The TRICK to Digital Twin Technology Adoption
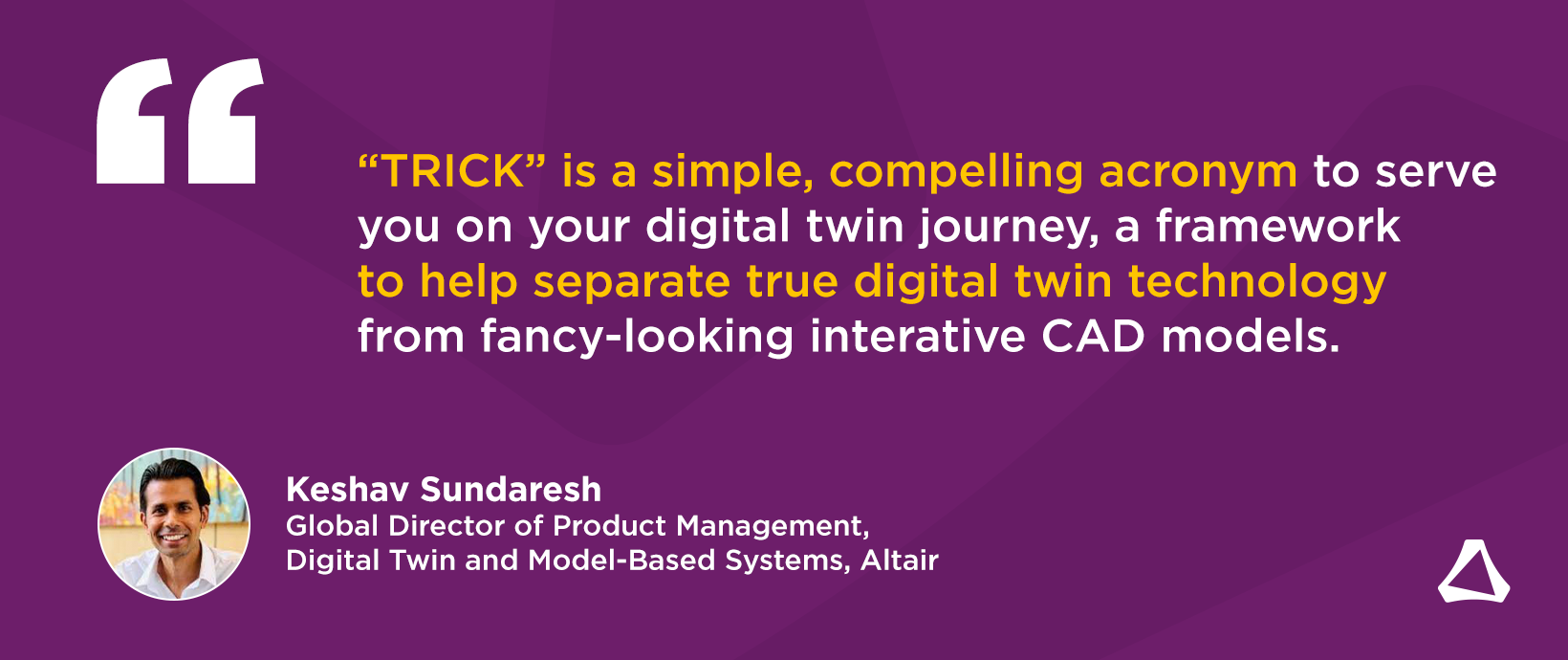
Look around you. The device you’re reading this on right now is one of many machines, devices, and tools that surround you and support your everyday life – at work and outside. At Altair, we say our technology is always around you – even when you’re not conscious of it – keeping you safe, connected, and empowering you to thrive in today’s fast-paced world.
But what, exactly, do we mean by that? How is our technology integrated into both consumer goods like smart electronic devices, vehicles, and light fixtures as well as industrial objects like assembly lines, sensors, and wind turbines? The answer is digital twin technology, which has a powerful, wide-ranging impact in business and beyond. What can digital twin capabilities mean for your business?
Digital twin capabilities:
- Drive operational efficiency
- Facilitate a model-based ecosystem, providing access to authoritative data and knowledge for faster, better decision-making
- Drive superior engineering quality and product development performance
- Flatten the disruption curve for production
Digital Twin Took Center Stage at CES 2024
Altair has been talking digital twin for years. But it’s not just Altair and myself that believe in digital twins – my recent experience at CES 2024 was more than enough proof of that. At this year’s event, digital twin-related booths, presentations, and demonstrations were ubiquitous. It seemed like every organization – no matter their specialty, industry, or size – was talking about digital twin capabilities and showcasing what they were doing (or planned to do) with the technology.
Five years ago, a scant few were talking about digital twin technology, let alone creating it. The technology just wasn’t there; people liked the concept of digital twin, but the reality was Frankenstein-ish. Very few companies then had the open architecture-based, flexible, and purpose-driven workflows necessary to implement digital twin capabilities. But now digital twin is firmly in the spotlight.
Today, the prevalence of accessible, intuitive data and high-performance computing (HPC) environments – like Altair’s – has changed the digital twin adoption landscape. Now, instead of a hodgepodge of solutions and environments, digital twin is more akin to a living and breathing dynamic system with a single, unbroken thread.
Digital twin capabilities have also boomed because people (executives in particular) are finally seeing their true business value. They concretely understand that digital twin can transform their business and propel them into a streamlined, digitalized future. It’s safe to say that these organizations wouldn’t be putting the time, effort, and creativity into showcasing digital twin capabilities at events like CES if they weren’t betting big.
However, there are still plenty of organizations – too many, in my opinion – that don’t understand what digital twin technology is and how they can start harnessing its power. Luckily, there’s a TRICK to digital twin – literally.
