Saving Lives with Simulations: CEDREM Collaborates with DuPont on Ballistic Protection Solutions

Understanding behind-armor blunt trauma is important for developing effective personal ballistic protection solutions. Even if a bullet is stopped by the armor, some damage can still be transmitted to the body.
By today’s standards, the
protections are assessed on plastilina blocks and only the residual back-face deformation is measured. The blunt trauma behind the armor is not studied.
To improve the protection assessment process, the Defense Science and Technology Laboratory (DSTL) developed a testing rig. The goal is to simplify the testing process and to perform measurements during the impact. DuPont has improved this first
rig and developed the Dynamic Trauma Analyzer (DTA). The DTA consists of three main parts:
- A thorax surrogate with a semi-cylindrical rubber
- A steel framework holding the surrogate and straps holding the to-be-tested protection solution
- A measuring system decoupled from the framework
A Digital Image Correlation (DIC) configuration is also possible.
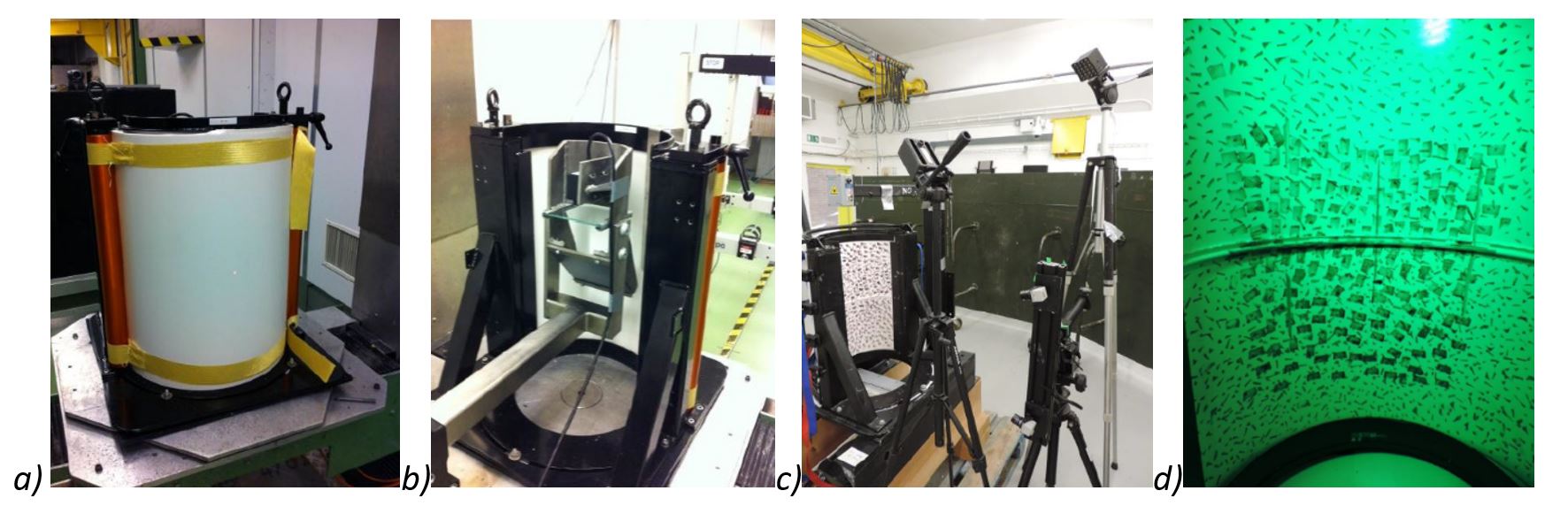
Figure 1. DTA pictures from the front (a), the back (b), and in DIC configuration (c and d).
