IoT in Development and Production
Buzzwords such as IoT and Digital Twin are not new to the digital world. They have been gaining momentum in development and production discussions as the digital transformation of production becomes more relevant. But how is it possible to truly integrate the internet of things in development and production and what are the benefits of connected products? While there is still debate over whether consumers are interested in having a “smart refrigerator” collecting data to order milk, matters are quite different for a manager in an industrial facility. Data collected in this sector can lead to more efficient processes and offer forecasts on maintenance intervals, the remaining lifespan of a product, or its functional safety.
Internet of Things
The term “Internet of Things” was first coined in the 1980’s but has gained significant traction over the last 10 years. It defines a series of physical objects (cars, refrigerators, phones, smart watches, etc.), or “things,” that are connected and able to collect and exchange data. Sensors and actuators embedded allow the devices to communicate with each other and collect data about themselves. The Internet of Things is a networks of connected devices and gateways constantly collecting and sending data.
Digital Twin
Digital Twin is a trend that keeps progressing. It is becoming instrumental in product development and throughout the entire product lifecycle. Looking at current digital product development, it may seem like the idea of digital twin has been around longer. Now the question is what turns a digital development model into a real digital twin? In an Altair Altair webinar series, Altair described its vision of IoT and digital twins as, “To turn a digital development model into a Digital Twin, data of the operating system needs to be collected and be fed into the virtual model, enable precise predictions and hence help to make future products even better. Together, digital twin and IoT have the ability to accelerate the development and production process.
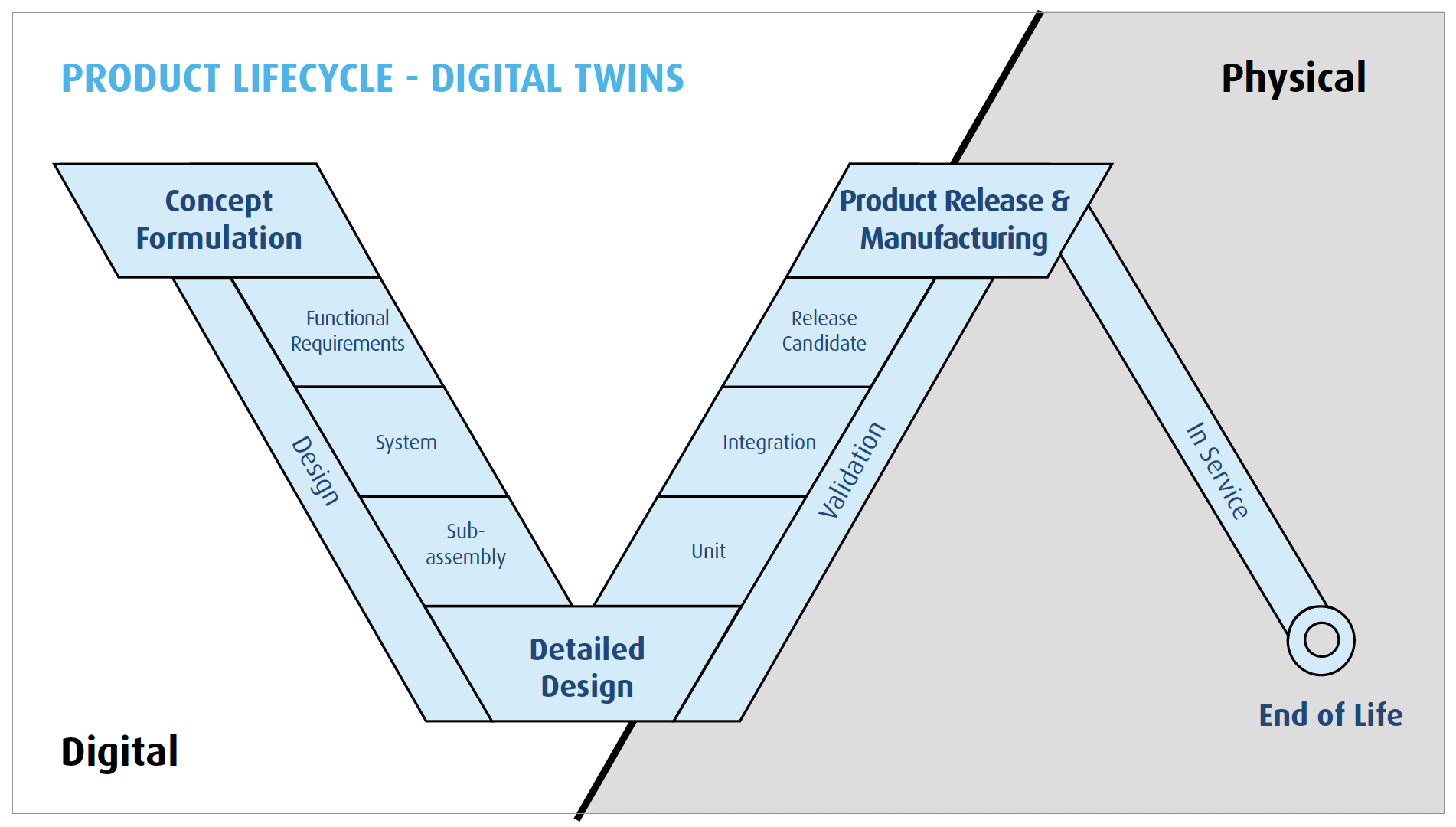
Virtual Model
With a traditional background in virtual product development and simulation, Altair offers several tools that can be used to develop a market ready product. At Hannover Messe, Altair presented a virtual, IoT enabled cobot (collaborative robot) along with the entire development process of such a device.
