ModelCenter Simplifies Multidisciplinary Optimization of an Electric Motor for an Automobile
Guest authors – Scott Ragon, Ilya Tolchinsky, and Olivier Morisot from Phoenix Integration
Designing a modern electric motor for an electrified automobile requires striking the perfect balance between cost, weight, and performance. From a modeling and simulation standpoint, predicting the overall performance of the motor requires multiple multi-disciplinary analyses, including electromagnetic, thermal, and stress analyses.
The traditional computer aided engineering (CAE) process is simply not possible when the validation of the design requires this many models and types of solvers. This process consists of setting up a model, running the simulation, post-processing data, reviewing results, extracting the outputs of one simulation that are inputs into another, and iterating until an acceptable design is achieved.
ModelCenter’s powerful integration capabilities provide engineers with the ability to quickly build automated multidisciplinary workflows. This enables the Altair Hyperworks™ software suite to be integrated in highly complex applications. In this example ModelCenter was used to solve the multidisciplinary problem of the design of an electric motor for an automobile and brought together electromagnetic, thermal, and structural performance criteria in a single workflow so that all the performance aspects and constraints can be simultaneously considered to design an efficient motor. The individual disciplines are evaluated using Altair solvers – Altair FluxMotor™ (initial baseline motor design), Altair Flux™ (EMAG), and Altair OptiStruct™ (thermal and stress analyses).
ModelCenter is a framework for model-based engineering and allows users to:
The design optimization problem is defined as follows:
After the workflow has been created, we can explore the design space to gain insight into our designs.
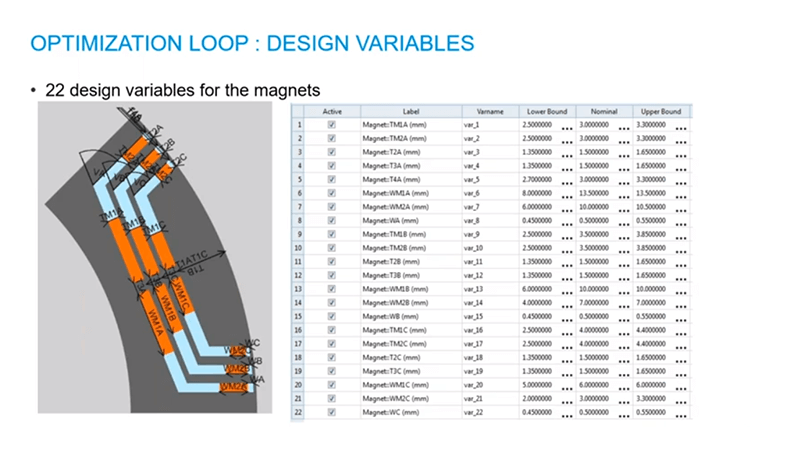
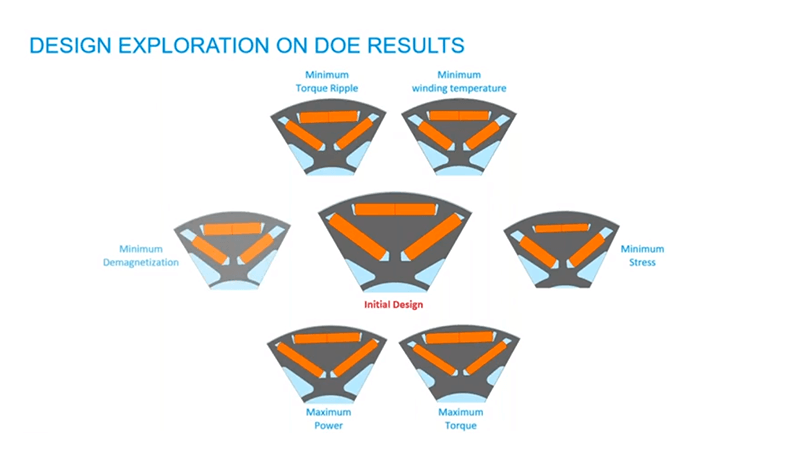
Based on the results of the DoE, we are now able to identify which design variables have the most impact on our design and performance targets, and what are the usable ranges for these variables. This will help us define the optimization problem properly so we can run an optimization loop to find best the compromise based on the current objectives.
