Preventing Crash Injury with Advanced Sports Simulation
Some may say Winter Olympic sports are some of the most dangerous. Take the sled sports, for example. These include skeleton, luge, and bobsledding. In skeleton and luge, athletes have nothing but a helmet protecting them from the course. In bobsledding, the sled gives athletes some additional protection, but it doesn’t take away the fact they’re careening down a slick, winding, and unforgiving course.
Physical protection aside, bobsled racers reach some of the highest speeds in their sport. As of 2019, the fastest bobsled reached 97 mph (156 kph) by a 4-man sled team at the BMW IBSF World Championships in Whistler, British Columbia.
Of course, these athletes train extremely hard, physically and mentally, to prepare for races and reach the finish line without any serious collisions. In bobsledding, the difference between a win and loss can depend on fractions of seconds.
At the beginning of races, racers must gain as much initial speed as possible and strategically distribute their weight in the heavy sleds to successfully navigate course turns. A false move can result in a collision, which can be devastating to the racer’s time and the racer’s safety. With virtual testing technology and a simulation-driven design approach, design teams can simulate these types of performance scenarios for highly nonlinear problems under dynamic loadings.
Using Altair® Inspire™, our team previously simulated the topology optimization of a bobsled using motion loads. We decided to further investigate this work to learn not only how to optimize a bobsled’s design, but how to make it as protective as possible it in the event of a major crash. First creating the model, we used Altair® Radioss® to simulate two bobsled crashes and the type of injury risks that can accompany this high-speed sport without proper training.
Creating and Validating the Bobsled Model
First, we exported the initial Inspire model into Altair® HyperWorks® and then meshed it with the Altair® HyperMesh® tool.
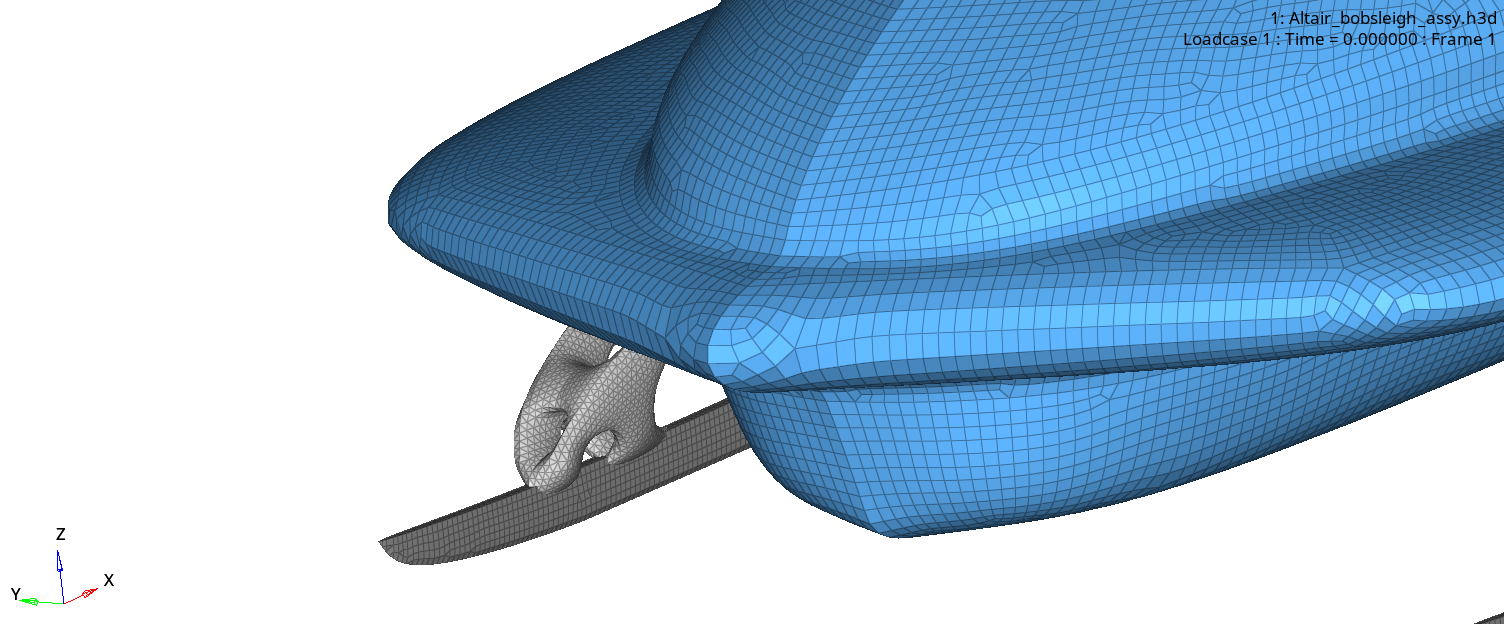
A bobsled’s core structure consists of a steel frame and a hull that’s closed in the front and open in the back. To adhere the cover and the reinforcement frame of the bobsled in HyperMesh, we created a welding line to connect the pieces. Next, we connected each rear axis to the reinforcement frame and defined a cylindrical joint between the front axis and the frame. The front runners on the sled need to be mobile enough so the pilot can steer the sled.