In the development of a cobot, or a similarly complex product, it is very important to consider the entire mechatronic system. This includes structure, sensors, actuators with dynamic controls and electromagnetic compatibility. When using industrial cobots, workplace safety is first priority. Safety can be achieved with lighter structures. Lighter structures and lighter components lead to less inertia, enhance the robot's arm performance and increase the durability of the system. In addition, a cobot must "consider" physically interacting with people when working side by side in the same environment, which adds to the complexity of the movement commands.
To fulfill all these requirements in product development and to design the multidisciplinary system of a cobot, Altair used its broad portfolio of CAE (computer aided engineering) tools. Among these tools are Altair Activate, for a model-based development approach, Flux, used for the design of electrical actuators and to assess the occurring electromagnetic and thermal phenomena, Altair's CFD Solver AcuSolve, for analyzing thermal conditions and OptiStruct, to optimize the structure and to remove undesired vibrations. In the development process of the cobot technology demonstrator, Altair also analyzed local effects (mechanical and electrical loads, thermal effects etc.) and combined Flux and Activate to design the complex cobot motor. This was done in order to study the interaction between electromagnetic systems, such as motors, actuators, and sensors. The antennas needed for the cobot to communicate with the internet or other devices, were developed with FEKO, Altair's EM solver. Winprop was also used to design the radio network and to ensure an efficient wireless communication.
Digital control algorithms play another key role when developing cobots. Altair Embed, with its broad tool portfolio for control system development, includes Software-in-the-Loop, Processor-in-the-Loop, and Hardware-in-the-Loop simulations and helps engineers develop these algorithms. From a control diagram, Embed also automatically generates real-time ready microprocessor code which can be used via a micro controller. This enables designers to set up and run an efficient and precise control strategy and to interactively update the control parameters.
