How Process Manufacturers Can Benefit from Smart Manufacturing Technologies
Any industry that produces bulk quantities of goods such as pharmaceuticals, food, chemicals, or cosmetics is seeking to produce high quality products consistently while reducing cost factors like waste and down time. Due to the nature of process manufacturing, multiple ingredients are combined to be mixed, coated, or sorted, so understanding the behavior of these processes is highly important.
Through the use of simulation modeling and smart manufacturing principals, manufacturers are now able to optimize these processes, leading to greater productivity and profitability. This progression is largely, if not solely, the result of what has been coined ‘Industry 4.0’; a reference to the next industrial revolution of which we are on the precipice.
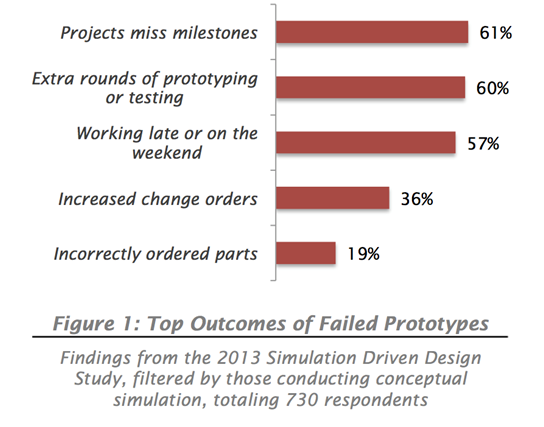
Leveraging data produced from smart manufacturing technologies is fundamental to achieving the benefits offered when applied to process manufacturing. Equipment maintenance, quality, efficiency monitoring, and building data and physics-based digital twins all produce data that needs to be converted, stored, and analyzed.
Equipment Maintenance The effects of downtime (whether scheduled or not) has an obvious impact on a process manufacturer’s output and when it comes to the maintenance of equipment, a preventative approach is usually taken. Based on experience and historical performance, companies schedule service on a regular basis because of wear and tear that leads to downtime if unattended.
Having access to real-time data enables process manufacturers to react more quickly to potential issues, ultimately reducing downtime and improving product quality. This is achieved by leveraging data streaming from equipment to predict exactly when maintenance is required, keeping equipment running for a more efficient maintenance process and an increase in uptime with minimum costs. For example, the use of vibration sensors provides an alert when motors, bearings, or other equipment begin to falter and require maintenance. Detecting anomalies may not even require additional sensor installations as observations of existing values such as the current of a motor for example, can be used to gain a greater insight into the behaviour of a machine’s performance.
Of course, all this data will need to be connected to the various systems in place and this is where Altair’s IoT application comes in. Connectivity is at the core of data extraction and control, growing in complexity when the number of equipment and devices increases and spreads geographically. Altair’s IoT application allows you to undertake device management, edge orchestration, data storage, data streaming, and dashboard visualizations, as well as custom application builds to get the most out of your Industry 4.0 and smart manufacturing initiatives.
Quality and Efficiency Both quality and efficiency are also aspects that process manufacturers monitor to either improve or maintain consistently. Take the pharmaceutical industry for example. Given the heavily regulated nature of this industry, the quality of a product can be the deciding factor behind whether a batch makes or loses money for the manufacturer.
Companies who implement a smart manufacturing approach focus on using data to continually compare product quality in real time. This preventative measure allows manufacturers to stop quality issues from happening in the first place, maintaining the company’s reputation, and ensuring its products remain of high quality.
Likewise, identifying bottlenecks and inefficiencies throughout the manufacturing process is imperative. By utilizing artificial intelligence and machine learning algorithms, data can be reviewed in real time to discover anomalies and correlate findings with detrimental events. This proactive approach enables a process manufacturer to identify the best set-up possible.
Digital Twin Digital twins help process manufacturers optimize product performance, gain visibility into the in-service life of a product, know when and where to perform predictive maintenance, and understand how to extend a product’s remaining useful life (RUL). These form part of the data-driven digital twin and can be an incredibly useful tool for process manufacturers wanting to gain insight into their machines.
