Using Casting Process Simulation to Improve Castings’ Environmental Footprint
This is a guest post from Håkan Fransson, technical simulation manager at NovaCast Systems, a member of the Altair Partner Alliance.
When a casting part is produced, a high amount of energy is generated since we need to melt the metal and then keep it at a high temperature during its filling into the mold cavity. This means that the production of a casting results in a big environmental footprint and high CO2 emissions during its manufacturing process. This footprint is inevitable but can be reduced by changing how you cast it. This article will be focused on the possibilities to improve this and also the use of casting process simulation to support the work.
Proof of how accurate simulations can be in terms of cold flows.
Possible improvements on the casting and the manufacturing process
There are a number of areas around the castings and its process that actually can be improved:
How NovaFlow&Solid can support the hunt of reduced environmental footprint:
With NovaFlow&Solid you get accurate cold flow predictions. This helps you to see where the limit goes for wall thickness but also test different ways to push this limit downwards by testing different ways to pour the part.
On the other hand, NovaFlow&Solid can also find the lowest temperature that can be used in order to fill the part. If using a lower temperature, the overheating of the melt could be less and the melt holding temperature could be less. This all results in lower energy consumption and less CO2 emissions.
The shrinkage prediction in NovaFlow&Solid can give you the ability to see how big the feeders really must be and you can also test different combinations of feeders to get the optimum yield. Casting yield = casting weight/(casting weight + feeder weight + gating system weight) x 100 = x %
The velocity prediction in NovaFlow&Solid during filling makes it possible to verify the design of a gating system. A classic approach is the ratio 1:2:4 meaning that the area of the channel should be twice the area of the down sprue and the ingate should have twice the area of the channel. The choke in the down sprue should be at the bottom end. All made in order to achieve a turbulence free filling with a an ingate speed of less than 0.5 m/s.
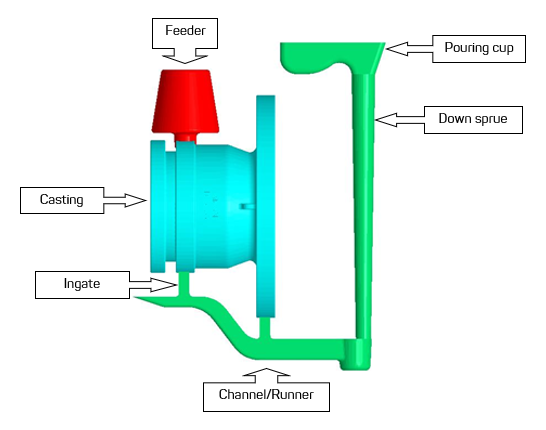
Correctly using a good casting process simulation system can really assist you in reducing the environmental footprint and make your foundry greener.
At NovaCast, we have a slogan “Every casting counts™” which means that you should be careful with every casting and give them all the possibility to be improved but I think also we should have the slogan of saying every kilogram counts as well as every kilowatt counts. The best resource is the one you did not have to use.
When a casting part is produced, a high amount of energy is generated since we need to melt the metal and then keep it at a high temperature during its filling into the mold cavity. This means that the production of a casting results in a big environmental footprint and high CO2 emissions during its manufacturing process. This footprint is inevitable but can be reduced by changing how you cast it. This article will be focused on the possibilities to improve this and also the use of casting process simulation to support the work.
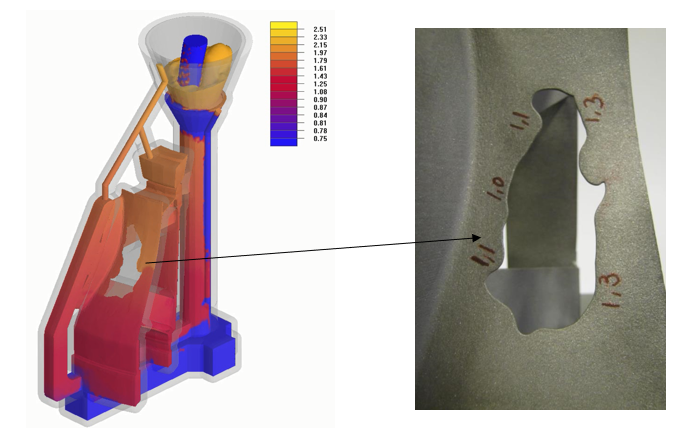
Possible improvements on the casting and the manufacturing process
There are a number of areas around the castings and its process that actually can be improved:
- Producing more thin-walled castings. This saves weight and energy both during the casting process but also in the final product.
- Yield improvement. By reducing the amount of liquid metal needed to produce the casting, you save poured amount of metal, energy and reduce C02 emissions.
- Optimize the casting parameters so a lower casting temperature could be used which saves energy and reduce CO2 emissions.
- Optimize your gating system technology without using for example filters which saves cost.
- Optimize your feeding system and the need for feeders by also optimizing the casting. Less need for exothermic feeders and less poured material gives lower cost, reduced material consumption, reduced energy consumption and lower CO2 emissions.
- Reduce defects in castings. Simulated castings gives lower scrap rate which results in lower cost, lower energy consumption, material need and less impact on the environment.
How NovaFlow&Solid can support the hunt of reduced environmental footprint:
With NovaFlow&Solid you get accurate cold flow predictions. This helps you to see where the limit goes for wall thickness but also test different ways to push this limit downwards by testing different ways to pour the part.
On the other hand, NovaFlow&Solid can also find the lowest temperature that can be used in order to fill the part. If using a lower temperature, the overheating of the melt could be less and the melt holding temperature could be less. This all results in lower energy consumption and less CO2 emissions.
The shrinkage prediction in NovaFlow&Solid can give you the ability to see how big the feeders really must be and you can also test different combinations of feeders to get the optimum yield. Casting yield = casting weight/(casting weight + feeder weight + gating system weight) x 100 = x %
The velocity prediction in NovaFlow&Solid during filling makes it possible to verify the design of a gating system. A classic approach is the ratio 1:2:4 meaning that the area of the channel should be twice the area of the down sprue and the ingate should have twice the area of the channel. The choke in the down sprue should be at the bottom end. All made in order to achieve a turbulence free filling with a an ingate speed of less than 0.5 m/s.
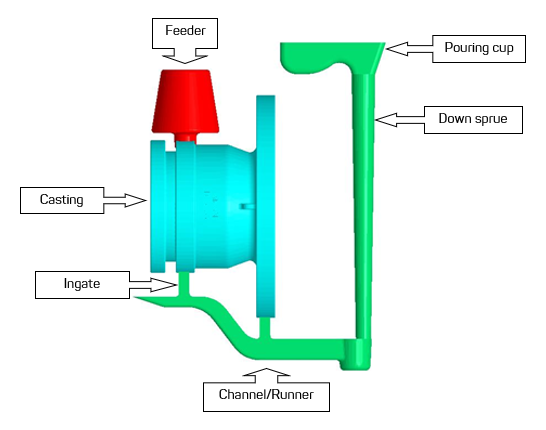
Correctly using a good casting process simulation system can really assist you in reducing the environmental footprint and make your foundry greener.
At NovaCast, we have a slogan “Every casting counts™” which means that you should be careful with every casting and give them all the possibility to be improved but I think also we should have the slogan of saying every kilogram counts as well as every kilowatt counts. The best resource is the one you did not have to use.