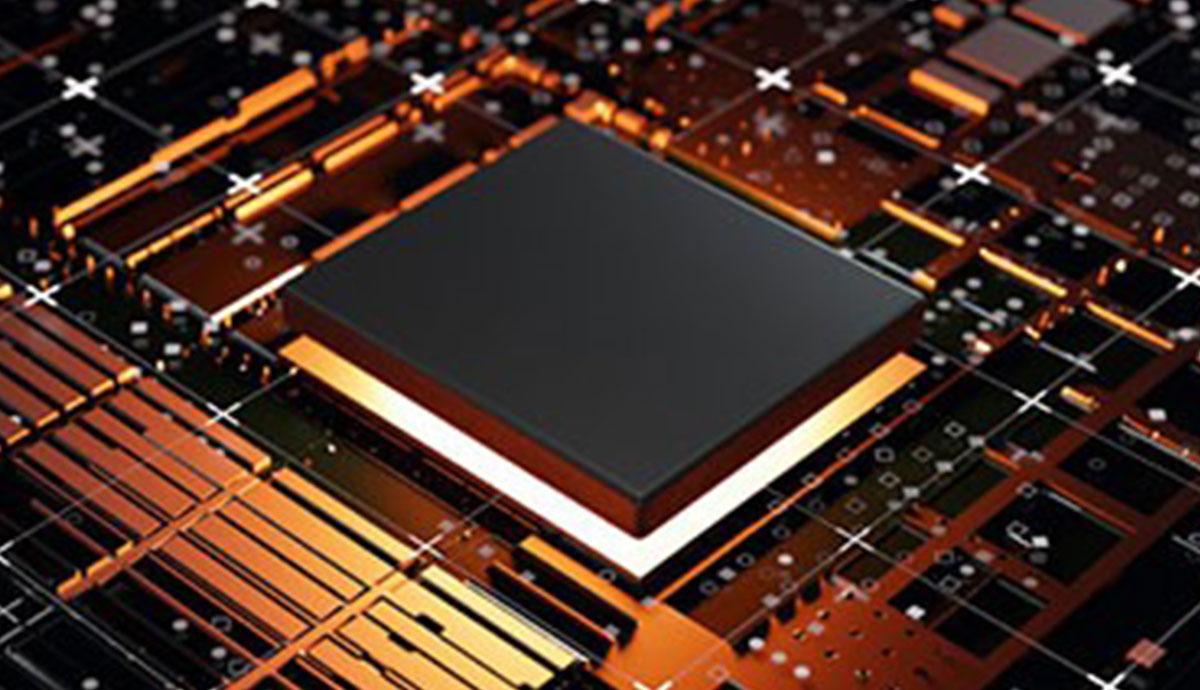
Samsung SDI is a global market leader in the high technology and environmental battery industry. Headquartered in South Korea, Samsung SDI has a 40-year history in the electronics industry and is now a top provider of energy and materials for rechargeable batteries.
When Samsung SDI transitioned to the electronic materials business, several challenges surfaced that needed to be addressed. The company had to move from digital display control circuits to battery control circuits, requiring a different approach to new electronic designs and related printed circuit board (PCB) manufacturing technologies.
A strong solution for PCB design review and verification was needed for existing and new products. Also, after acquiring a key player in the automotive battery pack business, Samsung SDI needed a solution that could setup and deploy PCB design review and verification where the design rules and user environment were centrally managed.
Samsung SDI chose to implement Altair PollExTM, an electronics simulation-driven design tool, to help ensure their design teams could consistently meet timing, performance, reliability, and compliance targets. PollEx provided an efficient collaboration environment that could be used by multiple teams within the organization. With this environment in place, PCB artwork engineers could upload PCB layout designs to a PDM server, allowing all engineers to then review the PCB designs while running PCB verification. Collaborating from a central location, Samsung estimated that this new PCB design review and verification process could save them six million USD a year thanks to a reduction of design iterations from 20 to nine and number of revision checks from six to three.
Read more about the Samsung SDI story
PollEx makes it easy to review and improve PCB layouts earlier and drive robust designs with fast simulation tools for signal integrity, power integrity, thermal, EMI vulnerability and ESD protection, and more without relying on “rules of thumb." With unsurpassed connectivity to all the major ECAD systems, discover how PollEx fits into your existing tool chains.
We invite you to join Altair’s ESD webinar series to learn more about the latest tools and strategies leading companies are using to improve their electronic system design processes. The first presentation, hosted by EE Times, covers solutions for electronic system reliability.