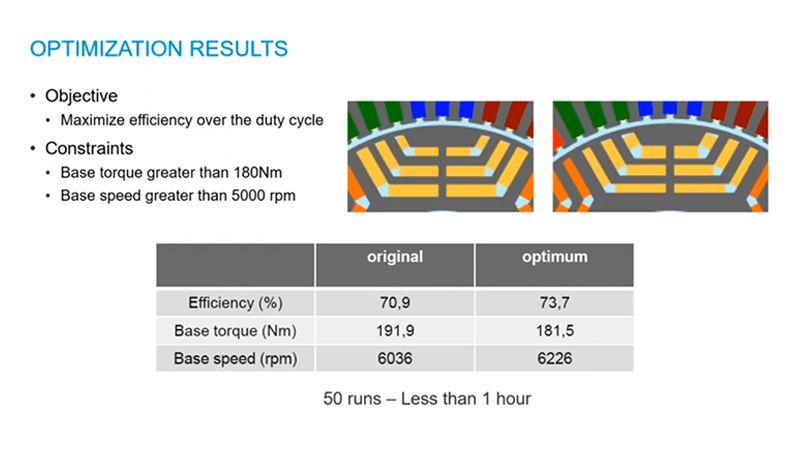
In this particular case, we were able to increase the efficiency of our motor by 3% while meeting all of our constraints in less than one hour.
To learn more about ModelCenter by Phoenix Integration, visit our partner page.
Designing a modern electric motor for an electrified automobile requires striking the perfect balance between cost, weight, and performance. From a modeling and simulation standpoint, predicting the overall performance of the motor requires multiple multi-disciplinary analyses, including electromagnetic, thermal, and stress analyses.
The traditional computer aided engineering (CAE) process is simply not possible when the validation of the design requires this many models and types of solvers. This process consists of setting up a model, running the simulation, post-processing data, reviewing results, extracting the outputs of one simulation that are inputs into another, and iterating until an acceptable design is achieved.
ModelCenter’s powerful integration capabilities provide engineers with the ability to quickly build automated multidisciplinary workflows. This enables the Altair Hyperworks™ software suite to be integrated in highly complex applications. In this example ModelCenter was used to solve the multidisciplinary problem of the design of an electric motor for an automobile and brought together electromagnetic, thermal, and structural performance criteria in a single workflow so that all the performance aspects and constraints can be simultaneously considered to design an efficient motor. The individual disciplines are evaluated using Altair solvers – Altair FluxMotor™ (initial baseline motor design), Altair Flux™ (EMAG), and Altair OptiStruct™ (thermal and stress analyses).
ModelCenter is a framework for model-based engineering and allows users to:
- Automate any modeling and simulation tool
- Integrate these tools together to create repeatable simulation workflows
- Set simulation parameters
- Automatically execute workflows