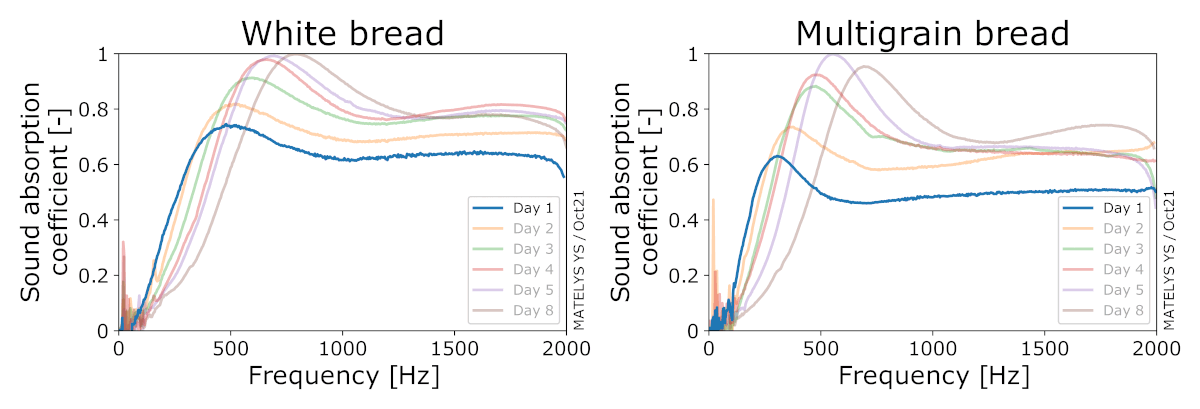
Within process manufacturing, discrete element modeling software such as Altair EDEM™ can be incorporated into the digital twin model to simulate processes such as mixing, coating, and die filling. In a holistic process model, forces, pressures and wear on the equipment caused by the bulk material can be analyzed, providing an understanding on how the material affects the equipment. In processes where having a deeper insight of equipment functionality when handling bulk material is necessary, EDEM coupled with Altair MotionSolve™ can provide a detailed analysis of bulk material on key components, such as a hydraulics system. This allows a better understanding of the equipment response to the interaction with the bulk material.
Data collected from existing processes can be sampled and compared to the optimal parameters in a simulated model to identify possible failures and issues, becoming an integral part of the decision-making process when considering how to improve or accelerate existing methods.
A combination of physics-driven and data-driven digital twins provides an process manufacturer with greater insight and control over their processes, enables the fine tuning of equipment and process parameters, ensures timely intervention for maintenance, and has an indirect impact on production and inventory costs. The Altair digital twin integration platform blends physics- and data-driven twins to support optimization throughout the products lifecycle.
For process manufacturers to remain competitive, an unquestionable solution will be the adoption of smart manufacturing technologies with the promise of improved efficiency whilst reducing cost and time spent on avoidable interruptions, making Altair the perfect partner. Altair offers a complete suite of simulation solutions that provide process manufacturers insight into complex mechanism and system operations, data analytics tools for data-driven smart operations, and solutions to connect industrial systems into the internet of things.
Click here to view our Process Manufacturing eGuide.
Through the use of simulation modeling and smart manufacturing principals, manufacturers are now able to optimize these processes, leading to greater productivity and profitability. This progression is largely, if not solely, the result of what has been coined ‘Industry 4.0’; a reference to the next industrial revolution of which we are on the precipice.
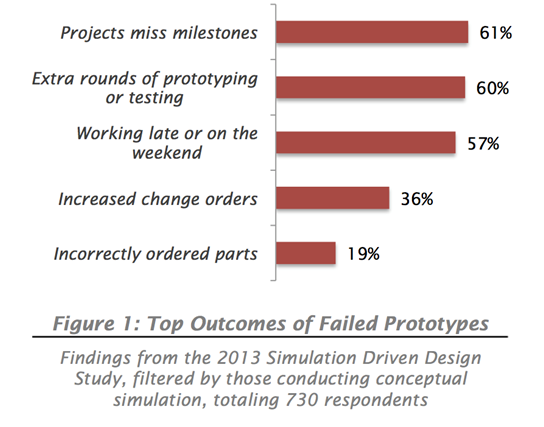
Leveraging data produced from smart manufacturing technologies is fundamental to achieving the benefits offered when applied to process manufacturing. Equipment maintenance, quality, efficiency monitoring, and building data and physics-based digital twins all produce data that needs to be converted, stored, and analyzed.
Equipment Maintenance The effects of downtime (whether scheduled or not) has an obvious impact on a process manufacturer’s output and when it comes to the maintenance of equipment, a preventative approach is usually taken. Based on experience and historical performance, companies schedule service on a regular basis because of wear and tear that leads to downtime if unattended.
Having access to real-time data enables process manufacturers to react more quickly to potential issues, ultimately reducing downtime and improving product quality. This is achieved by leveraging data streaming from equipment to predict exactly when maintenance is required, keeping equipment running for a more efficient maintenance process and an increase in uptime with minimum costs. For example, the use of vibration sensors provides an alert when motors, bearings, or other equipment begin to falter and require maintenance. Detecting anomalies may not even require additional sensor installations as observations of existing values such as the current of a motor for example, can be used to gain a greater insight into the behaviour of a machine’s performance.