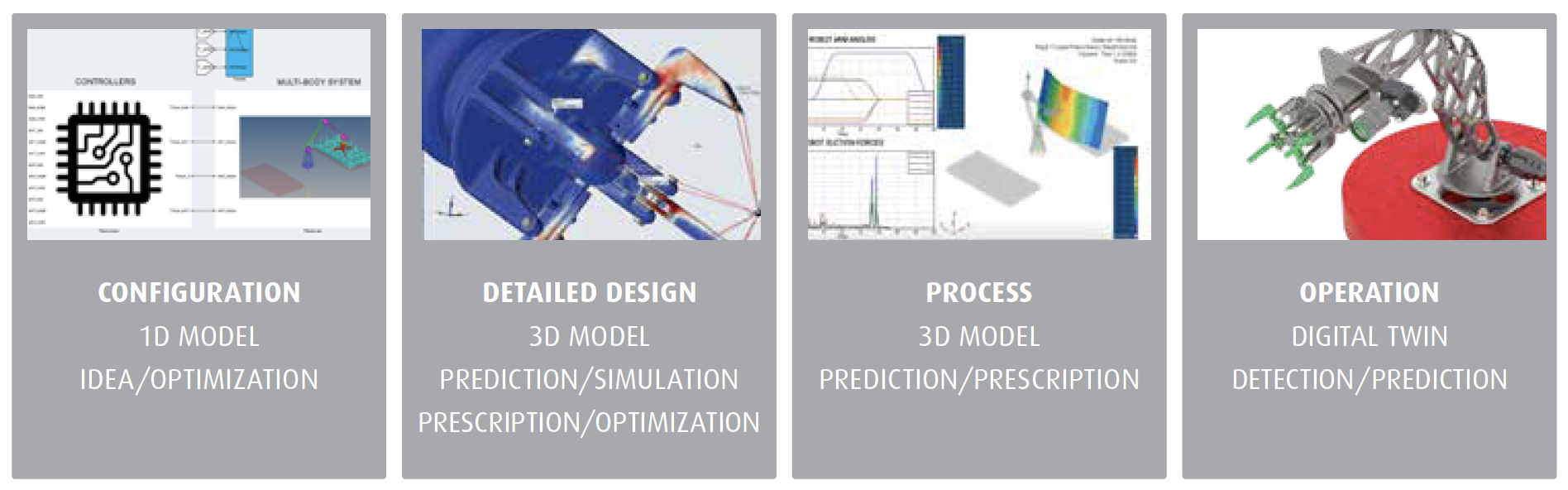
From Virtual Model to Digital Twin
Whether working with a cobot, vehicle or airplane engine, it is possible to create a product model that is very close to reality, thanks to coupling the physical with the virtual model.
The next step in creating a Digital Twin is to send operating data into the validated simulation model. The insights gained here are used for more than as just a tool to verify the development model. Considering operating data in a validated simulation model allows for conclusions to be drawn about the current state of the real product in operation. It also allows for predictions to be made concerning possible maintenance problems or failure (i.e. about the remaining lifetime of an engine). In addition to a representative original model, this process, known as Predictive Modeling, requires several steps to come to full fruition. These steps include:
A Digital Twin, created with these parameters in mind, offers valuable insights into a product currently in operation. What is more, it enables predictions about failure risk, functional safety, and durability of that specific product. The virtual prototype knows the ideal state of the product and therefore becomes a prediction tool for that product across its entire life cycle.
Pave the Way for Digital Transformation
The two basic factors when implementing strategies for a digital transformation are integration and transparency of information. Only in this way can sensor data be used to broaden digital models and to create a virtual image of the real world. In addition, technical assistance systems help to assess, visualize and communicate the newly gained information to make educated decisions and to be able to solve problems faster. The systems may operate autonomously and apply their own measures or delegate tasks, such as interference or conflict of interests, to a higher authority.
The expansion of virtual prototypes has come a long way since the first use of development models. Now, digital data is collected from sensors during operation and derives prediction models. Not only do digital twins offer the opportunity for the next step towards true to reality simulation models, they create the opportunity to make predictive models and build better products. Moreover, the resulting Digital Twin offers the opportunity to make predictions in relation to operative enhancements of machinery and facilities across the entire lifecycle of a product. This will become obvious in earlier and more cost-efficient decisions regarding maintenance, operation risks, and live span and will therefore offer a clear competitive advantage for companies from all industries.