- Streamline the development of complex systems by connecting systems architecture and requirements to modeling and simulation tools
- Generate a baseline design using FluxMotor
- Define the Design of Experiments (DoE) to explore the design space
- Run the DoE (using Flux for EMAG, and OptiStruct for thermal and mechanical analyses)
- From the results of the design space, create reduced order models that will replace the physics-based in the multi-disciplinary analyses so the workflow can be executed much faster, thus making optimization feasible
- Set-up the optimization problem
- Run the optimization problem to come up with the optimum design
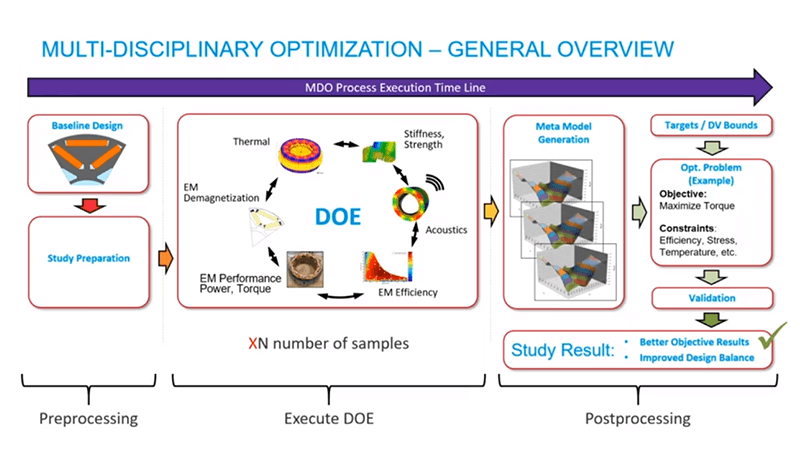
Diagram of the overall design and optimization process
ModelCenter provides an easy way to connect the different analysis tools into a sophisticated workflow. Shown above is graphical representation of the workflow which makes clear the order of execution of the components and the data dependencies between them. When components do not depend on each other, it is possible to run them in parallel to reduce execution time. The workflow is executed by Altair HyperStudy™ to search through the design space and find the best answer.The design optimization problem is defined as follows:
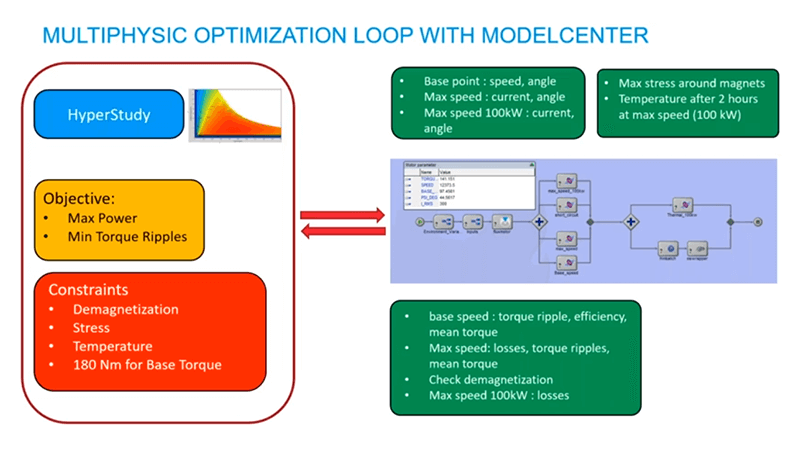
The design optimization problem is defined in the graphic above
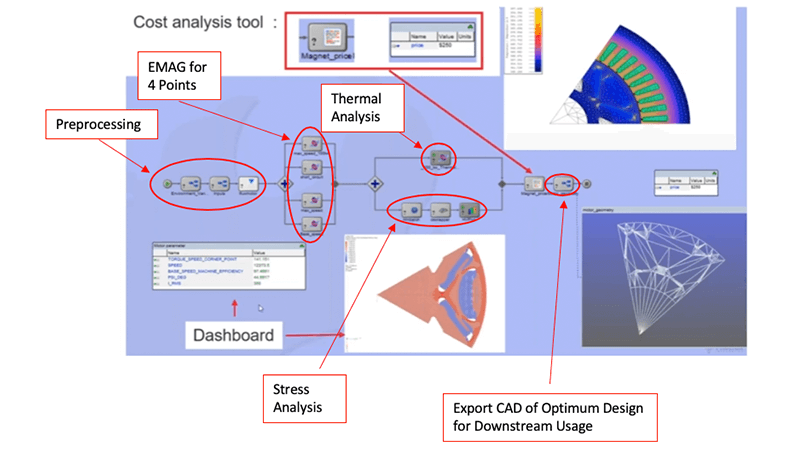
The associated ModelCenter workflow
The ModelCenter graphical user interface (GUI) allows the user to extract key information as the workflow is being executed, which provides a real time dashboard while the design iteration loops are running. In this particular instance, we selected a table with some of the key design variables and outputs, as well as graphic images of geometry along with stress and thermal results. This allows the analyst to get real time feedback on the analysis results and to monitor progress.After the workflow has been created, we can explore the design space to gain insight into our designs.