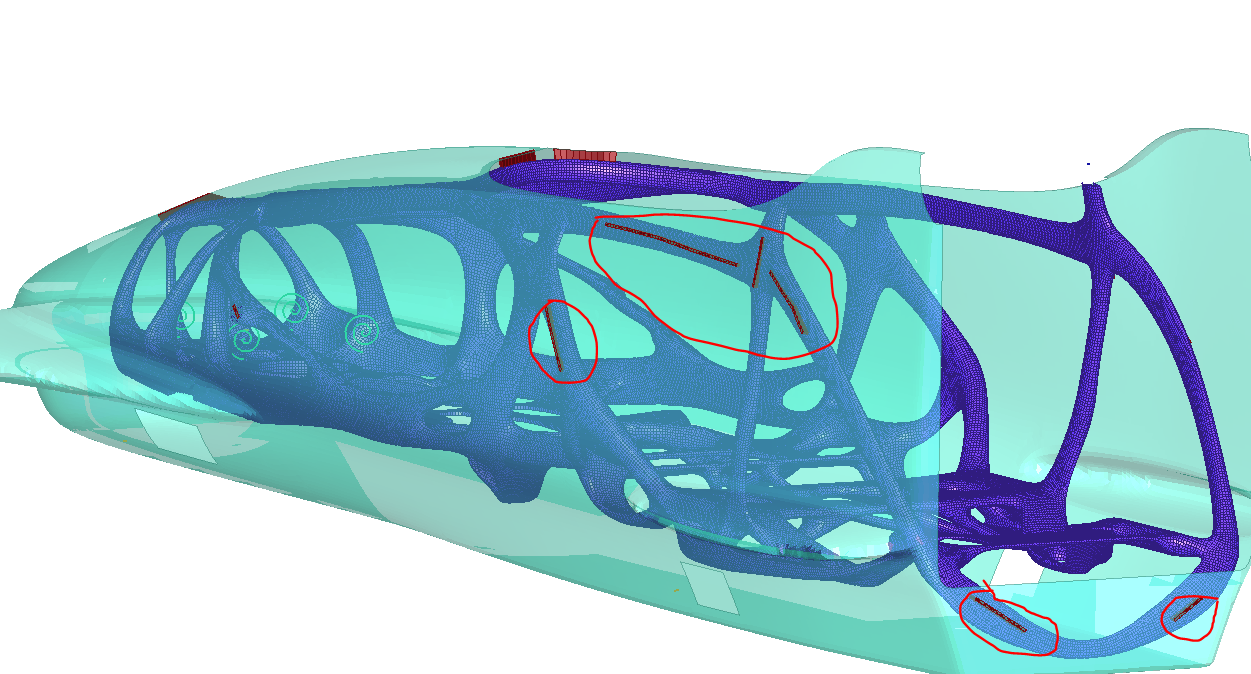
Next, we created contacts in HyperWorks, then defined in specific areas in order to handle the interactions between the sled’s different parts. When selecting design materials, it was assumed that only the sled cover and reinforcement frame were deformable. We used this assumption because in a crash, only these parts would significantly contribute to the occupant’s protection. We modeled the frame with aluminum and the cover with composite material.
