Designing Construction and Mining Equipment – Shorten Design Cycles and Optimize Equipment Performance with Bulk Material Simulation
Challenges of designing construction and mining equipment
Manufacturers of heavy equipment are faced with a wide range of challenges. To meet the demand of the market and stay competitive they need to continuously improve the performance, efficiency, and reliability of their machines but also deliver products quickly while ensuring product innovation. This means shortening the design cycle and getting it right the first time is critical.
What adds to the complexity of designing construction and mining equipment is that machines have to operate in very harsh environments and need to perform well in a wide range of conditions. Skid steer loaders, excavators, backhoe loaders, or truck bodies are all intended to handle bulk materials that can vary in shape and form, from large quarry rocks to cohesive soils, abrasive ores, or free flowing granules – to mention a few. These materials and their interaction with the machine parts have a strong effect on the equipment performance.
For instance, an excavator digging through a pile of rocks will require a stronger bucket and much more power than for a pile of dry sand, designers also have to then account for different deformations on the bucket arm due to the loading. The level of wear on the bucket may also vary based on whether a material is an abrasive sandstone or a soft soil.
A truck body needs to load and unload material quickly and without spillage to be efficient and reduce fuel consumption. A cohesive material might stick to the truck body during unloading or an abrasive one might result in a high level of wear.
When designing mining transfer chutes and conveyor systems the durability and reliability of the system is of key importance, material blocking chutes, or causing excessive wear can result in operational down-times as chutes are cleared or repaired.
Understanding how bulk materials will behave with equipment is therefore critical to ensure high performance. Customers are demanding customized solutions and confidence that equipment will perform as expected for a range of operating conditions.
Predicting bulk material behavior is however, difficult as sand, gravels, soils, rocks, and ores have very diverse properties. Assumptions of the anticipated material behavior is challenging and can lead to expensive mistakes. Physical testing is costly and time-consuming and typically restricted to a small number of available materials and motions. Is there a better alternative?