Internet of Things
The term “Internet of Things” was first coined in the 1980’s but has gained significant traction over the last 10 years. It defines a series of physical objects (cars, refrigerators, phones, smart watches, etc.), or “things,” that are connected and able to collect and exchange data. Sensors and actuators embedded allow the devices to communicate with each other and collect data about themselves. The Internet of Things is a networks of connected devices and gateways constantly collecting and sending data.
Digital Twin
Digital Twin is a trend that keeps progressing. It is becoming instrumental in product development and throughout the entire product lifecycle. Looking at current digital product development, it may seem like the idea of digital twin has been around longer. Now the question is what turns a digital development model into a real digital twin? In an Altair Altair webinar series, Altair described its vision of IoT and digital twins as, “To turn a digital development model into a Digital Twin, data of the operating system needs to be collected and be fed into the virtual model, enable precise predictions and hence help to make future products even better. Together, digital twin and IoT have the ability to accelerate the development and production process.
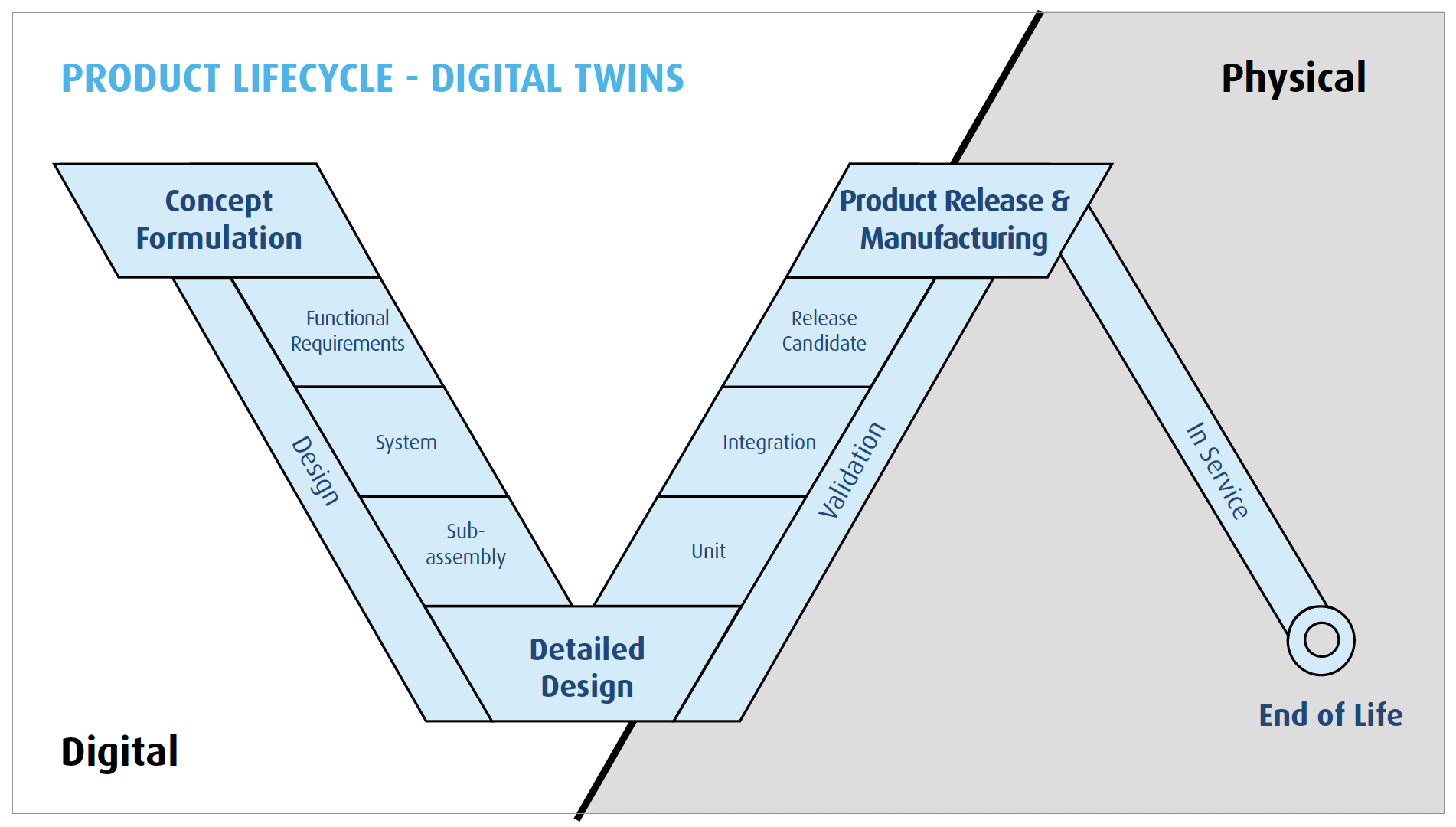
Virtual Model
With a traditional background in virtual product development and simulation, Altair offers several tools that can be used to develop a market ready product. At Hannover Messe, Altair presented a virtual, IoT enabled cobot (collaborative robot) along with the entire development process of such a device.
In the development of a cobot, or a similarly complex product, it is very important to consider the entire mechatronic system. This includes structure, sensors, actuators with dynamic controls and electromagnetic compatibility. When using industrial cobots, workplace safety is first priority. Safety can be achieved with lighter