Of course, all this data will need to be connected to the various systems in place and this is where Altair’s IoT application comes in. Connectivity is at the core of data extraction and control, growing in complexity when the number of equipment and devices increases and spreads geographically. Altair’s IoT application allows you to undertake device management, edge orchestration, data storage, data streaming, and dashboard visualizations, as well as custom application builds to get the most out of your Industry 4.0 and smart manufacturing initiatives.
Quality and Efficiency Both quality and efficiency are also aspects that process manufacturers monitor to either improve or maintain consistently. Take the pharmaceutical industry for example. Given the heavily regulated nature of this industry, the quality of a product can be the deciding factor behind whether a batch makes or loses money for the manufacturer.
Companies who implement a smart manufacturing approach focus on using data to continually compare product quality in real time. This preventative measure allows manufacturers to stop quality issues from happening in the first place, maintaining the company’s reputation, and ensuring its products remain of high quality.
Likewise, identifying bottlenecks and inefficiencies throughout the manufacturing process is imperative. By utilizing artificial intelligence and machine learning algorithms, data can be reviewed in real time to discover anomalies and correlate findings with detrimental events. This proactive approach enables a process manufacturer to identify the best set-up possible.
Digital Twin Digital twins help process manufacturers optimize product performance, gain visibility into the in-service life of a product, know when and where to perform predictive maintenance, and understand how to extend a product’s remaining useful life (RUL). These form part of the data-driven digital twin and can be an incredibly useful tool for process manufacturers wanting to gain insight into their machines.
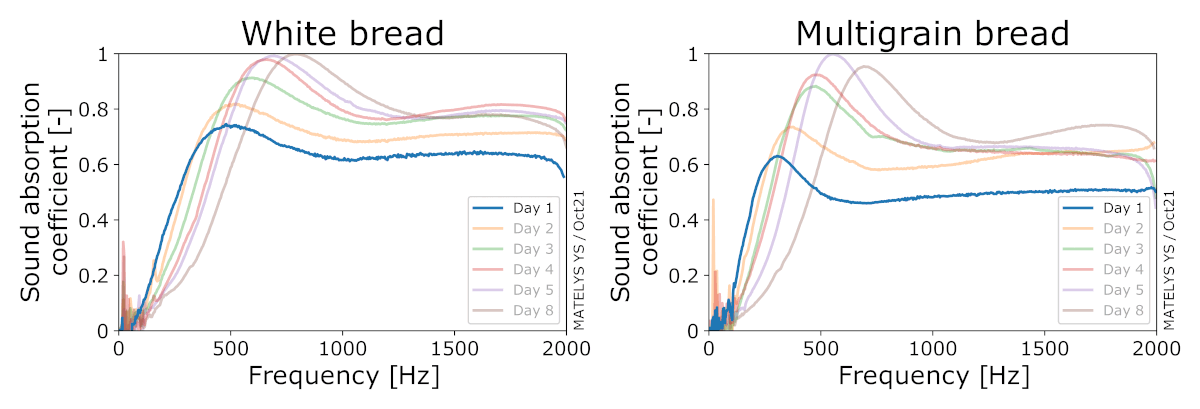
Within process manufacturing, discrete element modeling software such as Altair EDEM™ can be incorporated into the digital twin model to simulate processes such as mixing, coating, and die filling. In a holistic process model, forces, pressures and wear on the equipment caused by the bulk material can be analyzed, providing an understanding on how the material affects the equipment. In processes where having a deeper insight of equipment functionality when handling bulk material is necessary, EDEM coupled with Altair MotionSolve™ can provide a detailed analysis of bulk material on key components, such as a hydraulics system. This allows a better understanding of the equipment response to the interaction with the bulk material.
Data collected from existing processes can be sampled and compared to the optimal parameters in a simulated model to identify possible failures and issues, becoming an integral part of the decision-making process when considering how to improve or accelerate existing methods.
A combination of physics-driven and data-driven digital twins provides an process manufacturer with greater insight and control over their processes, enables the fine tuning of equipment and process parameters, ensures timely intervention for maintenance, and has an indirect impact on production and inventory costs. The Altair digital twin integration platform blends physics- and data-driven twins to support optimization throughout the products lifecycle.
For process manufacturers to remain competitive, an unquestionable solution will be the adoption of smart manufacturing technologies with the promise of improved efficiency whilst reducing cost and time spent on avoidable interruptions, making Altair the perfect partner. Altair offers a complete suite of simulation solutions that provide process manufacturers insight into complex mechanism and system operations, data analytics tools for data-driven smart operations, and solutions to connect industrial systems into the internet of things.
Click here to view our Process Manufacturing eGuide.