Using simulation in the design process
Computer-aided-engineering (CAE) tools such as finite element analysis and multi-body dynamics (MBD) are commonly used in the design process to perform virtual testing of equipment design. These techniques however, do not include the material itself that the machine is designed to handle.
This is where bulk material simulation and discrete element modeling (DEM) come into play. DEM is a particle-scale numerical method for modelling the bulk behavior of bulk materials. DEM provides crucial engineering insight into how materials will interact with equipment during a range of operating conditions.
DEM software such as Altair EDEMTM can be used for the design, performance analysis, and optimization of construction and mining equipment such as dump trucks, excavators, loaders and dozers.
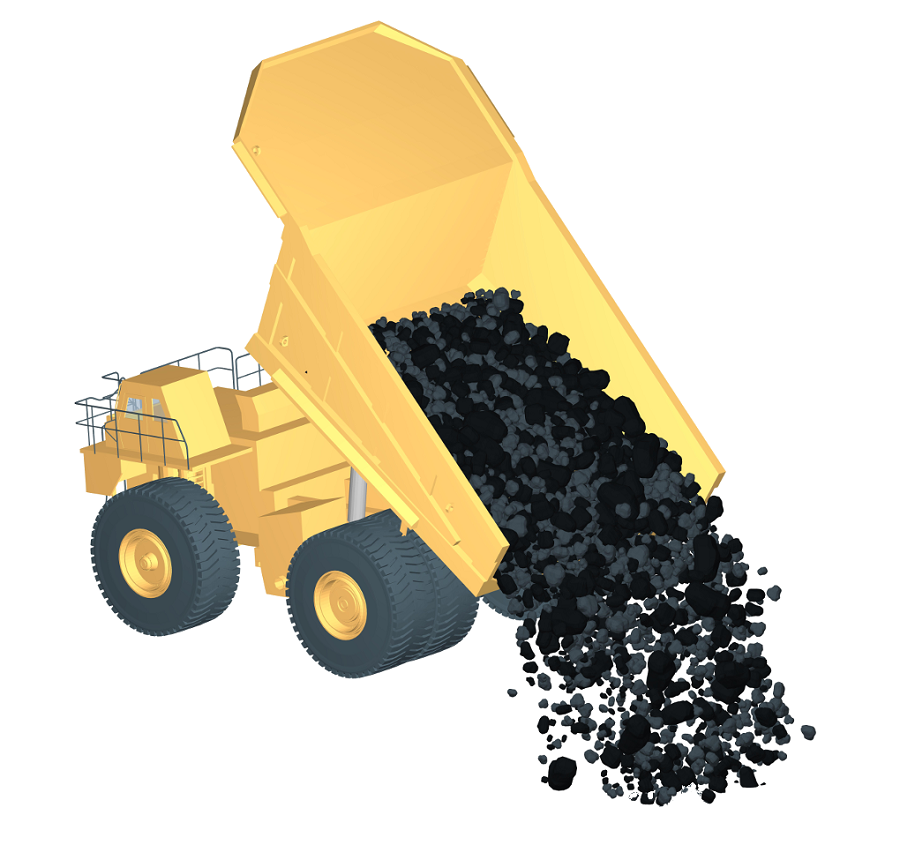
EDEM can be coupled to a wide range of other CAE tools to perform multi-body dynamics (MBD) analysis or FEA on the equipment. MBD is required to allow complex motions and material force-feedback on the equipment to be included in the equipment design and analysis.
Using EDEM bulk material simulation technology brings numerous benefits to original equipment manufacturers (OEMs) – including the ability to:
- Understand how different materials affect designs
- Virtually test designs for a wide range of materials with different properties
- Perform virtual repetitive testing– under the same conditions every time
- Predict bulk material behavior: identify risk of blockages, spillage and areas prone to wear
- Improve equipment reliability and design for worst-case scenarios
- Get key insight into equipment-material interactions
This insight brings confidence that a design will perform as planned in real conditions and can lead to key optimizations being made – resulting in improved durability and performance, lower fuel consumption and increased payload capacity.
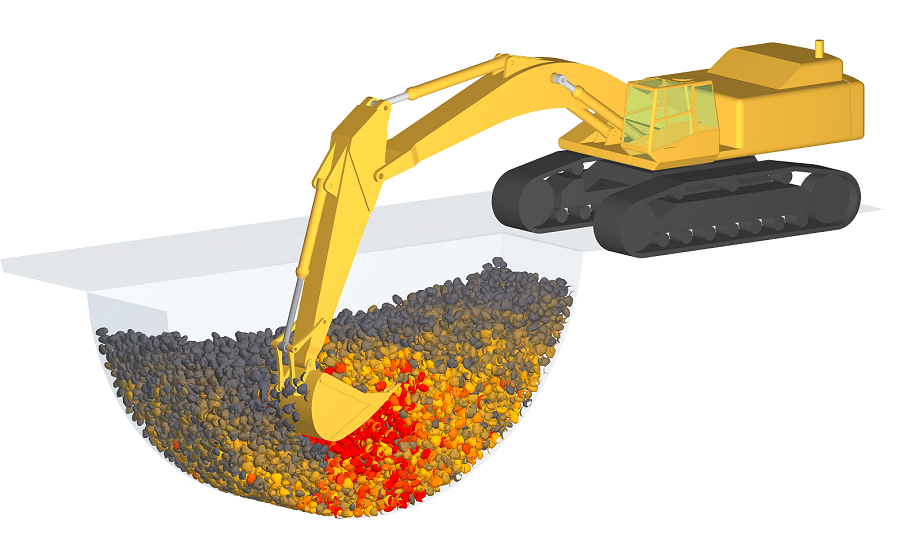
EDEM can be used together with FEA and MBD tools, enabling engineers to perform extensive what-if analysis and leading to improved designed accuracy and performance thanks to the addition of realistic bulk material loads.
Adding EDEM to the engineering toolkit can help engineers shorten design cycles, reduce product development time and costs, reduce the need and thus the cost of physical prototyping as well as driving product innovation.
Find out more about the various applications of EDEM simulation in the design of construction and mining equipment with this on-demand webinar.