structures. Lighter structures and lighter components lead to less inertia, enhance the robot's arm performance and increase the durability of the system. In addition, a cobot must "consider" physically interacting with people when working side by side in the same environment, which adds to the complexity of the movement commands.
To fulfill all these requirements in product development and to design the multidisciplinary system of a cobot, Altair used its broad portfolio of CAE (computer aided engineering) tools. Among these tools are Altair Activate, for a model-based development approach, Flux, used for the design of electrical actuators and to assess the occurring electromagnetic and thermal phenomena, Altair's CFD Solver AcuSolve, for analyzing thermal conditions and OptiStruct, to optimize the structure and to remove undesired vibrations. In the development process of the cobot technology demonstrator, Altair also analyzed local effects (mechanical and electrical loads, thermal effects etc.) and combined Flux and Activate to design the complex cobot motor. This was done in order to study the interaction between electromagnetic systems, such as motors, actuators, and sensors. The antennas needed for the cobot to communicate with the internet or other devices, were developed with FEKO, Altair's EM solver. Winprop was also used to design the radio network and to ensure an efficient wireless communication.
Digital control algorithms play another key role when developing cobots. Altair Embed, with its broad tool portfolio for control system development, includes Software-in-the-Loop, Processor-in-the-Loop, and Hardware-in-the-Loop simulations and helps engineers develop these algorithms. From a control diagram, Embed also automatically generates real-time ready microprocessor code which can be used via a micro controller. This enables designers to set up and run an efficient and precise control strategy and to interactively update the control parameters.