Why "TRICK"?
“TRICK” is a simple, compelling acronym to serve you on your digital twin journey. TRICK is neither sequential nor mutually exclusive. It’s merely a framework to help separate true digital twin technology from fancy-looking interactive CAD models, which are not digital twins but rather mere digital shadows. Without further ado, let’s explore the TRICK to digital twin technology.

T: Think in Systems
Digital twin technology is defined – literally and metaphorically – by its function as a system of systems. Digital twin technology is not merely the sum of its parts, a collection of a bunch of components, processes, and systems. Rather, it’s the interaction of all these things acting as one in a holistic environment.
Think of it this way: Imagine you’re tasked with building the best car in the world. To accomplish this, you can mix and match components and systems from any kind of car in the world. Maybe you want your car to have the body of a Maserati, the propulsion system of a Tesla, the infotainment console of a GMC, the steering of a Mercedes-Benz, the seats of a Lexus, and so on. If you threw all these disparate systems into a single car, do you think you’d have the “ultimate” car? You wouldn’t. Why not? Because these sophisticated mechanisms aren’t like Legos that you can just slot in at will, regardless of the pieces’ context. These are complex systems designed to function on their own and as part of a specific, holistic system – that holistic system being a vehicle model, in this case. This same principle applies to wind turbines, semiconductor capital equipment, aircraft, and so on.
Digital twin technology enables us to better understand and improve interactions between components and how they function. Everything lives in the spaces where systems interact. Engineers and designers should always be thinking at this level to minimize issues and maximize efficiency.
Customer evidence: “Leonardo Deploys Digital Twin to Capture In-Flight Behavior of Helicopter Radar”
R: Reduced-Order Modeling
When we want to share insights broadly, we want things to be as simple and actionable as possible. Real-life processes are often incredibly complex and hard to distill into a model or equation. But the beauty of mathematics is that it allows us to abstract, simplify, and standardize real-world knowledge. This is the goal of reduced-order modeling (ROM).
For people to scale their insights and unlock digital twin breakthroughs, they can’t be bogged down in messy, voluminous data. ROM helps reduce the computational complexity of models in physics-based or statistical simulations. Some of our solutions in Altair® HyperWorks®, our design and simulation platform – such as Altair® physicsAI™ and Altair® romAI™ – specialize in ROM within physics-based and test environments. And Altair® RapidMiner®, our data analytics and AI platform, offers targeted, powerful capabilities for all other kinds of data. But these are just two sides of the same coin.
Importance of Explainable, “White Box” Solutions
No matter how you approach ROM, you should always be using explainable, transparent solutions, otherwise known as “white box” solutions. White box solutions allow you to see exactly how AI-based models and algorithms are working, including:
- Metadata sources
- What datasets were used
- What underlying equations were used
This approach gives you greater insight and makes it clear to everyone throughout development how models are functioning and why. This is compared to “black box” solutions, which offer AI capabilities but are fully hidden from users – unexplainable, in other words.
Customer evidence: “Leveraging AI to Improve Accuracy in a Real-Time Hardware Application”
I: Integrate
Digital twin approaches work best when all users – including people without specialized engineering and data skill sets and non-coders – can leverage advanced tools without needing to rely on experts or support teams. This requires formalizing and democratizing computational intelligence.
With integrated digital twin capabilities, teams can virtualize products, processes, and equipment by integrating the best available models informed by sensor and metrology data, guided by domain knowledge, bolstered with software and hardware compute, and continuously synchronized with physical counterparts.
Customer evidence: “Digital Twin Slashes Waste 15% and Runtime Hours to Seconds”
C: Convergence is Key
Digital twin is a living, breathing model of systems that is grounded in physics assimilating data from inspections, sensors, etc. These systems can be physical, biological, or business process-related. Developing and sustaining a digital twin ecosystem that connects the infrastructure, environment, and methodology (tools, methods, and processes) requires the convergence of simulation, HPC, Internet of Things (IoT), and AI.
Being able to offer this in a single, unified environment is what has helped Altair deliver the market’s premier digital twin offering. Regardless of what industry you’re in or what product or system you want to model, we provide one total digital twin solution that optimizes workflows from concept to real-time in-service operation.
Customer evidence: “Harnessing the Power of Big Data, AI and Simulation to Accelerate Product Innovation” and “Developing Sustainability with AI”
K: Knowledge-Driven Workflows
Speaking of workflows, that brings us to TRICK’s final letter. As teams progress through the development and testing cycle, they generate a ton of knowledge at each step. But often, they’re losing a lot of knowledge and experience in the spaces between each step because information is trapped in silos. These silos act like a filter that sifts valuable nuggets of insight from between each phase until hardly any is left at the end of the line.
When I say digital twin means creating “knowledge-driven workflows,” I mean that it can capture information and experiences into a model-based ecosystem that can then be used to develop traceability and governance and improve product quality. A model-based systems engineering workflow breaks horizontal silos from requirements to product end of life by providing a model as a common language of communication.
These knowledge-driven workflows reduce design errors once you finally get to the product testing and release stages. There’s no such thing as a universal mistake-proof workflow, but you can certainly minimize errors and the time spent correcting them by harnessing previously lost knowledge.
As the maxim goes, life isn’t so much about being right as it is about being less and less wrong. Digital twin technology gives people a transformational way to innovate, become more efficient, and develop the next generation of standout products. Digital twin is the best way to be less wrong – and continuing to be less wrong is the real “TRICK” to unlocking innovation.
Click here to learn more about model-based systems engineering. To learn more about Altair’s digital twin capabilities, visit https://altair.com/digital-twin.