Beside the speed, weight, and precision of the athletes on the course, the composition of the sled itself plays a major role in the sport. The introduction of lightweight materials like composites and carbon fiber has led to more agile, aerodynamic sleds that can accelerate quicker and reach higher top speeds.
Before running the crash scenarios, we put a simple load case and crash scenario into action to ensure the model would act as expected. After verifying, it was time to load the virtual crash dummies into the sled.
Positioning the Dummies
The pre-simulation model was generated with the HyperWorks positioning module, and we ran the models using Radioss. We positioned the dummies in the bobsled using postures compatible with bobsled occupant stature. After that, we defined contact interfaces between the dummies and the bobsled.
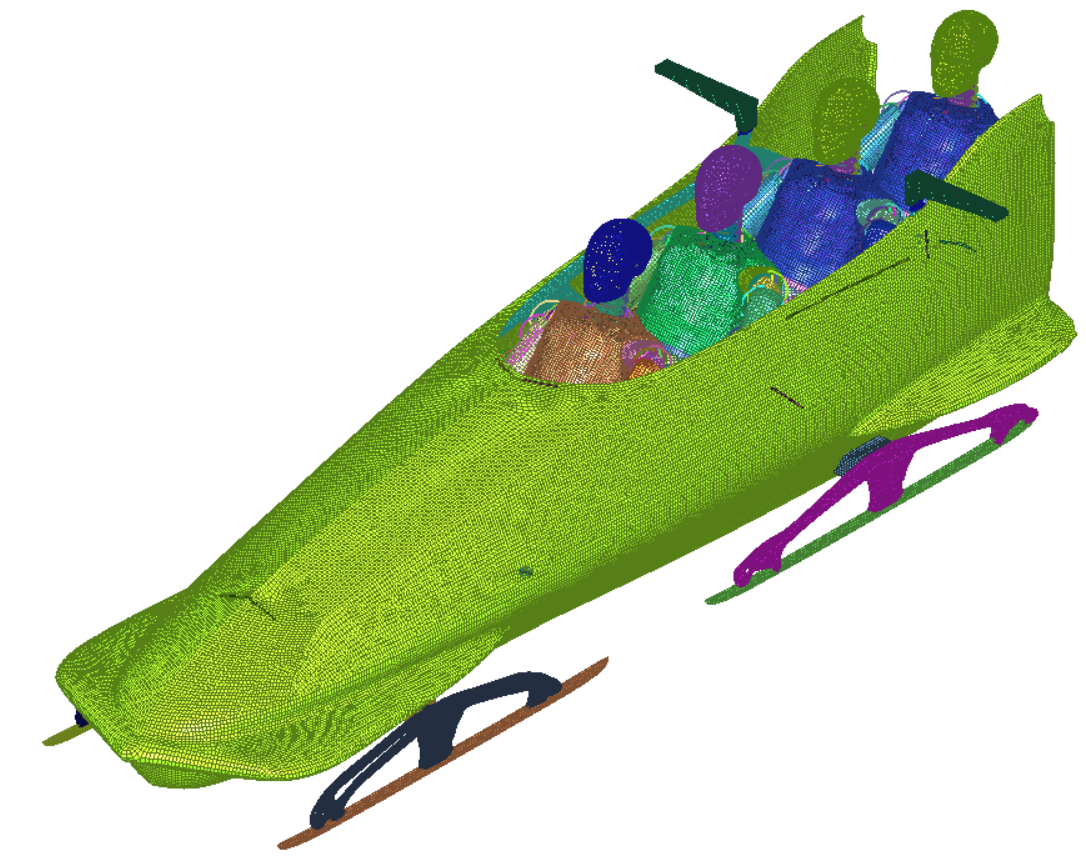
Simulating Crash Scenarios on the Track
We evaluated two scenarios in the project: a side wall impact and a step impact. The side wall impact scenario investigated what would happen if the athletes lost control of the sled, leading to an impact against the edge of the track. The step (low-height obstacle) impact observed the presence of an unexpected obstacle on the track, such as debris or uneven ice on the track from a previous run. We assessed occupant injuries from the crashes using standard injury criteria.