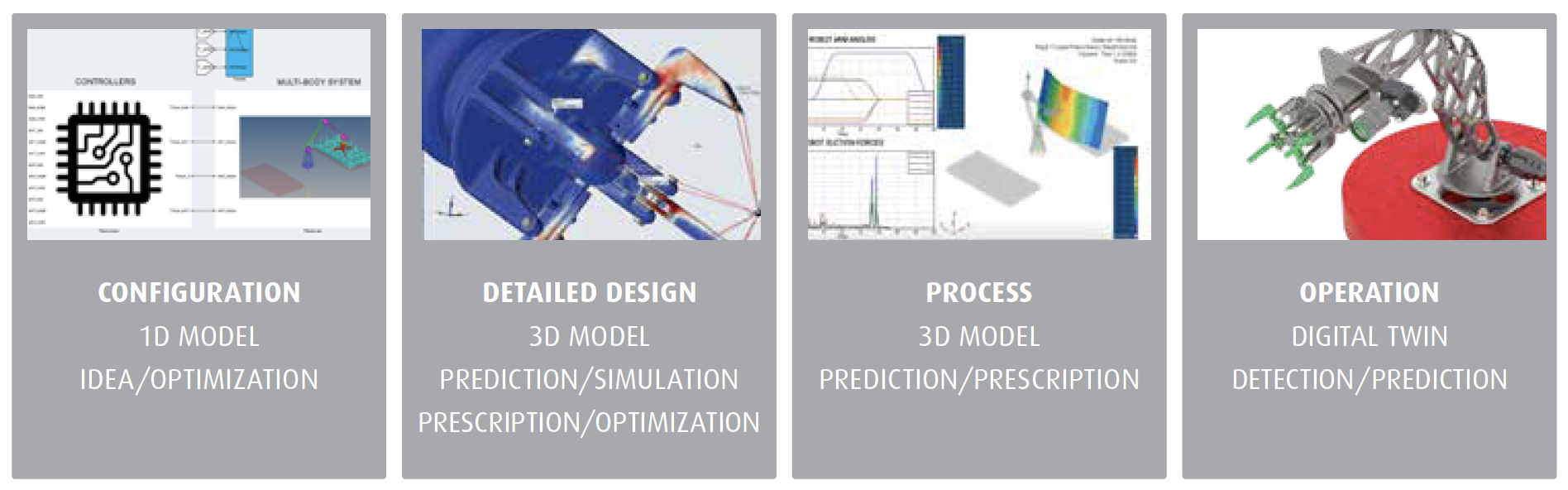
From Virtual Model to Digital Twin
Whether working with a cobot, vehicle or airplane engine, it is possible to create a product model that is very close to reality, thanks to coupling the physical with the virtual model.
The next step in creating a Digital Twin is to send operating data into the validated simulation model. The insights gained here are used for more than as just a tool to verify the development model. Considering operating data in a validated simulation model allows for conclusions to be drawn about the current state of the real product in operation. It also allows for predictions to be made concerning possible maintenance problems or failure (i.e. about the remaining lifetime of an engine). In addition to a representative original model, this process, known as Predictive Modeling, requires several steps to come to full fruition. These steps include:
- Goal definition
- Data capture and analysis, with data limited to parameters that meet the target
- Predictive Modeling / Beginning with simplified models and a step by step increase in complexity
- Predictions regarding the remaining lifespan
A Digital Twin, created with these parameters in mind, offers valuable insights into a product currently in operation. What is more, it enables predictions about failure risk, functional safety, and durability of that specific product. The virtual prototype knows the ideal state of the product and therefore becomes a prediction tool for that product across its entire life cycle.
Pave the Way for Digital Transformation
The two basic factors when implementing strategies for a digital transformation are integration and transparency of information. Only in this way can sensor data be used to broaden digital models and to create a virtual image of the real world. In addition, technical assistance systems help to assess, visualize and communicate the newly gained information to make educated decisions and to be able to solve problems faster. The systems may operate autonomously and apply their own measures or delegate tasks, such as interference or conflict of interests, to a higher authority.
The expansion of virtual prototypes has come a long way since the first use of development models. Now, digital data is collected from sensors during operation and derives prediction models. Not only do digital twins offer the opportunity for the next step towards true to reality simulation models, they create the opportunity to make predictive models and build better products. Moreover, the resulting Digital Twin offers the opportunity to make predictions in relation to operative enhancements of machinery and facilities across the entire lifecycle of a product. This will become obvious in earlier and more cost-efficient decisions regarding maintenance, operation risks, and live span and will therefore offer a clear competitive advantage for companies from all industries.