In order to develop new protection solutions, DuPont is interested in numerically reproducing the behavior of the DTA. This process can be broken down into three steps:
- Reproduce the threats (bullets)
- Reproduce the DuPont products (Kevlar® fabrics)
- Reproduce the DTA
The Threats
Within this study, personal protective products up to level NIJ III-A are considered. Hence, the associated bullets are:
- 9mm FMJ RN Remington
- .44 Magnum SJHP Remington
- .357 Magnum SJSP Remington
CEDREM has built 3D numerical models of these bullets. They are composed of a lead core and a copper envelope. Steinberg material laws represent these components, associated to Mie-Grüneisen equations of state. The mesh is composed of 3D hexahedrons.
Figure 2. Comparison between real and virtual bullets for 9mm (a) and .44 Magnum (b) calibres
The Protection Product
The DuPont product is the Kevlar® XP™ S103. It is a non-crimped fabric (NCF) of 2 aramid layers oriented at +45° and -45°. Many numerical strategies could be investigated to represent this product exploring different element
types (shell or solid) and different scales (microscopic, mesoscopic, macroscopic).
The microscopic approach was not investigated as it requires heavy models and long calculation times.
The macroscopic approach is the most typical. It was
investigated using a type 11 property card (SH_SANDW) and type 25 material card (COMPSH).
The mesoscopic approach was investigated using the KTex tools. They help building finite element models of many types of composite fabrics (UD, 2D, 3D…) at the scale of the yarns. They also help simulate the manufacturing processes specific to
composite materials and analyze their impact on the mechanical performance of the final part.
Two types of elements were compared, solids and shells. A variable thickness through the cross-section of the fibers was used to give an elliptic shape
to the shell elements.

Figure 3. Cross-section of the fibres with solids (a) and shells (b).
The DuPont protection solution, composed of 10 layers of this NCF, is represented with the two strategies.
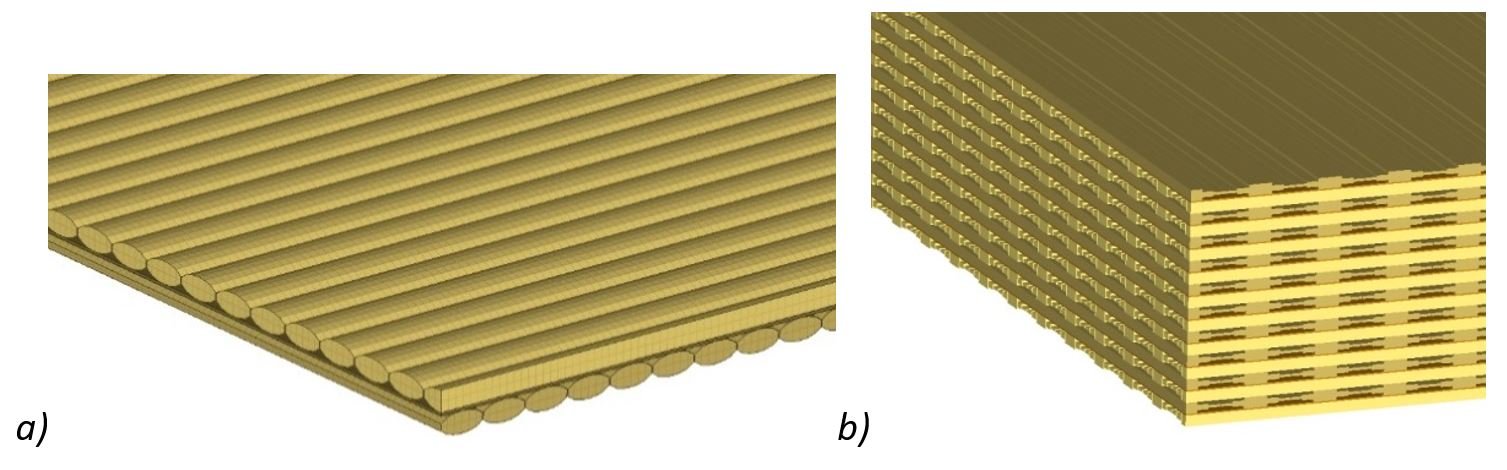
Figure 4. One layer of fabric with solid elements (a) and 10 layers of product with shell elements (b).