Scenario 1: Side Wall Impact
Looking at the crash kinematics, we could see that all occupants remained in the bobsled after the side wall impact, although the rear occupant suffered the most severe impact. Note that we exaggerated dummy positioning to better visualize the crash impact; in a real race, bobsled racers sit further down into the sled to minimize drag.
Next, we computed the dummy injury criteria with Altair® HyperGraph®. The criteria and threshold we used were defined by safety regulations in the field of automotive crashes.
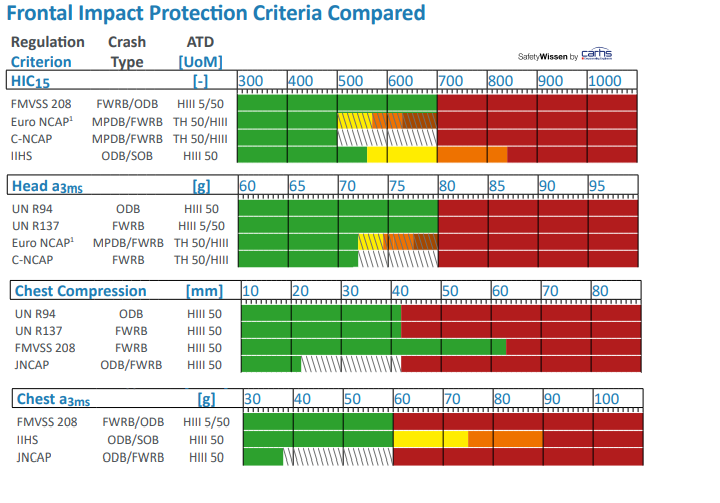
The dummies’ positioning was extremely important to observe. At the back of the sled, the dummies hit the wall more violently, experiencing severe impact due to the higher inertia load. Dummies behind the pilot all suffered damage to the head, and the head injury criterion (HIC) and the a3ms (highest amplitude of acceleration that lasts at least 3 milliseconds) calculated with HyperGraph showed that the injuries exceeded the recommended limit. This is why all racers use protective headgear.
The injury criterion also revealed that the two dummies at the back of the sled also suffered chest injuries. Because bobsledding uniforms are designed to be lightweight, flexible, and skintight, they lack bodily protection. With tools like Radioss, equipment designers can understand where to reinforce equipment such as bobsleds to protect vital areas of the body.
Crash Scenario 2: Step Impact
In this crash scenario, the bobsled encountered a short obstacle on the track. Before races begin, crews of track workers smooth out these stretches of ice to prevent impacts like these from occurring. It's necessary to level the tracks for high-speed racing because even a tiny bump or divot of less than 2 centimeters can endanger the athletes.
HyperView simulations showed that there was a significant vehicle ejection risk in this type of accident. Depending on its severity and where the occupant is located on the track, this accident could be deadly.
Conclusion
These examples show how bobsled teams and bobsled designers can use simulation-driven design to explore multiple designs and scenarios without the need for iterative re-runs and physical testing. In sports like bobsledding, where athletes can suffer significant injury resulting from poor design or an equipment malfunction, advanced simulation makes it effective to study multiple design scenarios at once – all in one platform.
Access to this type of simulation and optimization technology allows engineers to predict and prevent design failures before products meet the market, from sports to the automotive industry. With Radioss, engineers can evaluate and optimize product performance for vehicle crash and safety, shock and impact, and high-velocity impacts. As a versatile and comprehensive environment for accurately predicting crash responses, Radioss enables engineers to gain crucial insights into the manufacturability of complex designs. To learn more, visit https://www.altair.com/radioss/.