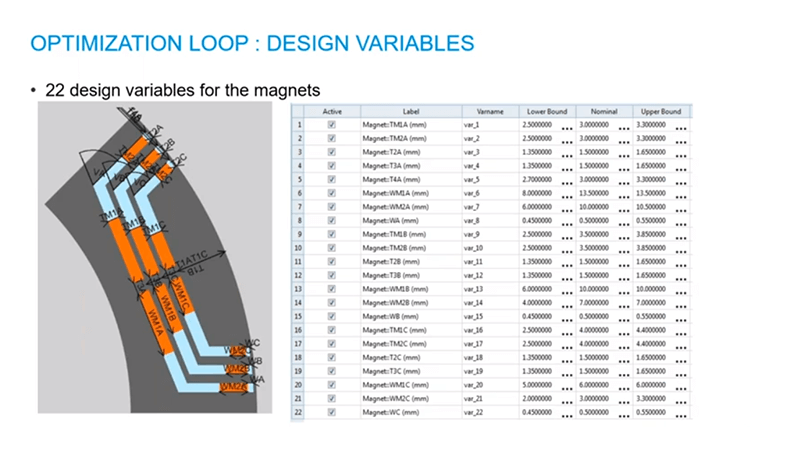
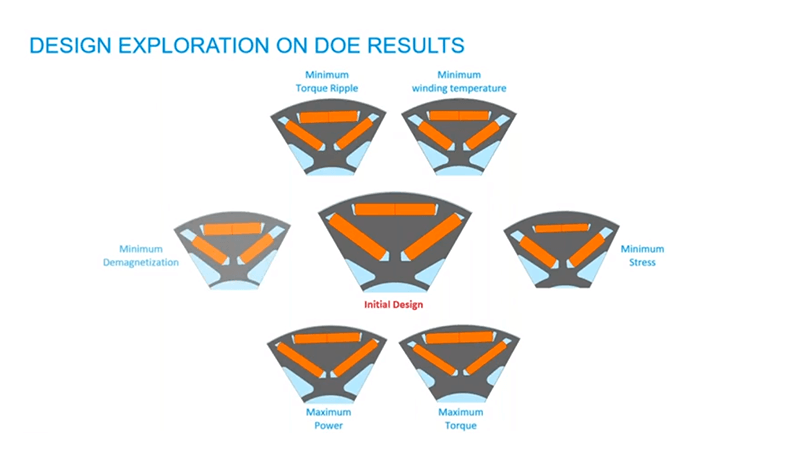
Based on the results of the DoE, we are now able to identify which design variables have the most impact on our design and performance targets, and what are the usable ranges for these variables. This will help us define the optimization problem properly so we can run an optimization loop to find best the compromise based on the current objectives.
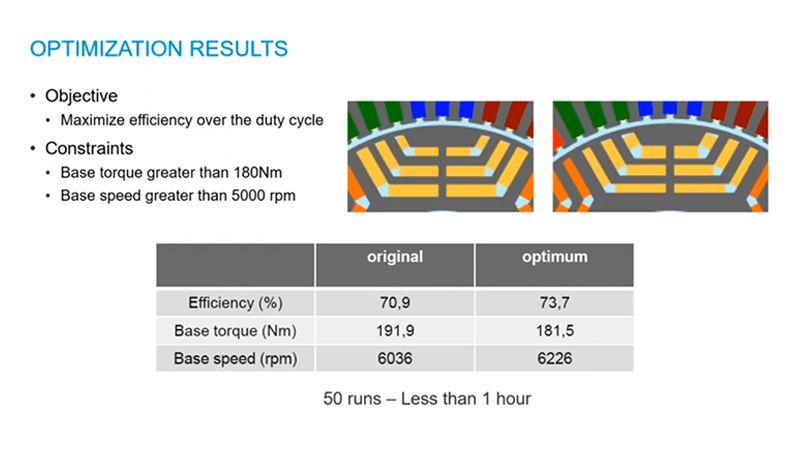
In this particular case, we were able to increase the efficiency of our motor by 3% while meeting all of our constraints in less than one hour.
To learn more about ModelCenter by Phoenix Integration, visit our partner page.