The DTA
The DTA is composed of a white hyper-elastic rubber material. Some quasi-static and dynamic compressive trials were performed to characterize it and assess its strain rate dependency.
Figure 5. Quasi-static and dynamic compression curves of the DTA rubber material
The DTA component was meshed with 3D solid elements. Different material laws were investigated: law 42 (Ogden), law 70 (visco-elastic foam) and law 36 (tabulated plastic).
In order to validate these numerical models, a 9mm bullet impact on the DTA
was simulated. A mesoscopically meshed patch of the DuPont protection product was linked to a macroscopic fabric to accelerate the calculations
Figure 6. Validation model of a 9mm impact.
In order to validate the model, the maximal back-face deformation and the time at which it is measured can be compared to experimental result
Figure 7. Back-face deformation and time of deformation comparison between simulations and experiments
The simulations also showed the same number of perforated plies as in the experiments, which is a good means to assess their validity
Figure 8. Number of perforated plies in the simulations
In order to reduce calculation time, a macroscopic material law of the DuPont product was implemented. Mesoscopic and macroscopic approaches show almost identical results.
Figure 9. Back-face deformation and time of deformation comparison between mesoscopic and macroscopic approaches of the 9mm bullet impact
Given the very good precision of the macroscopic model and the lower calculation times, the other threats were validated with this strategy.
With these results, the bullets, the DTA and the DuPont product numerical models are considered validated and the first aim of the study is achieved.
The second point of interest is to replace, in the simulations, the DTA by the numerical model of the human body, HUByx. HUByx was developed to simulate pressure propagation inside the body as well as the internal organs. Figure 11. HUByx visualization
Figure 11. HUByx visualization
In order to validate HUByx, some blunt impacts from the literature were reproduced with various impactors impacting the body at various speeds and in various locations. Pressure propagation was validated reproducing Merkle et al. experiments featuring
a human torso surrogate under blast loadings.
When replacing the DTA by HUByx, the human variability can easily be seen.
Since the DTA is representative of the lungs, its back-face deformation should match the deformation of the HUByx lungs. But when DTA is a homogenous material and impact location has almost no influence, this is completely different on the real
