Rotor Blades with Insights
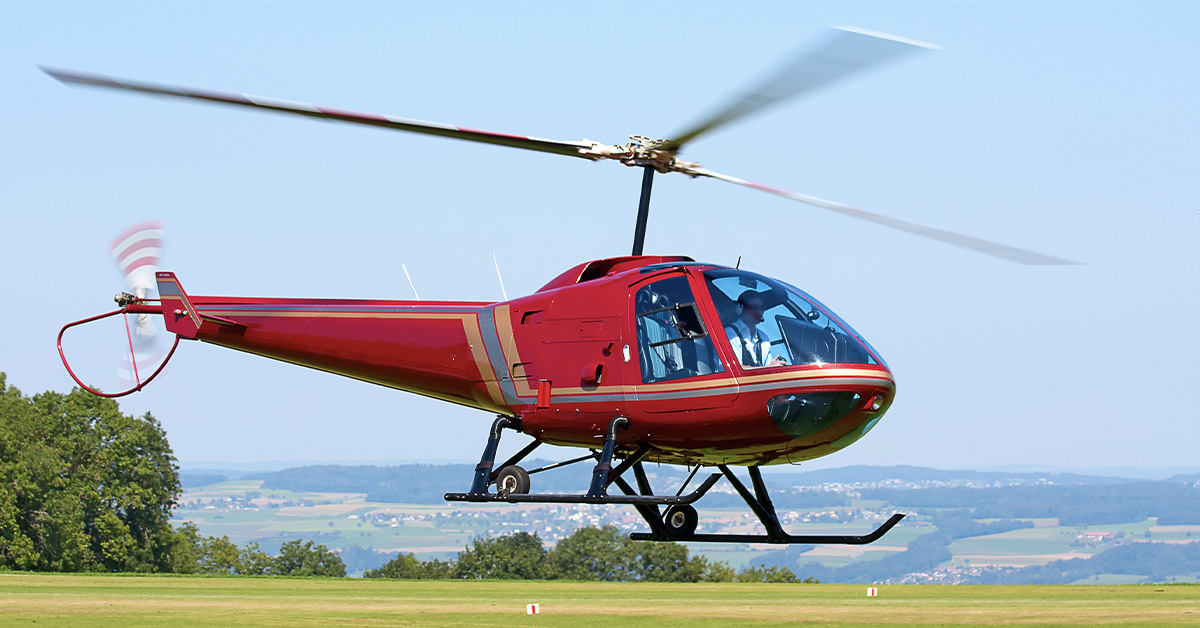
With the help of a powerful computer design tool, VABS, NASA and the US Army get heavily instrumented composite rotor blades to validate airflow simulations and measure rotor noise. HVAB blade design was driven by weight and center-of-gravity considerations rather than rotor performance, and buried sensors posed challenges for blade designer and fabricator Advanced Technologies Inc. (ATI) in Newport News, Virginia. “It’s the internals that are notably different,” observed ATI engineering manager David Pullman. “You’ve got almost 200 pressure sensors, temperature detectors and strain gauges. We had to undersize the spar to provide space for sensors.” ATI used the Variational Asymptotic Beam Sectional Analysis (VABS) design software from AnalySwift in West Jordan, Utah, to turn the complicated composite structure into a manageable engineering beam model. The VABS code computes properties of long, slender composite parts such as rotorcraft blades with accurate prediction of ply-level stresses and strains. Details of composite ply buildups can be modeled quickly. Pullman said, “We would evaluate the blade outside mold line and any unique properties. We basically developed a series of spar laminates, skin laminates, and iteratively evaluated the design to come up with spar and blade sections to meet customer requirements.