body. Between an impact on a rib, an impact between two ribs or an impact in the abdomen, the behavior of the body will be different.
The curves below show the displacement of the lung for a shot on the DTA, a shot on a rib and a shot between
two ribs.
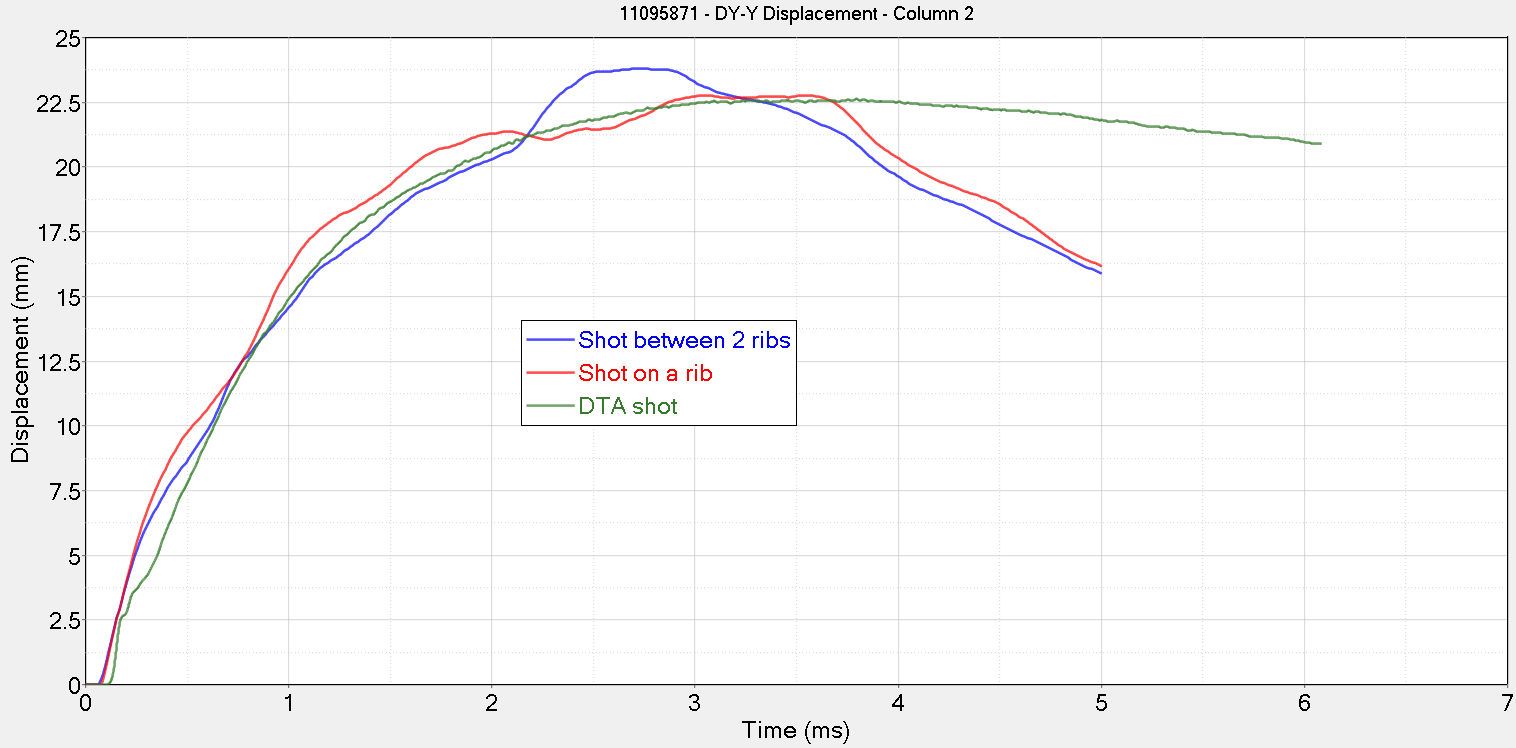
The DTA seems to be a good thorax average as its results is between the two numerical configurations results.
When looking at an impact in the stomach, the lung displacement cannot be observed anymore. A good solution is to measure the displacement
of the skin or of the ribs.
Figure 14. Comparison of the DTA displacement with the skin and rib displacement for a shot on a rib and a shot in the stomach
As expected, the displacement of the skin for a shot in the stomach is higher than for a shot on a rib as no ribcage stiffens the body at this location. The blue and red curves show the body variability that can be studied with HUByx.
In conclusion,
the DTA was highlighted as a new tool to dynamically and efficiently assess protection solutions. KTex Family tools can help represent woven protection solutions, even if they are more useful for 2D and 3D weaves. HUByx is a good surrogate to simulate
impacts on the human body. Coupling bullet impacts with woven protection solutions on a human body is possible. Different ways to improve HUByx can be imagined. The most important one would be to find a way to link the mechanical measurements inside
HUByx (stress, strain, pressure…) with injury thresholds. Another one would be to work on the bones materials to predict accurately the fractures under high speed loadings and strain rates. Finally, this study has drawn the spotlight on the
possibility to predict potential injury as a function of the impact location (sternum, spine, stomach, head…).
If you would like to learn more, please visit the KTex Family and HUByx solution pages.
This guest contribution on Innovation Intelligence is written by Edouard Ferry, Engineer at CEDREM. HUByx software by CEDREM is a finite element model of the human body simulating all the bones and organs as well as the internal fluid in between them, enabling the propagation of pressure waves inside the body. KTex Family software by CEDREM is a set of tools dedicated to modeling composite materials precisely at the scale of the yarns, taking into account the impact of manufacturing processes on their mechanical properties. Both HUByx and KTex Family are available through the
Altair Partner Alliance.